Produzione di obiettivi
Metodi di produzione
Le lastre e i tubi dei target di sputtering sono fabbricati con metodi convenzionali adattati allo specifico sistema di materiali. Questi metodi comprendono una serie di tecniche, tra cui la fusione, la laminazione e la lavorazione, che vengono selezionate in base alle proprietà del materiale e alle specifiche del target desiderato. Ad esempio, i materiali con punti di fusione elevati, come il tungsteno e il molibdeno, spesso richiedono processi specializzati come la metallurgia delle polveri per ottenere la densità e l'omogeneità necessarie.
Nel caso dei compositi, che in genere sono costituiti da due o più materiali distinti, il processo di produzione diventa più complesso. La metallurgia delle polveri, un metodo versatile, è spesso utilizzata per combinare questi materiali in una struttura coesiva. Questo processo prevede diverse fasi: le materie prime vengono prima miscelate in una miscela omogenea di polveri, che viene poi compattata nella forma desiderata ad alta pressione. La forma compattata viene successivamente sinterizzata a temperature elevate per ottenere un legame tra le particelle, ottenendo un obiettivo denso e uniforme.
Per i materiali che richiedono livelli di purezza e controllo ancora più elevati, vengono utilizzate tecniche avanzate come la fusione ad arco sotto vuoto o la fusione a fascio elettronico. Questi metodi non solo migliorano la purezza del target, ma ne perfezionano anche la microstruttura, fondamentale per ottenere prestazioni di sputtering ottimali. La scelta del metodo di produzione è quindi un fattore critico nel determinare la qualità finale e le prestazioni del target di sputtering.
Tecniche di purificazione
Per ottenere bersagli sputtering di altissima purezza, la rimozione delle impurità è fondamentale. Questo processo può essere realizzato attraverso due metodi principali: la fusione a fascio elettronico in un sistema ad alto vuoto e la lisciviazione in sali reattivi. Ciascun metodo offre vantaggi unici ed è adatto a diversi tipi di materiali e requisiti di produzione.
Fusione a fascio di elettroni
La fusione a fascio di elettroni (EBM) opera in condizioni di alto vuoto, riducendo al minimo il rischio di contaminazione da gas atmosferici. Il processo consiste nel dirigere un fascio focalizzato di elettroni sul materiale target, facendolo fondere e poi solidificare. Questo metodo è particolarmente efficace per i materiali con elevati punti di fusione, poiché l'intenso calore generato dal fascio di elettroni può facilmente superare le loro temperature di fusione. L'ambiente ad alto vuoto garantisce l'evacuazione di eventuali gas residui, purificando ulteriormente il materiale.
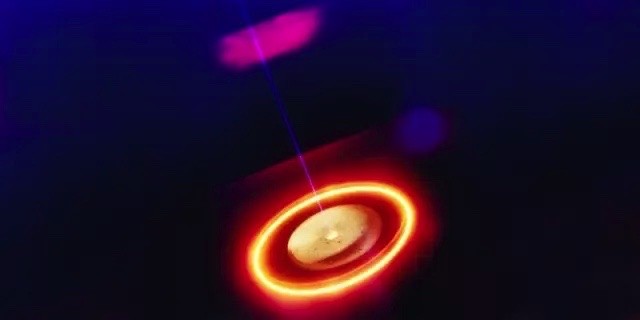
Lisciviazione in sali reattivi
La lisciviazione, invece, prevede l'immersione del materiale target in un bagno di sali reattivi. Questi sali reagiscono selettivamente con le impurità e le dissolvono, lasciando il materiale puro. Questa tecnica è spesso utilizzata per i materiali sensibili alle alte temperature o per quelli che richiedono un processo di purificazione più controllato. La scelta del sale e la durata del processo di lisciviazione sono fattori critici che possono influenzare in modo significativo la purezza del prodotto finale.
Entrambi i metodi sono componenti essenziali del processo di produzione dei target di sputtering ad altissima purezza e garantiscono che il prodotto finale soddisfi i rigorosi requisiti di purezza necessari per le applicazioni ad alte prestazioni.
