Introduzione
Indice dei contenuti
La pressatura isostatica è un processo produttivo essenziale, utilizzato per produrre pezzi complessi e di alta qualità. Due metodi comuni di pressatura isostatica sono la pressatura isostatica a sacco umido e la pressatura isostatica a sacco secco. In questo post esploreremo e confronteremo questi due metodi per comprenderne le differenze, i vantaggi, i limiti e l'idoneità a diversi scenari. Che siate alle prime armi con la pressatura isostatica o alla ricerca di un metodo alternativo, questo studio comparativo vi aiuterà a prendere una decisione consapevole. Quindi, tuffiamoci ed esploriamo il mondo della pressatura isostatica a sacchi umidi e a sacchi asciutti!
Informazioni sulla pressatura isostatica a freddo
Introduzione alla pressatura isostatica a freddo
La pressatura isostatica a freddo (CIP) è una tecnica utilizzata per formare materiali in polvere a temperatura ambiente applicando una pressione alla polvere. La pressione è solitamente compresa tra 100-600 MPa e il processo viene eseguito utilizzando un mezzo liquido come acqua, olio o una miscela di glicole. L'obiettivo del CIP è ottenere un pezzo "grezzo" con una resistenza sufficiente per la manipolazione e la lavorazione, che può poi essere ulteriormente sinterizzato per ottenere la resistenza finale.
Per i metalli, la pressatura isostatica a freddo può raggiungere una densità teorica di circa il 100%, mentre per le polveri ceramiche la densità può arrivare a circa il 95%. Questa tecnologia viene comunemente utilizzata per produrre grezzi da sottoporre a ulteriori processi di sinterizzazione o di pressatura isostatica a caldo.
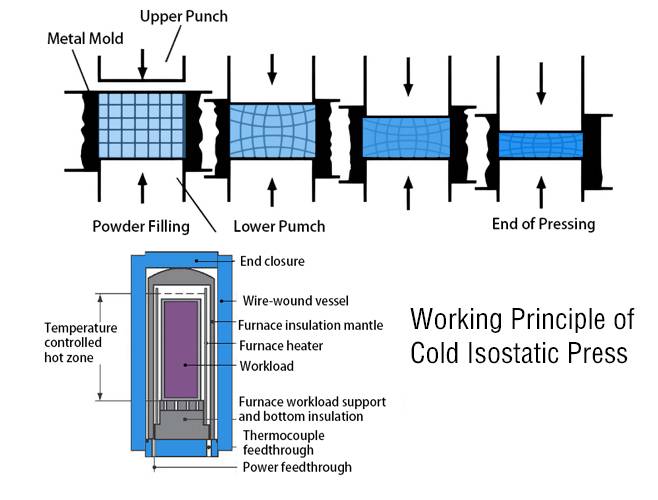
Differenziazione tra il metodo del sacco umido e il metodo del sacco secco
La pressatura isostatica a freddo può essere ulteriormente suddivisa in due metodi: il metodo del sacco umido e il metodo del sacco secco.
Metodo del sacco umido
Nel metodo del sacco umido, il materiale in polvere viene racchiuso in un sacco flessibile. Questo sacco viene poi immerso in un liquido ad alta pressione all'interno di un recipiente a pressione. La pressione isostatica viene applicata alle superfici esterne dello stampo, comprimendo la polvere nella forma desiderata. Il metodo del sacco umido è ideale per la produzione di pezzi dalle forme complesse e può essere utilizzato sia per la produzione di piccole che di grandi quantità. Inoltre, consente la pressatura di prodotti di grandi dimensioni.
Metodo del sacco a secco
Il metodo del sacco a secco, invece, prevede la creazione di uno stampo integrato nel recipiente a pressione stesso. La polvere viene aggiunta allo stampo, che viene poi sigillato. Si applica la pressione e il pezzo viene espulso una volta completata la compattazione. Il metodo del sacco a secco elimina la necessità della fase di immersione separata richiesta dal metodo del sacco umido, facilitando l'automazione.
Entrambi i metodi hanno i loro vantaggi e sono adatti a diverse applicazioni. La scelta tra i due metodi dipende dagli obiettivi specifici del progetto e dalle caratteristiche dei materiali coinvolti.
In sintesi, la pressatura isostatica a freddo è una tecnica preziosa per la formatura di materiali in polvere a temperatura ambiente. Consente di produrre pezzi ad alta densità e può essere utilizzata sia per i metalli che per le ceramiche. I metodi a sacco umido e a sacco asciutto offrono approcci diversi per ottenere la compattazione desiderata, con il metodo a sacco umido adatto a forme complesse e alla produzione di grandi quantità. La comprensione delle differenze tra questi metodi può aiutare a determinare l'approccio più appropriato per le vostre esigenze specifiche.
