Overview of the Manual Hydraulic Pellet Press
Table of Contents
Application of the press in preparing pellets for spectral analyses
A manual hydraulic pellet press is a valuable tool in the laboratory for preparing pellets with a smooth and homogeneous surface for spectral analyses. It is commonly used in applications such as X-ray fluorescence analysis or infrared spectroscopy for elemental analysis. The press is ideal for manufacturing high-quality pellets of solid samples in a fast and easy manner.
The press is frequently used in conjunction with pressing tools of various diameters, including 40 mm, 32 mm, 15 mm, and 12 mm. These tools allow for the preparation of pellets of different sizes and can accommodate a range of sample types. The variable pressure force of the press, which can go up to 250 kN, ensures that the desired level of compression is achieved for accurate spectral analyses.
The manual operation of the press is simple and convenient. The press features a hand lever that allows for easy application of pressure, and a clearly designed pressure force display in 10 kN steps. This makes it easy to monitor and control the pressure during the pellet preparation process. Additionally, the press has a single-stage piston stroke of up to 25 mm, which further enhances its efficiency and effectiveness.
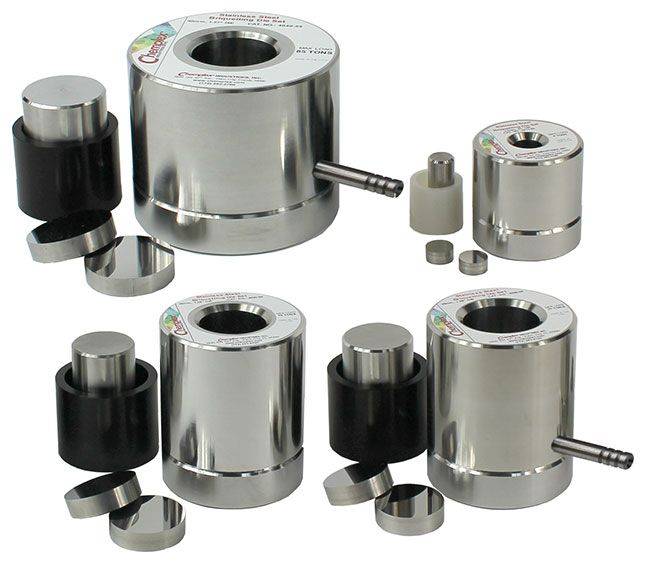
Benefits in manufacturing solid and highly permeable pellets
One of the key benefits of using a manual hydraulic pellet press is the ability to manufacture solid and highly permeable pellets. The press is designed to exert a large amount of force, which ensures that the pellets are tightly compacted and have a smooth surface. This is crucial for achieving accurate and reliable results in spectral analyses.
The press also offers the advantage of easy cleaning. Its solid and compact design, coupled with impact-resistant cladding, makes it durable and resistant to damage. This allows for easy maintenance and cleaning of the press, ensuring that it remains in optimal condition for consistent and high-quality pellet production.
Furthermore, the manual hydraulic pellet press features automatic pressure relief in case of overstress. This safety feature helps to prevent any damage to the press or the pellets being prepared. It provides peace of mind during the pellet preparation process and allows for efficient and worry-free operation.
In summary, the manual hydraulic pellet press is a versatile and reliable tool for preparing pellets for spectral analyses. Its ease of use, variable pressure force, and ability to manufacture solid and highly permeable pellets make it an essential equipment in any laboratory setting. Whether it is for FTIR, KBr, or XRF sample preparation, the manual hydraulic pellet press provides accurate and consistent results.
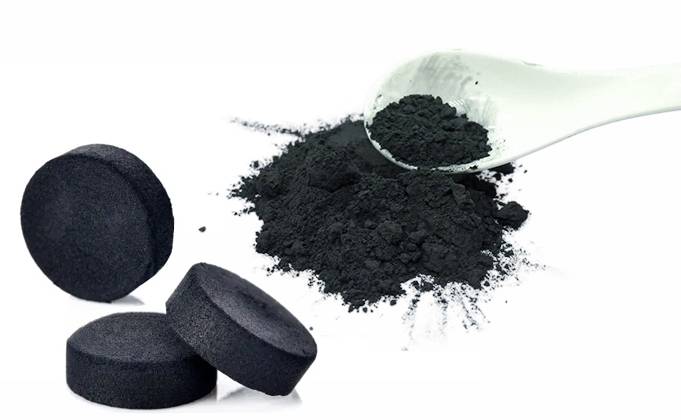
Features of the Pellet Press
Availability of pressing tools in different diameters
The pellet press offers a range of pressing tools with different diameters. This allows for the production of pellets with precise diameters, ranging from very thin to over 2 inches in length.
