Il processo di rivestimento PVD (Physical Vapor Deposition) è un metodo sofisticato utilizzato per creare rivestimenti sottili, durevoli e funzionali su vari substrati.Il processo prevede la vaporizzazione di un materiale solido in un ambiente sotto vuoto, il trasporto degli atomi vaporizzati sul substrato e il loro deposito per formare un film sottile.Questo processo migliora le proprietà del substrato, come la durezza, la resistenza all'usura e alla corrosione, oltre a migliorarne l'estetica.Il meccanismo del rivestimento PVD può essere suddiviso in diverse fasi chiave, tra cui la pulizia, la vaporizzazione, il trasporto, la reazione e la deposizione.Ogni fase è fondamentale per garantire la qualità e le prestazioni del rivestimento finale.
Punti chiave spiegati:
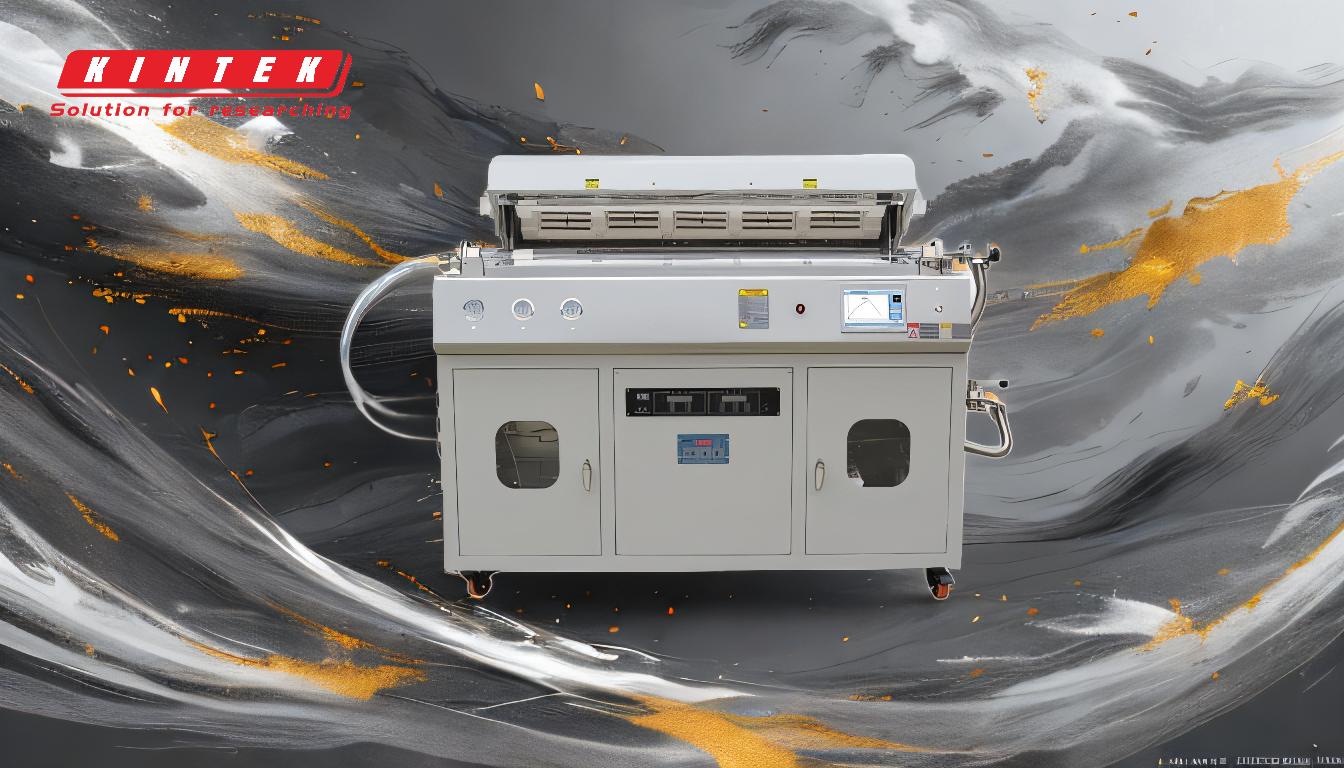
-
Pulizia e pretrattamento del substrato:
- Prima di iniziare il processo di rivestimento PVD, il substrato deve essere pulito a fondo per rimuovere eventuali contaminanti come oli, polvere o ossidi.Si tratta di un aspetto cruciale, perché le impurità presenti sulla superficie possono influire negativamente sull'adesione e sulla qualità del rivestimento.
- Per migliorare l'energia superficiale e l'adesione del rivestimento si possono utilizzare anche processi di pretrattamento, come la pulizia al plasma o l'incisione.Questa fase garantisce un'efficace adesione del rivestimento al substrato.
-
Creazione di un ambiente ad alto vuoto:
- Il processo di rivestimento PVD avviene in una camera a vuoto, evacuata a una pressione estremamente bassa, in genere compresa tra 10^-3 e 10^-9 Torr.Questo ambiente ad alto vuoto è essenziale per evitare la contaminazione da parte dei gas atmosferici e per consentire al materiale vaporizzato di raggiungere senza ostacoli il substrato.
