La sinterizzazione è un processo critico nella produzione di materiali, ma non è esente da problemi e difetti.I problemi più comuni sono l'eccessiva sinterizzazione, la sottointerizzazione, la formazione di bolle e la sudorazione, che possono compromettere la qualità e le prestazioni del prodotto finale.Inoltre, problemi come deformazioni e cedimenti dovuti alla gravità o all'attrito possono portare a difetti strutturali.La sinterizzazione ad alta temperatura, pur essendo efficace, consuma molta energia e può limitare la sintesi dei materiali e la stabilità delle fasi.I metodi di sinterizzazione tradizionali spesso richiedono un riscaldamento prolungato e temperature elevate, con conseguente crescita di grani e pori residui.Questi difetti e limiti evidenziano la necessità di un controllo preciso dei parametri di sinterizzazione per garantire risultati ottimali.
Punti chiave spiegati:
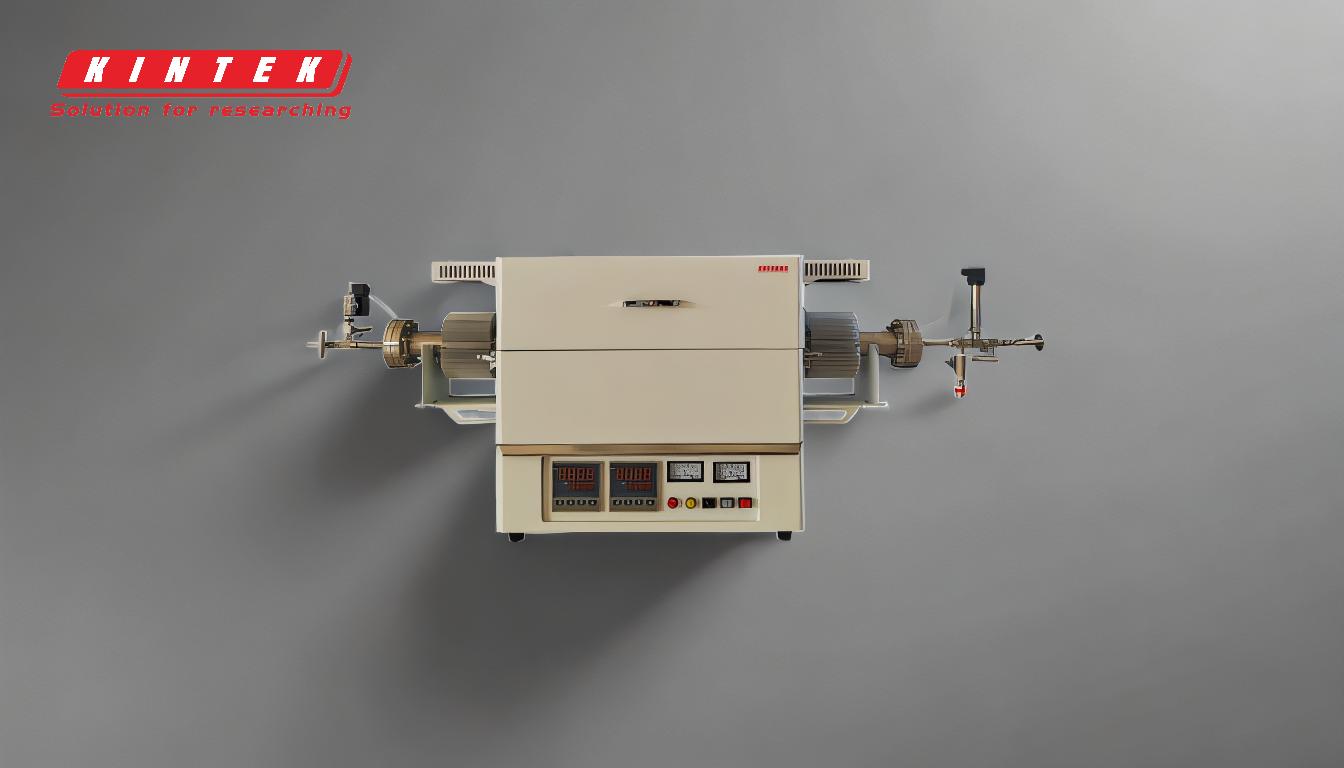
-
Sovrainteressamento:
- Definizione:Si verifica quando la temperatura di sinterizzazione è troppo alta o il tempo di sinterizzazione è troppo lungo.
- Impatto:Porta al deterioramento del prodotto, come la crescita eccessiva dei grani, la perdita delle proprietà meccaniche o addirittura la fusione del materiale.
- Esempio:Nella produzione di ceramica, la sovrasinterizzazione può causare la fragilità del materiale e la perdita della sua integrità strutturale.
-
Sottosinterizzazione:
- Definizione:Si verifica quando la temperatura di sinterizzazione è troppo bassa o il tempo di sinterizzazione è troppo breve.
- Impatto:Si ottiene un legame inadeguato tra le particelle, con conseguente scarsa resistenza meccanica e densificazione insufficiente.
- Esempio:Nella sinterizzazione delle polveri metalliche, la sinterizzazione può dare origine a un prodotto finale poroso con proprietà strutturali deboli.
-
Vesciche:
- Definizione:Difetti superficiali causati dal rilascio di gas intrappolati durante il processo di sinterizzazione.
- Impatto:Provoca imperfezioni superficiali, come bolle o vesciche, che possono compromettere la qualità estetica e funzionale del prodotto.
- Esempio:Nelle piastrelle di ceramica, la formazione di bolle può causare irregolarità superficiali inaccettabili per le finiture di alta qualità.