Variable pressure force up to 250 kN
The pellet press provides a variable pressure force of up to 250 kilonewtons (kN). This allows for flexibility in the compression of materials, ensuring optimal pellet formation.
Clearly designed pressure force display
The pellet press features a clearly designed pressure force display. This display shows the pressure force in 10 kN steps, allowing for easy monitoring and adjustment during the pellet production process.
Ease of operation and cleaning
The pellet press is designed for ease of operation and cleaning. It can be operated via a hand lever, making it simple to use. Additionally, all contact parts can be easily dismantled for cleaning, ensuring hygienic pellet production.
Single-stage piston stroke
With a single-stage piston stroke of up to 25 mm, the pellet press allows for efficient pellet formation. This stroke length ensures that the pellets are properly compressed and have a smooth, homogeneous surface.
Automatic pressure relief in case of overstress
To ensure safety during operation, the pellet press is equipped with automatic pressure relief in case of overstress. This feature protects the press from damage and prevents accidents.
Solid and compact design with impact-resistant cladding
The pellet press has a solid and compact design, making it durable and long-lasting. It is built with impact-resistant cladding, ensuring that it can withstand the rigors of pellet production.
In summary, the pellet press offers a range of features that make it a versatile and reliable tool for pellet production. With its availability of pressing tools in different diameters, variable pressure force, ease of operation and cleaning, single-stage piston stroke, automatic pressure relief, and solid and compact design, it provides an efficient and effective solution for producing high-quality pellets. Whether you need to produce pellets for material science research, lamination, or electrode punching, the pellet press is a valuable addition to any lab or production facility.
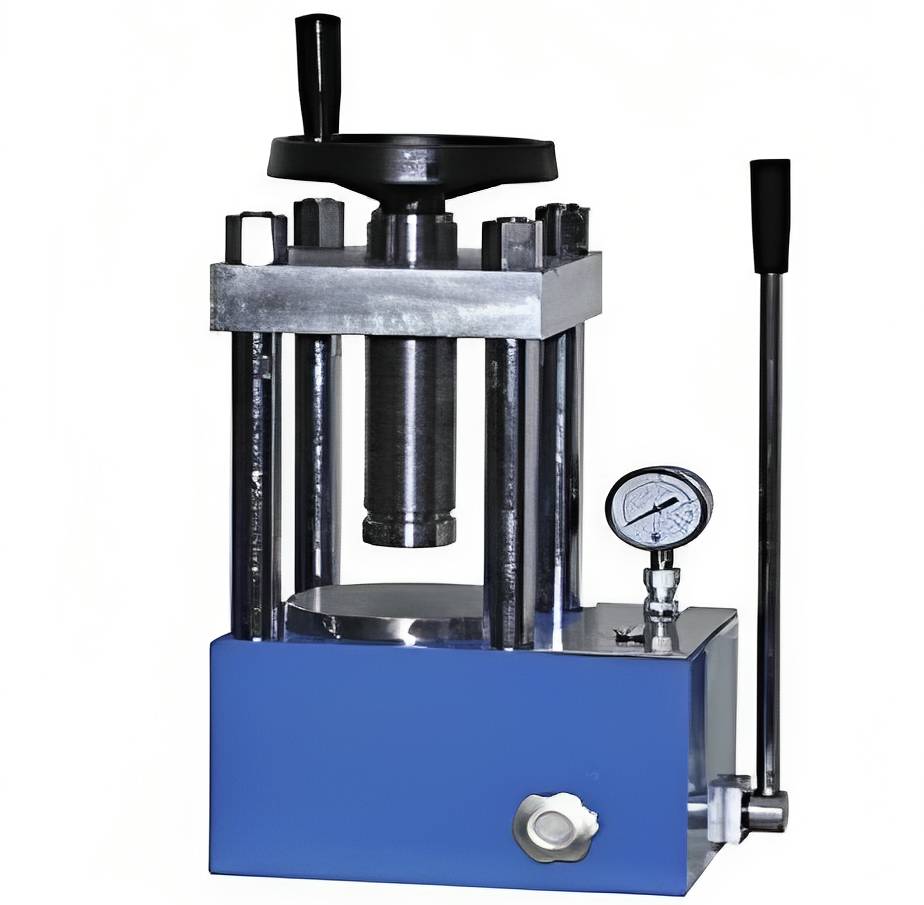
Operating the Pellet Press
Steps in filling the sample
To operate a manual hydraulic press, first make sure that the area around the press is clear and free of obstructions. Then, place a workpiece – e.g. a pellet die containing a sample material – on the piston. It is critical that the workpiece is centered on the piston.
