La PVD, o Physical Vapor Deposition, è una tecnica di deposizione di materiali utilizzata per creare film sottili e rivestimenti su varie superfici.Implica l'uso di metalli e altri materiali per formare rivestimenti altamente durevoli, resistenti all'usura e alla corrosione.I rivestimenti PVD sono noti per la loro capacità di migliorare le proprietà dei substrati, come il miglioramento della durezza, la riduzione dell'attrito e l'aumento della resistenza all'ossidazione e alle alte temperature.Il processo viene eseguito a temperature più basse rispetto ad altri metodi come la CVD (Chemical Vapor Deposition), rendendolo adatto a un'ampia gamma di applicazioni, tra cui il settore aerospaziale, i rivestimenti decorativi e il trattamento del vetro.
Punti chiave spiegati:
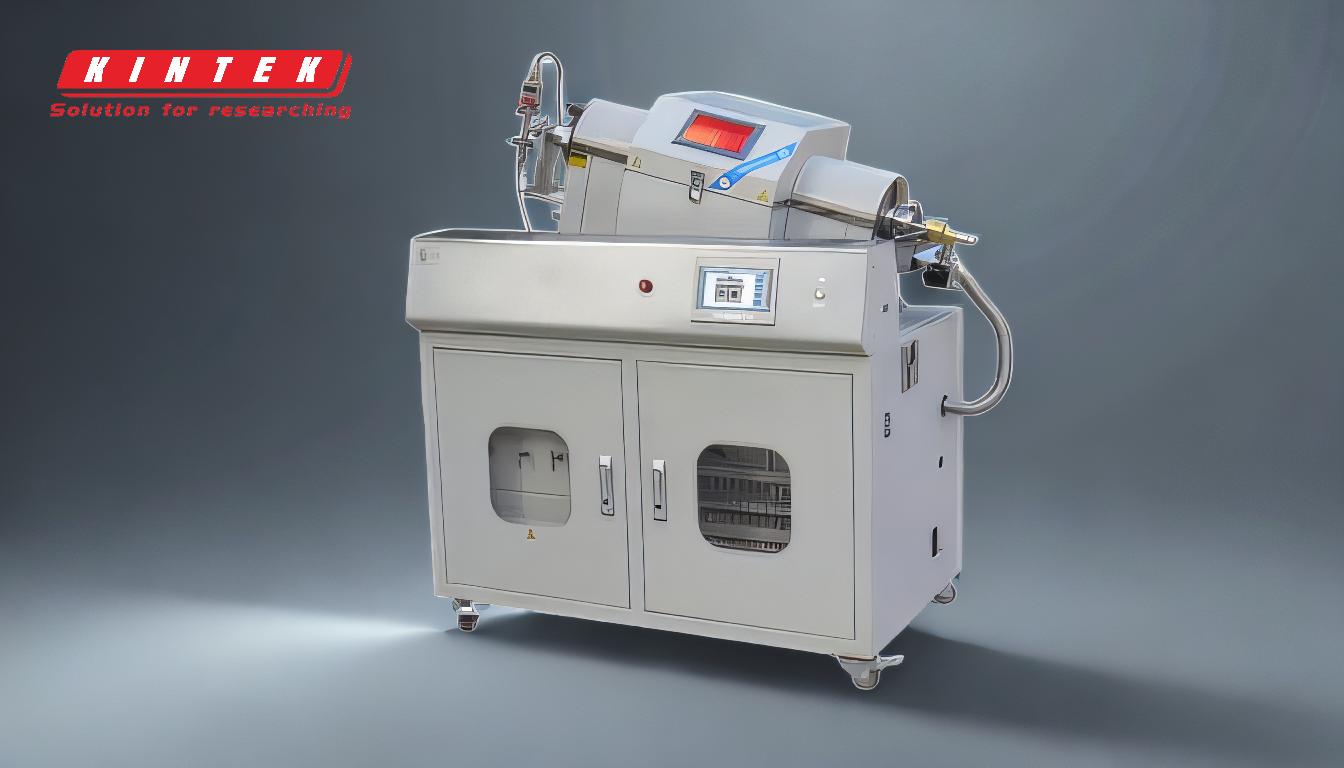
-
Definizione di PVD:
- PVD è l'acronimo di Physical Vapor Deposition (deposizione fisica da vapore), una tecnica utilizzata per depositare film sottili e rivestimenti su superfici.
