I sistemi a gas inerte sono ampiamente utilizzati nelle industrie per prevenire la combustione riducendo la concentrazione di ossigeno in uno spazio confinato.Se da un lato offrono notevoli vantaggi in termini di sicurezza, dall'altro presentano diversi svantaggi.Tra questi, gli elevati costi iniziali e operativi, la complessità della manutenzione, i potenziali pericoli derivanti da un uso improprio e le limitazioni in alcuni ambienti.La comprensione di questi inconvenienti è fondamentale per gli acquirenti di apparecchiature e materiali di consumo per prendere decisioni informate e garantire operazioni sicure ed efficienti.
Punti chiave spiegati:
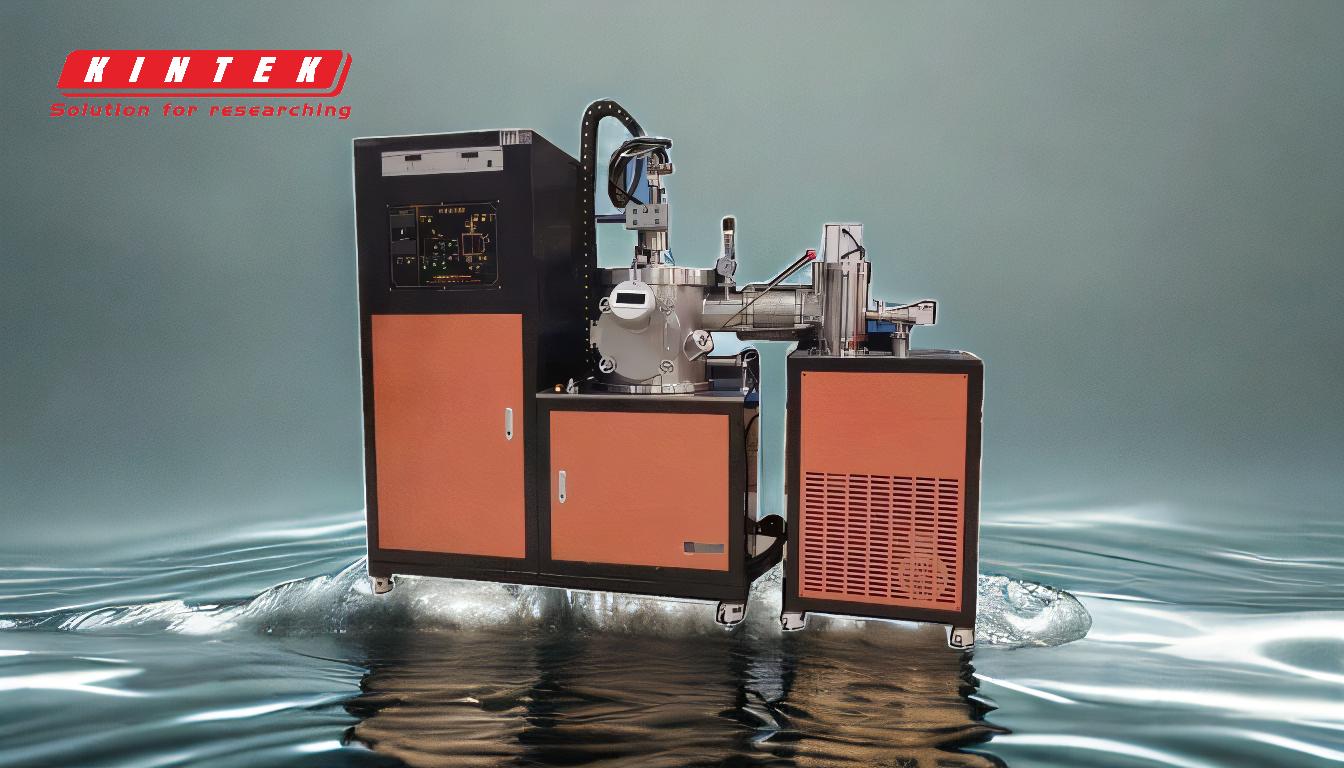
-
Alti costi iniziali e operativi:
- Investimento iniziale:I sistemi a gas inerte richiedono notevoli costi iniziali per le attrezzature, l'installazione e la configurazione.Ciò include l'acquisto di generatori di gas, serbatoi di stoccaggio e sistemi di distribuzione.
- Spese operative:I costi di manutenzione e funzionamento di questi sistemi possono essere significativi.Ciò include il costo dei gas inerti (ad esempio, azoto, argon), il consumo di energia per la generazione del gas e la manutenzione regolare.
- Impatto economico:Per le attività più piccole o per le industrie con budget limitati, questi costi possono essere proibitivi, rendendo difficile giustificare l'investimento.