Pressatura isostatica del sacco umido
Processo di pressatura isostatica in sacchi umidi
Nella pressatura isostatica in sacchi umidi, la polvere viene riempita in uno stampo e sigillata ermeticamente all'esterno del recipiente di pressione. Lo stampo viene quindi immerso nel fluido in pressione all'interno del recipiente. La pressione isostatica viene applicata alla superficie esterna dello stampo, comprimendo la polvere in una massa solida. Questo processo è più lento rispetto ad altri tipi di pressatura isostatica a freddo e richiede dai 5 ai 30 minuti. Tuttavia, i progressi delle pompe ad alto volume e dei meccanismi di caricamento possono contribuire a velocizzare il processo.
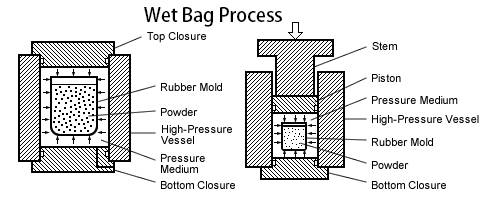
Vantaggi della pressatura isostatica a sacchi umidi
La pressatura isostatica in sacchi umidi offre diversi vantaggi. È altamente applicabile e adatta alla ricerca sperimentale e alla produzione di piccoli lotti. Può pressare simultaneamente più pezzi di forma diversa in un unico cilindro ad alta pressione e produrre pezzi grandi e complessi. Il processo di produzione è breve e conveniente. I processi di wet bag consentono anche di progettare forme piuttosto complesse in stampi elastomerici, ottenendo alte densità compatte.
Scenari ideali per l'utilizzo della pressatura isostatica con sacco umido
La pressatura isostatica a sacco umido è particolarmente adatta alla produzione di pezzi di grandi dimensioni. È comunemente utilizzata nelle industrie in cui sono richieste densità compatte elevate e in cui le forme complesse non possono essere compattate con presse monoassiali. Tuttavia, è importante notare che il carico e lo scarico degli stampi può limitare l'automazione e ridurre la produttività della pressatura a sacco umido. Anche il costo degli utensili e la complessità del processo sono maggiori rispetto alla pressatura monoassiale.
In sintesi, la pressatura isostatica in sacchi umidi offre un metodo versatile ed efficiente per la produzione di pezzi grandi e complessi con densità compatte elevate. È particolarmente vantaggioso per la ricerca sperimentale, la produzione di piccoli lotti e le industrie che richiedono forme complesse. Pur presentando alcune limitazioni in termini di automazione e produttività, i progressi tecnologici continuano a migliorare l'efficienza della pressatura isostatica a sacco umido.
Pressatura isostatica con sacchi a secco
Processo di pressatura isostatica con sacco a secco
La pressatura isostatica con sacchi a secco è un metodo di produzione utilizzato per piccoli pezzi con forme assialsimmetriche. È comunemente utilizzato nella produzione di corpi ceramici di alta qualità per le candele di accensione. Il processo prevede la compattazione di una polvere secca o semi-secca in uno stampo elastomerico immerso in un liquido pressurizzato. La polvere viene modellata con l'aiuto di utensili rigidi, come un mandrino in acciaio, abbinato allo stampo elastomerico flessibile. Le pressioni di formatura tipiche per la ceramica vanno da 21 a 210 MPa (3000-30000 psi). Uno dei principali vantaggi della pressatura isostatica a secco è che l'attrezzatura in gomma è integrata nell'apparecchiatura, eliminando la necessità di fasi separate di immersione e rimozione. Ciò comporta una maggiore facilità di automazione e velocità di produzione.
Vantaggi dell'utilizzo della pressatura isostatica a secco
La pressatura isostatica a secco offre diversi vantaggi nel processo di produzione. In primo luogo, consente di produrre corpi ceramici di alta qualità, in particolare per le candele di accensione. Lo stampo integrato e l'utensileria in gomma facilitano l'automazione, consentendo di ottenere tassi di produzione più elevati. Inoltre, il processo garantisce una densità uniforme e basse tensioni intrappolate nei pezzi compattati, con conseguente minima distorsione durante la cottura. Ciò riduce la necessità di una successiva lavorazione, che può essere difficile e costosa. Nel complesso, la pressatura isostatica a secco offre efficienza, precisione ed economicità per i pezzi di piccole dimensioni con forme asimmetriche.
