La sinterizzazione di metalli in polvere e ceramica è un processo di produzione fondamentale utilizzato per creare materiali densi, resistenti e durevoli da forme in polvere. Implica il riscaldamento del portacipria (o parte "verde") al di sotto del punto di fusione in un ambiente controllato, come ad esempio un forno di sinterizzazione , per legare insieme le particelle attraverso la diffusione e la crescita dei grani. Questo processo è ampiamente utilizzato in settori come quello automobilistico, aerospaziale ed elettronico per produrre componenti con forme e proprietà precise. La sinterizzazione può avvenire in vari ambienti, tra cui vuoto, atmosfera controllata o condizioni di pressatura a caldo, a seconda del materiale e del risultato desiderato. Il processo migliora le proprietà meccaniche, termiche ed elettriche del prodotto finale eliminando la porosità e migliorando il legame delle particelle.
Punti chiave spiegati:
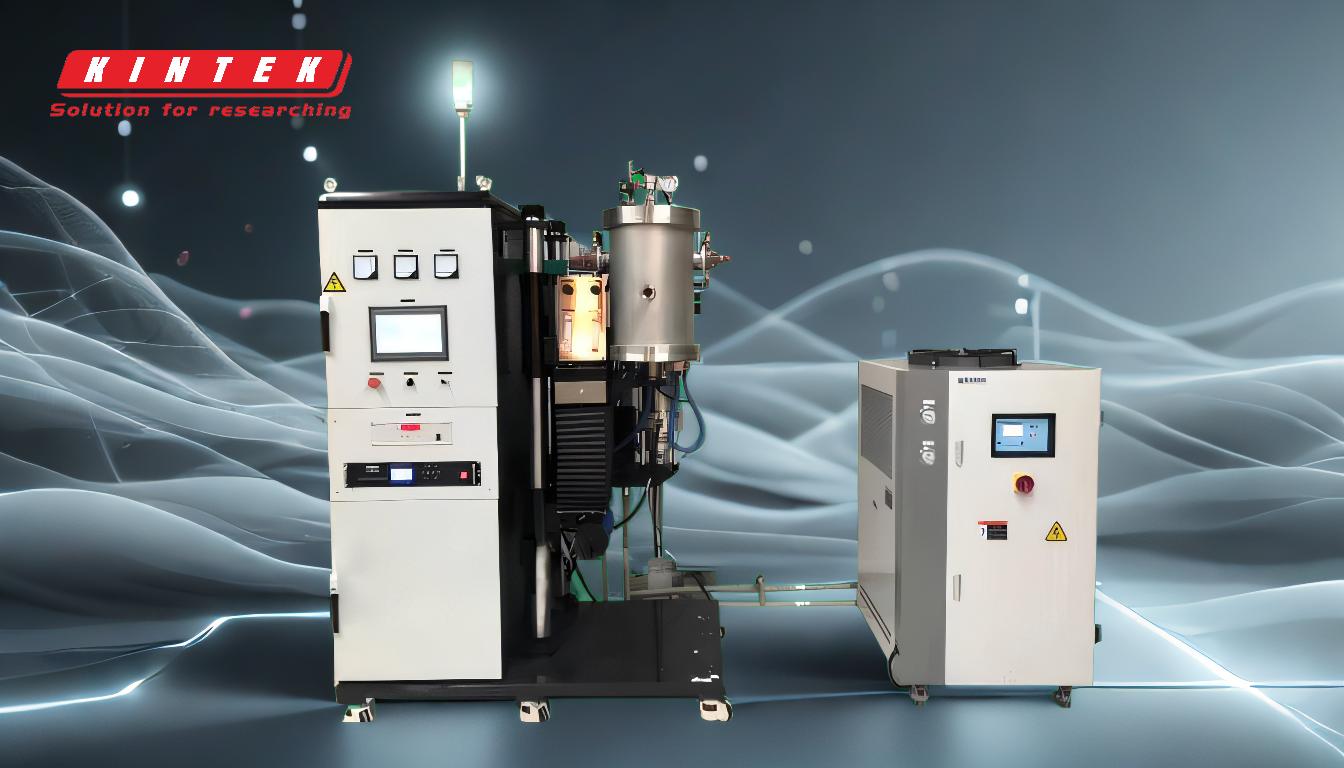
-
Definizione e scopo della sinterizzazione:
- La sinterizzazione è un processo termico utilizzato per legare metalli in polvere o ceramica in un materiale solido e denso senza sciogliere l'intera massa. È essenziale per ottenere elevata resistenza, durezza e precisione dimensionale nelle parti prodotte.
