La deposizione fisica da vapore (PVD) è una tecnica ampiamente utilizzata per depositare film sottili di materiale su un substrato.Il processo prevede il passaggio di una sostanza di rivestimento da una forma condensata a una forma di vapore e poi di nuovo a una forma condensata come film sottile sulla superficie degli oggetti.Le principali varianti del PVD comprendono l'evaporazione termica o sotto vuoto, la placcatura ionica e lo sputtering.Ognuno di questi metodi ha caratteristiche e applicazioni uniche, ma tutti condividono il principio comune di essere metodi di rivestimento a secco.
Punti chiave spiegati:
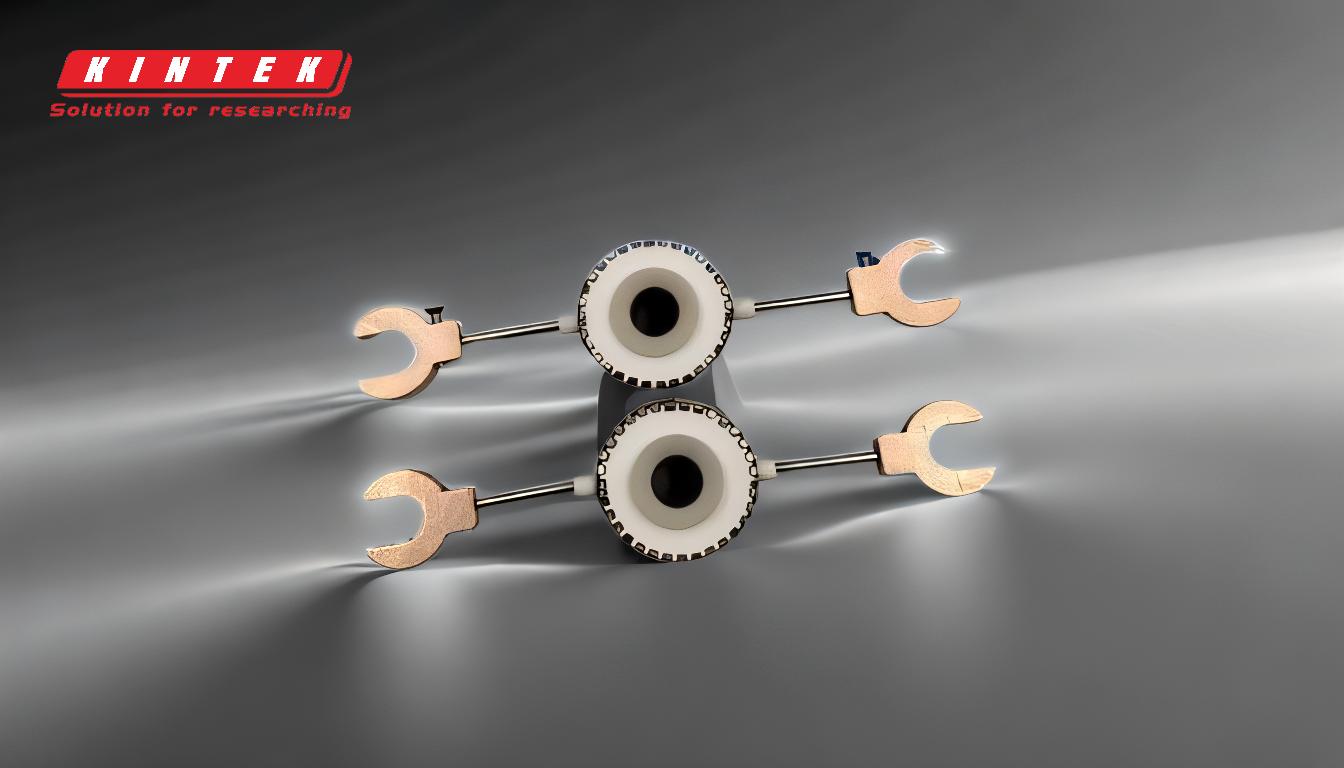
-
Vuoto o evaporazione termica:
- Processo:In questo metodo, il materiale da depositare viene riscaldato sotto vuoto fino a vaporizzarlo.Il vapore si condensa quindi sul substrato più freddo, formando un film sottile.
- Applicazioni:Questo metodo è comunemente utilizzato per depositare metalli, leghe e alcuni composti.È particolarmente utile per le applicazioni che richiedono elevata purezza e uniformità.
- Vantaggi:Elevata velocità di deposizione, buona uniformità e capacità di depositare un'ampia gamma di materiali.
- Limitazioni:Limitato ai materiali che possono essere vaporizzati a temperature ragionevoli e il processo può essere meno efficace per le geometrie complesse.