Next, slowly turn the leadscrew at the top of the press to bring the nose of the leadscrew onto the top of the workpiece. Now, use the handle to pump hydraulic oil into the piston and start applying a load. Continue pumping until the desired load is reached. Once the desired load has been achieved, turn the release valve to release the pressure.
The procedure is the same no matter what object has been placed in the press. Paying careful attention to the positioning of the work and the load that has been applied is key to success.
Securing the magnetically-held door
The Pellet Press from KinTek is equipped with a magnetically-held door that securely closes during operation. This ensures that the sample material remains contained within the press and prevents any contamination or spillage. Simply close the door and the powerful magnet will hold it securely in place.
Building up the desired pressure with the hand lever
The Pellet Press operates by applying pressure through a hand lever. By exerting force on the lever, the mechanical advantage of the press system increases, resulting in a higher pressure being applied to the sample material. The press is designed to provide a steadily increasing mechanical advantage up to a ratio of approximately 50 to 1 at the end of the stroke. This means that a force of 20 pounds applied to the lever can develop approximately 1000 pounds on the press ram, which is sufficient to produce firm pellets from most powdered materials without the need for adding a binder.
To build up the desired pressure, simply apply force to the hand lever. The press will respond accordingly, compressing the sample material into a pellet or tablet form. It is important to apply consistent and controlled force to ensure uniformity in the pellets produced.
The Pellet Press from KinTek is a compact, hand-operated press that can be used anywhere in the laboratory. It requires very little bench space and no fixed mounting. The press produces uniform pellets in a polished die and ejects them smoothly into a receiver without incidents of contamination.
For smaller pellets with a diameter of less than 8 mm, it is recommended to use a smaller press to ensure accuracy in the force applied. With a smaller press, you have more control and can better gauge the force being applied. Using a 40 Ton press for a 6 mm die set, for example, can make it difficult to accurately apply the desired force, as a single pump of the handle can quickly exceed the maximum force for the smaller die. Planning ahead and knowing the desired force before pressing is crucial to avoid errors.
The Pellet Press also comes with a Perspex safety guard and pressure gauge for added safety and convenience. Minimum assembly is required, allowing you to start using the press straight away.
To summarize, operating the Pellet Press involves filling the sample, securing the magnetically-held door, and building up the desired pressure with the hand lever. By following these steps and using the Pellet Press correctly, you can efficiently and effectively produce uniform pellets from powdered materials for a variety of laboratory applications.
Recommendation for Comminution of Solid Samples
Use of Vibrating Cup Mill for size-reduction of hard, brittle and fibrous materials
Pressed Pellets
Pressing powder into pellets is a more rigorous sample preparation than pouring loose powders into a sample cup. The process includes grinding a sample into a fine powder, ideally to a grain size of < 75um, mixing it with a binding/grinding aid, and then pressing the mixture in a die at between 20 and 30T to produce a homogeneous sample pellet. The binding/grinding aid is usually a cellulose wax mixture and combines with the sample in a proportion of 20%-30% binder to sample.
Grinding machines
The two most common types of grinding equipment are vibratory mills and planetary mills. Both types of grinding equipment can grind samples to a fine powder and are suitable for different industries. The type of vibratory mill is usually expressed in terms of sample size, with 300g, 200g, 100g, 50g, 10g, etc. They are also available in 1 sample, 2 samples, and 3 samples at a time.
