La forgiatura è un processo produttivo molto versatile che offre numerosi vantaggi, come una maggiore resistenza dei pezzi, forme personalizzate e specifiche di prestazioni uniche.È particolarmente vantaggioso per le applicazioni che richiedono elevata resistenza e durata.Il processo comprime la struttura dei grani del metallo, migliorandone le proprietà meccaniche e riducendo difetti come la porosità e la segregazione della lega.Tuttavia, la forgiatura presenta anche dei limiti, tra cui i costi iniziali di attrezzaggio più elevati e le limitazioni nella produzione di geometrie molto complesse.Di seguito analizziamo in dettaglio i principali vantaggi e limiti del processo di forgiatura.
Punti chiave spiegati:
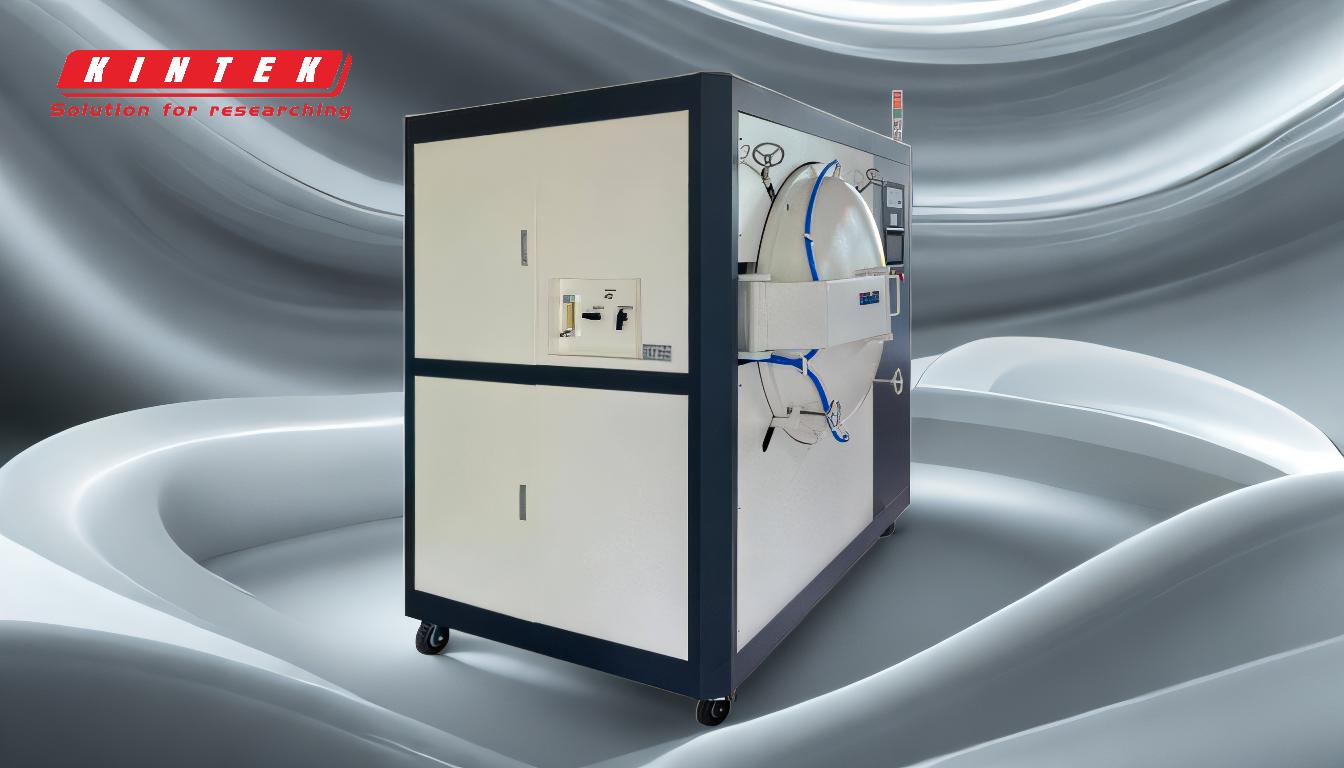
-
Vantaggi della forgiatura:
-
Resistenza e durata superiori:
- La forgiatura comprime la struttura dei grani del metallo, allineandola alla forma del pezzo.Questo flusso di grani aumenta la forza, la tenacità e la resistenza alla fatica del materiale, rendendo i pezzi forgiati ideali per le applicazioni ad alta sollecitazione.
