L'evaporazione a fascio di elettroni e i sistemi di sputtering ionico sono entrambe tecniche di deposizione fisica del vapore (PVD) utilizzate per creare film sottili, ma differiscono significativamente nei meccanismi, nei parametri operativi e nelle applicazioni.L'evaporazione a fascio di elettroni utilizza un fascio di elettroni focalizzato per riscaldare e vaporizzare materiali ad alta temperatura, ottenendo un'elevata velocità di deposizione e l'idoneità per applicazioni come pannelli solari e vetro.Lo sputtering, invece, consiste nel bombardare un materiale bersaglio con ioni energetici per espellere gli atomi, che poi si depositano su un substrato.Lo sputtering opera a temperature più basse, garantisce una migliore adesione e omogeneità del film ed è ideale per substrati complessi e film sottili di elevata purezza.Ciascun metodo presenta vantaggi distinti a seconda dei requisiti specifici del progetto.
Punti chiave spiegati:
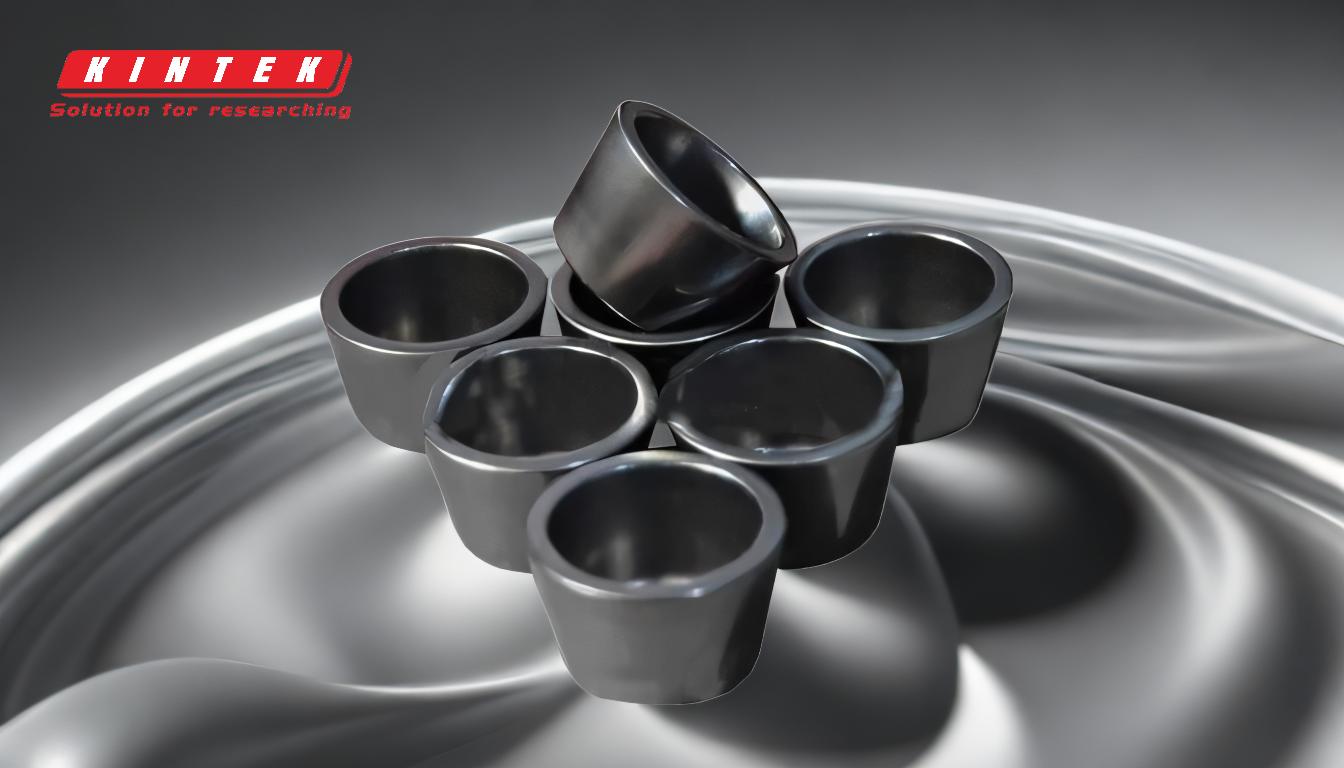
-
Meccanismo di deposizione:
- Evaporazione a fascio di elettroni:Utilizza un fascio di elettroni focalizzato per riscaldare e vaporizzare il materiale di partenza.Il materiale vaporizzato si condensa sul substrato formando un film sottile.
- Sputtering ionico:Si tratta di bombardare un materiale bersaglio con ioni energetici (in genere argon) in un ambiente di plasma.La collisione espelle gli atomi dal bersaglio, che si depositano sul substrato.
-
Ambiente operativo:
- Evaporazione a fascio di elettroni:Richiede un ambiente ad alto vuoto per ridurre al minimo la contaminazione e garantire una vaporizzazione efficiente.
