Lo sputtering è una tecnica di deposizione di film sottili ampiamente utilizzata, nota per l'elevata purezza, il controllo preciso e l'uniformità.Tuttavia, presenta diversi svantaggi che possono influire sulla sua efficienza, sui costi e sull'idoneità all'applicazione.Tra gli svantaggi principali si annoverano i tassi di deposizione più lenti, gli elevati costi operativi e delle apparecchiature, la sensibilità al calore, i rischi di contaminazione del film e le difficoltà nell'ottenere uno spessore uniforme del film.Inoltre, lo sputtering incontra limitazioni nella selezione dei materiali, nel controllo del processo e nell'integrazione con altre tecniche di fabbricazione.Questi fattori la rendono meno ideale per alcune applicazioni, in particolare quelle che richiedono un'elevata produttività, una bassa contaminazione o complesse combinazioni di materiali.
Punti chiave spiegati:
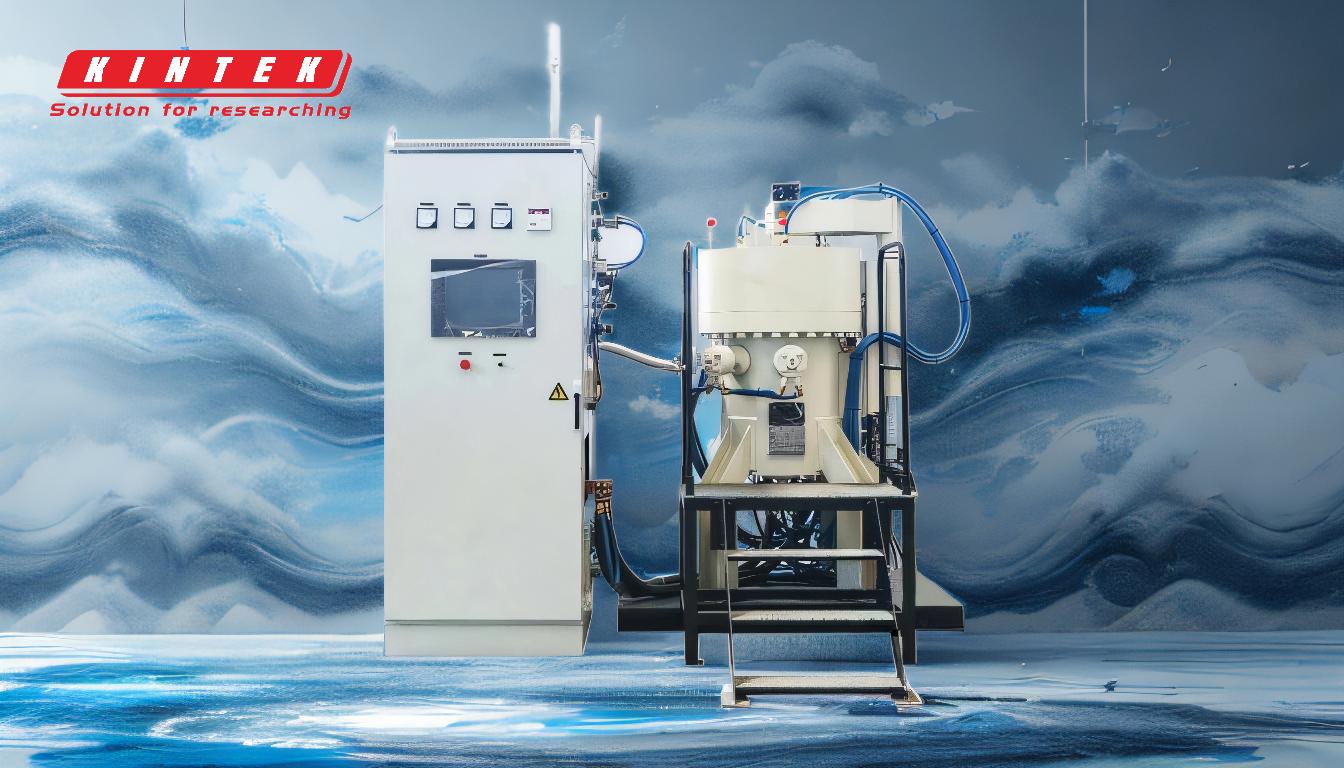
-
Tassi di deposizione più lenti
- Lo sputtering ha in genere tassi di deposizione più bassi rispetto a metodi come l'evaporazione termica.Ciò è dovuto alla natura fisica del processo, in cui gli atomi vengono espulsi da un materiale target e depositati su un substrato.La velocità ridotta può limitare la produttività, rendendolo meno adatto alla produzione di grandi volumi.
-
Costi operativi e di attrezzatura elevati
- I sistemi di sputtering sono costosi da acquistare e mantenere.La necessità di sistemi di vuoto di alta qualità, di fonti di alimentazione RF o DC e di sistemi di raffreddamento aumenta il costo complessivo.Inoltre, i target di sputtering sono spesso costosi e l'uso dei materiali può essere inefficiente, aumentando ulteriormente le spese.
