Gli altiforni sono fondamentali per la produzione di ferro e la scelta delle materie prime influisce in modo significativo sulla loro efficienza e sulle loro prestazioni.Sebbene il sinterizzato sia un materiale comunemente utilizzato negli altiforni, l'uso del sinterizzato al 100% non è pratico per diverse ragioni tecniche e operative.Il sinterizzato, un prodotto di minerale di ferro prelavorato, offre vantaggi come una migliore permeabilità e un consumo energetico ridotto.Tuttavia, affidarsi esclusivamente al sinterizzato può comportare problemi quali una minore stabilità del forno, un aumento del volume delle scorie e limitazioni nel controllo del flusso di gas e della temperatura.In genere, per ottimizzare le prestazioni del forno si utilizza una miscela bilanciata di sinterizzazione, pellet e minerale in pezzatura, che garantisce un funzionamento regolare e una produzione di ferro di alta qualità.
Spiegazione dei punti chiave:
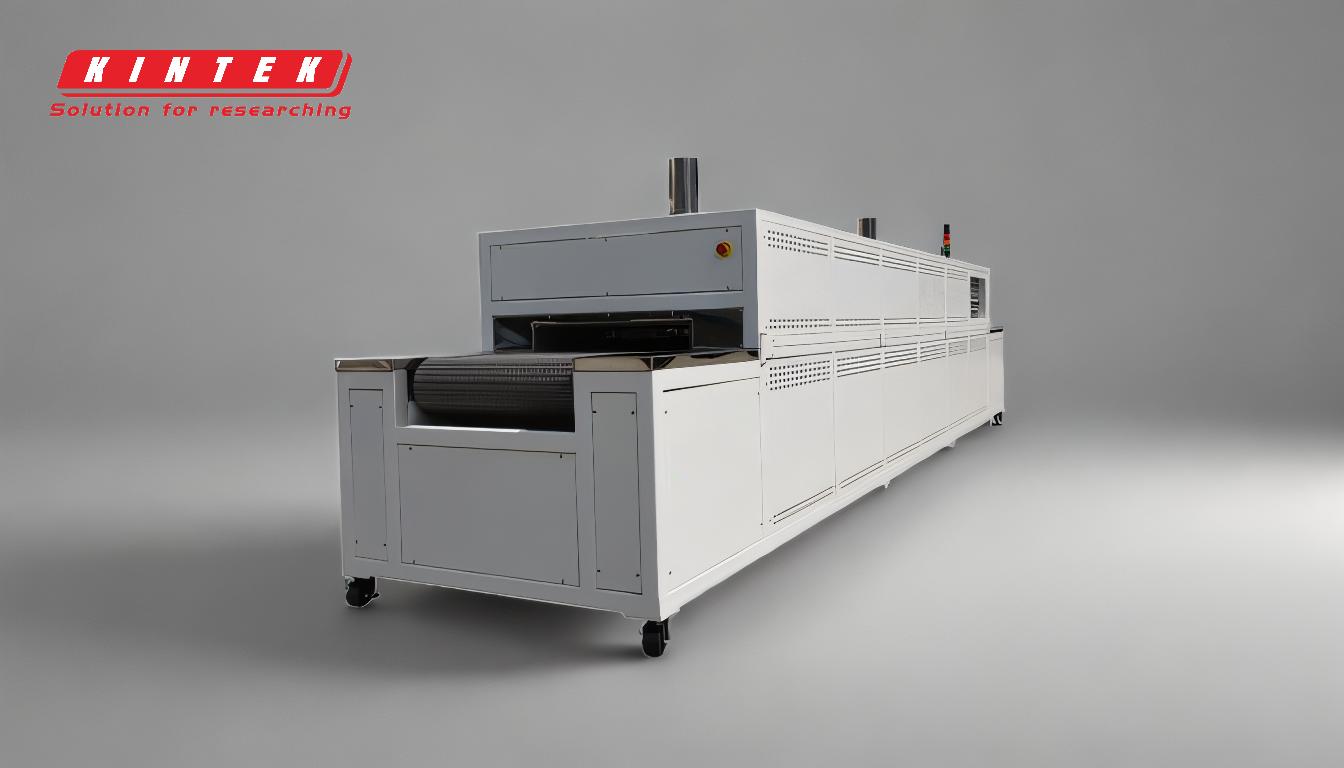
-
Stabilità e permeabilità del forno:
- La sinterizzazione migliora la permeabilità dell'altoforno, consentendo un migliore flusso di gas e una migliore distribuzione del calore.Tuttavia, l'uso del 100% di sinterizzazione può portare a una distribuzione del gas non uniforme e a una permeabilità ridotta, poiché le particelle di sinterizzazione possono impacchettarsi troppo densamente.Ciò può causare instabilità nel forno, con conseguenti inefficienze operative e potenziali interruzioni.
