Gli stampi a due piastre sono ampiamente utilizzati nello stampaggio a iniezione per la loro semplicità ed economicità.Tuttavia, presentano alcuni svantaggi, soprattutto nei progetti a più cavità.Una delle sfide principali consiste nel bilanciare il flusso di plastica fusa in più cavità, che può portare a un riempimento non uniforme e a difetti nel prodotto finale.Inoltre, l'allineamento della linea di divisione con la porta in uno stampo a due piastre può complicare il processo di progettazione e produzione.Queste limitazioni possono avere un impatto sull'efficienza, la qualità e il costo della produzione, rendendo essenziale un'attenta valutazione della loro idoneità per applicazioni specifiche.
Spiegazione dei punti chiave:
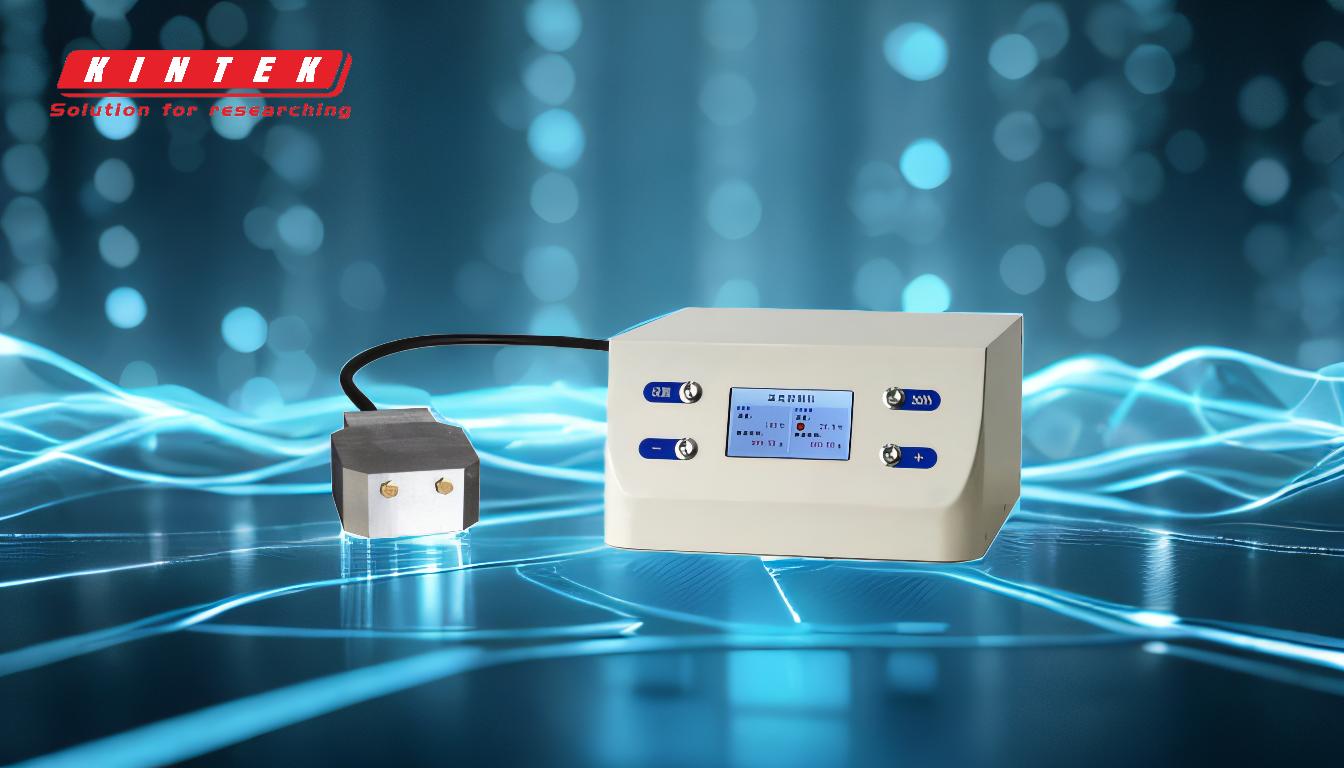
-
Sfide nel bilanciamento del flusso di plastica fusa:
- Negli stampi a due piastre a più cavità, è difficile garantire una distribuzione uniforme della plastica fusa in ogni cavità.
