Il rivestimento PVD (Physical Vapor Deposition) è un processo sofisticato utilizzato per depositare film sottili di materiale su un substrato, migliorandone le proprietà come la resistenza all'usura, la durezza e l'aspetto estetico.Il processo prevede il riscaldamento di un materiale target fino alla sua vaporizzazione, quindi il deposito del vapore sulla superficie del substrato.I materiali più comuni utilizzati nei rivestimenti PVD includono metalli come il titanio, il cromo, il tungsteno e l'alluminio, spesso combinati con gas reattivi come l'azoto o gli idrocarburi per formare rivestimenti come i nitruri e i carbonitruri.Il processo PVD è versatile, in grado di incorporare un'ampia gamma di materiali inorganici e alcuni organici, rendendolo adatto a varie applicazioni, dai rivestimenti decorativi durevoli ai componenti aerospaziali ad alte prestazioni.
Punti chiave spiegati:
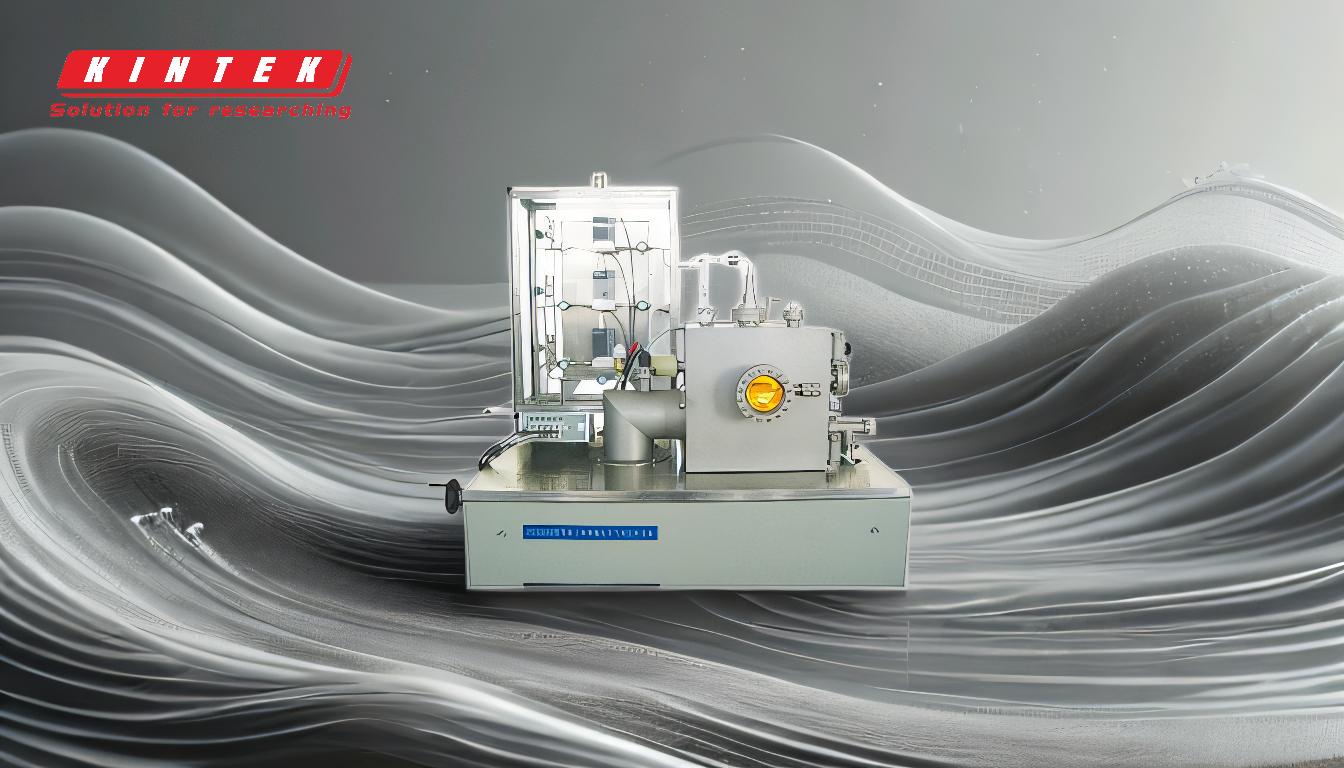
-
Materiali di destinazione nel rivestimento PVD:
- Metalli e leghe:I metalli più comuni utilizzati nei rivestimenti PVD includono titanio, cromo, tungsteno e alluminio.Questi metalli sono scelti per le loro proprietà specifiche, come la durezza, la resistenza all'usura e la capacità di formare forti legami con i gas reattivi.
