La sinterizzazione e la fusione sono entrambi processi utilizzati per legare i materiali, in particolare i metalli, ma differiscono significativamente nei meccanismi, nei requisiti di temperatura e nei risultati.La sinterizzazione prevede il riscaldamento dei materiali a una temperatura inferiore al loro punto di fusione, spesso combinato con la pressione, per legare le particelle tra loro attraverso la diffusione atomica.Questo processo evita la liquefazione, ottenendo una massa solida con porosità controllata e imperfezioni minime.La fusione, invece, comporta il riscaldamento del materiale fino al suo punto di fusione, provocando un completo cambiamento di fase da solido a liquido.Questa procedura richiede un'energia maggiore e può portare a imperfezioni come restringimenti o deformazioni.La sinterizzazione è preferibile per i materiali con punti di fusione elevati e per le applicazioni che richiedono un controllo preciso delle proprietà del prodotto finale.
Punti chiave spiegati:
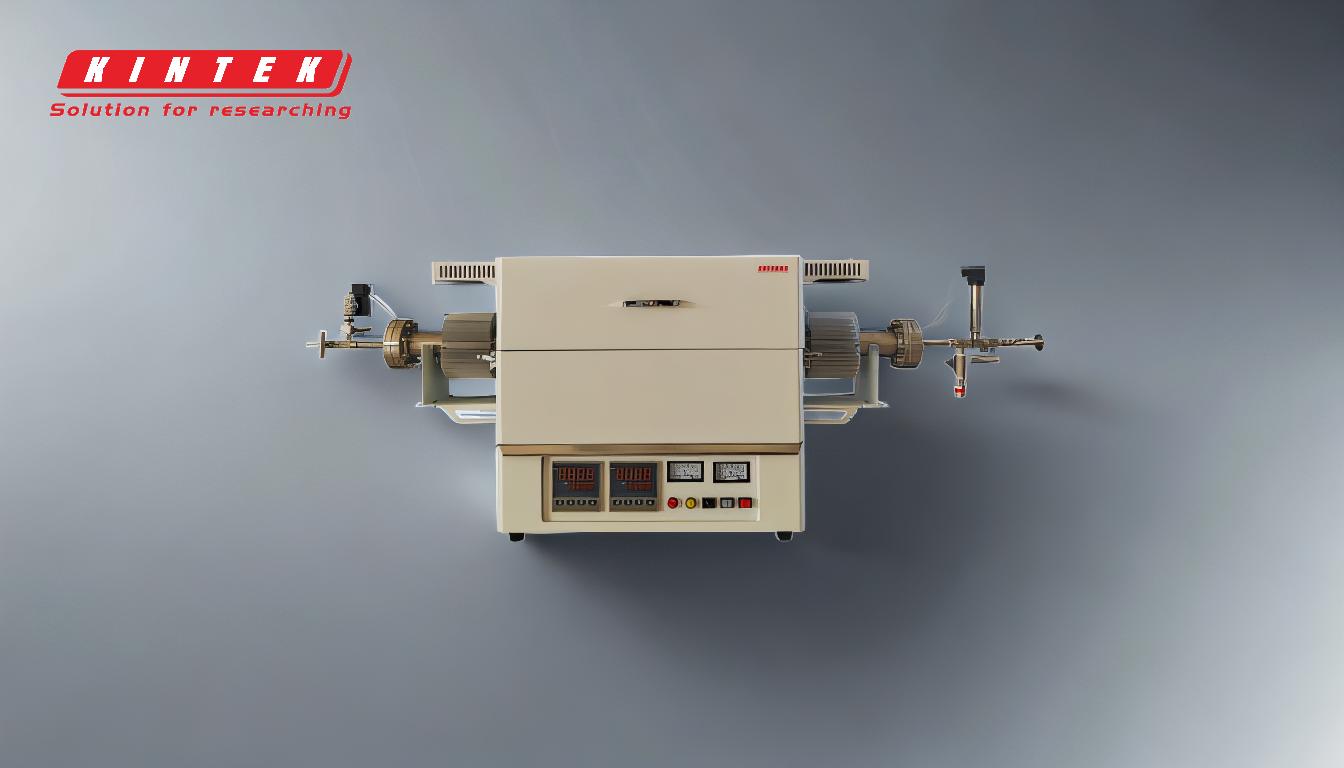
-
Requisiti di temperatura:
- Sinterizzazione:Si verifica a temperature inferiori al punto di fusione del materiale.Ciò consente l'incollaggio senza liquefazione e lo rende adatto a materiali con punti di fusione estremamente elevati, come il tungsteno e il molibdeno.