-
Sensibilità al calore e requisiti di raffreddamento
- Una parte significativa dell'energia utilizzata nello sputtering viene convertita in calore, che deve essere efficacemente rimosso per evitare danni al substrato o al target.I sistemi di raffreddamento sono necessari, ma possono ridurre i ritmi di produzione e aumentare il consumo di energia, aumentando i costi operativi.
-
Rischi di contaminazione del film
- Lo sputtering può introdurre contaminazione nel film depositato.Le impurità del materiale bersaglio o i contaminanti gassosi del plasma possono attivarsi e incorporarsi nel film.Questo è particolarmente problematico nello sputtering reattivo, dove è necessario un attento controllo della composizione del gas per evitare l'avvelenamento del target.
-
Sfide per ottenere uno spessore uniforme del film
- La distribuzione del flusso di deposizione nello sputtering è spesso non uniforme, soprattutto per substrati o target di grandi dimensioni.Per ottenere uno spessore uniforme possono essere necessarie attrezzature mobili o configurazioni complesse, che aggiungono complessità e costi al processo.
-
Limitazioni nella selezione dei materiali
- Lo sputtering è limitato dalle temperature di fusione e dalle proprietà dei materiali di destinazione.Alcuni materiali possono non essere adatti allo sputtering a causa dei loro bassi punti di fusione o di altre caratteristiche fisiche, limitando la gamma di rivestimenti che possono essere prodotti.
-
Difficoltà di combinazione con i processi di sollevamento (Lift-Off)
- L'integrazione dello sputtering con i processi lift-off utilizzati nella strutturazione dei film è difficile.Il trasporto diffuso degli atomi sputati rende impossibile l'ombreggiatura completa, con conseguente contaminazione e difficoltà nell'ottenere modelli precisi.
-
Sfide del controllo attivo
- Rispetto ad altri metodi di deposizione, come la deposizione laser pulsata, lo sputtering offre un controllo meno attivo sulla crescita strato per strato.Questo può limitarne l'uso in applicazioni che richiedono un controllo preciso a livello atomico.
-
Pressioni operative elevate e problemi di tenuta
- I processi di sputtering tradizionali operano a pressioni relativamente elevate, che possono portare alla permeazione attraverso le guarnizioni in elastomero e ad altri problemi del sistema di vuoto.Questi problemi possono influire sulla qualità e sull'efficienza del processo di deposizione.
-
Disomogeneità della densità del plasma
- Per i catodi rettangolari di grandi dimensioni (ad esempio, >1m), può essere difficile ottenere una densità di plasma uniforme, con conseguente distribuzione non uniforme dello spessore dello strato.Ciò richiede ulteriori soluzioni ingegneristiche.
-
Inefficienza energetica
- La maggior parte dell'energia incidente sul bersaglio viene convertita in calore anziché essere utilizzata per la deposizione, rendendo il processo meno efficiente dal punto di vista energetico rispetto ad altre tecniche.
-
Complicazioni dello sputtering reattivo
- Nello sputtering reattivo, il controllo preciso della composizione del gas è fondamentale per evitare l'avvelenamento del bersaglio, in cui la superficie del bersaglio viene alterata chimicamente, riducendo l'efficienza di deposizione e la qualità del film.
Comprendendo questi svantaggi, gli acquirenti di apparecchiature e materiali di consumo possono decidere con cognizione di causa se lo sputtering è la tecnica giusta per le loro applicazioni specifiche, considerando fattori come il costo, la produttività e i requisiti dei materiali.
Tabella riassuntiva:
Svantaggio | Dettagli principali |
---|---|
Tassi di deposizione più lenti | Produzione inferiore rispetto a metodi come l'evaporazione termica. |
Costi operativi e di attrezzatura elevati | Sistemi costosi, requisiti di vuoto e target di sputtering costosi. |
Sensibilità al calore | Richiede sistemi di raffreddamento, riducendo i ritmi di produzione e aumentando il consumo energetico. |
Rischi di contaminazione del film | Le impurità provenienti dai target o dal plasma possono influire sulla qualità del film. |
Sfide legate allo spessore uniforme del film | Flusso di deposizione non uniforme, soprattutto per i substrati di grandi dimensioni. |
Limitazioni nella selezione dei materiali | Limitata dalle proprietà e dai punti di fusione del materiale di destinazione. |
Integrazione con i processi Lift-Off | Difficile da combinare con tecniche precise di strutturazione del film. |
Sfide del controllo attivo | Crescita strato per strato meno precisa rispetto ad altri metodi. |
Pressioni operative elevate | Possono causare problemi al sistema del vuoto e alla tenuta. |
Disomogeneità della densità del plasma | Difficile ottenere una densità di plasma uniforme per catodi di grandi dimensioni. |
Inefficienza energetica | La maggior parte dell'energia viene convertita in calore, non in deposito. |
Complicazioni dello sputtering reattivo | Richiede un controllo preciso del gas per evitare l'avvelenamento del bersaglio. |
Avete bisogno di aiuto per decidere se lo sputtering è adatto alla vostra applicazione? Contattate i nostri esperti oggi stesso per una consulenza su misura!