Il processo di colorazione PVD (Physical Vapor Deposition) è una tecnologia di rivestimento sotto vuoto utilizzata per applicare strati colorati sottili, durevoli e vivaci su substrati.Questo processo prevede la trasformazione di un materiale solido in uno stato di vapore, che poi si condensa su un substrato per formare una pellicola sottile.Il colore si ottiene introducendo gas reattivi durante il processo, che reagiscono chimicamente con il materiale vaporizzato per creare composti con proprietà ottiche specifiche.I rivestimenti PVD sono noti per la loro durata, la resistenza all'usura e la capacità di produrre un'ampia gamma di colori, che li rende popolari in settori come quello automobilistico, della gioielleria e dell'elettronica di consumo.Il processo viene eseguito in condizioni di alto vuoto, garantendo rivestimenti uniformi e di alta qualità.
Punti chiave spiegati:
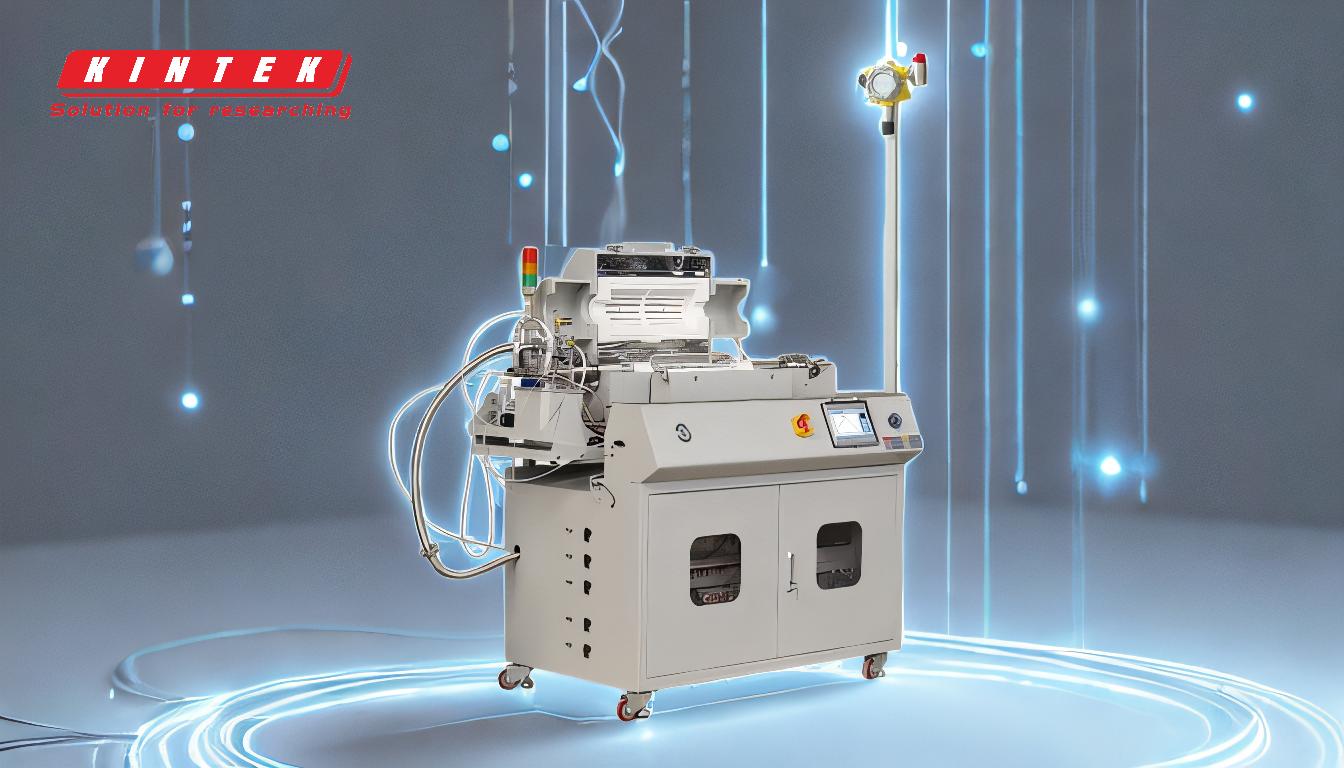
-
Panoramica del processo PVD:
- Il PVD è un processo di rivestimento sotto vuoto in cui un materiale solido viene vaporizzato e poi depositato su un substrato per formare un film sottile.
- Il processo viene eseguito in condizioni di alto vuoto, garantendo un ambiente pulito e controllato per la deposizione.
- Il PVD è ampiamente utilizzato per rivestimenti decorativi e funzionali grazie alla sua capacità di produrre finiture durevoli, resistenti all'usura ed esteticamente gradevoli.
-
Fasi del processo di colorazione PVD:
- Vaporizzazione:Il materiale solido (target) viene vaporizzato con metodi quali lo sputtering, l'evaporazione o l'ablazione laser.Questa fase prevede la conversione del solido in uno stato di vapore, spesso eccitando il materiale con plasma o sorgenti ad alta energia.
