La sinterizzazione della ceramica è un processo in più fasi che trasforma i materiali ceramici in polvere in strutture solide e dense attraverso il calore e la pressione, senza fondere il materiale.Il processo prevede la preparazione di una miscela di polveri ceramiche, la formazione della forma desiderata (corpo verde) e il successivo riscaldamento ad alte temperature per fondere insieme le particelle.In questo modo si ottiene un prodotto ceramico denso e a bassa porosità, con una maggiore resistenza meccanica e durata.Il processo è fondamentale per la creazione di ceramiche ad alte prestazioni utilizzate in vari settori, tra cui quello elettronico, aerospaziale e medico.
Punti chiave spiegati:
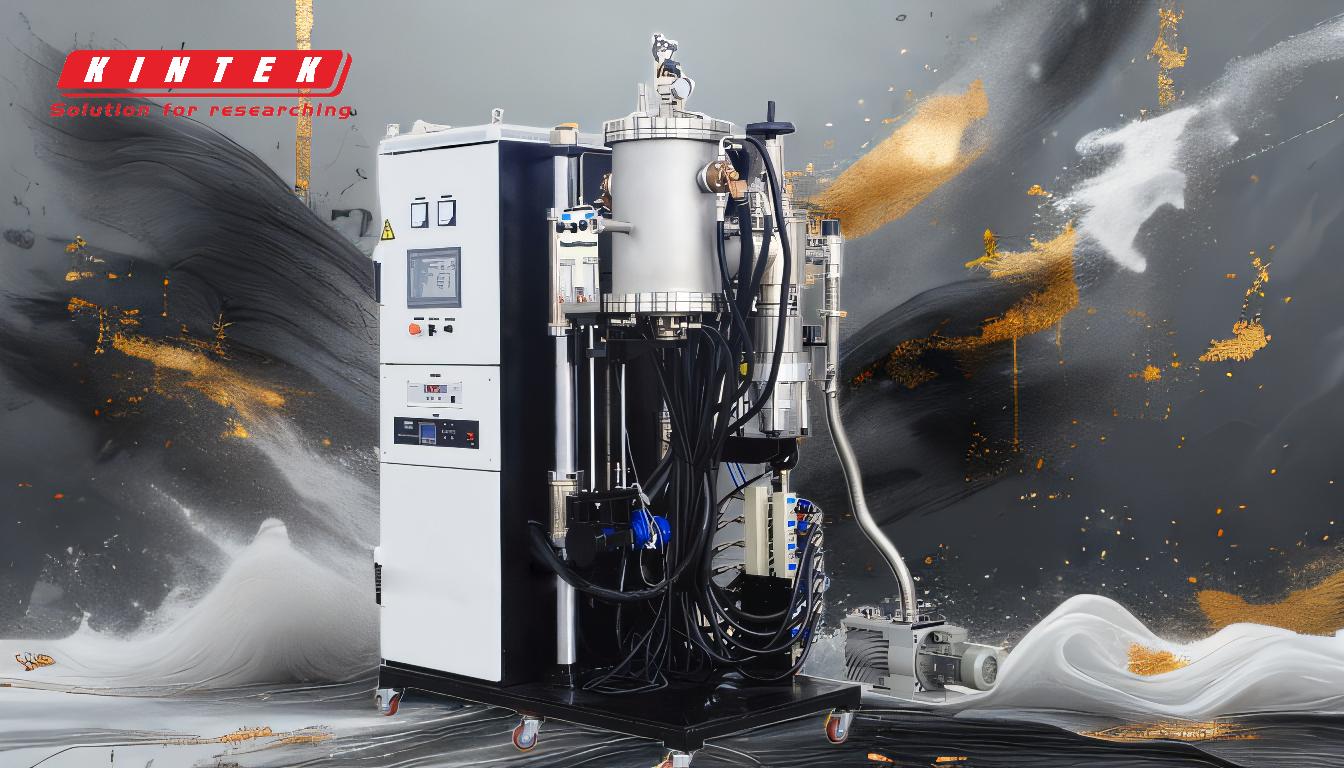
-
Composizione e preparazione della polvere:
- Il processo inizia con la preparazione di un impasto di polvere ceramica.Si tratta di mescolare le polveri ceramiche grezze con additivi quali leganti, deflocculanti e acqua per formare un impasto.I leganti aiutano a tenere insieme le particelle, mentre i deflocculanti ne impediscono l'agglomerazione.
- L'impasto viene poi essiccato a spruzzo per creare una polvere fluida, più facile da maneggiare e da pressare negli stampi.
