La distanza del substrato di destinazione nello sputtering è un parametro critico che influenza direttamente la qualità, l'uniformità e lo spessore del film sottile depositato.Questa distanza deve essere attentamente controllata per garantire condizioni di deposizione ottimali, poiché influisce sull'energia cinetica delle particelle sputate, sulla loro direzionalità e sulla velocità di deposizione complessiva.La distanza ideale tra il target e il substrato varia in base a fattori quali il metodo di sputtering, il materiale del target, il materiale del substrato, la pressione della camera e la potenza di sputtering.In genere, si utilizza una distanza compresa tra 5 e 15 cm, ma applicazioni specifiche possono richiedere aggiustamenti per ottenere le proprietà del film desiderate.Una spaziatura adeguata garantisce una copertura uniforme, riduce al minimo i difetti e migliora la qualità complessiva del rivestimento.
Spiegazione dei punti chiave:
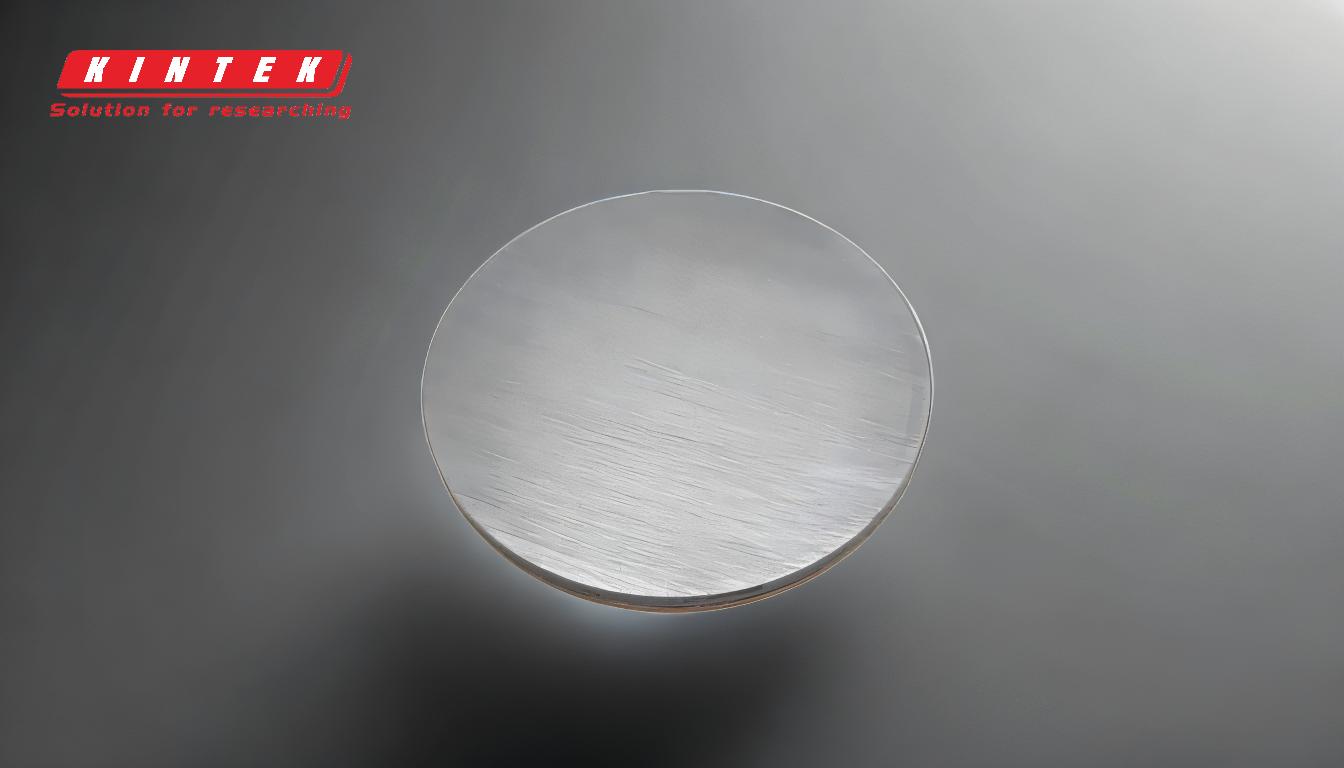
-
Importanza della distanza del substrato di destinazione:
- La distanza tra il target e il substrato è fondamentale per ottenere una deposizione uniforme di film sottile.
- Essa influisce sull'energia cinetica e sulla direzionalità delle particelle polverizzate, che a loro volta influenzano lo spessore, l'uniformità e la qualità del film.
- Una spaziatura adeguata garantisce tassi di deposizione costanti e riduce al minimo i difetti, come i rivestimenti non uniformi o i vuoti.
