La sinterizzazione è un processo critico nella produzione di zirconia, in cui il calore viene utilizzato per fondere i materiali in una massa solida senza raggiungere lo stato liquido.Questo processo ha un impatto significativo sulla resistenza meccanica e sulla qualità complessiva del prodotto finale.Le condizioni di sinterizzazione, in particolare in un forno di forno di sinterizzazione della zirconia Il forno di sinterizzazione di zirconia è un'apparecchiatura che richiede un controllo preciso della temperatura, della pressione e dell'atmosfera.Il controllo della temperatura è particolarmente importante in quanto influenza la diffusione ai bordi dei grani e la diffusione in massa, che dipendono da fattori quali la dimensione delle particelle, la distribuzione del materiale, la composizione e l'ambiente di sinterizzazione.I forni di sinterizzazione avanzati, come quelli utilizzati nelle applicazioni dentali, sono dotati di regolatori ad alta precisione, elementi riscaldanti efficienti e sistemi di circolazione dell'aria ottimizzati per garantire una distribuzione uniforme del calore, mantenere i livelli di ossigeno e ottenere il colore e la finitura superficiale desiderati della zirconia sinterizzata.
Punti chiave spiegati:
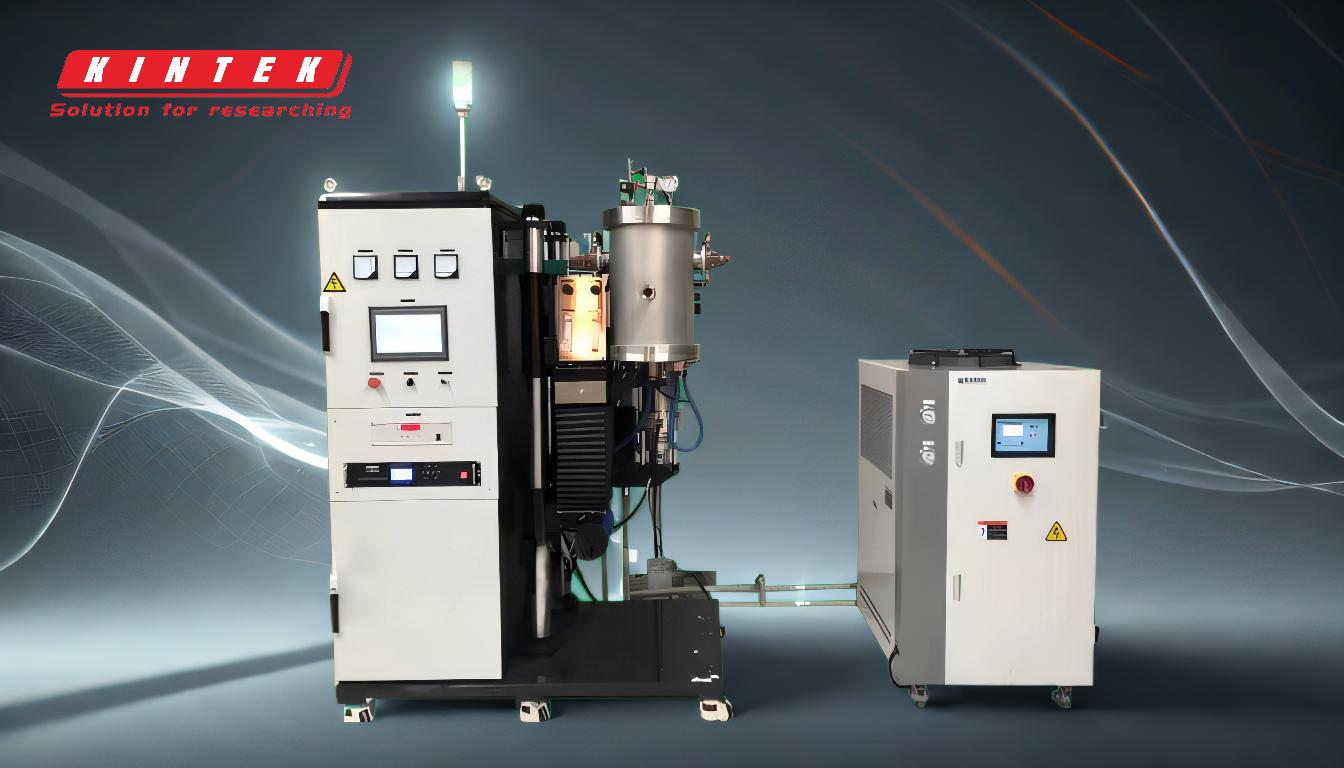
-
Controllo della temperatura:
- La temperatura è il fattore più critico nella sinterizzazione.Influisce direttamente sulla diffusione ai bordi dei grani e sulla diffusione in massa, che sono essenziali per ottenere un prodotto finale denso e resistente.