- Sputtering ionico:Funziona in un ambiente a vuoto ridotto e spesso all'interno di un campo magnetico chiuso per migliorare la ionizzazione e l'efficienza di deposizione.
-
Velocità di deposizione:
- Evaporazione a fascio di elettroni:Offre una velocità di deposizione più elevata, che la rende adatta ad applicazioni che richiedono una rapida formazione del film.
- Sputtering ionico:In genere ha una velocità di deposizione inferiore, soprattutto per i materiali dielettrici, ma offre un migliore controllo delle proprietà del film.
-
Adesione e qualità del film:
- Evaporazione a fascio di elettroni:Produce film con minore adesione e minore omogeneità, che possono richiedere trattamenti post-deposizione.
- Sputtering ionico:Garantisce una migliore adesione, una maggiore omogeneità del film e granulometrie più piccole, per ottenere film sottili di qualità superiore.
-
Requisiti di temperatura:
- Evaporazione a fascio di elettroni:Richiede temperature elevate per vaporizzare il materiale di partenza, il che può limitarne l'uso con substrati sensibili alla temperatura.
- Sputtering ionico:Funziona a temperature più basse, rendendola adatta a materiali sensibili alla temperatura e a substrati complessi.
-
Scalabilità e automazione:
- Evaporazione a fascio di elettroni:Meno scalabile e più difficile da automatizzare a causa della dipendenza dall'alto vuoto e dal controllo preciso del fascio di elettroni.
- Sputtering ionico:Più scalabile e più facile da automatizzare, ideale per la produzione su larga scala e le applicazioni industriali.
-
Applicazioni:
- Evaporazione a fascio di elettroni:Comunemente utilizzato in applicazioni come pannelli solari, rivestimenti di vetro e film ottici, grazie alla sua elevata velocità di deposizione.
- Sputtering ionico:Preferito per la produzione elettrica e ottica, per i film sottili di elevata purezza e per i rivestimenti su substrati complessi, grazie alla qualità superiore del film e all'adesione.
-
Energia delle specie depositate:
- Evaporazione a fascio di elettroni:Produce specie di vapore a bassa energia, che possono dare origine a film meno densi.
- Sputtering ionico:Espelle gli atomi a più alta energia, dando origine a film più densi e aderenti.
-
Assorbimento di gas:
- Evaporazione a fascio di elettroni:Meno incline all'assorbimento di gas grazie all'ambiente ad alto vuoto.
- Sputtering ionico:È più probabile che assorba gas, il che può influire sulle proprietà del film, ma consente anche lo sputtering reattivo per creare film composti.
-
Direzionalità delle particelle atomizzate:
- Evaporazione a fascio di elettroni:Produce un flusso di vapore più disperso, che può portare a una deposizione meno direzionale.
- Sputtering ionico:Espelle le particelle in modo più direzionale, migliorando la copertura di geometrie complesse.
In sintesi, la scelta tra l'evaporazione a fascio elettronico e lo sputtering ionico dipende dai requisiti specifici del progetto, come la velocità di deposizione, la qualità del film, la complessità del substrato e la scalabilità.Ciascun metodo presenta vantaggi e limiti unici, che li rendono adatti a diverse applicazioni nella deposizione di film sottili.
Tabella riassuntiva:
Aspetto | Evaporazione a fascio di elettroni | Sputtering a ioni |
---|---|---|
Meccanismo | Il fascio di elettroni focalizzato riscalda e vaporizza i materiali. | Gli ioni energetici bombardano il materiale bersaglio per espellere gli atomi. |
Ambiente operativo | È richiesto il vuoto spinto. | Vuoto più basso, spesso con un campo magnetico. |
Velocità di deposizione | Velocità di deposizione più elevata. | Tasso di deposizione più basso, migliore controllo delle proprietà del film. |
Adesione e qualità del film | Minore adesione, minore omogeneità. | Migliore adesione, maggiore omogeneità, granulometria ridotta. |
Temperatura di esercizio | Sono necessarie temperature elevate, meno adatte a substrati sensibili. | Temperature più basse, ideali per materiali sensibili e substrati complessi. |
Scalabilità | Meno scalabile, più difficile da automatizzare. | Più scalabile, più facile da automatizzare per la produzione su larga scala. |
Applicazioni | Pannelli solari, rivestimenti di vetro, film ottici. | Produzione elettrica/ottica, film di elevata purezza, substrati complessi. |
Energia degli atomi depositati | Specie di vapore a bassa energia, film meno densi. | Atomi a più alta energia, film più densi e aderenti. |
Assorbimento di gas | Meno inclini all'assorbimento di gas. | Maggiore probabilità di assorbire gas, consentendo lo sputtering reattivo. |
Direzionalità | Flusso di vapore disperso, meno direzionale. | Più direzionale, migliore copertura su geometrie complesse. |
Avete bisogno di aiuto per scegliere la tecnica PVD giusta per il vostro progetto? Contattate i nostri esperti oggi stesso per una guida personalizzata!