La sinterizzazione è un processo di produzione che trasforma i materiali in polvere in corpi solidi e densi applicando calore e pressione senza raggiungere il punto di fusione del materiale.Questo processo è ampiamente utilizzato in settori quali la metallurgia delle polveri, la ceramica e la plastica.Le fasi principali comprendono la preparazione della polvere compatta, l'applicazione della pressione per modellare il materiale, il riscaldamento per fondere le particelle e il raffreddamento e la solidificazione in una massa unificata.A seconda del materiale e delle proprietà desiderate, vengono impiegati diversi metodi, come la sinterizzazione convenzionale, la sinterizzazione al plasma di scintilla (SPS) e la sinterizzazione a microonde.La sinterizzazione aumenta la resistenza, la durata e la densità del materiale, rendendola essenziale per la produzione di componenti ad alte prestazioni.
Punti chiave spiegati:
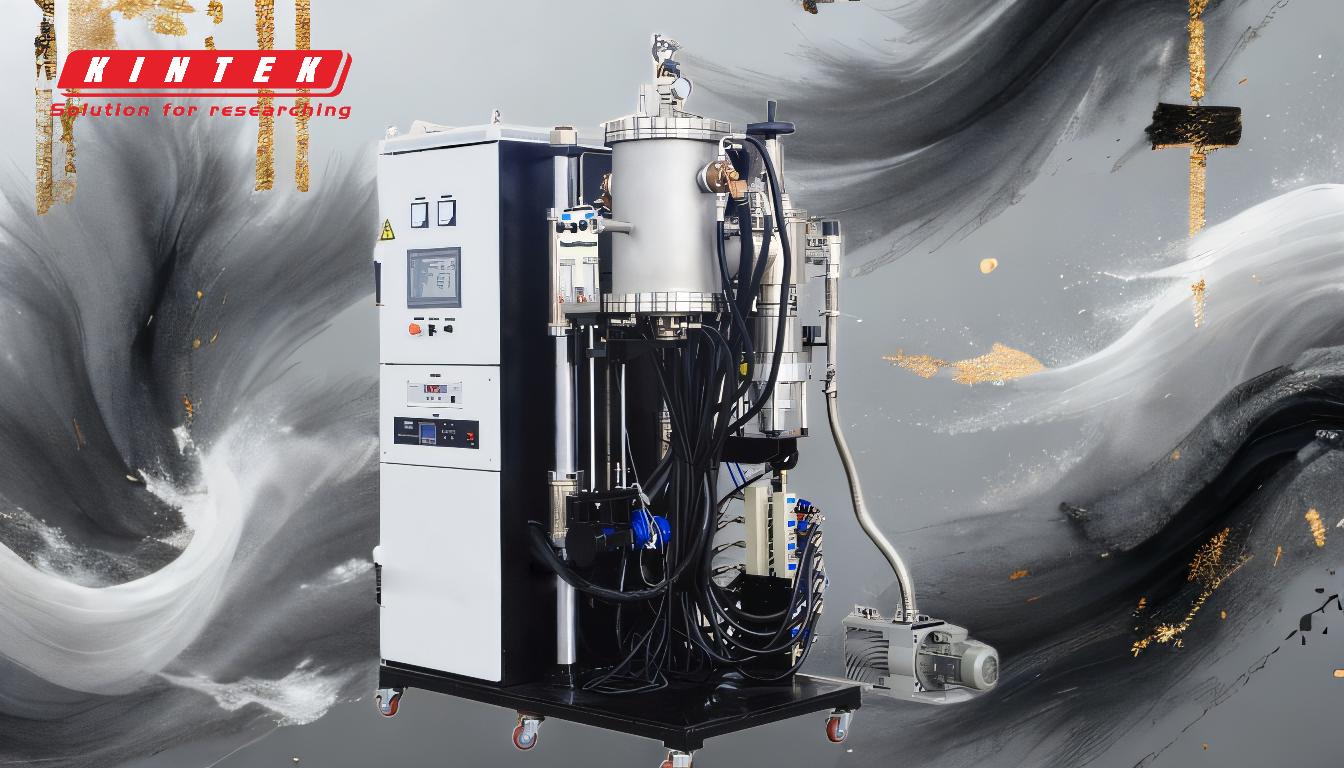
-
Definizione e scopo della sinterizzazione:
- La sinterizzazione è un processo che compatta e fonde materiali in polvere in una massa densa e solida utilizzando calore e pressione senza fondere il materiale.