-
Formare il corpo verde:
- La polvere essiccata a spruzzo viene pressata in uno stampo con metodi meccanici, come la pressatura a freddo o a caldo.Questa fase modella la polvere in un "corpo verde", che è una struttura ceramica fragile e non cotta.
- Il corpo verde mantiene la forma desiderata, ma non ha la forza e la densità del prodotto finale.È fondamentale maneggiare con cura il corpo verde per evitare crepe o deformazioni.
-
Bruciatura del legante (debinding):
- Prima della sinterizzazione, il corpo verde viene riscaldato a bassa temperatura per rimuovere i leganti organici utilizzati durante il processo di formatura.Questa fase, nota come debinding, è essenziale per evitare difetti nel prodotto finale.
- La temperatura è attentamente controllata per garantire la completa rimozione del legante senza danneggiare il corpo verde.
-
Sinterizzazione (cottura):
- Il corpo verde viene quindi riscaldato a una temperatura elevata, in genere appena inferiore al punto di fusione del materiale ceramico, in un'atmosfera controllata (ad esempio, in un forno a tunnel o in un forno periodico).
- Durante la sinterizzazione, le particelle di ceramica subiscono la diffusione e il movimento dei bordi dei grani, portando alla densificazione e alla fusione delle particelle.Il risultato è un prodotto ceramico denso e a bassa porosità, con proprietà meccaniche migliorate.
- Il processo di sinterizzazione può essere migliorato utilizzando tecniche come la sinterizzazione in fase liquida (LPS), in cui una piccola quantità di fase liquida accelera la fusione delle particelle.
-
Raffreddamento e solidificazione:
- Dopo la sinterizzazione, il prodotto ceramico viene gradualmente raffreddato a temperatura ambiente.Questa fase è fondamentale per evitare stress termici e fessurazioni.
- La velocità di raffreddamento viene controllata per garantire che il materiale si solidifichi in una massa unificata e densa con la microstruttura e le proprietà desiderate.
-
Fattori che influenzano la sinterizzazione:
- Temperatura e tempo:La temperatura e la durata della sinterizzazione devono essere attentamente controllate per ottenere una densificazione ottimale senza sinterizzazione eccessiva, che può portare alla crescita dei grani e alla riduzione della resistenza.
- Atmosfera:L'atmosfera di sinterizzazione (ad esempio, aria, vuoto o gas inerte) influisce sulle proprietà finali della ceramica.Ad esempio, la sinterizzazione in atmosfera riducente può impedire l'ossidazione di alcuni materiali.
- Caratteristiche della polvere:Le dimensioni, la forma e la distribuzione delle particelle ceramiche influenzano il comportamento di sinterizzazione.Le particelle più fini generalmente sinterizzano più facilmente a causa della loro maggiore energia superficiale.
-
Applicazioni della ceramica sinterizzata:
-
Le ceramiche sinterizzate sono utilizzate in un'ampia gamma di applicazioni, tra cui:
- Elettronica:Per substrati, isolanti e condensatori.
- Aerospaziale:Per scudi termici e componenti del motore.
- Medico:Per impianti e protesi dentarie.
- Industriale:Per utensili da taglio, parti resistenti all'usura e filtri.
-
Le ceramiche sinterizzate sono utilizzate in un'ampia gamma di applicazioni, tra cui:
Comprendendo e ottimizzando ogni fase del processo di sinterizzazione, i produttori possono produrre materiali ceramici di alta qualità su misura per applicazioni specifiche.Il processo richiede un controllo preciso di parametri quali temperatura, pressione e atmosfera per ottenere le proprietà desiderate del materiale.
Tabella riassuntiva:
Passo | Descrizione |
---|---|
Preparazione della polvere | Miscelare le polveri ceramiche con leganti, deflocculanti e acqua per formare un impasto. |
Formazione del corpo verde | Premere la polvere in uno stampo per creare una fragile struttura ceramica non cotta. |
Deceraggio | Il calore rimuove i leganti, garantendo l'assenza di difetti nel prodotto finale. |
Sinterizzazione | Il calore ad alte temperature fonde le particelle, creando un prodotto ceramico denso. |
Raffreddamento | Raffreddare gradualmente per solidificare il materiale e prevenire lo stress termico. |
Applicazioni | Utilizzato nei settori elettronico, aerospaziale, medico e industriale. |
Ottimizzate il vostro processo di sinterizzazione della ceramica... contattate oggi i nostri esperti per soluzioni su misura!