La deposizione per evaporazione è una tecnica chiave nella fabbricazione di film sottili, in cui un materiale viene vaporizzato e poi depositato su un substrato per formare uno strato sottile e uniforme.Il processo prevede il riscaldamento del materiale target fino alla sua transizione allo stato gassoso, seguito dal trasporto di questi atomi o molecole vaporizzati sul substrato, dove si condensano e formano un film solido.Questo metodo è ampiamente utilizzato in settori quali la produzione di semiconduttori, la produzione di pannelli solari e le tecnologie di visualizzazione.Il processo può essere realizzato con diversi metodi, tra cui l'evaporazione termica, l'evaporazione a fascio di elettroni e lo sputtering, ciascuno con i propri vantaggi e applicazioni.
Punti chiave spiegati:
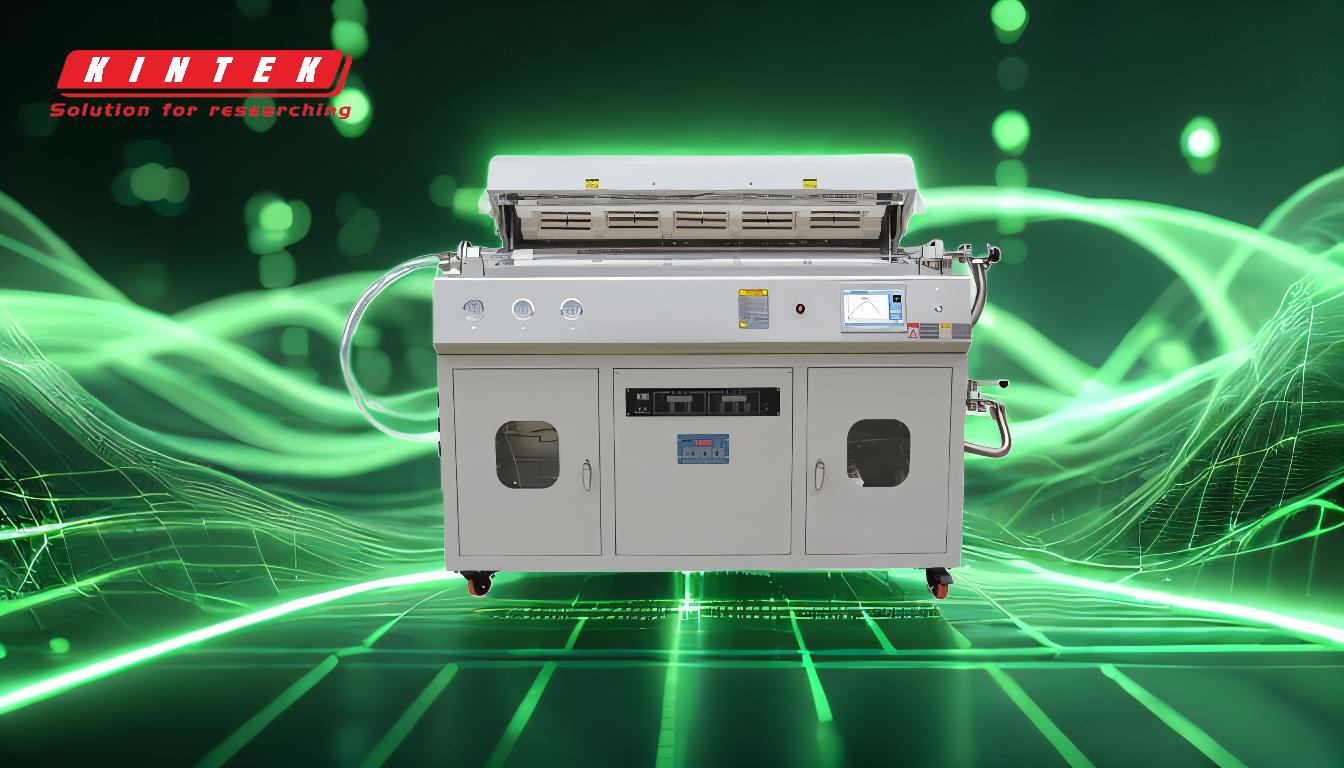
-
Processo di evaporazione:
- Il materiale da depositare viene riscaldato fino a raggiungere il suo punto di vaporizzazione.Ciò può avvenire utilizzando l'energia termica di un elemento riscaldante in tungsteno o di un fascio di elettroni.Gli atomi o le molecole acquistano energia sufficiente per superare le forze di legame nella fase solida o liquida e passare alla fase gassosa.