- Comporta il trasferimento fisico di materiale da una sorgente a un substrato, in genere in un ambiente sotto vuoto.
-
Materiali utilizzati in PVD:
- I materiali PVD includono principalmente metalli come il titanio, il cromo, l'alluminio e i loro composti (ad esempio, nitruro di titanio (TiN), nitruro di cromo (CrN)).
- Questi materiali sono scelti per la loro capacità di formare rivestimenti duri, durevoli e resistenti alla corrosione.
-
Proprietà dei rivestimenti PVD:
- Resistenza all'usura:I rivestimenti PVD sono altamente resistenti all'usura e sono quindi ideali per le applicazioni in cui la durata è fondamentale.
- Sforzo di compressione:I film PVD presentano spesso sollecitazioni di compressione più elevate rispetto ai film CVD, il che contribuisce alla loro durata.
- Spessore:I rivestimenti PVD sono molto sottili, in genere da 0,5 a 5 micron, ma forniscono una protezione e un miglioramento significativi al substrato.
- Durezza:La durezza dei rivestimenti PVD è un fattore chiave nella loro capacità di migliorare il limite di fatica e la resistenza dei substrati.Ad esempio, i rivestimenti TiN possono aumentare il limite di fatica della lega Ti-6Al-4V del 22%.
-
Vantaggi del PVD:
- Deposizione a bassa temperatura:La PVD può essere eseguita a temperature inferiori rispetto alla CVD, rendendola adatta a materiali sensibili alla temperatura.
- Migliore resistenza all'ossidazione:I rivestimenti PVD migliorano la resistenza all'ossidazione dei substrati, rendendoli adatti ad applicazioni ad alta temperatura.
- Riduzione dell'attrito:I rivestimenti PVD riducono l'attrito, a tutto vantaggio delle applicazioni meccaniche e industriali.
- Resistenza alla corrosione:I rivestimenti PVD sono altamente resistenti alla corrosione e sono quindi ideali per l'uso in ambienti difficili.
-
Applicazioni del PVD:
- Aerospaziale:Il PVD è utilizzato nella tecnologia aerospaziale per migliorare la resistenza dei componenti alle alte temperature e all'ablazione.
- Rivestimenti decorativi:Il PVD è particolarmente indicato per le applicazioni decorative, come i rivestimenti di orologi, gioielli ed elementi architettonici.
- Rivestimenti del vetro:Il PVD viene utilizzato per applicare rivestimenti sottili e durevoli al vetro, migliorandone le proprietà e l'aspetto.
- Strati di barriera di diffusione:I rivestimenti PVD sono utilizzati come barriere di diffusione nei componenti elettronici per impedire la migrazione dei materiali.
-
Confronto con CVD:
- I rivestimenti PVD sono generalmente più resistenti all'usura e presentano una maggiore tensione di compressione rispetto ai rivestimenti CVD.
- Il PVD può essere depositato a temperature più basse, il che è vantaggioso per i substrati che non possono sopportare temperature elevate.
-
Riproduzione della finitura originale:
- I rivestimenti PVD possono replicare la finitura originale dei materiali con uno sforzo minimo, il che li rende ideali per le applicazioni in cui l'estetica è importante.
In sintesi, la PVD è una tecnica versatile ed efficace per depositare rivestimenti sottili, durevoli e ad alte prestazioni su vari substrati.La sua capacità di migliorare proprietà come la durezza, la resistenza all'usura e alla corrosione la rende un processo prezioso in settori che vanno dall'aerospaziale alle applicazioni decorative.
Tabella riassuntiva:
Aspetto | Dettagli |
---|---|
Definizione | La deposizione fisica da vapore (PVD) deposita film sottili in un ambiente sotto vuoto. |
Materiali | Titanio, cromo, alluminio e loro composti (ad esempio, TiN, CrN). |
Proprietà | Resistenza all'usura, alla compressione, rivestimenti sottili (0,5-5 µm), elevata durezza. |
Vantaggi | Deposizione a bassa temperatura, resistenza all'ossidazione, riduzione dell'attrito. |
Applicazioni | Aerospaziale, rivestimenti decorativi, trattamenti del vetro, barriere di diffusione. |
Confronto con la CVD | Maggiore resistenza all'usura, maggiore sollecitazione di compressione, temperatura di deposizione più bassa. |
Siete pronti a scoprire come il PVD può migliorare i vostri materiali? Contattateci oggi stesso per una consulenza esperta!