Il rivestimento PVD (Physical Vapor Deposition) è un processo sofisticato utilizzato per applicare strati sottili, durevoli e funzionali sulle superfici di vari materiali.Il processo prevede la vaporizzazione di un materiale solido in un ambiente sotto vuoto e il successivo deposito degli atomi vaporizzati sul substrato.Il risultato è uno strato sottile e incollato che migliora l'aspetto, la durata e la funzionalità del substrato.Il processo di rivestimento PVD è altamente controllato e prevede precise condizioni di temperatura e pressione ed è ampiamente utilizzato nei settori che richiedono rivestimenti ad alte prestazioni, come quello aerospaziale, automobilistico e dei dispositivi medici.
Punti chiave spiegati:
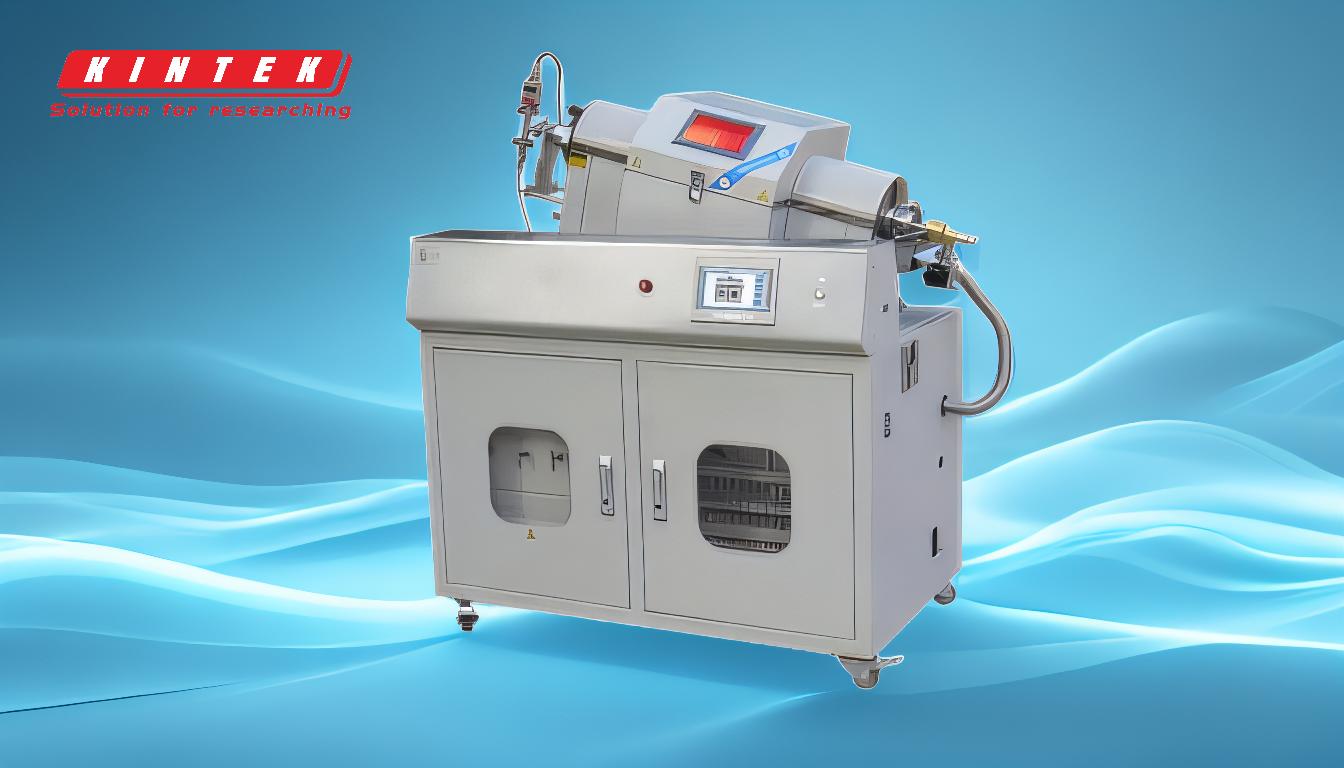
-
Principio di base del rivestimento PVD:
- Vaporizzazione del materiale solido: Il principio fondamentale del rivestimento PVD prevede la vaporizzazione di un materiale solido (spesso metalli come titanio, zirconio o cromo) in un ambiente sotto vuoto.Ciò si ottiene con vari metodi, come lo sputtering, l'evaporazione a fascio di elettroni o la scarica ad arco catodico.
- Deposizione sul substrato: Gli atomi vaporizzati attraversano il vuoto e si depositano sulla superficie del substrato.Questa deposizione avviene atomo per atomo, formando uno strato sottile e uniforme che si lega fortemente al substrato.