Piastre di supporto/Tubo, saldatura e incollaggio per diffusione
Le piastre di supporto svolgono un ruolo cruciale nelle prestazioni dei target di sputtering, richiedendo proprietà quali bassa resistività, elevata permeabilità magnetica e buona conducibilità termica. Queste caratteristiche sono essenziali per garantire un trasferimento efficiente dell'energia e una distribuzione ottimale del campo magnetico durante il processo di sputtering.
Per fissare i target a queste piastre di supporto, si utilizzano due tecniche principali: la saldatura e l'incollaggio per diffusione.La saldatura prevede l'uso di un metallo d'apporto con un punto di fusione inferiore a quello dei materiali del target e della piastra di supporto. Questo metodo consente di controllare con precisione la resistenza e le proprietà termiche del legame, rendendolo adatto ad applicazioni che richiedono una gestione termica specifica.
Al contrario,l'incollaggio per diffusione è un processo di giunzione allo stato solido che non prevede la fusione dei materiali. Si basa invece sull'applicazione di pressione e temperatura elevate per creare un forte legame metallurgico tra il target e la piastra di supporto. Questa tecnica è particolarmente vantaggiosa per le applicazioni ad alta temperatura e per i materiali che possono degradarsi se esposti a temperature elevate, in quanto riduce al minimo i danni termici e garantisce un legame solido.
La scelta tra la saldatura e l'incollaggio per diffusione dipende spesso dai requisiti specifici dell'applicazione, comprese le proprietà dei materiali del target e della piastra di supporto, le condizioni operative e le caratteristiche di incollaggio desiderate. Entrambi i metodi sono parte integrante del successo dell'integrazione dei target con le piastre di supporto, garantendo la longevità e l'efficienza del processo di sputtering.
Uniformità del target di sputtering e qualità del film
Considerazioni macroscopiche e microscopiche
L'uniformità dei target di sputtering non è solo un attributo desiderabile, ma un fattore critico che influenza direttamente la qualità dei film depositati. Questa uniformità è influenzata da una combinazione di caratteristiche macroscopiche e microscopiche, ognuna delle quali svolge un ruolo significativo nel determinare la velocità di sputtering e il processo complessivo di formazione del film.
Fattori macroscopici:
- Porosità: La presenza di pori all'interno del materiale di destinazione può portare a incongruenze nel processo di sputtering. I pori agiscono come barriere, interrompendo il flusso uniforme di atomi dal target al substrato. Ciò può comportare uno spessore e una composizione non uniformi del film, a scapito delle prestazioni del prodotto finale.
- Dimensione dei grani: La dimensione dei grani all'interno del materiale di destinazione è un altro fattore macroscopico che influisce sull'uniformità. I grani più grandi possono portare a tassi di sputtering non uniformi, in quanto il processo di rimozione del materiale diventa meno coerente sulla superficie del target.
Fattori microscopici:
- Orientamento dei cristalli: A livello microscopico, l'orientamento dei grani di cristallo all'interno del materiale target gioca un ruolo cruciale. Diversi orientamenti dei cristalli presentano velocità di sputtering diverse, un fenomeno noto come sputtering preferenziale. Ciò può causare variazioni localizzate nella composizione e nella struttura del film, influenzandone la qualità e le prestazioni complessive.
Controllando attentamente i fattori macroscopici e microscopici, i produttori possono garantire un processo di sputtering più uniforme, che porta a film di qualità superiore con proprietà costanti.
Porosità e vuoti
La porosità e i vuoti sono difetti critici che possono insorgere in varie fasi del processo di produzione, con un impatto significativo sull'uniformità della velocità di sputtering e sulla qualità complessiva del film depositato. Questi difetti spesso derivano dalle limitazioni intrinseche dei metodi di produzione convenzionali, come la colata, la metallurgia delle polveri e persino durante le fasi di purificazione, dove i processi ad alta temperatura possono introdurre incongruenze microstrutturali.
Ad esempio, nella metallurgia delle polveri, il consolidamento delle polveri metalliche in forma solida può lasciare vuoti microscopici se il processo di sinterizzazione non è perfettamente controllato. Analogamente, durante la fusione, l'intrappolamento di gas può creare porosità, soprattutto nei materiali con punti di fusione elevati, dove la viscosità del metallo fuso può impedire la fuoriuscita dei gas. Questi vuoti e pori possono agire come siti preferenziali per l'innesco di cricche, portando a velocità di sputtering non uniformi e a una scarsa qualità del film.