-
Sudorazione:
- Definizione:Si verifica quando una fase liquida fuoriesce dal materiale durante il trattamento termico.
- Impatto:Può causare contaminazione superficiale, distribuzione non uniforme del materiale e compromissione delle proprietà meccaniche.
- Esempio:In alcune leghe metalliche, la sudorazione può causare la segregazione degli elementi di lega, con conseguente incoerenza delle proprietà del materiale.
-
Deformazioni e cedimenti:
- Definizione:Deformazione del materiale dovuta alla gravità o all'attrito durante il processo di sinterizzazione.
- Impatto:Si verificano imprecisioni dimensionali e difetti strutturali nel pezzo finale.
- Esempio:Nella produzione additiva, la deformazione può far deviare le parti dalla forma prevista, richiedendo una post-lavorazione per correggerla.
-
Sfide della sinterizzazione ad alta temperatura:
- Definizione:Processi di sinterizzazione che richiedono temperature estremamente elevate.
- Impatto:Consuma più energia e può limitare i tipi di materiali che possono essere sinterizzati a causa di problemi di stabilità termica.
- Esempio:La sinterizzazione ad alta temperatura delle ceramiche può portare a instabilità di fase, in cui il materiale può subire trasformazioni di fase indesiderate.
-
Crescita dei grani e pori residui:
- Definizione:Problemi derivanti da tempi di sinterizzazione prolungati e da temperature elevate.
- Impatto:La crescita dei grani può ridurre la resistenza meccanica del materiale, mentre i pori residui possono compromettere la densità e l'integrità strutturale.
- Esempio:Nella metallurgia delle polveri, una crescita eccessiva dei grani può portare a una microstruttura grossolana, riducendo la tenacità del materiale.
-
Consumo di energia e impatto ambientale:
- Definizione:Elevati requisiti energetici per i metodi di sinterizzazione tradizionali.
- Impatto:Aumenta i costi di produzione e l'impronta ambientale, rendendo il processo meno sostenibile.
- Esempio:L'elevato consumo energetico dei forni di sinterizzazione contribuisce ad aumentare i costi operativi e le emissioni di carbonio.
-
Sfide del controllo di processo:
- Definizione:Difficoltà nel mantenere un controllo preciso sui parametri di sinterizzazione.
- Impatto:Risultati di sinterizzazione incoerenti, con conseguente variabilità della qualità del prodotto.
- Esempio:Un controllo incoerente della temperatura può dare origine a pezzi con densità e proprietà meccaniche variabili.
-
Limitazioni del materiale:
- Definizione:Vincoli sui tipi di materiali che possono essere efficacemente sinterizzati.
- Impatto:Limita la gamma di applicazioni e le potenziali innovazioni nella scienza dei materiali.
- Esempio:Alcuni materiali avanzati, come le ceramiche ad alte prestazioni, potrebbero non essere adatti ai metodi di sinterizzazione tradizionali a causa della loro sensibilità termica.
In conclusione, sebbene la sinterizzazione sia un potente processo produttivo, è essenziale comprenderne e mitigarne i potenziali difetti e limiti.Controllando attentamente i parametri di sinterizzazione ed esplorando metodi di sinterizzazione alternativi, i produttori possono migliorare la qualità dei prodotti e ampliare la gamma di materiali che possono essere efficacemente sinterizzati.
Tabella riassuntiva:
Difetto/Limitazione | Definizione | Impatto | Esempio |
---|---|---|---|
Svergolamento | Temperatura troppo alta o tempo troppo lungo. | Deterioramento del prodotto, crescita eccessiva dei grani o fusione. | La ceramica diventa fragile e perde integrità strutturale. |
Sinterizzazione | Temperatura troppo bassa o tempo troppo breve. | Scarsa resistenza meccanica e densificazione insufficiente. | La sinterizzazione delle polveri metalliche dà luogo a un prodotto poroso e debole. |
Vesciche | Gas intrappolati rilasciati durante la sinterizzazione. | Imperfezioni superficiali come bolle o vesciche. | Le piastrelle di ceramica sviluppano irregolarità superficiali. |
Sudorazione | La fase liquida fuoriesce durante il trattamento termico. | Contaminazione superficiale, distribuzione non uniforme del materiale. | Le leghe metalliche subiscono la segregazione degli elementi, con conseguente incoerenza delle proprietà. |
Deformazioni e cedimenti | Deformazione dovuta alla gravità o all'attrito. | Imprecisioni dimensionali e difetti strutturali. | I pezzi prodotti con la fabbricazione additiva si discostano dalle forme previste. |
Sfide ad alta temperatura | Sono richieste temperature estremamente elevate. | Elevato consumo di energia e limitazioni dei materiali. | La ceramica subisce trasformazioni di fase indesiderate. |
Crescita dei grani e pori | Riscaldamento prolungato e temperature elevate. | Resistenza meccanica ridotta e densità compromessa. | La metallurgia delle polveri produce microstrutture grossolane. |
Consumo di energia | Elevati requisiti energetici per la sinterizzazione tradizionale. | Aumento dei costi e dell'impatto ambientale. | I forni di sinterizzazione contribuiscono ad aumentare le emissioni di carbonio. |
Controllo del processo | Difficoltà a mantenere parametri di sinterizzazione precisi. | Qualità del prodotto incoerente. | I pezzi hanno densità e proprietà meccaniche diverse. |
Limitazioni dei materiali | Vincoli sui materiali sinterizzabili. | Limita le applicazioni e le innovazioni. | Le ceramiche ad alte prestazioni potrebbero non essere adatte alla sinterizzazione tradizionale. |
Problemi di difetti di sinterizzazione?Ottimizzate il vostro processo con una guida esperta. contattateci oggi stesso !