-
Complessità nella manutenzione:
- Requisiti per la manutenzione regolare:I sistemi a gas inerte richiedono frequenti ispezioni, calibrazioni e interventi di manutenzione per garantirne il corretto funzionamento.Ciò può richiedere tempo e personale specializzato.
- Competenza tecnica:Una corretta manutenzione richiede spesso conoscenze e formazione specializzate, che potrebbero non essere facilmente disponibili in tutte le organizzazioni.
- Tempi di inattività:Le attività di manutenzione possono comportare tempi di inattività operativa, con ripercussioni sulla produttività e potenziali perdite finanziarie.
-
Potenziali pericoli derivanti da un uso improprio:
- Rischio di asfissia:I gas inerti possono sostituire l'ossigeno nell'aria, creando un rischio di asfissia per i lavoratori se il sistema non è gestito correttamente o se si verificano perdite.
- Errore umano:Un funzionamento errato o la mancata osservanza dei protocolli di sicurezza possono portare a situazioni pericolose, tra cui l'esaurimento dell'ossigeno in spazi ristretti.
- Perdite di gas:Le perdite nel sistema possono passare inosservate, provocando un graduale accumulo di gas inerte e rappresentando un grave rischio per la salute del personale.
-
Limitazioni in alcuni ambienti:
- Vincoli spaziali:I sistemi a gas inerte richiedono uno spazio adeguato per l'installazione, che potrebbe non essere disponibile in tutte le strutture, soprattutto negli impianti più vecchi o più piccoli.
- Problemi di compatibilità:Alcuni materiali o processi possono non essere compatibili con i gas inerti, limitandone l'applicabilità in alcuni settori.
- Condizioni ambientali:Temperature estreme o condizioni di umidità possono influire sulle prestazioni dei sistemi a gas inerte, richiedendo misure aggiuntive per garantire l'affidabilità.
-
Sfide normative e di conformità:
- Regolamenti severi:L'uso di sistemi a gas inerte è spesso soggetto a severi requisiti normativi, che possono variare a seconda della regione e del settore.La conformità a queste normative può essere complessa e costosa.
- Documentazione e rendicontazione:Le organizzazioni devono mantenere registrazioni dettagliate delle prestazioni del sistema, della manutenzione e dei controlli di sicurezza, con un ulteriore aggravio del carico amministrativo.
- Ispezione e audit:Le ispezioni e gli audit periodici da parte degli enti normativi possono richiedere tempo e risorse aggiuntive per risolvere i problemi individuati.
-
Impatto sulla qualità del prodotto:
- Rischi di contaminazione:In alcuni casi, l'introduzione di gas inerti può portare alla contaminazione dei prodotti, soprattutto in settori come quello alimentare o farmaceutico, dove la purezza è fondamentale.
- Interferenze di processo:La presenza di gas inerti può interferire con alcuni processi produttivi, incidendo potenzialmente sulla qualità o sulla resa del prodotto.
- Costo del controllo qualità:Potrebbero essere necessarie misure aggiuntive per monitorare e controllare l'impatto dei gas inerti sulla qualità del prodotto, con un aumento dei costi operativi.
In conclusione, se da un lato i sistemi a gas inerte offrono notevoli vantaggi in termini di sicurezza, dall'altro comportano una serie di svantaggi che devono essere attentamente considerati.I costi elevati, la complessità della manutenzione, i potenziali pericoli, le limitazioni ambientali, le sfide normative e l'impatto sulla qualità del prodotto sono tutti fattori che gli acquirenti di apparecchiature e materiali di consumo devono valutare quando decidono di implementare questi sistemi.Un'adeguata pianificazione, formazione e gestione continua sono essenziali per mitigare questi svantaggi e garantire un uso sicuro ed efficace dei sistemi a gas inerte.
Tabella riassuntiva:
Svantaggio | Dettagli principali |
---|---|
Alti costi iniziali e operativi | Costi iniziali considerevoli per le apparecchiature, l'installazione e la manutenzione continua. |
Complessità della manutenzione | Richiede ispezioni frequenti, personale specializzato e può causare tempi di inattività. |
Rischi potenziali | Rischio di asfissia, errore umano e perdite di gas se non gestite correttamente. |
Limitazioni in alcuni ambienti | Vincoli di spazio, problemi di compatibilità e sfide ambientali. |
Sfide normative e di conformità | Regolamenti severi, documentazione e ispezioni frequenti. |
Impatto sulla qualità del prodotto | Rischi di contaminazione, interferenze di processo e costi aggiuntivi per il controllo della qualità. |
Avete bisogno di aiuto per decidere se un sistema a gas inerte è adatto alla vostra attività? Contattate i nostri esperti oggi stesso per una consulenza personalizzata!