- Il materiale vaporizzato viene quindi trasportato al substrato attraverso un ambiente sotto vuoto.
-
Trasporto:
- Gli atomi o le molecole vaporizzate viaggiano attraverso un vuoto ad alta pressione fino al substrato.Questo ambiente sottovuoto è fondamentale perché impedisce la contaminazione e garantisce che il materiale vaporizzato raggiunga il substrato senza reagire con altri gas.
-
Deposizione:
- Quando raggiunge il substrato, il materiale vaporizzato si condensa e forma un film sottile e uniforme.La qualità del film dipende da fattori quali la temperatura del substrato, la velocità di deposizione e le condizioni di vuoto.
-
Metodi di deposizione per evaporazione:
- Evaporazione termica:Utilizza un elemento riscaldante in tungsteno per vaporizzare il materiale di destinazione.Questo metodo è adatto per depositare metalli puri, non metalli, ossidi e nitruri.
- Evaporazione a fascio di elettroni (E-beam):Utilizza un fascio di elettroni ad alta energia per far evaporare il materiale.Questo metodo è particolarmente utile per i materiali con elevati punti di fusione ed è comunemente utilizzato nella produzione di pannelli solari e vetro.
- Deposizione per sputtering:Si tratta di bombardare il materiale bersaglio con ioni ad alta energia di gas argon per dislocare gli atomi, che poi si depositano sul substrato.Questo metodo è efficace per creare film uniformi e di alta qualità.
-
Applicazioni:
- Pannelli solari:Utilizzato per depositare strati metallici conduttivi che migliorano l'efficienza delle celle solari.
- Display OLED:Essenziale per creare gli strati sottili e conduttivi necessari per la tecnologia OLED.
- Transistor a film sottile:Utilizzato nella fabbricazione dei transistor utilizzati nei dispositivi elettronici.
-
Vantaggi:
- Alta purezza:L'ambiente sotto vuoto garantisce che il film depositato sia privo di contaminanti.
- Uniformità:Il processo consente la deposizione di strati molto sottili e uniformi, un aspetto critico per molte applicazioni.
- Versatilità:Può essere utilizzato con un'ampia gamma di materiali, tra cui metalli, ossidi e nitruri.
-
Sfide:
- Requisiti per il vuoto spinto:Il mantenimento di un alto vuoto può essere tecnicamente impegnativo e costoso.
- Limitazioni dei materiali:Alcuni materiali possono non essere adatti alla deposizione per evaporazione a causa del loro elevato punto di fusione o di altre proprietà.
- Complessità:Il processo richiede un controllo preciso di parametri quali temperatura, pressione e velocità di deposizione.
In sintesi, la deposizione per evaporazione è una tecnica versatile e ampiamente utilizzata per la creazione di film sottili in varie applicazioni industriali.Comprendendo le fasi e i metodi principali coinvolti, si può apprezzare la complessità e la precisione necessarie per ottenere risultati di alta qualità.
Tabella riassuntiva:
Aspetto | Dettagli |
---|---|
Processo | Il materiale viene vaporizzato e depositato su un substrato per formare un film sottile. |
Fasi principali | 1.Evaporazione 2.Trasporto 3.Deposizione |
Metodi | Evaporazione termica, evaporazione a fascio di elettroni, sputtering |
Applicazioni | Pannelli solari, display OLED, transistor a film sottile |
Vantaggi | Elevata purezza, uniformità, versatilità |
Sfide | Requisiti di vuoto elevato, limitazioni dei materiali, complessità del processo |
Scoprite come la deposizione per evaporazione può migliorare il vostro processo di produzione... contattate i nostri esperti oggi stesso !