Inoltre, la presenza di porosità e vuoti può influenzare la conducibilità termica ed elettrica del materiale target, complicando ulteriormente il processo di sputtering. Ad esempio, le regioni con un'elevata porosità possono effettuare lo sputtering a velocità diverse rispetto alle aree più dense, con conseguenti variazioni nello spessore e nella composizione del film. Questa non uniformità è particolarmente problematica nelle applicazioni in cui le proprietà precise del film sono critiche, come nella produzione di semiconduttori.
Sputtering preferenziale e morfologia dei grani
Le diverse orientazioni dei cristalli presentano velocità di sputtering variabili, un fenomeno noto comesputtering preferenziale. Questa erosione selettiva può influenzare in modo significativo lamorfologia dei grani e dimensionedimensione del materiale, che sono direttamente influenzate dai processi di produzione impiegati.
Nel contesto delladeposizione fisica da vapore (PVD) l'uniformità del film spruzzato dipende in larga misura dalla consistenza del materiale di destinazione. Lastruttura dei grani del target, caratterizzata dalla sua orientazione e dimensione, gioca un ruolo cruciale nel determinare l'efficienza dello sputtering e la qualità del film risultante. Ad esempio, i grani con determinate orientazioni possono erodere più rapidamente, portando a uno sputtering non uniforme e compromettendo potenzialmente l'integrità del film depositato.
I processi di produzione, come lametallurgia delle polveri epressatura isostatica a caldo (HIP)sono determinanti per modellare la struttura dei grani del materiale di destinazione. Questi processi non solo influenzano la densità e la porosità del target, ma dettano anche la morfologia finale dei grani, che a sua volta influisce sul comportamento dello sputtering. Pertanto, la comprensione e il controllo di questi parametri di produzione sono essenziali per ottimizzare le prestazioni dei target di sputtering PVD.
Pressatura isostatica a caldo (HIP) e trattamento termico ad alta pressione (HPHT)
Applicazioni HIP
La pressatura isostatica a caldo (HIP) è un processo critico nella produzione di target di sputtering di alta qualità, in particolare per i materiali prodotti mediante fusione e metallurgia delle polveri. La funzione principale dell'HIP è quella di eliminare la porosità e i vuoti all'interno di questi materiali, migliorandone così la densità e l'uniformità. Questo processo prevede di sottoporre il materiale ad alta pressione e temperatura in un ambiente controllato, che lo comprime e lo costringe a raggiungere una densità quasi perfetta.
L'importanza dell'HIP nel ridurre la porosità non può essere sopravvalutata. La porosità, che può derivare da vari processi di produzione, influisce significativamente sulla velocità di sputtering e sulla qualità complessiva del film formato. Eliminando questi vuoti microscopici, l'HIP assicura che il target di sputtering si comporti in modo uniforme durante il processo di sputtering, portando a una deposizione più uniforme del film.
Inoltre, l'HIP contribuisce all'integrità strutturale dei target di sputtering. I materiali sottoposti a HIP presentano proprietà meccaniche superiori, tra cui una maggiore resistenza e tenacità. Ciò è particolarmente importante per le applicazioni ad alte prestazioni, dove l'affidabilità e la longevità dei target di sputtering sono fondamentali.
In sintesi, l'HIP è una tecnica indispensabile per la produzione di bersagli di sputtering, che garantisce la conformità ai severi requisiti di alta densità, uniformità e integrità strutturale.
Vantaggi dell'HPHT
Il trattamento ad alta pressione e alta temperatura (HPHT) offre diversi vantaggi nella produzione di vari sistemi di materiali. Uno dei vantaggi principali è la migliore uniformità della temperatura, che garantisce che l'intero sistema di materiali sia sottoposto a condizioni termiche coerenti. Questa uniformità è fondamentale per mantenere l'integrità e le prestazioni del prodotto finale.