- Introduzione di gas reattivi:Un gas reattivo (ad esempio, azoto, ossigeno o acetilene) viene introdotto nella camera.Questo gas reagisce chimicamente con il materiale vaporizzato per formare composti con proprietà ottiche specifiche, che determinano il colore del rivestimento.
- Trasporto:Il materiale vaporizzato e il gas reattivo vengono trasportati attraverso la camera a vuoto fino al substrato.Questa fase assicura una distribuzione uniforme della miscela di vapore e gas.
- Deposizione:Il materiale vaporizzato e il gas reattivo si condensano sul substrato, formando una sottile pellicola colorata.Il processo di deposizione avviene a temperature relativamente basse, il che lo rende adatto a un'ampia gamma di materiali, tra cui plastiche e metalli.
-
Formazione del colore in PVD:
- Il colore del rivestimento PVD è determinato dalla composizione chimica del materiale depositato e dal gas reattivo utilizzato.
- Ad esempio, il nitruro di titanio (TiN) produce un rivestimento color oro, mentre il nitruro di titanio e alluminio (TiAlN) può produrre una gamma di colori, tra cui blu, viola e bronzo.
- Anche lo spessore del rivestimento e l'angolo di deposizione possono influenzare il colore finale, consentendo di ottenere un'ampia gamma di tonalità ed effetti.
-
Vantaggi dei rivestimenti PVD:
- Durata:I rivestimenti PVD sono altamente resistenti all'usura, alla corrosione e ai graffi e sono quindi ideali per le applicazioni che richiedono finiture di lunga durata.
- Estetica:Il processo può produrre un'ampia gamma di colori e finiture, da quelle metalliche a quelle opache, migliorando il fascino visivo dei prodotti.
- Rispetto dell'ambiente:Il PVD è un processo pulito che produce scarti minimi e non comporta l'uso di sostanze chimiche nocive, il che lo rende rispettoso dell'ambiente.
- Versatilità:Il PVD può essere applicato a una varietà di substrati, tra cui metalli, plastiche e ceramiche, rendendolo adatto a diversi settori.
-
Applicazioni dei rivestimenti colorati PVD:
- Industria automobilistica:I rivestimenti PVD sono utilizzati per decorazioni, emblemi e componenti funzionali come fasce elastiche e parti di motore.
- Gioielli:Il processo viene utilizzato per creare rivestimenti durevoli e resistenti ai graffi su orologi, anelli e altri accessori.
- Elettronica di consumo:I rivestimenti PVD vengono applicati a smartphone, laptop e altri dispositivi per migliorarne l'aspetto e la durata.
- Applicazioni architettoniche:Il PVD viene utilizzato per rivestire maniglie di porte, rubinetterie e altri dispositivi per fornire vantaggi sia estetici che funzionali.
-
Confronto con altri processi di rivestimento:
- CVD (Deposizione chimica da vapore):A differenza della PVD, la CVD comporta reazioni chimiche sulla superficie del substrato e spesso richiede temperature più elevate.Il PVD è preferito per le applicazioni che richiedono temperature più basse e un controllo più preciso delle proprietà del rivestimento.
- Elettrodeposizione:I rivestimenti PVD sono generalmente più durevoli e rispettosi dell'ambiente rispetto alla galvanoplastica, che spesso comporta l'uso di sostanze chimiche tossiche e produce più rifiuti.
-
Sfide e considerazioni:
- Costo:Il processo PVD può essere più costoso dei metodi di rivestimento tradizionali a causa della necessità di attrezzature specializzate e di condizioni di alto vuoto.
- Complessità:Per ottenere colori e finiture uniformi è necessario un controllo preciso dei parametri di processo, come il flusso di gas, la pressione e la temperatura.
- Compatibilità del substrato:Sebbene il PVD possa essere applicato a un'ampia gamma di materiali, alcuni substrati possono richiedere un pretrattamento per garantire una corretta adesione del rivestimento.
Conoscendo il processo di colorazione PVD, gli acquirenti possono prendere decisioni informate sulla sua idoneità per le loro applicazioni specifiche, bilanciando fattori quali il costo, la durata e i requisiti estetici.
Tabella riassuntiva:
Aspetto | Dettagli |
---|---|
Panoramica del processo | Tecnologia di rivestimento sottovuoto per strati sottili, durevoli e dai colori vivaci. |
Fasi principali | Vaporizzazione, introduzione di gas reattivi, trasporto e deposizione. |
Formazione del colore | Determinata dalla composizione chimica, dal gas reattivo e dall'angolo di deposizione. |
Vantaggi | Durata, estetica, rispetto dell'ambiente e versatilità. |
Applicazioni | Automotive, gioielleria, elettronica di consumo e architettura. |
Confronto con la CVD | La PVD è preferita per le temperature più basse e il controllo preciso. |
Sfide | Costi più elevati, complessità del processo e considerazioni sulla compatibilità dei substrati. |
Siete pronti a migliorare i vostri prodotti con rivestimenti PVD durevoli e vivaci? Contattateci oggi stesso per saperne di più!