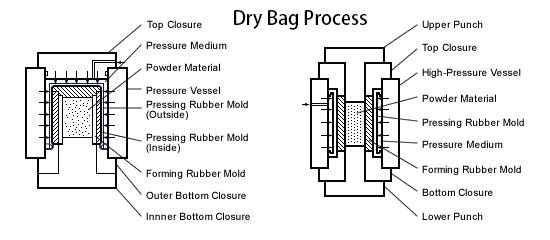
Scenari ideali per l'utilizzo della pressatura isostatica a secco
La pressatura isostatica con sacchi a secco è un metodo di produzione ideale per la produzione di piccoli pezzi con forme assialsimmetriche. È particolarmente indicato per la produzione di corpi ceramici di alta qualità per le candele di accensione. L'integrazione di utensili in gomma nell'apparecchiatura consente una facile automazione, rendendolo adatto alla produzione di grandi volumi. Questo metodo è efficiente, preciso ed economico, e rappresenta la scelta preferita per le industrie che richiedono piccoli pezzi con forme asimmetriche.
Limiti della pressatura isostatica a secco
Sebbene la pressatura isostatica a secco offra numerosi vantaggi, presenta anche alcune limitazioni. Una limitazione è rappresentata dall'attrito sul lato dello stampo che non subisce la compressione del liquido pressurizzante. Ciò può comportare una minore precisione delle superfici pressate adiacenti al sacco flessibile, rispetto ad altri metodi di pressatura come la pressatura meccanica o l'estrusione. Ciò può richiedere una successiva lavorazione per ottenere la finitura superficiale desiderata. Inoltre, il processo dei sacchi a secco presenta maggiori limitazioni di forma e dimensione rispetto ad altri metodi, il che può richiedere una lavorazione verde per sviluppare le caratteristiche superficiali necessarie per determinate applicazioni.
In conclusione, la pressatura isostatica a secco è un valido metodo di produzione per piccoli pezzi con forme assialsimmetriche, in particolare nella produzione di corpi ceramici di alta qualità per candele di accensione. Offre efficienza, precisione e convenienza economica, e rappresenta la scelta ideale per le industrie che richiedono tali componenti. Tuttavia, è importante considerare i limiti del processo, come la minore precisione delle superfici pressate e le limitazioni di forma e dimensione, quando si determina la sua idoneità per applicazioni specifiche.
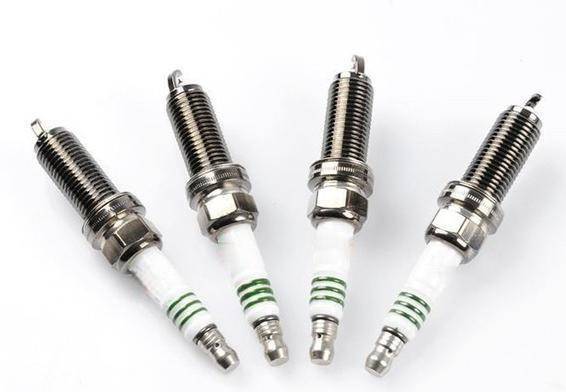
Confronto tra pressatura isostatica a sacco umido e a sacco secco
Confronto tra processo produttivo e costi
La pressatura isostatica in sacchi umidi prevede che la polvere venga inserita in uno stampo di formatura e quindi collocata in un cilindro ad alta pressione per la pressatura dopo la sigillatura. Durante la pressatura, lo stampo è completamente immerso nel liquido e a diretto contatto con il mezzo di trasmissione della pressione. Questo metodo è adatto alla ricerca sperimentale e alla produzione di piccoli lotti. Consente la pressatura simultanea di più pezzi di forma diversa in un unico cilindro ad alta pressione, il che lo rende ideale per la produzione di pezzi grandi e complessi. Il processo di produzione è breve ed economico.
La variante a sacco secco della pressatura isostatica prevede la creazione di uno stampo integrato nel recipiente di pressione. In questo processo, la polvere viene aggiunta allo stampo, viene sigillata, viene applicata la pressione e quindi il pezzo viene espulso. Il metodo del sacco a secco consente un'automazione più semplice rispetto al metodo del sacco a umido, poiché gli stampi sono integrati nel recipiente. È più adatto alla produzione di pezzi piccoli e offre tassi di produzione più elevati.
Confronto tra automazione e ciclo operativo
Il metodo del sacco umido richiede il carico e lo scarico degli stampi, il che riduce la produttività e limita l'automazione. D'altra parte, il metodo del sacco a secco, con i suoi stampi integrati, consente un'automazione più semplice e tassi di produzione più elevati. Il ciclo operativo della pressatura isostatica a sacco umido prevede la rimozione dello stampo dal recipiente in pressione, il recupero del pezzo e la ripetizione del processo. Nel metodo del sacco a secco, lo stampo viene sigillato, si applica la pressione e il pezzo viene espulso.
