La temperatura di un forno per la fusione del vetro è tipicamente compresa tra 1.500°C e 1.600°C (da 2.732°F a 2.912°F) a seconda del tipo di vetro prodotto e del progetto specifico del forno.I forni per la fusione del vetro sono progettati per mantenere temperature estremamente elevate per fondere materie prime come sabbia silicea, soda e calcare in vetro fuso.La temperatura deve essere attentamente controllata per garantire la corretta fusione, omogeneizzazione e raffinazione del vetro.I forni continui, come descritto nel riferimento, operano in condizioni di temperatura permanente, il che corrisponde alla necessità di un calore elevato e costante nella produzione del vetro.
Punti chiave spiegati:
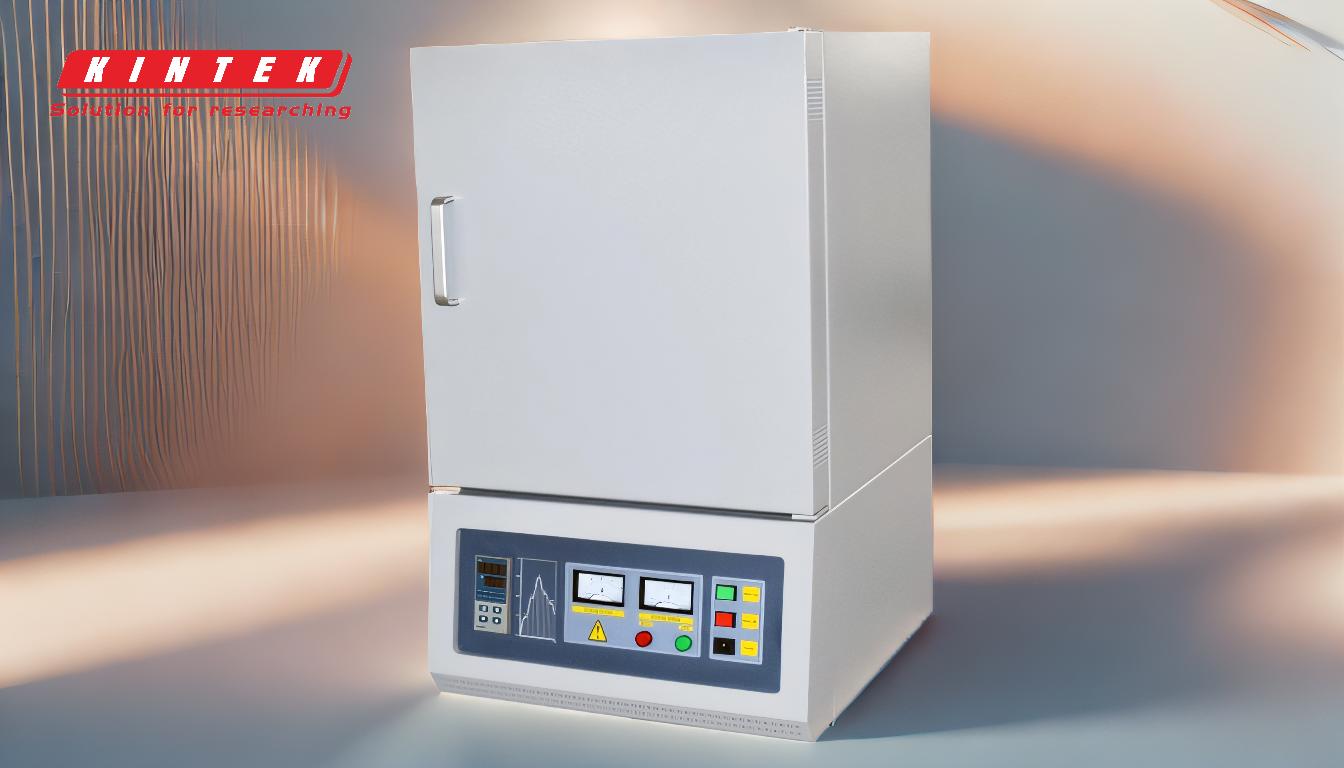
-
Intervallo di temperatura dei forni per la fusione del vetro:
- I forni per la fusione del vetro funzionano a temperature comprese tra 1.500°C e 1.600°C (da 2.732°F a 2.912°F) .