- Un flusso disomogeneo può causare difetti come scatti corti, deformazioni o dimensioni incoerenti dei pezzi.
- Questo problema si aggrava nei progetti complessi in cui le cavità sono situate a distanze diverse dalla porta.
-
Allineamento della linea di separazione con il gate:
- La linea di divisione in uno stampo a due piastre deve essere allineata con la porta, il che limita la flessibilità del progetto.
- Questo allineamento può complicare la progettazione dello stampo, soprattutto per i pezzi più complessi o per le configurazioni a più cavità.
- Inoltre, può aumentare il rischio di formazione di bolle o altri difetti sulla linea di divisione.
-
Flessibilità di progettazione limitata:
- Gli stampi a due piastre sono meno versatili rispetto agli stampi a tre piastre o ai sistemi a canale caldo.
- Non sono ideali per i pezzi che richiedono un rivestimento complesso o per quelli con requisiti estetici specifici.
- La semplicità degli stampi a due piastre spesso comporta una riduzione delle opzioni di personalizzazione.
-
Maggiore rischio di difetti:
- A causa delle difficoltà nel bilanciamento del flusso e nell'allineamento delle porte, gli stampi a due piastre sono più soggetti a difetti.
- I problemi più comuni sono le linee di saldatura, le trappole d'aria e la qualità incostante dei pezzi.
- Questi difetti possono aumentare gli scarti e i costi di produzione.
-
Tempi di ciclo più lunghi:
- I limiti degli stampi a due piastre possono comportare tempi di raffreddamento e di ciclo più lunghi.
- Ciò è particolarmente vero per gli stampi a più cavità, dove può verificarsi un raffreddamento non uniforme.
- Tempi di ciclo più lunghi riducono l'efficienza produttiva complessiva e aumentano i costi operativi.
-
Requisiti di manutenzione più elevati:
- La complessità del bilanciamento del flusso e dell'allineamento delle paratoie può comportare una maggiore usura dello stampo.
- Per garantire prestazioni costanti è necessaria una manutenzione regolare, che va ad aggiungersi al costo totale di proprietà.
-
Non adatto a tutte le applicazioni:
- Gli stampi a due piastre sono più adatti per i pezzi semplici con requisiti semplici di gating.
- Per i pezzi complessi o per le applicazioni ad alta precisione, possono essere più adatti stampi alternativi (ad esempio, stampi a tre piastre o sistemi a canale caldo).
Comprendendo questi svantaggi, i produttori possono decidere con cognizione di causa se uno stampo a due piastre è la scelta giusta per le loro specifiche esigenze di produzione.Sebbene offrano semplicità e risparmio, i loro limiti devono essere attentamente valutati rispetto ai requisiti del progetto.
Tabella riassuntiva:
Svantaggio | Impatto |
---|---|
Sfide di bilanciamento del flusso | Riempimento non uniforme, difetti come scatti corti, deformazioni o dimensioni incoerenti. |
Allineamento della linea di separazione | Flessibilità progettuale limitata, maggiore rischio di formazione di bolle. |
Flessibilità di progettazione limitata | Meno versatile per pezzi complessi o requisiti estetici specifici. |
Maggiore rischio di difetti | Le linee di saldatura, le trappole d'aria e la qualità incoerente dei pezzi aumentano la percentuale di scarti. |
Tempi di ciclo più lunghi | Un raffreddamento non uniforme porta a una riduzione dell'efficienza produttiva. |
Maggiore necessità di manutenzione | Aumenta l'usura e richiede una manutenzione regolare. |
Non adatto a tutte le applicazioni | Ideale per pezzi semplici; progetti complessi possono richiedere stampi alternativi. |
Avete bisogno di aiuto per scegliere lo stampo giusto per il vostro progetto? Contattate oggi stesso i nostri esperti per soluzioni su misura!