-
Placcatura ionica:
- Processo:La placcatura ionica prevede l'uso di un plasma per ionizzare il materiale vaporizzato prima che si depositi sul substrato.Ciò può avvenire per sputtering o per evaporazione, con l'aggiunta di un plasma per migliorare l'adesione e le proprietà del film.
- Applicazioni:Questo metodo è utilizzato per applicazioni che richiedono una forte adesione, come il rivestimento di utensili da taglio, componenti ottici e finiture decorative.
- Vantaggi:Migliore adesione, migliore densità e migliori proprietà del film grazie al bombardamento ionico.
- Limitazioni:Rispetto alla semplice evaporazione o allo sputtering, sono necessarie apparecchiature e controlli di processo più complessi.
-
Sputtering:
- Processo:Lo sputtering consiste nel bombardare un materiale bersaglio con ioni ad alta energia, facendo sì che gli atomi vengano espulsi dal bersaglio e depositati sul substrato.
- Applicazioni:Questo metodo è ampiamente utilizzato nell'industria dei semiconduttori, per il rivestimento di componenti ottici e nella produzione di celle solari a film sottile.
- Vantaggi:Capacità di depositare un'ampia gamma di materiali, compresi metalli, leghe e composti, con buona uniformità e controllo delle proprietà del film.
- Limitazioni:Tassi di deposizione inferiori rispetto all'evaporazione e il processo può essere più complesso e costoso.
-
Deposizione a fascio di ioni:
- Processo:In questo metodo, un fascio di ioni focalizzato viene utilizzato per spruzzare materiale da un bersaglio, che viene poi depositato sul substrato.Il fascio di ioni può essere diretto e controllato con grande precisione.
- Applicazioni:Questa tecnica è utilizzata per applicazioni che richiedono un controllo preciso dello spessore e della composizione del film, come nella produzione di dispositivi microelettronici e rivestimenti ottici.
- Vantaggi:Alta precisione e controllo del processo di deposizione, capacità di depositare materiali complessi.
- Limitazioni:Tassi di deposizione limitati e costi di attrezzatura più elevati.
-
Altre varianti:
- Deposizione di vapore ad arco:Questo metodo utilizza un arco elettrico per vaporizzare il materiale target, che viene poi depositato sul substrato.È particolarmente utile per depositare rivestimenti duri, come il nitruro di titanio.
- Deposizione laser pulsata (PLD):Nella PLD, un laser ad alta potenza viene utilizzato per ablare il materiale da un bersaglio, che viene poi depositato sul substrato.Questo metodo è utilizzato per depositare ossidi complessi e altri materiali con una stechiometria precisa.
In sintesi, le principali varianti di PVD - evaporazione termica o sotto vuoto, placcatura ionica e sputtering - hanno ciascuna processi, applicazioni, vantaggi e limiti unici.La comprensione di queste varianti è fondamentale per selezionare il metodo PVD appropriato per applicazioni specifiche, garantendo prestazioni ed efficienza ottimali nei processi di deposizione di film sottili.
Tabella riassuntiva:
Variante | Processo | Applicazioni | Vantaggi | Limitazioni |
---|---|---|---|---|
Evaporazione sotto vuoto | Il materiale viene riscaldato sotto vuoto fino alla vaporizzazione, quindi si condensa sul substrato. | Metalli, leghe, applicazioni ad alta purezza. | Elevata velocità di deposizione, buona uniformità, ampia gamma di materiali. | Limitato ai materiali vaporizzabili, meno efficace per geometrie complesse. |
Placcatura ionica | Utilizza il plasma per ionizzare il materiale vaporizzato prima della deposizione. | Utensili da taglio, componenti ottici, finiture decorative. | Migliore adesione, migliore densità, migliori proprietà del film. | Richiede attrezzature complesse e controllo del processo. |
Sputtering | Il materiale target viene bombardato con ioni, espellendo gli atomi per la deposizione. | Semiconduttori, componenti ottici, celle solari a film sottile. | Ampia gamma di materiali, buona uniformità, controllo preciso delle proprietà del film. | Tassi di deposizione inferiori, maggiore complessità e costo. |
Deposizione con fascio ionico | Il fascio di ioni focalizzato sputa il materiale per una deposizione precisa. | Microelettronica, rivestimenti ottici. | Alta precisione, capacità di depositare materiali complessi. | Tassi di deposizione limitati, costi più elevati delle apparecchiature. |
Altre varianti | Include la deposizione ad arco di vapore e la deposizione laser pulsata (PLD). | Rivestimenti duri (ad esempio, nitruro di titanio), ossidi complessi con stechiometria precisa. | Vantaggi specifici per applicazioni di nicchia. | Limitazioni diverse a seconda del metodo. |
Avete bisogno di aiuto per scegliere il metodo PVD più adatto alla vostra applicazione? Contattate i nostri esperti oggi stesso per soluzioni su misura!