- Viene utilizzata per migliorare le proprietà dei materiali, come la resistenza, la durata e la densità, rendendola ideale per applicazioni nella metallurgia delle polveri, nella ceramica e nella plastica.
-
Fasi del processo di sinterizzazione:
-
Preparazione della polvere compatta:
- La materia prima viene preparata in polvere e mescolata con agenti di accoppiamento, se necessario.
- La polvere viene poi compattata nella forma desiderata utilizzando metodi come la pressatura a freddo, la stampa 3D o altre tecniche di formatura.
-
Applicazione della pressione:
- La pressione viene applicata alla polvere compatta per ottenere la forma e la densità iniziale richieste.
-
Riscaldamento e consolidamento:
- Il materiale compattato viene riscaldato a una temperatura appena inferiore al suo punto di fusione, consentendo alle particelle di fondersi insieme.
- Questa fase attiva i meccanismi di diffusione, facendo migrare gli atomi attraverso i confini delle particelle e formando legami forti.
-
Raffreddamento e solidificazione:
- Dopo il riscaldamento, il materiale viene raffreddato, consentendogli di solidificarsi in una massa unificata e densa con porosità ridotta.
-
Preparazione della polvere compatta:
-
Tipi di metodi di sinterizzazione:
-
Sinterizzazione convenzionale:
- Il metodo più comune, che prevede il riscaldamento del materiale in un forno a temperature e atmosfere controllate.
-
Sinterizzazione al plasma di scintilla (SPS):
- Tecnica di sinterizzazione rapida che utilizza correnti elettriche pulsate per generare calore e pressione simultaneamente, riducendo i tempi di lavorazione.
-
Sinterizzazione a microonde:
- Utilizza l'energia delle microonde per riscaldare il materiale in modo uniforme, ottenendo spesso una sinterizzazione più rapida e migliori proprietà del materiale.
-
Sinterizzazione convenzionale:
-
Materiali adatti alla sinterizzazione:
- La sinterizzazione è applicabile a un'ampia gamma di materiali, tra cui metalli (ad esempio, tungsteno, molibdeno), ceramiche e plastiche.
- È particolarmente utile per i materiali con punti di fusione elevati, dove i metodi tradizionali di fusione e colata non sono praticabili.
-
Vantaggi della sinterizzazione:
-
Proprietà del materiale migliorate:
- La sinterizzazione aumenta la forza, la durezza e la resistenza all'usura riducendo la porosità e creando una struttura densa.
-
Costo-efficacia:
- Il processo riduce al minimo gli sprechi di materiale e consente di produrre forme complesse con una lavorazione minima.
-
Versatilità:
- La sinterizzazione può essere adattata a diversi materiali e applicazioni, rendendola una tecnica di produzione versatile.
-
Proprietà del materiale migliorate:
-
Applicazioni della sinterizzazione:
-
Metallurgia delle polveri:
- Utilizzato per produrre componenti metallici come ingranaggi, cuscinetti e parti di automobili.
-
Produzione di ceramica:
- Essenziale per la creazione di componenti ceramici ad alta resistenza utilizzati nell'elettronica, nell'aerospaziale e nei dispositivi medici.
-
Plastica e materiali compositi:
- Utilizzata per produrre parti in plastica durevoli con proprietà meccaniche migliorate.
-
Metallurgia delle polveri:
Conoscendo il processo di sinterizzazione e i suoi vari metodi, i produttori possono ottimizzare le proprietà dei materiali e produrre componenti di alta qualità per diversi settori industriali.
Tabella riassuntiva:
Aspetto | Dettagli |
---|---|
Definizione | Compatta e fonde materiali in polvere utilizzando calore e pressione senza fonderli. |
Passi chiave |
1.Preparare la polvere compatta
2.Applicare la pressione 3.Riscaldare e consolidare 4.Raffreddare e solidificare |
Metodi | Convenzionale, plasma a scintilla (SPS), microonde |
Materiali | Metalli (tungsteno, molibdeno), ceramica, plastica |
Vantaggi | Maggiore resistenza, economicità e versatilità |
Applicazioni | Metallurgia delle polveri, produzione di ceramica, materie plastiche e compositi |
Siete pronti a migliorare le proprietà dei vostri materiali con la sinterizzazione? Contattate i nostri esperti oggi per saperne di più!