- Fusione:Richiede il riscaldamento del materiale fino al suo punto di fusione, inducendo un completo cambiamento di fase da solido a liquido.Questo processo richiede un'energia significativamente maggiore.
-
Meccanismo di legame:
- Sinterizzazione:Si basa sulla diffusione atomica attraverso i confini delle particelle sottoposte a calore e pressione.Le particelle si densificano e si fondono senza fondere, ottenendo una massa solida con porosità controllata.
- Fusione:Comporta la fusione del materiale, che poi si solidifica in una massa unificata al momento del raffreddamento.Questo processo può portare a imperfezioni come restringimenti o deformazioni dovute al completo cambiamento di fase.
-
Energia e controllo:
- Sinterizzazione:Richiede meno energia rispetto alla fusione e offre un maggiore controllo sulle proprietà del prodotto finale, come porosità e densità.Questo lo rende ideale per le applicazioni che richiedono precisione.
- Fusione:Consuma più energia ed è meno controllabile, spesso causa di imperfezioni.Si utilizza in genere quando è necessario un legame completamente denso e in fase liquida.
-
Applicazioni e materiali:
- Sinterizzazione:Comunemente utilizzato per materiali con punti di fusione elevati e in applicazioni in cui la porosità controllata è vantaggiosa, come nei filtri, nei cuscinetti e in alcuni tipi di ceramica.
- Fusione:Utilizzato in processi come la fusione, la saldatura e la brasatura, in cui è necessaria una fase liquida per unire materiali o creare forme complesse.
-
Fasi del processo:
-
Sinterizzazione:
- Preparazione:Miscelazione di materiali primari e agenti di accoppiamento, seguita dalla compressione della polvere nella forma desiderata.
- Riscaldamento:Riscaldamento per rimuovere l'agente di accoppiamento e fondere il materiale primario in un insieme a bassa porosità.
- Fusione delle particelle:Le particelle si densificano e si fondono, spesso accelerate dalla sinterizzazione in fase liquida (LPS).
- Solidificazione:Raffreddamento e solidificazione in una massa unificata.
-
Fusione:
- Fusione:Riscaldamento del materiale fino al suo punto di fusione per indurre una fase liquida.
- Solidificazione:Raffreddamento del liquido per formare una massa solida, spesso con imperfezioni dovute al cambiamento di fase.
-
Sinterizzazione:
-
Tipi di sinterizzazione:
- Sinterizzazione in fase liquida transitoria:Comporta l'aggiunta di un materiale (ad esempio, rame al ferro) che fonde a temperature di sinterizzazione, creando una fase liquida temporanea che si indurisce al raffreddamento.
- Sinterizzazione in fase liquida permanente:Utilizza un materiale liquido permanente (ad esempio, il carburo) che scorre nelle aperture e nelle fessure, incollando ulteriormente i materiali.
-
Vantaggi e svantaggi:
-
Sinterizzazione:
- Vantaggi:Consumo energetico ridotto, porosità controllata, imperfezioni minime, adatto a materiali ad alto punto di fusione.
- Svantaggi:Limitato ai materiali che possono legare senza fondere, può richiedere ulteriori fasi di lavorazione.
-
Fusione:
- Vantaggi:Crea un legame completamente denso, adatto a forme complesse e alla giunzione di materiali dissimili.
- Svantaggi:Consumo di energia più elevato, rischio di imperfezioni, limitato ai materiali che possono resistere alla fusione.
-
Sinterizzazione:
Comprendendo queste differenze chiave, si può scegliere il processo più adatto in base alle proprietà del materiale e ai risultati desiderati per applicazioni specifiche.
Tabella riassuntiva:
Aspetto | Sinterizzazione | Fusione |
---|---|---|
Temperatura di fusione | Al di sotto del punto di fusione | Al punto di fusione |
Meccanismo | Diffusione atomica sotto calore e pressione | Cambiamento di fase completo da solido a liquido |
Consumo di energia | Più basso | Più alto |
Controllo | Elevato controllo su porosità e densità | Minore controllo, rischio di imperfezioni |
Applicazioni | Filtri, cuscinetti, ceramica | Fusione, saldatura, brasatura |
Vantaggi | Energia ridotta, imperfezioni minime, adatto a materiali ad alto punto di fusione | Legame completamente denso, adatto a forme complesse |
Svantaggi | Limitato ai materiali che si legano senza fondere | Energia più elevata, rischio di ritiro o deformazione |
Avete bisogno di aiuto per scegliere il processo giusto per la vostra applicazione? Contattate i nostri esperti oggi stesso !