Lo sputtering, pur essendo una tecnica ampiamente utilizzata per la deposizione di film sottili, presenta diversi svantaggi degni di nota che possono influire sulla sua efficienza, sui costi e sull'idoneità per alcune applicazioni.Questi svantaggi includono spese di capitale elevate, bassi tassi di deposizione per alcuni materiali, potenziale contaminazione del film e difficoltà nel controllare lo spessore e l'uniformità del film.Inoltre, lo sputtering richiede spesso attrezzature e sistemi di raffreddamento complessi, che possono aumentare i costi operativi e ridurre i tassi di produzione.Il processo è anche meno compatibile con alcuni materiali, in particolare con i solidi organici, che possono degradarsi sotto il bombardamento ionico.Inoltre, lo sputtering può introdurre impurità nel substrato e il suo meccanismo di trasporto diffuso complica l'integrazione con i processi di lift-off per la strutturazione dei film.
Punti chiave spiegati:
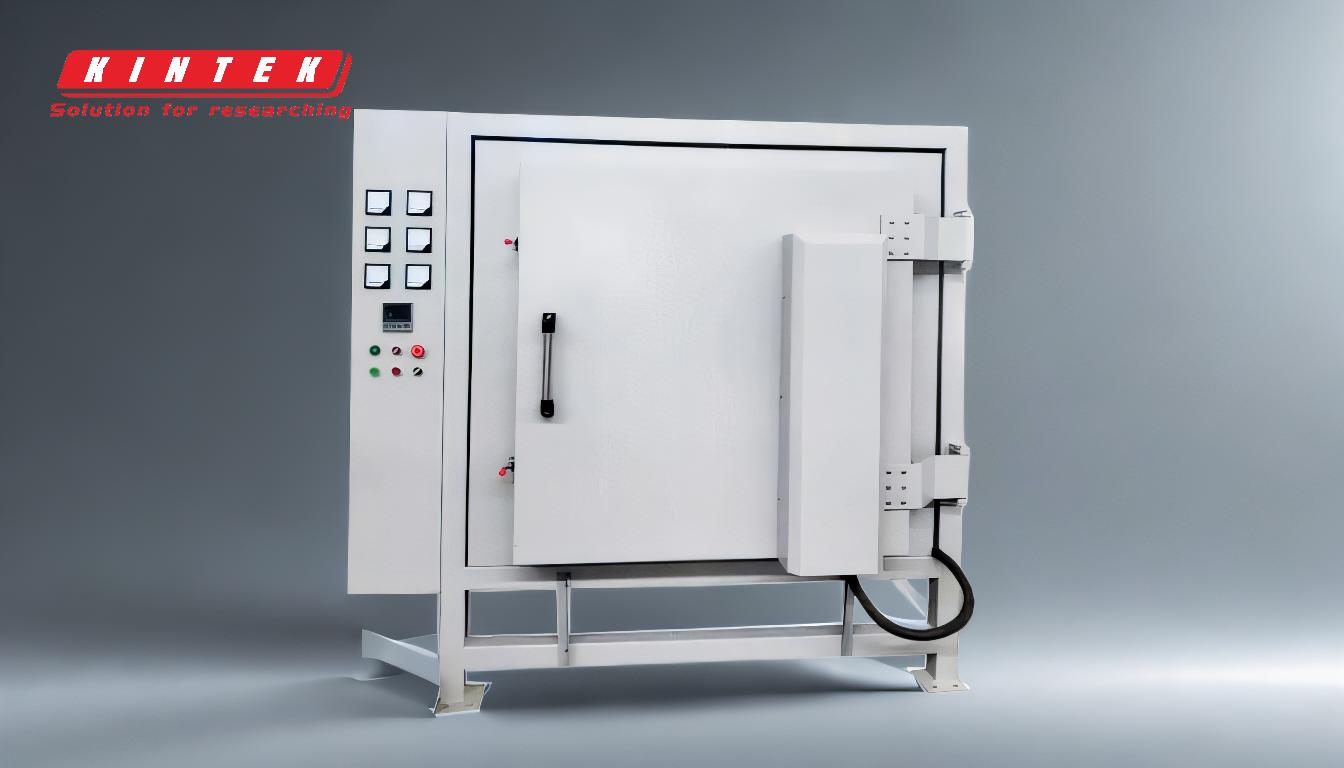
-
Spese di capitale elevate:
- Le apparecchiature di sputtering sono spesso costose e richiedono un investimento iniziale significativo.Ciò include il costo dei dispositivi ad alta pressione, dei sistemi di raffreddamento e di altri componenti specializzati.
- La necessità di un sistema di raffreddamento non solo aumenta il costo del capitale iniziale, ma incrementa anche le spese energetiche correnti, riducendo il rapporto costo-efficacia complessivo del processo.
