La colata sottovuoto e la colata centrifuga sono due metodi distinti utilizzati nella produzione, ciascuno con i propri vantaggi e limiti.La colata sottovuoto è particolarmente apprezzata per la sua capacità di produrre getti puliti e di alta qualità con impurità minime, che la rendono ideale per settori come quello aerospaziale e nucleare, dove l'integrità dei materiali è fondamentale.La colata centrifuga, invece, è nota per la sua efficienza nella produzione di componenti cilindrici con eccellenti proprietà meccaniche.La scelta tra i due metodi dipende dai requisiti specifici dell'applicazione, tra cui le proprietà del materiale, la geometria del componente e il volume di produzione.
Punti chiave spiegati:
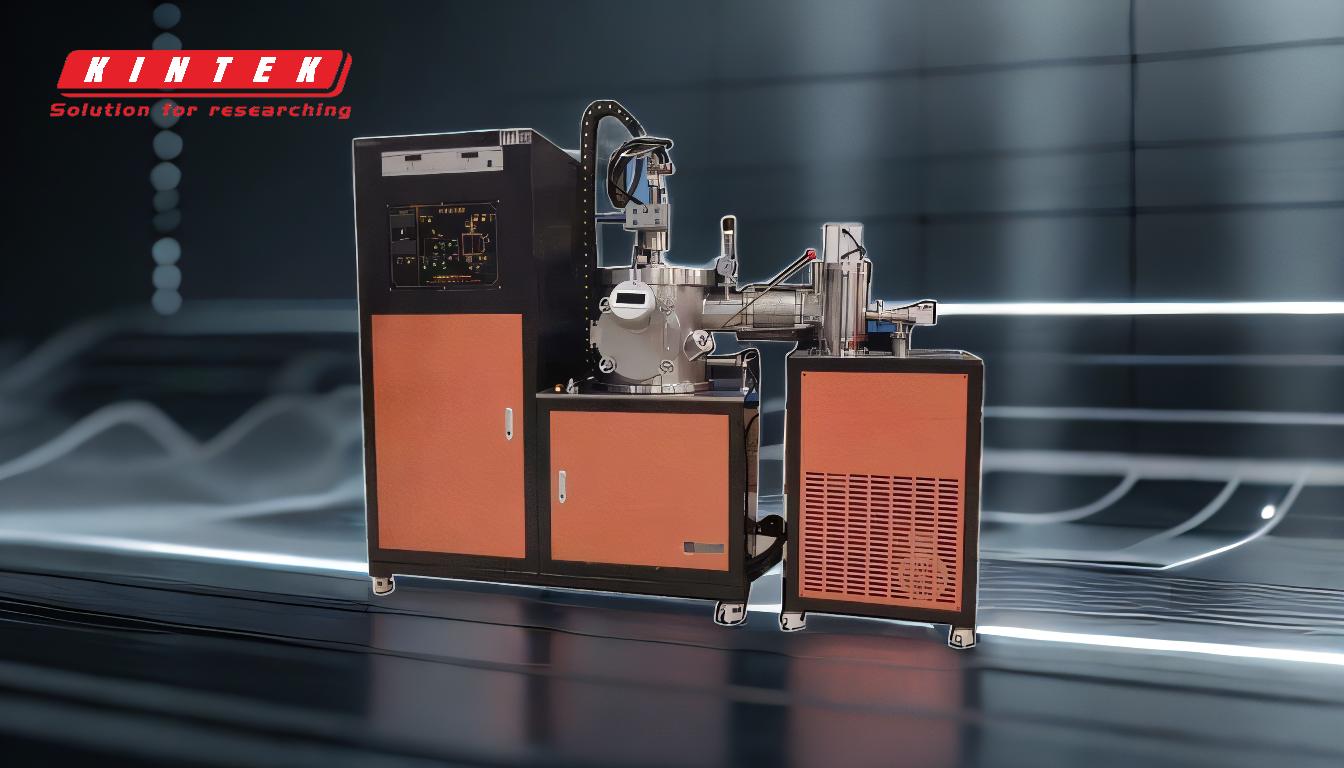
-
Pulizia e qualità dei materiali:
- Colata sotto vuoto:Questo metodo è rinomato per la produzione di getti con elevati livelli di pulizia.L'ambiente sotto vuoto impedisce l'ossidazione e la contaminazione, garantendo proprietà superiori del materiale.Ciò è particolarmente importante in settori come quello aerospaziale e nucleare, dove anche piccole impurità possono compromettere l'integrità dei componenti.