- Questa temperatura elevata è necessaria per fondere materie prime come sabbia silicea, soda e calcare in uno stato fuso omogeneo.
- La temperatura esatta dipende dal tipo di vetro prodotto (ad esempio, vetro soda-calce, vetro borosilicato) e dal progetto del forno.
-
Scopo delle alte temperature:
- Fusione:Le materie prime devono essere riscaldate al loro punto di fusione per formare una miscela di vetro liquido.
- Omogeneizzazione:Le alte temperature assicurano che il vetro fuso abbia una composizione uniforme, sia privo di bolle e sia pronto per essere modellato.
- Raffinazione:A queste temperature le impurità e i gas vengono rimossi per produrre vetro chiaro e di alta qualità.
-
Funzionamento del forno continuo:
- Come indicato nel riferimento, i forni continui operano in condizioni di temperatura permanente.
- Questo aspetto è fondamentale per la produzione del vetro, in quanto il mantenimento di una temperatura costante assicura un flusso costante di vetro fuso e una qualità costante del prodotto.
- I forni continui sono ideali per la produzione di vetro su larga scala, dove si utilizzano ripetutamente le stesse materie prime e gli stessi processi.
-
Fattori che influenzano la temperatura:
- Composizione del vetro:I diversi tipi di vetro richiedono temperature di fusione leggermente diverse.Ad esempio, il vetro borosilicato, utilizzato nelle apparecchiature di laboratorio, richiede spesso temperature più elevate rispetto al vetro soda-lime.
- Design del forno:Il tipo di forno (ad esempio, rigenerativo, a recupero o elettrico) può influenzare la temperatura di esercizio e l'efficienza.
- Fonte di energia:I forni possono utilizzare gas naturale, elettricità o altri combustibili, che possono influenzare il controllo e la distribuzione della temperatura.
-
Controllo e monitoraggio della temperatura:
- Il controllo preciso della temperatura è essenziale per evitare il sotto-riscaldamento (che porta a una fusione incompleta) o il surriscaldamento (che può danneggiare il forno o degradare la qualità del vetro).
- I forni avanzati utilizzano sensori e sistemi automatizzati per monitorare e regolare la temperatura in tempo reale.
-
Confronto con altri forni:
- A differenza dei forni per il trattamento termico dei metalli (ad esempio, ricottura o tempra), i forni per la fusione del vetro operano a temperature molto più elevate a causa delle proprietà uniche dei materiali che formano il vetro.
- Il riferimento sottolinea che i forni continui sono specializzati per processi specifici, il che vale anche per i forni per la fusione del vetro.
Comprendendo questi punti chiave, l'acquirente può valutare meglio le specifiche e le capacità dei forni per la fusione del vetro, assicurandosi che soddisfino i requisiti di produzione per il tipo di vetro specifico.
Tabella riassuntiva:
Aspetto chiave | Dettagli |
---|---|
Intervallo di temperatura | 1,500°C–1,600°C (2,732°F–2,912°F) |
Scopo delle alte temperature | Fusione delle materie prime, omogeneizzazione e raffinazione delle impurità |
Funzionamento del forno | I forni continui mantengono una temperatura permanente per una qualità costante |
Fattori che influenzano la temperatura | Tipo di vetro, design del forno e fonte di energia |
Controllo della temperatura | Il monitoraggio in tempo reale e i sistemi automatizzati garantiscono la precisione |
Assicuratevi che la vostra produzione di vetro sia conforme agli standard del settore. contattate oggi stesso i nostri esperti per soluzioni su misura!