La temperatura più adatta per la combustione del cemento in un forno rotativo è tipicamente compresa tra 1400°C a 1500°C .Questo intervallo di temperatura garantisce la corretta formazione del clinker, che è il prodotto intermedio nella produzione del cemento.Al di sotto di questo intervallo, le reazioni chimiche necessarie per la formazione del clinker possono essere incomplete, mentre temperature superiori a questo intervallo possono comportare un consumo energetico eccessivo e potenziali danni al rivestimento del forno.Il processo prevede il riscaldamento delle materie prime (calcare, argilla e altri additivi) a questo intervallo di temperatura per facilitare le reazioni chimiche che producono il clinker.
Punti chiave spiegati:
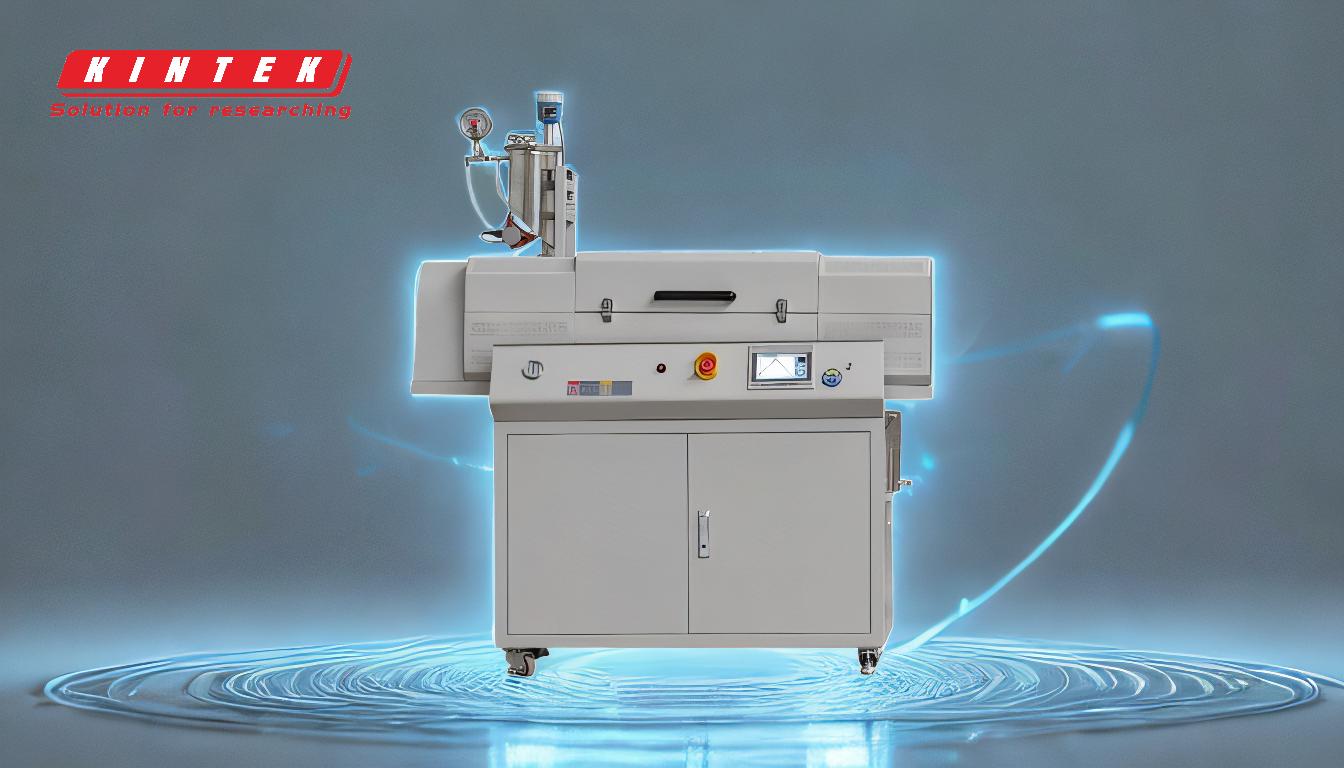
-
Intervallo di temperatura ottimale per la combustione del cemento:
- L'intervallo di temperatura ideale per la combustione del cemento in un forno rotante è da 1400°C a 1500°C .Questo intervallo è critico per la formazione del clinker, che è il componente principale del cemento.
- A questa temperatura, le materie prime subiscono una serie di reazioni chimiche, tra cui la calcinazione (decomposizione del calcare in calce) e la sinterizzazione (formazione di composti del clinker come alite e belite).
