L'indurimento è un processo utilizzato per aumentare la durezza e la resistenza dei materiali, tipicamente metalli, attraverso il trattamento termico o altri metodi. Sebbene offra vantaggi significativi, come una migliore resistenza all’usura e una maggiore durata, presenta anche numerosi svantaggi. Questi includono maggiore fragilità, ridotta duttilità, potenziale di fessurazione e limitazioni nella selezione dei materiali. Inoltre, il processo può essere costoso, richiedere molto tempo e può introdurre tensioni residue che influiscono sulle prestazioni del materiale. Comprendere questi inconvenienti è fondamentale per prendere decisioni informate nella selezione e nell’applicazione dei materiali.
Punti chiave spiegati:
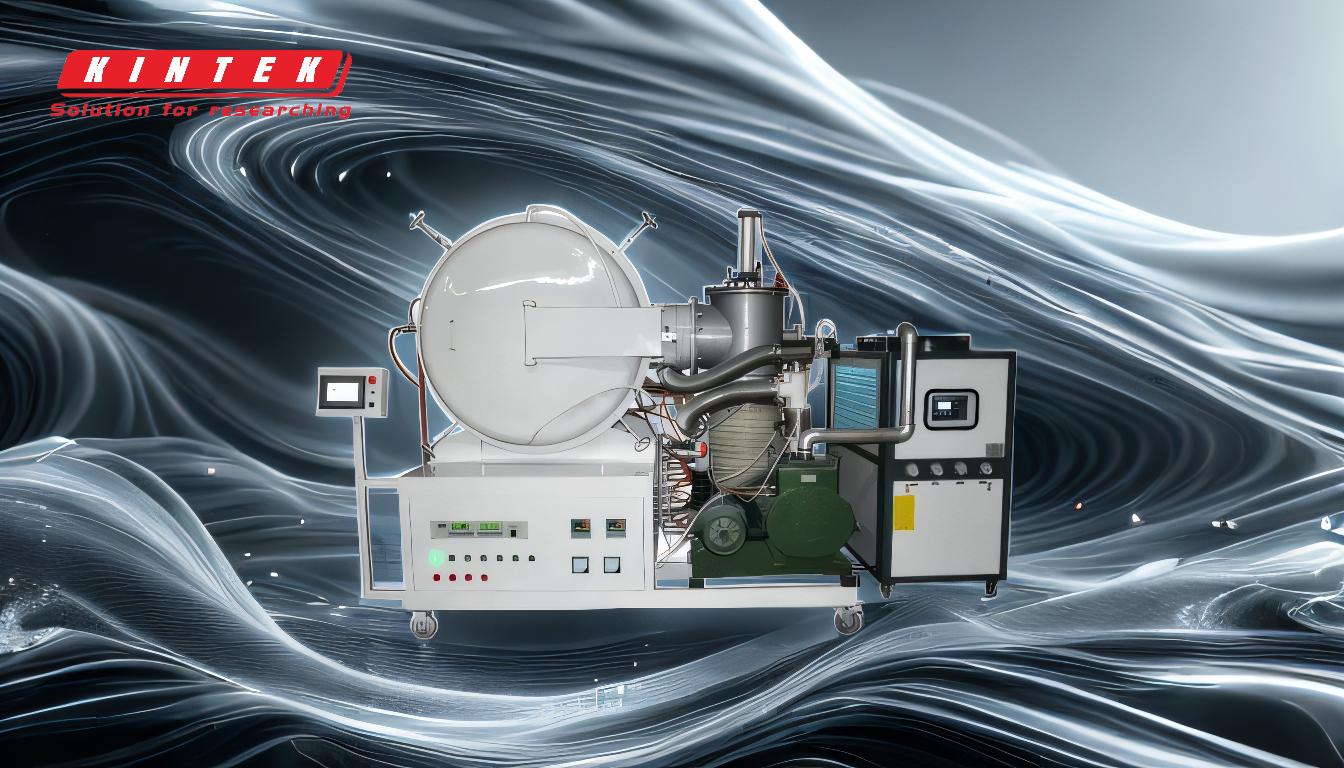
-
Maggiore fragilità:
- L'indurimento spesso porta ad un aumento significativo della fragilità, rendendo il materiale più incline a cedimenti improvvisi sotto impatto o stress.