-
Proprietà metallurgiche migliorate:
- Il processo riduce al minimo i difetti metallurgici come porosità, vuoti e segregazione della lega.Il risultato è un materiale più uniforme e privo di difetti, che migliora la risposta del pezzo al trattamento termico e riduce il rischio di guasti.
-
Forme e dimensioni personalizzate:
- La forgiatura consente di creare forme e dimensioni personalizzate, rendendola adatta ad applicazioni specializzate.Il processo può produrre pezzi con specifiche prestazionali uniche, difficili da ottenere con altri metodi di produzione.
-
Tempo di lavorazione ridotto:
- I pezzi forgiati spesso richiedono una minore lavorazione rispetto a quelli fusi o lavorati.La forma quasi netta prodotta dalla forgiatura riduce lo spreco di materiale e i tempi di lavorazione, con conseguenti risparmi sui costi.
-
Efficiente dal punto di vista dei costi per la produzione di grandi volumi:
- Sebbene i costi iniziali di attrezzaggio per la forgiatura possano essere elevati, il processo diventa conveniente per i volumi di produzione elevati grazie alla sua efficienza e alla riduzione degli scarti di materiale.
-
Resistenza e durata superiori:
-
Limitazioni della forgiatura:
-
Elevati costi iniziali di attrezzaggio:
- La forgiatura richiede stampi e utensili specializzati, che possono essere costosi da progettare e produrre.Questo rende il processo meno economico per la produzione di bassi volumi o di prototipi.
-
Complessità geometrica limitata:
- La forgiatura è meno adatta a produrre geometrie molto complesse o dettagli intricati rispetto a processi come la fusione o la produzione additiva.Il processo è più adatto a pezzi con forme relativamente semplici.
-
Limitazioni del materiale:
- Non tutti i materiali sono adatti alla forgiatura.Alcune leghe e materiali possono non rispondere bene alle alte temperature e pressioni coinvolte nel processo, limitando la gamma di applicazioni.
-
Vincoli dimensionali:
- Le dimensioni dei pezzi forgiati sono limitate dalla capacità delle attrezzature di forgiatura.Pezzi estremamente grandi o pesanti possono richiedere attrezzature specializzate, con conseguente aumento dei costi e della complessità.
-
Finitura superficiale e tolleranze:
- I pezzi forgiati spesso richiedono una lavorazione supplementare per ottenere tolleranze e finiture superficiali precise.Pur riducendo i tempi di lavorazione, la forgiatura non elimina la necessità di operazioni secondarie.
-
Elevati costi iniziali di attrezzaggio:
In sintesi, la forgiatura è un processo produttivo molto efficace per la produzione di pezzi forti, durevoli e di forma personalizzata.I suoi vantaggi in termini di resistenza, proprietà metallurgiche e convenienza per la produzione di grandi volumi ne fanno una scelta privilegiata per molti settori.Tuttavia, i suoi limiti in termini di complessità geometrica, costi iniziali di attrezzaggio e idoneità dei materiali devono essere considerati con attenzione quando si sceglie il metodo di produzione appropriato per una determinata applicazione.
Tabella riassuntiva:
Aspetto | Vantaggi | Limitazioni |
---|---|---|
Forza e durata | Maggiore forza, tenacità e resistenza alla fatica grazie alla struttura a grani compressi. | Elevati costi iniziali di attrezzaggio, che lo rendono meno economico per la produzione di bassi volumi. |
Proprietà metallurgiche | Riduzione al minimo di difetti come porosità e segregazione della lega, migliorando l'uniformità del materiale. | Complessità geometrica limitata, non adatta a progetti molto complessi. |
Forme e dimensioni personalizzate | Capacità di produrre forme e dimensioni personalizzate per applicazioni specializzate. | Limitazioni dei materiali: non tutte le leghe sono adatte alla forgiatura. |
Riduzione dei tempi di lavorazione | La forma quasi netta riduce lo spreco di materiale e i tempi di lavorazione, con conseguente risparmio sui costi. | Vincoli di dimensione dovuti alla capacità delle attrezzature, che richiedono strumenti specializzati. |
Costo-efficacia | Economico per la produzione di grandi volumi grazie all'efficienza e alla riduzione degli scarti. | È necessaria una lavorazione supplementare per ottenere tolleranze e finiture superficiali precise. |
Volete saperne di più sulla forgiatura e su come può essere utile al vostro progetto? Contattate i nostri esperti oggi stesso per una consulenza personalizzata!