La sinterizzazione è un processo critico nella metallurgia delle polveri e nella produzione di ceramiche, in cui i materiali in polvere vengono trasformati in corpi solidi e densi mediante l'applicazione di calore e pressione, in genere al di sotto del punto di fusione del materiale.Questo processo prevede diverse fasi, tra cui la formazione di un pezzo verde, la rimozione dell'agente legante e la sinterizzazione vera e propria, in cui le particelle si fondono insieme.La macchina di sinterizzazione svolge un ruolo fondamentale nel controllo della temperatura, dell'atmosfera e della pressione per garantire il raggiungimento delle proprietà desiderate del materiale.I componenti chiave del processo di sinterizzazione comprendono materie prime come polveri contenenti ferro, agenti di fusione e combustibile, che devono soddisfare criteri specifici per una sinterizzazione efficace.
Punti chiave spiegati:
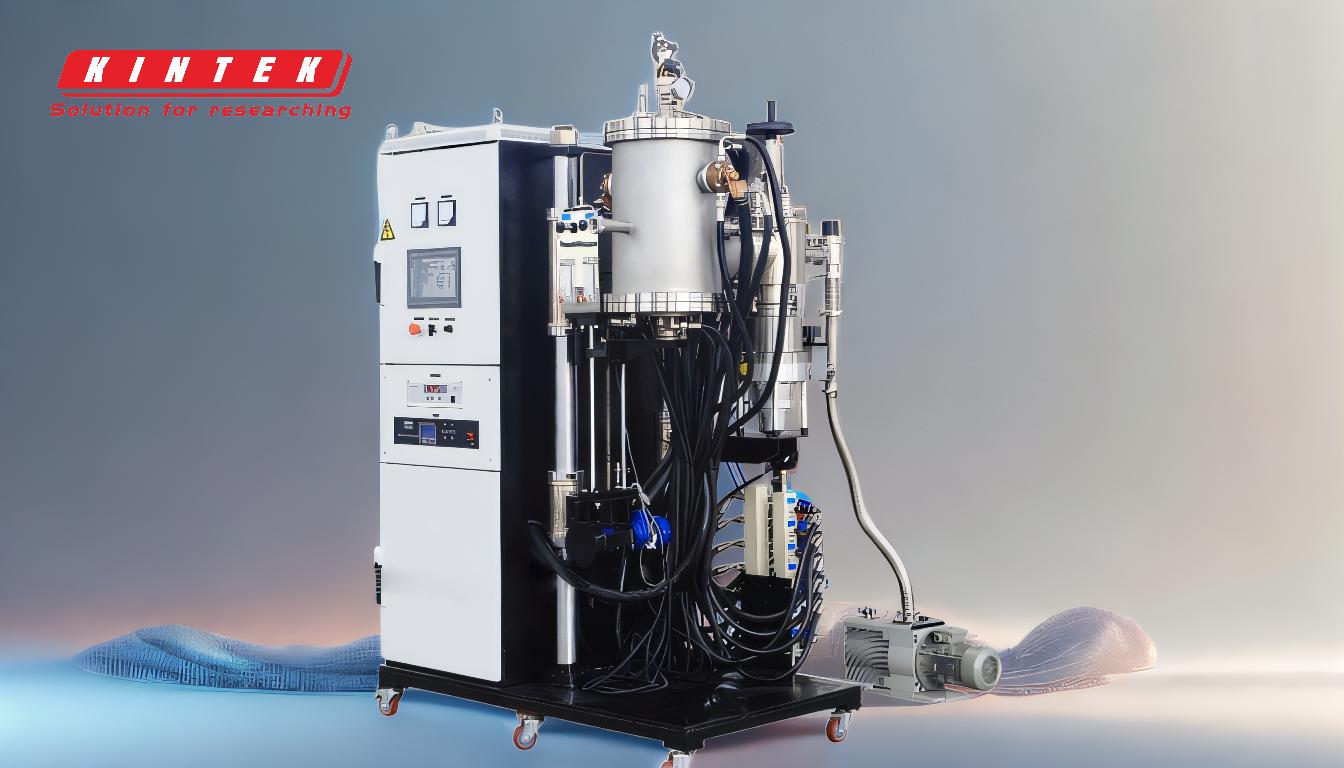
-
Definizione e scopo della sinterizzazione:
- La sinterizzazione è un processo che compatta e forma una massa solida di materiale applicando calore o pressione senza raggiungere il punto di fusione del materiale.