- Il processo è ampiamente utilizzato nella metallurgia delle polveri e nella produzione di ceramica per produrre forme e componenti complessi con proprietà personalizzate.
-
Fasi del processo di sinterizzazione:
- Preparazione della polvere: Polveri metalliche o ceramiche vengono selezionate e miscelate con leganti o lubrificanti per migliorare la scorrevolezza e la compattazione.
- Compattazione: La polvere viene pressata in una parte "verde" mediante presse meccaniche o idrauliche. Questo passaggio conferisce alla parte la sua forma e resistenza iniziali.
- Sinterizzazione: La parte verde viene riscaldata in a forno di sinterizzazione a temperature inferiori al punto di fusione del materiale. Durante questa fase, le particelle si legano per diffusione e la parte si restringe man mano che la porosità si riduce.
-
Tipi di forni di sinterizzazione:
- Forno di sinterizzazione sotto vuoto: Funziona in un ambiente sotto vuoto per prevenire l'ossidazione e la contaminazione. Ideale per materiali sensibili all'ossigeno, come il titanio o alcune ceramiche.
- Forno di sinterizzazione in atmosfera: Utilizza atmosfere controllate (ad esempio, azoto, argon) per proteggere il materiale e migliorare la qualità della sinterizzazione. Comunemente utilizzato per metalli come acciaio inossidabile e rame.
- Forno di sinterizzazione a pressa a caldo: Combina alta temperatura e pressione per accelerare la densificazione. Adatto per ceramiche avanzate e materiali compositi.
-
Meccanismi chiave nella sinterizzazione:
- Diffusione: Gli atomi migrano attraverso i confini delle particelle, portando a legami e densificazione.
- Crescita del grano: Le particelle diventano più grandi man mano che i grani più piccoli si uniscono, migliorando le proprietà meccaniche.
- Eliminazione dei pori: La porosità diminuisce man mano che le particelle si riorganizzano e si legano, risultando in un materiale più denso.
-
Applicazioni della sinterizzazione:
- Metalli: Utilizzato per produrre ingranaggi, cuscinetti e componenti strutturali nell'industria automobilistica e aerospaziale.
- Ceramica: Applicato nella produzione di utensili da taglio, isolanti e impianti biomedici.
- Compositi: Consente la produzione di materiali avanzati con proprietà su misura per applicazioni specifiche.
-
Vantaggi della sinterizzazione:
- Conveniente: Riduce lo spreco di materiale e consente una produzione quasi perfetta.
- Versatilità: Adatto per un'ampia gamma di materiali, inclusi metalli, ceramica e compositi.
- Proprietà migliorate: Migliora la robustezza, la durezza e la resistenza all'usura del prodotto finale.
-
Sfide e considerazioni:
- Controllo della temperatura: È necessario un riscaldamento preciso per evitare la fusione o la sinterizzazione incompleta.
- Gestione dell'atmosfera: Il controllo adeguato dell'ambiente del forno è fondamentale per prevenire la contaminazione o l'ossidazione.
- Selezione dei materiali: La scelta della composizione della polvere e del legante influisce sul risultato della sinterizzazione e sulle proprietà finali.
Comprendendo il processo di sinterizzazione e il ruolo di a forno di sinterizzazione , i produttori possono ottimizzare i parametri di produzione per ottenere componenti di alta qualità con le proprietà desiderate. Questo processo è indispensabile nella produzione moderna, poiché offre un equilibrio tra precisione, efficienza e prestazioni dei materiali.
Tabella riassuntiva:
Aspetto | Dettagli |
---|---|
Definizione | Processo termico per legare metalli/ceramiche in polvere senza scioglierli. |
Passaggi chiave | Preparazione delle polveri, compattazione, sinterizzazione in forno. |
Tipi di forni | Forni di sinterizzazione sotto vuoto, atmosfera, pressa a caldo. |
Meccanismi chiave | Diffusione, crescita del grano, eliminazione dei pori. |
Applicazioni | Ingranaggi, cuscinetti, utensili da taglio, impianti biomedici e altro ancora. |
Vantaggi | Conveniente, versatile, migliora la robustezza e la resistenza all'usura. |
Sfide | Controllo della temperatura, gestione dell'atmosfera, selezione dei materiali. |
Ottimizza il tuo processo di produzione con la sinterizzazione— contatta i nostri esperti oggi stesso per soluzioni su misura!