Grinding bowl
The choice of a suitable mortar vessel is important when crushing and grinding, especially when analyzing trace elements. Commonly used materials are generally classified as hard chromium steel (affecting Fe, Cr, Ni, Mn, Si, etc.), tungsten carbide (affecting W, Co, etc.), agate (affecting Si), zirconium oxide (affecting Zr), hot-pressed sintered corundum (affecting Al), etc.
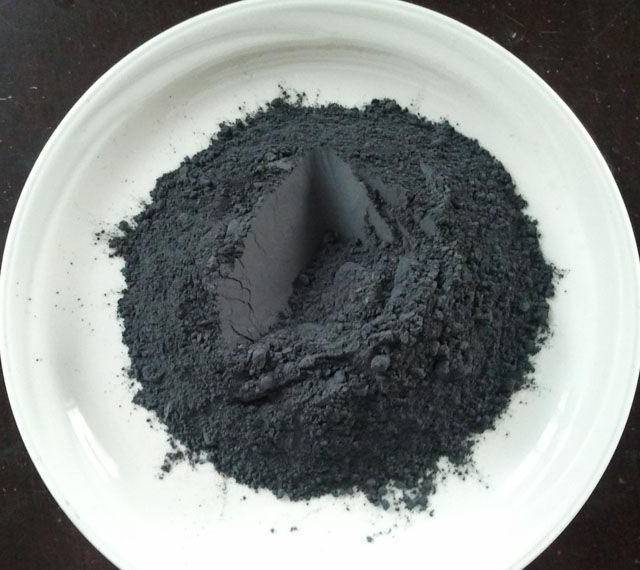
It's as easy as this:
- Fill in the sample
- Close the magnetically-held door
- Build-up the desired pressure using the hand lever - that's it.
For the comminution of solid samples - dry or in suspension - KinTek recommends the Vibrating Cup Mill. It is ideal for extremely fast size-reduction of hard, brittle, and fibrous materials down to analytical fineness.
Samples can be classified as solids, powders, and liquids according to the original form of the sample, and samples are processed in different ways. We will present a series on: powder-pressed flake preparation, powder-fused flake preparation, and block sample preparation. This article introduces a few of the common methods used in powder compacting, plastic ring compacting, boric acid-rimmed priming compacting, and steel ring compacting.
Sample preparation process
Powder compacting is a common method of sample preparation for X-ray fluorescence spectroscopy. The general sample preparation procedure is that the sample is crushed, dried, processed to a certain particle size by grinding equipment, and finally pressed into a stable disc by pressing equipment.
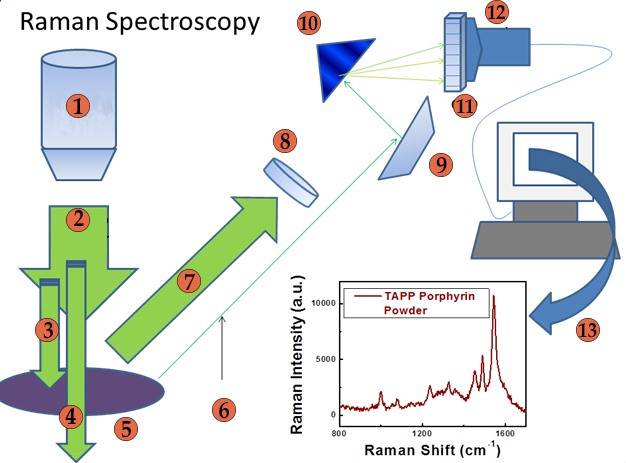
Small pieces of jaw-crushed sample are processed to a suitable size by a vibratory grinder.
If you are interested in this product you can browse our company website:https://kindle-tech.com/products/manual-lab-hydraulic-press-12t-15t-24t-30t-40t, we always insist on the principle of quality first. During the production process, we strictly control every step of the process, using high quality materials and advanced production technology to ensure the stability and durability of our products. to ensure that their performance meets the highest standards. We believe that only by providing customers with excellent quality can we win their trust and long-term cooperation.
CONTATTATECI PER UNA CONSULENZA GRATUITA
I prodotti e i servizi di KINTEK LAB SOLUTION sono stati riconosciuti da clienti di tutto il mondo. Il nostro personale sarà lieto di assistervi per qualsiasi richiesta. Contattateci per una consulenza gratuita e parlate con uno specialista del prodotto per trovare la soluzione più adatta alle vostre esigenze applicative!