- Viene utilizzato per creare materiali densi e ad alta resistenza da forme in polvere, comunemente nella metallurgia delle polveri e nella produzione di ceramiche.
-
Fasi del processo di sinterizzazione:
- Formazione del pezzo verde: Una miscela di polvere primaria e un agente legante (come cera o polimero) viene modellata nella forma desiderata.
- Rimozione dell'agente legante: Durante il riscaldamento, l'agente legante evapora o brucia.
- Sinterizzazione: La temperatura viene aumentata fino a un punto in cui le particelle iniziano a fondersi in superficie, sia attraverso una fusione parziale che tramite un agente legante intermedio.
-
Componenti delle materie prime di sinterizzazione:
- Materie prime contenenti ferro: Includono polvere di minerale ad alto contenuto di ferro, concentrato di ferro e altri materiali ricchi di ferro.
- Agenti di fusione: Devono avere un elevato contenuto di CaO valido, basse impurità, contenuto specifico di acqua e dimensioni delle particelle.
- Combustibile: In genere comprende polvere di coke e carbone senza fumo, che deve avere un alto contenuto di carbonio fisso, basse ceneri e basso contenuto di zolfo.
-
Fasi fondamentali dell'operazione di sinterizzazione:
- Panno: Comporta la posa del fondo e la miscelazione dei materiali sulla macchina di sinterizzazione.
- Accensione: La superficie dello scomparto sul carrello viene accesa e mantenuta a un'adeguata temperatura elevata.
- Sinterizzazione: Richiede un controllo preciso del volume d'aria, del vuoto, dello spessore dello strato, della velocità e del punto finale di sinterizzazione per garantire risultati ottimali.
-
Forno di sinterizzazione ad atmosfera:
- Questo tipo di forno controlla l'atmosfera (come azoto o argon) per ottimizzare l'ambiente di sinterizzazione.
- Comprende dispositivi di riscaldamento, meccanismi di pressione, camere di sinterizzazione e sistemi di controllo del gas.
- L'atmosfera controllata consente la migrazione del materiale, il movimento dei confini dei grani, l'eliminazione dei pori e il ritiro, dando vita a un corpo ceramico denso con specifiche proprietà di resistenza.
-
Vantaggi della sinterizzazione:
- Produce materiali con proprietà meccaniche migliorate, come una maggiore resistenza e durata.
- Permette di creare forme e strutture complesse che sarebbero difficili da ottenere con i processi di fusione e colata tradizionali.
- È adatto a materiali con punti di fusione estremamente elevati, come il tungsteno e il molibdeno.
Comprendendo questi punti chiave, si può apprezzare la complessità e la precisione richieste nel processo di sinterizzazione, nonché il ruolo critico che le macchine di sinterizzazione svolgono per ottenere le proprietà desiderate del materiale.
Tabella riassuntiva:
Aspetto | Dettagli |
---|---|
Definizione | Compattazione di materiali in polvere utilizzando calore/pressione al di sotto del punto di fusione. |
Fasi | Formazione del pezzo verde, rimozione dell'agente legante e fusione delle particelle. |
Componenti chiave | Polveri contenenti ferro, agenti di fusione e combustibile. |
Operazione di sinterizzazione | Panno, accensione e controllo preciso di aria, vuoto e temperatura. |
Sinterizzazione in atmosfera | Ambiente controllato per la migrazione del materiale, l'eliminazione dei pori e il ritiro. |
Vantaggi | Maggiore resistenza, forme complesse e idoneità ai materiali ad alta fusione. |
Scoprite come la sinterizzazione può trasformare il vostro processo di produzione... contattate i nostri esperti oggi stesso !