-
Bassi tassi di deposizione:
- Lo sputtering ha generalmente tassi di deposizione più bassi rispetto ad altre tecniche come l'evaporazione termica.Ciò è particolarmente vero per alcuni materiali, come il SiO2, che possono rallentare i ritmi di produzione.
- Le basse velocità di sputtering possono rappresentare una limitazione significativa negli ambienti di produzione ad alta produttività, dove la velocità è fondamentale.
-
Contaminazione del film:
- Uno dei principali svantaggi dello sputtering è il rischio di contaminazione del film.Le impurità del materiale target o dell'ambiente di sputtering possono essere introdotte nel film, degradandone la qualità.
- I contaminanti gassosi presenti nel plasma possono attivarsi e incorporarsi nel film in crescita, aumentando ulteriormente il rischio di contaminazione.
- Nella deposizione sputter reattiva, è necessario un attento controllo della composizione del gas per evitare l'avvelenamento del bersaglio, che può anche portare alla contaminazione.
-
Difficoltà nel controllare lo spessore e l'uniformità del film:
- Il raggiungimento di uno spessore uniforme del film può essere un'impresa ardua nello sputtering a causa della distribuzione non uniforme del flusso di deposizione.Ciò richiede spesso l'uso di attrezzature mobili per garantire un rivestimento uniforme.
- Il trasporto diffuso degli atomi polverizzati rende difficile ottenere un'ombreggiatura completa, complicando l'integrazione con i processi di lift-off per la strutturazione del film.
-
Limitazioni dei materiali:
- Alcuni materiali, in particolare i solidi organici, sono suscettibili di degradazione sotto il bombardamento ionico inerente al processo di sputtering.Ciò limita la gamma di materiali che possono essere efficacemente depositati con questa tecnica.
- La selezione dei materiali di rivestimento è vincolata anche dalla loro temperatura di fusione, poiché i materiali con punti di fusione molto elevati potrebbero non essere adatti allo sputtering.
-
Introduzione delle impurità:
- Lo sputtering opera in un intervallo di vuoto inferiore rispetto all'evaporazione, il che aumenta la probabilità di introdurre impurità nel substrato.Ciò può influire sulla purezza e sulle prestazioni dei film depositati.
-
Apparecchiature complesse e manutenzione:
- Il processo di sputtering richiede attrezzature complesse, tra cui dispositivi ad alta pressione e sistemi di raffreddamento, che possono essere difficili da mantenere e gestire.
- La necessità di manutenzione da parte dell'utente e le limitazioni dei parametri di processo possono complicare ulteriormente l'uso dello sputtering nelle applicazioni industriali.
-
Elevata temperatura del substrato:
- Il processo di sputtering può causare un aumento significativo della temperatura del substrato, che può essere indesiderabile per i materiali o le applicazioni sensibili alla temperatura.
- Questo aumento di temperatura può anche rendere il substrato più suscettibile alla contaminazione da gas impuri.
In sintesi, sebbene lo sputtering sia una tecnica di deposizione versatile e ampiamente utilizzata, presenta diversi svantaggi che possono limitarne l'efficacia in alcune applicazioni.Tra questi, i costi elevati, i bassi tassi di deposizione, i rischi di contaminazione, le difficoltà di controllo delle proprietà del film, le limitazioni dei materiali e i requisiti complessi delle apparecchiature.La comprensione di questi inconvenienti è fondamentale per selezionare il metodo di deposizione appropriato per applicazioni specifiche e per ottimizzare il processo di sputtering per mitigarne i limiti.
Tabella riassuntiva:
Svantaggio | Descrizione |
---|---|
Spese di capitale elevate | Apparecchiature e sistemi di raffreddamento costosi aumentano i costi iniziali e correnti. |
Basse velocità di deposizione | I tassi più bassi per materiali come il SiO2 limitano la produzione ad alta produttività. |
Contaminazione del film | Le impurità provenienti dagli obiettivi o dal plasma possono degradare la qualità del film. |
Controllo dello spessore del film | Un flusso di deposizione non uniforme complica l'ottenimento di rivestimenti uniformi. |
Limitazioni dei materiali | I solidi organici si degradano sotto il bombardamento ionico; i materiali ad alta fusione sono meno adatti. |
Introduzione di impurità | Un intervallo di vuoto inferiore aumenta i rischi di impurità nei substrati. |
Apparecchiature complesse | I dispositivi ad alta pressione e i sistemi di raffreddamento richiedono una manutenzione significativa. |
Aumento della temperatura del substrato | I materiali sensibili alla temperatura possono degradarsi a causa del calore generato durante lo sputtering. |
Avete bisogno di aiuto per scegliere il giusto metodo di deposizione di film sottili? Contattate oggi stesso i nostri esperti per soluzioni su misura!