L'HPHT consente inoltre di controllare la velocità di raffreddamento, un fattore essenziale per evitare stress termici e cricche nei materiali. Gestendo con precisione il processo di raffreddamento, i produttori possono ottenere le proprietà meccaniche desiderate e ridurre al minimo i difetti. Questo livello di controllo è particolarmente importante nella produzione di materiali di alto valore come i diamanti, dove anche piccole imperfezioni possono avere un impatto significativo sulla qualità e sul valore di mercato.
Inoltre, l'HPHT facilita la ripetibilità dei tempi di processo, garantendo che ogni lotto di materiali sia prodotto in condizioni identiche. Questa ripetibilità è fondamentale per mantenere costanti la qualità e le prestazioni del prodotto. Per esempio, nell'industria dei diamanti, l'HPHT può trasformare i diamanti meno attraenti in diamanti di alta qualità, incolori, rosa, blu o giallo canarino, aumentandone significativamente il valore di mercato.
Il processo HPHT consiste nel sottoporre i diamanti a pressione e temperatura elevate, che non solo ne migliorano il colore, ma ne esaltano anche la limpidezza. Questo rende i diamanti HPHT molto desiderabili nell'industria della gioielleria, dove la chiarezza e il colore sono fattori determinanti per la qualità di un diamante. Nonostante alcune differenze tra i diamanti HPHT e quelli CVD (Chemical Vapor Deposition), il trattamento HPHT viene spesso utilizzato per migliorare la finitura dei diamanti CVD, assicurando che soddisfino gli standard di alta qualità.
In sintesi, il trattamento HPHT offre una serie di vantaggi essenziali per la produzione di materiali di alta qualità. La sua capacità di fornire una migliore uniformità di temperatura, velocità di raffreddamento controllate e tempi di processo ripetibili lo rende una tecnica preziosa in diversi settori, in particolare nella produzione di materiali di alto valore come i diamanti.
HIP incannulata e incollaggio per diffusione
Le tecniche di pressatura isostatica a caldo incannulata (HIP) e di incollaggio per diffusione sono parte integrante della produzione di forme complesse e garantiscono un solido incollaggio tra il target e la piastra di supporto. Questi metodi sono particolarmente vantaggiosi quando si tratta di materiali pregiati che richiedono proprietà superiori come la resistenza alla corrosione e all'usura, spesso applicati su substrati più economici per ottimizzare l'efficienza dei costi.
L'HIP può facilitare più legami di diffusione in un singolo ciclo di processo, rendendolo una soluzione versatile ed efficiente per le esigenze di produzione complesse. La tecnica è compatibile con un'ampia gamma di materiali, tra cui metalli come il nichel, il cobalto, il tungsteno, il titanio, il molibdeno, l'alluminio, il rame e le leghe a base di ferro, oltre a ceramiche, vetri, intermetalli e plastiche ad alte prestazioni.
Il processo prevede un controllo rigoroso della purezza del gas inerte, in genere utilizzando l'argon, per soddisfare o superare le specifiche dei clienti, delle forze armate e dell'industria. I cicli HIP riproducibili e automatizzati sono personalizzati per soddisfare le esigenze specifiche dei clienti, garantendo la tracciabilità dei componenti dall'inizio alla fine. Inoltre, è disponibile un supporto tecnico per l'HIP di nuovi materiali o leghe e il processo è adattabile a vari requisiti di utensili, garantendo la compatibilità con il ciclo HIP e le specifiche del materiale.
Sfruttando l'HIP cannulato e l'incollaggio per diffusione, i produttori possono ottenere non solo legami forti e affidabili, ma anche la produzione di geometrie complesse che sarebbe difficile ottenere con altri metodi. La versatilità e la precisione rendono queste tecniche indispensabili per la produzione di target di sputtering di alta qualità.
CONTATTATECI PER UNA CONSULENZA GRATUITA
I prodotti e i servizi di KINTEK LAB SOLUTION sono stati riconosciuti da clienti di tutto il mondo. Il nostro personale sarà lieto di assistervi per qualsiasi richiesta. Contattateci per una consulenza gratuita e parlate con uno specialista del prodotto per trovare la soluzione più adatta alle vostre esigenze applicative!