- Il vuoto assicura inoltre che il materiale vaporizzato rimanga pulito e puro, il che è fondamentale per ottenere rivestimenti di alta qualità.
-
Vaporizzazione del materiale target:
- Il materiale di destinazione, che è la fonte del rivestimento, viene vaporizzato utilizzando una delle diverse tecniche, come lo sputtering, l'evaporazione ad arco o l'evaporazione a fascio di elettroni.Nello sputtering, gli ioni ad alta energia bombardano il bersaglio, staccando gli atomi dalla sua superficie.Nell'evaporazione ad arco, un arco elettrico vaporizza il materiale bersaglio, mentre nell'evaporazione a fascio elettronico, un fascio di elettroni focalizzato riscalda e vaporizza il bersaglio.
- La scelta della tecnica di vaporizzazione dipende dal materiale da rivestire e dalle proprietà desiderate del rivestimento.
-
Trasporto degli atomi vaporizzati:
- Una volta vaporizzato il materiale target, gli atomi o le molecole vengono trasportati attraverso la camera a vuoto fino al substrato.Questo trasporto avviene in linea retta grazie all'assenza di molecole d'aria nell'ambiente del vuoto.
- La distanza tra il bersaglio e il substrato e l'energia degli atomi vaporizzati influenzano l'uniformità e lo spessore del rivestimento.
-
Reazione con gas reattivi (opzionale):
- Durante la fase di trasporto, nella camera a vuoto possono essere introdotti gas reattivi come azoto, ossigeno o acetilene.Questi gas reagiscono con gli atomi di metallo vaporizzati per formare composti come nitruri, ossidi o carburi metallici.
- Questa fase di reazione è fondamentale per modificare le proprietà del rivestimento.Ad esempio, l'aggiunta di azoto può portare alla formazione di un rivestimento di nitruro metallico duro e resistente all'usura.
-
Deposizione e condensazione sul substrato:
- Gli atomi o le molecole vaporizzate raggiungono infine il substrato, dove si condensano e formano un film sottile e uniforme.Questa deposizione avviene atomo per atomo, dando luogo a un rivestimento altamente controllato e preciso.
- Il processo di deposizione è influenzato da fattori quali la temperatura del substrato, l'energia degli atomi vaporizzati e l'angolo di incidenza degli atomi sul substrato.
-
Controllo di qualità e finitura:
- Dopo il deposito del rivestimento, vengono adottate misure di controllo della qualità per garantire che il rivestimento sia conforme alle specifiche richieste.Ciò può comportare la verifica dello spessore, dell'adesione, della durezza e di altre proprietà del rivestimento.
- Per migliorare l'aspetto o le prestazioni del rivestimento possono essere applicati anche processi di finitura, come la lucidatura o ulteriori trattamenti superficiali.
-
Vantaggi ambientali e operativi:
- Il rivestimento PVD è considerato un processo ecologico perché non comporta l'uso di sostanze chimiche nocive e non produce rifiuti significativi.Il processo è anche altamente efficiente, con una perdita minima di materiale.
- I rivestimenti risultanti sono durevoli, resistenti all'usura e alla corrosione e possono essere personalizzati per soddisfare specifici requisiti funzionali o estetici.
In sintesi, il meccanismo del rivestimento PVD prevede una serie di fasi accuratamente controllate che trasformano un materiale solido di destinazione in un sottile rivestimento ad alte prestazioni su un substrato.Ogni fase, dalla pulizia e vaporizzazione alla deposizione e alla finitura, svolge un ruolo fondamentale nel garantire la qualità e la funzionalità del prodotto finale.Il processo è estremamente versatile e consente di creare rivestimenti con un'ampia gamma di proprietà, il che lo rende una tecnica preziosa in settori come quello automobilistico, aerospaziale, dei dispositivi medici e dell'elettronica di consumo.
Tabella riassuntiva:
Passo | Descrizione |
---|---|
Pulizia e pretrattamento | Rimuovere i contaminanti e migliorare l'adesione attraverso la pulizia e il trattamento della superficie. |
Ambiente ad alto vuoto | Creare il vuoto per evitare la contaminazione e garantire la pulizia del materiale vaporizzato. |
Vaporizzazione del target | Utilizzare lo sputtering, l'evaporazione ad arco o il fascio di elettroni per vaporizzare il materiale target. |
Trasporto degli atomi | Trasportare gli atomi vaporizzati verso il substrato in linea retta. |
Reazione con i gas (opzionale) | Introdurre gas reattivi per modificare le proprietà del rivestimento (ad esempio, la durezza). |
Deposizione e condensazione | Depositare gli atomi sul substrato per formare un film sottile e uniforme. |
Controllo qualità e finitura | Testate e migliorate le proprietà del rivestimento in termini di prestazioni e aspetto. |
Vantaggi ambientali | Ecologico, efficiente e produce rivestimenti durevoli e su misura. |
Sfruttate il potenziale dei rivestimenti PVD per le vostre applicazioni. contattate i nostri esperti oggi stesso !