-
Intervallo tipico per la distanza del substrato di destinazione:
- Un intervallo comune per la distanza del substrato bersaglio nello sputtering è di da 5 a 15 cm .
- Questo intervallo è adatto alla maggior parte delle applicazioni standard di sputtering, fornendo un equilibrio tra velocità di deposizione e qualità del film.
- Tuttavia, la distanza esatta può essere regolata in base a specifici requisiti sperimentali o industriali.
-
Fattori che influenzano la distanza ottimale:
- Metodo sputtering:Le diverse tecniche di sputtering (ad esempio, CC, RF, magnetron) possono richiedere distanze diverse a causa delle differenze nell'energia degli ioni e nei meccanismi di deposizione.
- Materiali del target e del substrato:La massa e le proprietà dei materiali del target e del substrato influenzano la resa dello sputtering e il comportamento delle particelle.
- Pressione della camera:Pressioni più elevate possono ridurre il percorso libero medio delle particelle, richiedendo distanze più brevi per mantenere l'efficienza della deposizione.
- Potenza di sputtering:Livelli di potenza più elevati possono aumentare l'energia delle particelle polverizzate, consentendo potenzialmente di raggiungere distanze maggiori dal substrato di destinazione senza compromettere la qualità del film.
-
Impatto sulla velocità di deposizione e sulla qualità del film:
- Tasso di deposizione:Una distanza inferiore aumenta generalmente la velocità di deposizione a causa della riduzione della dispersione delle particelle e del maggiore flusso di particelle sul substrato.
- Qualità del film:Una distanza maggiore può migliorare l'uniformità del film consentendo alle particelle di distribuirsi in modo più uniforme sul substrato, ma può anche ridurre l'efficienza di deposizione.
-
Considerazioni pratiche sulla configurazione dell'apparecchiatura:
- Uniformità:Per ottenere uno spessore uniforme del film è essenziale che il substrato sia posizionato parallelamente alla superficie di destinazione.
- Regolabilità:I sistemi di sputtering devono consentire una regolazione precisa della distanza del substrato target per adattarsi a materiali e condizioni di processo diversi.
- Monitoraggio:Il monitoraggio in tempo reale dello spessore e della qualità del film può aiutare a ottimizzare la distanza durante il processo di sputtering.
-
Regolazioni specifiche per l'applicazione:
- Rivestimenti di alta precisione:Per le applicazioni che richiedono rivestimenti estremamente uniformi o privi di difetti, può essere necessario ridurre al minimo e controllare attentamente la distanza del substrato di destinazione.
- Deposizione su larga scala:In ambito industriale, è possibile utilizzare distanze maggiori per rivestire substrati più grandi o più substrati contemporaneamente, anche se ciò può richiedere la regolazione di altri parametri (ad esempio, potenza, pressione) per mantenere la qualità.
-
Ottimizzazione sperimentale:
- La distanza ottimale dal substrato viene spesso determinata sperimentalmente per applicazioni specifiche.
- Fattori quali lo spessore del film desiderato, le dimensioni del substrato e le proprietà del materiale devono guidare il processo di ottimizzazione.
In sintesi, la distanza del substrato di destinazione nello sputtering è un parametro chiave che deve essere attentamente controllato per ottenere una deposizione di film sottile di alta qualità.Sebbene si utilizzi comunemente un intervallo generale compreso tra 5 e 15 cm, la distanza esatta deve essere adattata al metodo di sputtering specifico, ai materiali e ai requisiti dell'applicazione.Una spaziatura adeguata garantisce una deposizione uniforme, riduce al minimo i difetti e migliora le prestazioni complessive del substrato rivestito.
Tabella riassuntiva:
Fattore chiave | Impatto sulla distanza del substrato di destinazione |
---|---|
Gamma tipica | Da 5 a 15 cm |
Metodo di sputtering | Lo sputtering a corrente continua, a radiofrequenza o a magnetron può richiedere la regolazione della distanza per ottenere l'energia e la resa ottimale degli ioni. |
Materiali del target/substrato | La massa e le proprietà del materiale influenzano la resa dello sputtering e il comportamento delle particelle. |
Pressione della camera | Una pressione più elevata può richiedere distanze più brevi per mantenere l'efficienza di deposizione. |
Potenza di sputtering | Una potenza più elevata consente di raggiungere distanze maggiori senza compromettere la qualità del film. |
Velocità di deposizione | Le distanze ridotte aumentano la velocità di deposizione; le distanze più lunghe migliorano l'uniformità. |
Esigenze specifiche dell'applicazione | Rivestimenti di alta precisione o deposizioni su larga scala possono richiedere distanze personalizzate. |
Avete bisogno di aiuto per ottimizzare il vostro processo di sputtering? Contattate i nostri esperti oggi stesso per soluzioni su misura!