- Un mix di sinterizzazione, pellet e minerale in pezzatura garantisce una distribuzione granulometrica più uniforme, migliorando il flusso di gas e mantenendo la stabilità del forno.
-
Formazione e volume delle scorie:
- Il sinterizzato contiene fondenti come il calcare, che contribuiscono alla formazione delle scorie durante il processo di produzione del ferro.Tuttavia, un uso eccessivo di sinterizzazione può portare a volumi di scorie più elevati a causa dell'aumento del contenuto di fondente.Questo non solo aumenta l'energia necessaria per fondere le scorie, ma riduce anche l'efficienza del forno.
- Una miscela equilibrata di materie prime aiuta a controllare il volume e la composizione delle scorie, ottimizzando le prestazioni del forno e riducendo il consumo energetico.
-
Controllo della temperatura e del flusso di gas:
- L'uso di sinterizzazione al 100% può rendere difficile il controllo della temperatura e del flusso di gas all'interno dell'altoforno.Il sinterizzato ha un punto di fusione più alto rispetto ad altri materiali come i pellet, il che può portare a punti caldi localizzati e a una distribuzione non uniforme della temperatura.
- Incorporando pellet e minerale in pezzatura, l'operatore del forno può regolare meglio la temperatura e il flusso di gas, garantendo un processo di produzione del ferro più costante ed efficiente.
-
Costi e disponibilità:
- Sebbene il sinterizzato sia efficace dal punto di vista dei costi e facilmente disponibile, affidarsi esclusivamente ad esso potrebbe non essere economicamente conveniente nel lungo periodo.La produzione di sinterizzazione richiede energia e risorse significative e la sua disponibilità può essere limitata dalla fornitura di materie prime e dalla capacità produttiva.
- Un mix diversificato di materie prime, tra cui pellet e minerali in pezzatura, consente una maggiore flessibilità nell'approvvigionamento e nella gestione dei costi, garantendo un'attività più sostenibile ed economica.
-
Qualità del ferro prodotto:
- La qualità del ferro prodotto in un altoforno è influenzata dalle materie prime utilizzate.Il sinterizzato da solo potrebbe non fornire la composizione chimica e le proprietà fisiche desiderate per un ferro di alta qualità.
- Una combinazione di sinterizzazione, pellet e minerale in pezzatura garantisce una composizione chimica più equilibrata, che si traduce in ferro di qualità superiore con meno impurità.
-
Flessibilità operativa:
- L'utilizzo di una miscela di materie prime offre flessibilità operativa, consentendo agli operatori del forno di regolare l'alimentazione in base a condizioni e requisiti variabili.Questa adattabilità è fondamentale per mantenere livelli di produzione costanti e rispettare gli standard di qualità.
- Affidarsi esclusivamente al sinterizzato limita questa flessibilità, rendendo più difficile rispondere alle fluttuazioni della qualità delle materie prime, alla domanda del mercato o alle sfide operative.
In conclusione, sebbene il sinterizzato sia un componente prezioso nelle operazioni di altoforno, l'uso del sinterizzato al 100% non è fattibile a causa del suo impatto sulla stabilità del forno, sul volume delle scorie, sul controllo della temperatura, sui costi e sulla qualità del ferro.Una miscela equilibrata di sinterizzazione, pellet e minerale in pezzatura è essenziale per ottimizzare le prestazioni dell'altoforno, garantendo una produzione di ferro efficiente e di alta qualità.
Tabella riassuntiva:
Fattore | Impatto della sinterizzazione al 100% | Soluzione con materie prime miste |
---|---|---|
Stabilità del forno | Flusso di gas irregolare, permeabilità ridotta e instabilità | La distribuzione uniforme delle dimensioni delle particelle con sinterizzazione, pellet e minerale in pezzatura aumenta la stabilità |
Volume delle scorie | Aumento del volume delle scorie grazie al maggiore contenuto di fondente | La miscela bilanciata controlla il volume della scoria, riducendo il consumo energetico |
Controllo della temperatura | Punti caldi localizzati e distribuzione non uniforme della temperatura | I pellet e i minerali in pezzatura migliorano la regolazione della temperatura e il flusso di gas |
Costo e disponibilità | Limitato dalla fornitura di materie prime e dagli alti costi di produzione | Il mix diversificato garantisce economicità e flessibilità operativa |
Qualità del ferro | Composizione chimica e proprietà fisiche non ottimali | Una miscela bilanciata garantisce ferro di qualità superiore con meno impurità |
Flessibilità operativa | Adattabilità limitata a condizioni mutevoli | I materiali misti consentono aggiustamenti in base alla qualità delle materie prime e alla domanda del mercato |
Ottimizzate le prestazioni del vostro altoforno con la giusta miscela di materie prime... contattate oggi i nostri esperti per soluzioni su misura!