-
Perché 1400°C - 1500°C sono adatti:
- Reazioni chimiche:A temperature inferiori a 1400°C, le reazioni chimiche necessarie per la formazione del clinker possono non andare a buon fine, dando luogo a un clinker di scarsa qualità.Al di sopra dei 1500°C, le reazioni possono diventare troppo intense, causando sovracombustione e inefficienza energetica.
- Efficienza energetica:Il mantenimento della temperatura entro questo intervallo garantisce un uso efficiente dell'energia.Temperature eccessive comportano un maggiore consumo di combustibile e un aumento dei costi operativi.
- Protezione del rivestimento del forno:L'esposizione prolungata a temperature superiori a 1500°C può danneggiare il rivestimento refrattario del forno, riducendone la durata e aumentando i costi di manutenzione.
-
Confronto con altri tipi di forno:
- Forni rotativi indiretti:Questi forni operano tipicamente a temperature inferiori (1200-1300°C per il tubo del forno e meno di 1150°C per il materiale).Non sono adatti alla produzione di cemento, poiché non possono raggiungere le temperature necessarie per la formazione del clinker.
- Forni rotativi elettrici:Con una temperatura massima di esercizio di 1100°C, i forni rotativi elettrici non sono adatti alla produzione di cemento a causa della loro incapacità di raggiungere le necessarie temperature di formazione del clinker.
-
Fattori che influenzano la selezione della temperatura:
- Composizione della materia prima:La composizione chimica delle materie prime può influenzare la temperatura di combustione richiesta.Ad esempio, le materie prime con un contenuto di silice più elevato possono richiedere temperature leggermente più alte.
- Design del forno:Il design del forno rotativo, compresi lunghezza, diametro e rivestimento refrattario, può influire sulla distribuzione della temperatura e sull'efficienza del trasferimento di calore.
- Tipo di combustibile:Il tipo di combustibile utilizzato (ad esempio, carbone, gas naturale o combustibili alternativi) può influenzare la temperatura di combustione e, di conseguenza, la temperatura complessiva del forno.
-
Considerazioni pratiche:
- Controllo della temperatura:Il controllo preciso della temperatura è essenziale per mantenere le condizioni ottimali di combustione.Questo obiettivo viene generalmente raggiunto attraverso sistemi di controllo avanzati che monitorano e regolano l'alimentazione di combustibile e aria.
- Processo di raffreddamento:Dopo la formazione del clinker, è necessario raffreddarlo rapidamente per preservarne la qualità.Ciò avviene solitamente in un raffreddatore collegato al forno, dove il clinker viene raffreddato da circa 1400°C a meno di 200°C.
-
Impatto della temperatura sulla qualità del cemento:
- Qualità del clinker:La temperatura influisce direttamente sulla qualità del clinker, che a sua volta influenza la resistenza e la durata del prodotto cementizio finale.
- Consumo di energia:Il funzionamento all'interno dell'intervallo di temperatura ottimale riduce al minimo il consumo di energia, rendendo il processo più economico e rispettoso dell'ambiente.
- Considerazioni ambientali:Il mantenimento della temperatura corretta contribuisce a ridurre le emissioni di sostanze inquinanti come gli ossidi di azoto (NOx) e l'anidride solforosa (SO2), che sono sottoprodotti della combustione ad alta temperatura.
In sintesi, la temperatura più idonea per la combustione del cemento in un forno rotativo è compresa tra 1400°C e 1500°C.Questo intervallo garantisce una formazione efficiente del clinker, l'efficienza energetica e la protezione del rivestimento del forno, contribuendo inoltre alla produzione di cemento di alta qualità.
Tabella riassuntiva:
Aspetto | Dettagli |
---|---|
Temperatura ottimale | Da 1400°C a 1500°C |
Scopo | Garantisce la corretta formazione del clinker e l'efficienza energetica |
Reazioni chimiche | La calcinazione e la sinterizzazione avvengono a questo intervallo |
Efficienza energetica | Riduce al minimo il consumo di combustibile e i costi operativi |
Protezione del rivestimento del forno | Previene i danni al rivestimento refrattario |
Qualità del cemento | Un clinker di alta qualità porta a un cemento durevole e resistente |
Impatto ambientale | Riduce le emissioni di NOx e SO2 |
Avete bisogno della consulenza di un esperto per ottimizzare il vostro forno rotativo per la produzione di cemento? Contattateci oggi stesso per saperne di più!