- Ciò è particolarmente problematico nelle applicazioni in cui il materiale è soggetto a carichi dinamici o urti.
-
Duttilità ridotta:
- Il processo di indurimento riduce tipicamente la duttilità del materiale, il che significa che diventa meno capace di subire deformazioni plastiche senza rompersi.
- Questa riduzione della duttilità può limitare la capacità del materiale di assorbire energia, rendendolo inadatto per applicazioni che richiedono flessibilità.
-
Potenziale di cracking:
- Durante il processo di tempra, soprattutto nei metodi di raffreddamento rapido come la tempra, esiste un elevato rischio di fessurazione dovuta a stress termici.
- Le crepe possono compromettere l'integrità strutturale del materiale, portando a guasti prematuri.
-
Sollecitazioni residue:
- L'indurimento può introdurre tensioni residue all'interno del materiale, che possono portare a distorsioni o deformazioni.
- Queste sollecitazioni possono anche ridurre la durata a fatica del materiale, rendendolo più suscettibile a guasti sotto carico ciclico.
-
Limitazioni materiali:
- Non tutti i materiali sono adatti all'indurimento. Alcune leghe e metalli potrebbero non rispondere bene al processo, limitando la gamma di materiali che possono essere efficacemente induriti.
- Ciò può limitare le opzioni di progettazione e richiedere l’uso di materiali o trattamenti alternativi.
-
Considerazioni su costi e tempi:
- Il processo di indurimento può essere costoso e richiedere attrezzature specializzate e ambienti controllati.
- Richiede anche molto tempo, il che può aumentare i tempi di produzione e i costi complessivi.
-
Durezza superficiale e proprietà del nucleo:
- L'indurimento spesso dà come risultato una superficie molto più dura del nucleo del materiale. Questa discrepanza può portare a problemi come delaminazione o scheggiatura in determinate condizioni.
- Il bilanciamento della durezza superficiale con le proprietà del nucleo è una considerazione fondamentale nella progettazione e nell'applicazione di materiali temprati.
-
Preoccupazioni ambientali e di sicurezza:
- Il processo di indurimento, in particolare quelli che comportano alte temperature e trattamenti chimici, possono comportare rischi per l'ambiente e la sicurezza.
- La corretta gestione e smaltimento delle sostanze chimiche, nonché il rispetto dei protocolli di sicurezza, sono essenziali per mitigare questi rischi.
In sintesi, sebbene la tempra offra vantaggi significativi in termini di robustezza del materiale e resistenza all’usura, è essenziale considerare attentamente i suoi svantaggi. Questi includono maggiore fragilità, ridotta duttilità, potenziale di fessurazione, tensioni residue, limitazioni dei materiali, considerazioni su costi e tempi, discrepanze nelle proprietà della superficie del nucleo e preoccupazioni ambientali e di sicurezza. Comprendere questi inconvenienti consente un migliore processo decisionale nella selezione e nell'applicazione dei materiali, garantendo che i vantaggi dell'indurimento siano massimizzati e minimizzandone gli impatti negativi.
Tabella riassuntiva:
Svantaggio | Descrizione |
---|---|
Maggiore fragilità | Rischio più elevato di guasto improvviso sotto stress o impatto. |
Duttilità ridotta | Diminuzione della capacità di deformarsi senza rompersi, limitando la flessibilità. |
Potenziale di cracking | Elevato rischio di crepe dovute a stress termici durante il raffreddamento rapido. |
Sollecitazioni residue | Introduce tensioni interne, che portano a distorsioni o ridotta durata a fatica. |
Limitazioni materiali | Non tutti i materiali possono essere induriti, limitando le opzioni di progettazione. |
Considerazioni su costi e tempi | Processo costoso e dispendioso in termini di tempo che richiede attrezzature specializzate. |
Discrepanza superficie-nucleo | Superficie più dura rispetto al nucleo, con rischio di delaminazione o scheggiatura. |
Rischi ambientali e per la sicurezza | Le alte temperature e le sostanze chimiche pongono problemi di sicurezza e ambientali. |
Hai bisogno di aiuto per selezionare il materiale o il processo giusto? Contatta i nostri esperti oggi stesso per soluzioni su misura!