- Fusione centrifuga:Anche se la colata centrifuga può produrre getti di alta qualità, potrebbe non raggiungere lo stesso livello di pulizia della colata sotto vuoto.Il processo si basa sulla forza centrifuga per distribuire il metallo fuso, che a volte può portare a inclusioni o impurità intrappolate nella colata.
-
Idoneità all'applicazione:
- Colata sotto vuoto:Ideale per applicazioni che richiedono materiali di elevata purezza e geometrie complesse.È comunemente utilizzata nell'industria aerospaziale, nucleare e medica, dove l'integrità dei materiali è fondamentale.
- Fusione centrifuga:Ideale per la produzione di componenti cilindrici o simmetrici, come tubi e anelli.È ampiamente utilizzato nei settori automobilistico, navale e industriale.
-
Proprietà meccaniche:
- Colata sotto vuoto:L'ambiente controllato della colata sotto vuoto consente un controllo preciso della velocità di raffreddamento, che può migliorare le proprietà meccaniche dei getti.In questo modo si ottengono componenti con una forza, una duttilità e una resistenza alla fatica superiori.
- Fusione centrifuga:La forza centrifuga utilizzata in questo metodo aiuta a produrre getti con una struttura densa e a grana fine, che può migliorare le proprietà meccaniche come la resistenza alla trazione e all'usura.Tuttavia, le proprietà meccaniche potrebbero non essere così uniformi come quelle ottenute con la colata sotto vuoto.
-
Volume e costi di produzione:
- Colata sotto vuoto:Generalmente più costoso a causa della necessità di attrezzature specializzate e ambienti controllati.Si utilizza in genere per volumi di produzione medio-bassi, dove il costo è giustificato dalla necessità di ottenere getti di alta qualità.
- Fusione centrifuga:Più conveniente per i volumi di produzione elevati, soprattutto per i componenti con geometrie semplici.Il processo è relativamente semplice e non richiede lo stesso livello di controllo ambientale della colata sotto vuoto.
-
Complessità e flessibilità:
- Colata sotto vuoto:Offre una maggiore flessibilità in termini di complessità dei componenti che possono essere prodotti.Può gestire con facilità progetti intricati e sezioni a parete sottile.
- Fusione centrifuga:Limitato alle forme più semplici e simmetriche.Sebbene sia eccellente per la produzione di componenti uniformi e cilindrici, potrebbe non essere adatto a geometrie più complesse.
In conclusione, la scelta tra colata sotto vuoto e centrifuga dipende dai requisiti specifici dell'applicazione.La colata sotto vuoto è superiore per i componenti complessi e di elevata purezza, mentre la centrifuga è più conveniente per i volumi elevati e le geometrie semplici.Ogni metodo ha i suoi punti di forza e i suoi limiti e la decisione deve basarsi su una valutazione approfondita delle proprietà del materiale, del progetto del componente e delle esigenze di produzione.
Tabella riassuntiva:
Aspetto | Colata sotto vuoto | Colata centrifuga |
---|---|---|
Pulizia del materiale | Elevata pulizia, impurità minime, ideale per l'industria aerospaziale e nucleare. | Buona qualità, ma può presentare inclusioni dovute alla forza centrifuga. |
Idoneità all'applicazione | Ideale per geometrie complesse e di elevata purezza (aerospaziale, medicale). | Ideale per i componenti cilindrici (tubi, tubazioni, anelli). |
Proprietà meccaniche | Forza, duttilità e resistenza alla fatica superiori. | Struttura densa e a grana fine; buona resistenza alla trazione e all'usura. |
Volume e costo di produzione | Costoso, adatto a volumi medio-bassi. | Conveniente per la produzione di alti volumi. |
Complessità e flessibilità | Gestisce progetti intricati e sezioni a parete sottile. | Limitato a forme più semplici e simmetriche. |
Avete bisogno di aiuto per scegliere il metodo di fusione giusto per il vostro progetto? Contattate i nostri esperti oggi stesso per una consulenza personalizzata!