La scelta del miglior materiale per un mulino a sfere dipende dall'applicazione specifica, dalle proprietà del materiale e dai risultati desiderati.Le sfere in ceramica sono molto durevoli e riducono al minimo la contaminazione, rendendole ideali per le applicazioni ad alta purezza.Le sfere in acciaio, invece, sono robuste e più adatte a compiti di fresatura intensivi, soprattutto quando si tratta di materiali duri.Anche i ciottoli di selce e le sfere di acciaio inossidabile sono opzioni valide, ognuna delle quali offre vantaggi unici a seconda dei requisiti di macinazione.La comprensione delle proprietà e dei vantaggi di ciascun tipo di media è fondamentale per ottimizzare il processo di macinazione.
Punti chiave spiegati:
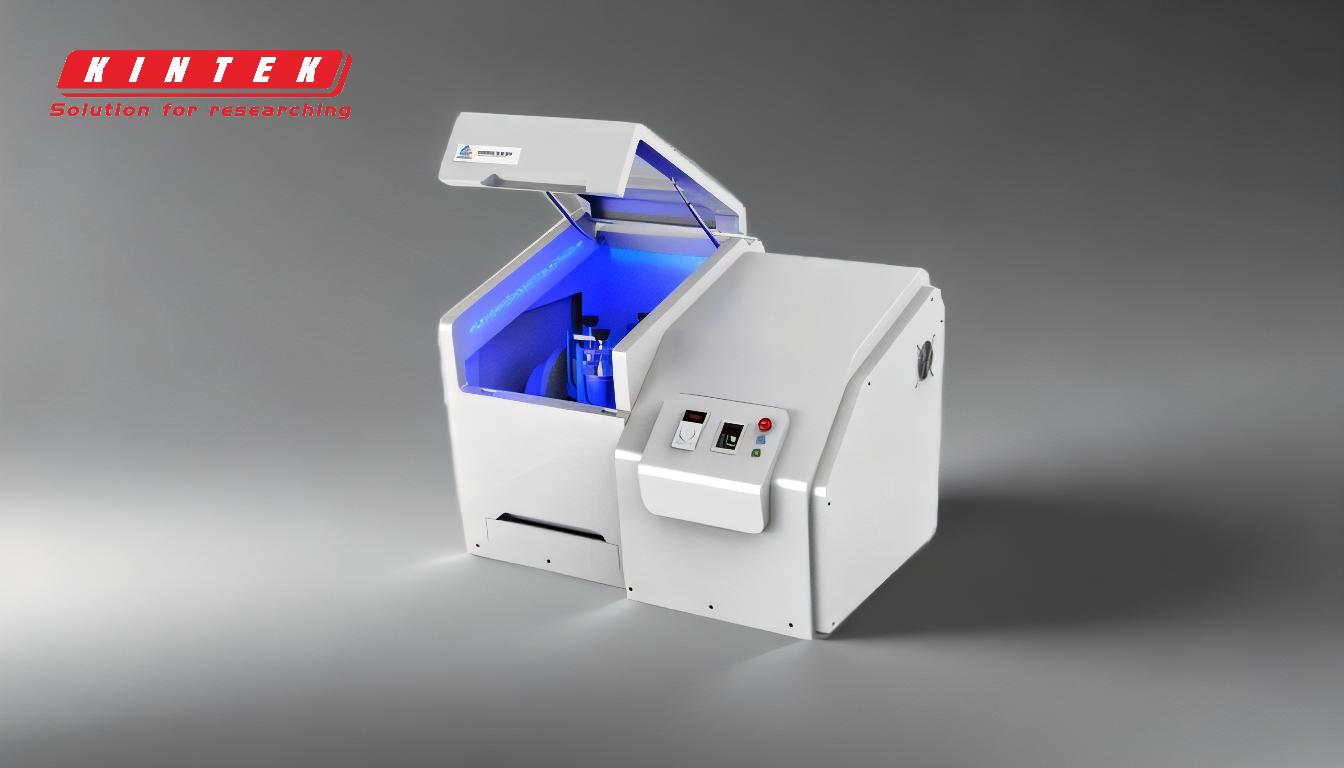
-
Sfere in ceramica
- Elevata durata:Le sfere in ceramica sono note per le loro prestazioni di lunga durata, riducendo la necessità di frequenti sostituzioni.
- Contaminazione minima:Sono ideali per le applicazioni che richiedono un'elevata purezza, in quanto non introducono impurità nel materiale da macinare.
- Applicazioni:Comunemente utilizzate in settori come quello farmaceutico, alimentare ed elettronico, dove è necessario evitare la contaminazione.
-
Sfere in acciaio
- Robustezza:Le sfere in acciaio sono estremamente durevoli e possono sopportare lavori di fresatura pesanti.
- Durezza del materiale:Sono particolarmente efficaci per la fresatura di materiali duri grazie alla loro elevata densità e resistenza.
- Applicazioni:Adatti a settori come l'industria mineraria, la metallurgia e l'edilizia, dove la robustezza e la durata sono fondamentali.
-
Ciottoli di selce
- Materiale naturale:I ciottoli di selce sono un mezzo di macinazione naturale, spesso utilizzato per i materiali più morbidi.
- Convenienti:Sono generalmente meno costose delle sfere in ceramica o in acciaio.
- Applicazioni:Ideale per applicazioni in cui il costo è un fattore significativo e il materiale da fresare non è estremamente duro.
-
Sfere in acciaio inox
- Resistenza alla corrosione:Queste sfere sono resistenti alla ruggine e alla corrosione e sono quindi adatte ai processi di macinazione a umido.
- Versatilità:Possono essere utilizzate in una varietà di applicazioni di fresatura, comprese quelle con materiali corrosivi.
- Applicazioni:Comunemente utilizzati nei processi chimici, nelle industrie alimentari e in tutte le applicazioni in cui è necessaria la resistenza alla corrosione.
-
Fattori da considerare nella scelta dei materiali
- Durezza del materiale:La durezza del materiale da macinare deve corrispondere a quella dei mezzi di macinazione per garantire una macinazione efficace.
- Rischio di contaminazione:Per applicazioni di elevata purezza, scegliere supporti che riducano al minimo la contaminazione, come le sfere in ceramica.
- Durata e costi:Considerare l'equilibrio tra la durata dei mezzi e il costo, soprattutto per le operazioni su larga scala.
- Ambiente di macinazione:Il fatto che il processo di macinazione sia a secco o a umido può influenzare la scelta dei media, con l'acciaio inossidabile che è preferibile per gli ambienti umidi grazie alla sua resistenza alla corrosione.
Valutando attentamente questi fattori, è possibile selezionare i mezzi di macinazione più appropriati per il proprio mulino a sfere, garantendo prestazioni ed efficienza ottimali.
Tabella riassuntiva:
Tipo di supporto | Proprietà principali | Applicazioni |
---|---|---|
Sfere in ceramica | Elevata durata, contaminazione minima | Farmaceutica, industria alimentare, elettronica (applicazioni ad alta purezza) |
Sfere in acciaio | Robuste, ad alta densità, durevoli | Miniere, metallurgia, edilizia (lavori di fresatura pesanti) |
Ciottoli di selce | Naturale, conveniente | Materiali morbidi, applicazioni sensibili ai costi |
Acciaio inossidabile | Resistente alla corrosione, versatile | Lavorazione chimica, industrie alimentari, ambienti di macinazione a umido |
Avete bisogno di aiuto per selezionare il mezzo di macinazione perfetto per il vostro mulino a sfere? Contattate i nostri esperti oggi stesso per una consulenza personalizzata!