- Ceramica e composti:La PVD può anche depositare ceramiche e composti come carburi, nitruri, siliciuri e boruri.Questi materiali sono spesso utilizzati in applicazioni specializzate che richiedono prestazioni elevate, come i componenti aerospaziali e automobilistici.
- Elementi della tavola periodica:Il processo può utilizzare un'ampia gamma di elementi della tavola periodica, consentendo di creare rivestimenti unici su misura per esigenze specifiche.
-
Gas reattivi:
- Azoto:Spesso utilizzato per formare rivestimenti di nitruro, noti per la loro durezza e resistenza all'usura.Ad esempio, il nitruro di titanio (TiN) è un rivestimento PVD comunemente utilizzato negli utensili da taglio.
- Gas a base di idrocarburi:Questi gas sono utilizzati per creare rivestimenti di carbonitruro, che combinano le proprietà dei carburi e dei nitruri.Sono particolarmente utili nelle applicazioni che richiedono durezza e basso attrito.
-
Materiali del substrato:
- Materiali di base:Il substrato, o materiale di base, può essere costituito da vari materiali, tra cui metalli, plastiche e ceramiche.La scelta del substrato dipende dall'applicazione prevista e dalle proprietà desiderate del prodotto finale.
- Preparazione della superficie:Prima del processo PVD, il substrato viene spesso sottoposto a una preparazione della superficie, come la pulizia e la lucidatura, per garantire una corretta adesione del rivestimento.
-
Processo di rivestimento PVD:
- Vaporizzazione:Il materiale di destinazione viene riscaldato fino alla vaporizzazione.Ciò può essere ottenuto con metodi come lo sputtering o l'evaporazione.
- Deposizione:Il materiale vaporizzato viene quindi depositato sulla superficie del substrato, formando un film sottile.Lo spessore del film può variare da pochi nanometri a qualche micrometro.
- Uniformità:Il processo PVD è noto per la produzione di rivestimenti uniformi, essenziali per garantire prestazioni e aspetto costanti.
-
Applicazioni dei rivestimenti PVD:
- Rivestimenti durevoli-decorativi:Utilizzati in prodotti in cui sono importanti sia la durata che l'aspetto estetico, come orologi, gioielli ed elettronica di consumo.
- Rivestimenti ad alte prestazioni:Si applica a componenti che richiedono proprietà meccaniche superiori, come utensili da taglio, stampi e parti di motori.
- Rivestimenti di carbonio simile al diamante (DLC):Questi rivestimenti offrono un'elevata durezza e un basso attrito, che li rendono ideali per le applicazioni nei settori automobilistico e aerospaziale.
- Alternative al cromo PVD:Utilizzato come alternativa ecologica alla cromatura tradizionale, offre proprietà estetiche e protettive simili.
-
Vantaggi del rivestimento PVD:
- Proprietà migliorate:I rivestimenti PVD migliorano la resistenza all'usura, la durezza e la resistenza alla corrosione del substrato.
- Estetica:Il processo può produrre rivestimenti con una varietà di colori e finiture, migliorando il fascino visivo del prodotto.
- Impatto ambientale:Il PVD è considerato un processo rispettoso dell'ambiente, grazie agli scarti minimi e al minor consumo di energia rispetto ai metodi di rivestimento tradizionali.
La comprensione di questi componenti e processi chiave consente di apprezzare la versatilità e l'efficacia dei rivestimenti PVD in varie applicazioni industriali.
Tabella riassuntiva:
Componente | Descrizione |
---|---|
Materiali di destinazione | Metalli (es. titanio, cromo), ceramica ed elementi della tavola periodica. |
Gas reattivi | Azoto, idrocarburi (ad esempio, per i rivestimenti di nitruro e carbonitruro). |
Materiali del substrato | Metalli, plastiche, ceramiche; richiede la preparazione della superficie per l'adesione. |
Processo | Metodi di vaporizzazione e deposizione (ad esempio, sputtering, evaporazione). |
Applicazioni | Rivestimenti decorativi durevoli, rivestimenti ad alte prestazioni, DLC, alternative al cromo PVD. |
Vantaggi | Maggiore resistenza all'usura, durezza, resistenza alla corrosione ed estetica. |
Sfruttate il potenziale dei rivestimenti PVD per le vostre applicazioni... contattate i nostri esperti oggi stesso !