-
Ambiente di vuoto:
- Condizioni di alto vuoto: Il processo si svolge in una camera a vuoto, dove la pressione viene notevolmente ridotta per creare un ambiente ad alto vuoto.In questo modo si garantisce che il materiale vaporizzato rimanga pulito e non contaminato, ottenendo un rivestimento di alta qualità.
- Atmosfera controllata: L'ambiente sottovuoto consente anche l'introduzione di gas reattivi (ad esempio, azoto) per modificare la composizione del rivestimento.Ad esempio, l'aggiunta di azoto può portare alla formazione di nitruri metallici, che migliorano le proprietà del rivestimento.
-
Metodi di vaporizzazione:
- Sputtering: In questo metodo, ioni ad alta energia bombardano il materiale bersaglio, provocando l'espulsione di atomi dalla superficie e il successivo deposito sul substrato.
- Evaporazione con fascio di elettroni: Un fascio di elettroni viene utilizzato per riscaldare il materiale target, provocandone la vaporizzazione.Gli atomi vaporizzati si condensano sul substrato.
- Scarica ad arco catodico: Un arco elettrico viene utilizzato per vaporizzare il materiale di destinazione, producendo un plasma ad alta densità di atomi metallici ionizzati che si depositano sul substrato.
-
Fasi del processo di rivestimento PVD:
- Preparazione: Il substrato viene pulito e posizionato nella camera da vuoto.Anche il materiale target viene posizionato all'interno della camera.
- Evacuazione: La camera viene evacuata per creare un ambiente ad alto vuoto, che in genere raggiunge pressioni comprese tra 10^-3 e 10^-6 Pa.
- Vaporizzazione: Il materiale target viene vaporizzato con uno dei metodi sopra menzionati (sputtering, evaporazione a fascio di elettroni o scarica ad arco catodico).
- Trasporto: Gli atomi vaporizzati attraversano il vuoto e vengono trasportati sul substrato.
- Deposizione: Gli atomi si condensano sul substrato, formando uno strato sottile e uniforme.Il substrato può essere ruotato o spostato per garantire un rivestimento uniforme.
- Spurgo: Dopo la deposizione, la camera viene spurgata con gas inerte per rimuovere eventuali vapori residui e prepararsi al ciclo successivo.
-
Vantaggi del rivestimento PVD:
- Durata: I rivestimenti PVD sono altamente durevoli e offrono un'eccellente resistenza all'usura, alla corrosione e alle alte temperature.
- Sottili e uniformi: I rivestimenti sono estremamente sottili (in genere nell'ordine dei nanometri e dei micrometri) e uniformi, per garantire prestazioni costanti.
- Eco-compatibile: Il rivestimento PVD è considerato più ecologico rispetto ad altri metodi di rivestimento come la deposizione chimica da vapore (CVD), in quanto produce meno sottoprodotti nocivi.
- Versatilità: I rivestimenti PVD possono essere applicati a un'ampia gamma di materiali, tra cui metalli, ceramiche e polimeri, rendendoli adatti a diverse applicazioni.
-
Applicazioni del rivestimento PVD:
- Aerospaziale: I rivestimenti PVD sono utilizzati per migliorare le prestazioni e la longevità dei componenti aerospaziali, come le pale delle turbine e le parti dei motori.
- Automotive: Nell'industria automobilistica, i rivestimenti PVD vengono applicati per migliorare la resistenza all'usura e l'estetica di componenti come parti del motore, ruote e finiture.
- Dispositivi medici: I rivestimenti PVD sono utilizzati su impianti medici e strumenti chirurgici per migliorare la biocompatibilità e ridurre l'usura.
- Elettronica di consumo: I rivestimenti PVD vengono applicati a custodie per smartphone, orologi e altri dispositivi elettronici per migliorarne la durata e fornire una finitura di qualità superiore.
In sintesi, il rivestimento PVD è un processo altamente controllato e versatile che prevede la vaporizzazione di un materiale solido nel vuoto e il suo deposito su un substrato per formare uno strato sottile, resistente e funzionale.Il processo offre numerosi vantaggi, tra cui la durata, l'uniformità e il rispetto dell'ambiente, che lo rendono adatto a un'ampia gamma di applicazioni industriali.
Tabella riassuntiva:
Aspetto | Dettagli |
---|---|
Principio di base | Vaporizzazione di materiale solido nel vuoto e deposizione su un substrato. |
Ambiente sotto vuoto | Le condizioni di alto vuoto garantiscono rivestimenti puliti e non contaminati. |
Metodi di vaporizzazione | Sputtering, evaporazione a fascio di elettroni, scarica ad arco catodico. |
Fasi del processo | Preparazione, evacuazione, vaporizzazione, trasporto, deposizione, spurgo. |
Vantaggi | Durata, strati sottili e uniformi, ecocompatibilità, applicazioni versatili. |
Applicazioni | Aerospaziale, automotive, dispositivi medici, elettronica di consumo. |
Scoprite come il rivestimento PVD può migliorare i vostri prodotti... contattate i nostri esperti oggi stesso !