Confronto dell'idoneità per diversi volumi di produzione
La pressatura isostatica a sacco umido è particolarmente adatta alla ricerca sperimentale e alla produzione di piccoli lotti. Consente la pressatura simultanea di più pezzi di forma diversa in un unico cilindro ad alta pressione, il che lo rende adatto alla produzione di pezzi grandi e complessi. Il metodo del sacco a secco, invece, è più adatto alla produzione di pezzi più piccoli e offre tassi di produzione più elevati.
Limiti di dimensione e forma del prodotto a confronto
La pressatura isostatica a sacco umido è più adatta alla produzione di pezzi di grandi dimensioni rispetto al metodo a sacco secco. Ciò è dovuto alla possibilità di pressare simultaneamente più pezzi di forma diversa in un unico cilindro ad alta pressione. Tuttavia, il carico e lo scarico degli stampi nel metodo del sacco umido riduce la produttività e limita l'automazione. Il metodo del sacco a secco, con i suoi stampi integrati, offre un'automazione più semplice e tassi di produzione più elevati. Entrambi i tipi di pressatura isostatica hanno costi di attrezzaggio e complessità di processo più elevati rispetto alla pressatura monoassiale.
La pressatura isostatica, che sia a sacco umido o a secco, viene spesso scelta per ottenere densità compatte elevate e per accedere a forme che non possono essere compattate con presse monoassiali. Il metodo del sacco umido consente di progettare forme piuttosto complesse negli stampi elastomerici. I processi a sacco umido offrono anche il vantaggio di densità più elevate, poiché comportano un attrito molto ridotto. Il metodo del sacco a secco è in vantaggio per quanto riguarda l'automazione e la velocità di produzione.
In generale, la scelta tra la pressatura isostatica con sacchi a umido e quella con sacchi a secco dipende dai requisiti specifici del processo produttivo, come le dimensioni dei pezzi desiderati, la forma, il volume di produzione e il livello di automazione.
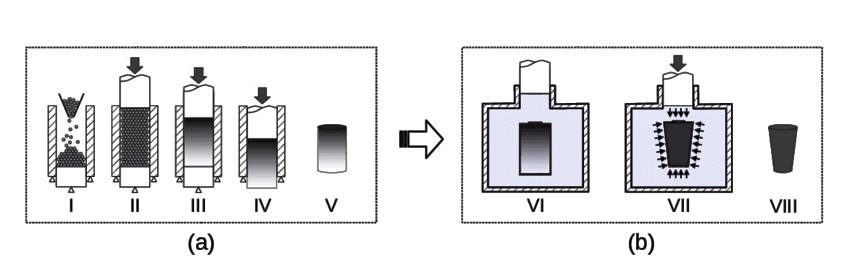
Conclusioni
In conclusione, sia la pressatura in sacchi umidisia la pressatura isostatica e la pressatura isostatica a secco presentano vantaggi e limiti. La pressatura isostatica a sacco umido è ideale per le situazioni in cui è richiesta una pressione più elevata e offre una migliore uniformità e densità del prodotto finale. D'altro canto, la pressatura isostatica a secco è più adatta a volumi di produzione ridotti e offre tempi di ciclo più rapidi. Tuttavia, presenta limitazioni in termini di dimensioni e forma del prodotto. In definitiva, la scelta tra i due metodi dipende dai requisiti e dai vincoli specifici del processo produttivo.
Se siete interessati a questo prodotto, potete consultare il nostro sito web aziendale:.https://kindle-tech.com/product-categories/isostatic-pressInsistiamo sempre sul principio della qualità prima di tutto. Durante il processo di produzione, controlliamo rigorosamente ogni fase del processo, utilizzando materiali di alta qualità e tecnologie di produzione avanzate per garantire la stabilità e la durata dei nostri prodotti. per assicurare che le loro prestazioni soddisfino gli standard più elevati. Crediamo che solo fornendo ai clienti una qualità eccellente possiamo conquistare la loro fiducia e la loro collaborazione a lungo termine.
CONTATTATECI PER UNA CONSULENZA GRATUITA
I prodotti e i servizi di KINTEK LAB SOLUTION sono stati riconosciuti da clienti di tutto il mondo. Il nostro personale sarà lieto di assistervi per qualsiasi richiesta. Contattateci per una consulenza gratuita e parlate con uno specialista del prodotto per trovare la soluzione più adatta alle vostre esigenze applicative!