- I moderni forni di sinterizzazione, come il forno per la sinterizzazione della zirconia utilizzano sistemi di controllo intelligente della temperatura PID per mantenere temperature precise con un'accuratezza di ±1℃.
- I controllori basati sull'intelligenza artificiale sono utilizzati anche per garantire temperature uniformi in tutte le zone del forno, migliorando l'efficienza e riducendo il consumo energetico.
-
Elementi di riscaldamento e distribuzione del calore:
- Le barre di silicio molibdeno per uso dentale, di elevata purezza e non inquinanti, sono comunemente utilizzate nei forni di sinterizzazione per fornire una distribuzione uniforme del calore.
- Gli elementi riscaldanti avanzati assicurano che il calore venga trasferito uniformemente alla superficie della zirconia e condotto al suo nucleo, ottenendo un prodotto denso e meccanicamente resistente.
-
Fasi di sinterizzazione:
- Il processo di sinterizzazione consiste tipicamente in tre fasi: riscaldamento, sinterizzazione e raffreddamento.
- Nella fase di riscaldamento, il materiale viene portato gradualmente alla temperatura richiesta.
- Durante la fase di sinterizzazione, il materiale viene mantenuto a una temperatura specifica per consentire la diffusione e il legame delle particelle.
- La fase di raffreddamento è altrettanto importante, poiché un raffreddamento rapido o non uniforme può causare difetti nel prodotto finale.
-
Controllo dell'atmosfera:
- L'ambiente di sinterizzazione, compresi i livelli di ossigeno, deve essere attentamente controllato per ottenere il colore e la finitura superficiale desiderati della zirconia.
- Sistemi efficienti di circolazione dell'aria nei forni di sinterizzazione aiutano a mantenere livelli ottimali di ossigeno e a prevenire la contaminazione.
-
Programmazione e automazione:
- I moderni forni di sinterizzazione possono memorizzare più programmi (ad esempio, fino a 40 programmi) e sono dotati di interfacce di facile utilizzo, come i touch screen a colori da 7 pollici, per una facile modifica dei parametri.
- Le funzioni di memoria consentono al forno di riprendere le operazioni dal punto di interruzione in caso di interruzione di corrente, garantendo la coerenza del processo di sinterizzazione.
-
Efficienza e capacità:
- Alcuni forni di sinterizzazione offrono programmi di sinterizzazione rapida che completano il processo in soli 65 minuti, compresi riscaldamento, mantenimento in caldo e raffreddamento.
- Questi forni possono gestire grandi volumi, come impilare tre strati di crogioli e sinterizzare fino a 150 unità in un unico ciclo.
-
Considerazioni ambientali:
- Nei forni di sinterizzazione vengono utilizzati materiali isolanti ecologici per garantire temperature stabili e ridurre il consumo energetico.
- Questi materiali contribuiscono anche alla sostenibilità complessiva del processo di sinterizzazione.
Controllando attentamente queste condizioni, i forni di sinterizzazione assicurano la produzione di zirconia di alta qualità con le proprietà meccaniche, la finitura superficiale e il colore desiderati.
Tabella riassuntiva:
Condizione chiave | Descrizione |
---|---|
Controllo della temperatura | Controllo preciso (±1℃) mediante sistemi PID e AI per una distribuzione uniforme del calore. |
Elementi di riscaldamento | Le barre di silicio molibdeno di elevata purezza garantiscono un trasferimento uniforme del calore. |
Fasi di sinterizzazione | Le fasi di riscaldamento, sinterizzazione e raffreddamento sono gestite con attenzione per evitare difetti. |
Controllo dell'atmosfera | Livelli di ossigeno e circolazione dell'aria controllati per ottenere il colore e la finitura desiderati. |
Programmabilità | Fino a 40 programmi con touch screen da 7 pollici per una facile modifica dei parametri. |
Efficienza | Programmi di sinterizzazione rapidi (65 minuti) ed elevata capacità (150 unità per ciclo). |
Impatto ambientale | I materiali isolanti ecologici riducono il consumo energetico e migliorano la sostenibilità. |
Siete pronti a ottimizzare il vostro processo di sinterizzazione? Contattate oggi stesso i nostri esperti per soluzioni su misura!