La pressatura isostatica a caldo (HIP) è un processo di produzione che migliora le proprietà dei materiali applicando temperatura e pressione elevate in modo uniforme in tutte le direzioni. Se da un lato offre vantaggi significativi, come il miglioramento delle proprietà meccaniche e la capacità di produrre componenti ad alta densità, dall'altro presenta diversi svantaggi. Tra questi, i costi elevati delle attrezzature e della produzione, le dimensioni limitate degli obiettivi a causa dei vincoli delle attrezzature, la bassa efficienza produttiva e le difficoltà nel controllo della temperatura. Inoltre, l'HIP richiede competenze specifiche per il suo funzionamento e potrebbe non essere compatibile con alcuni materiali in polvere, limitandone ulteriormente l'applicabilità.
Punti chiave spiegati:
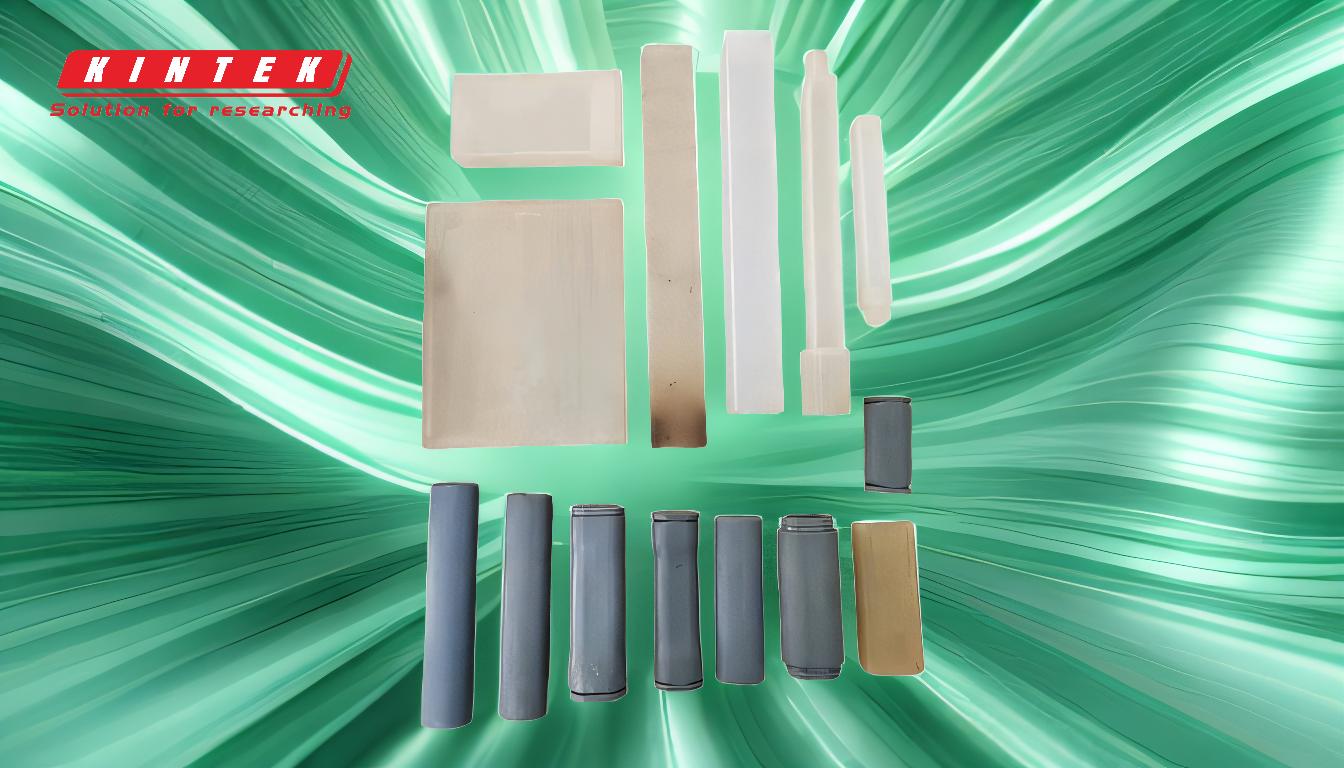
-
Elevati costi di produzione e di attrezzature:
- L'attrezzatura HIP è costosa da acquistare e mantenere e richiede un investimento iniziale significativo.
- Il processo stesso è costoso a causa della necessità di temperature e pressioni elevate, nonché di materiali specializzati come le polveri essiccate a spruzzo.
- Questi costi rendono l'HIP meno competitivo rispetto ad altri metodi di sinterizzazione, soprattutto per la produzione su larga scala.
-
Dimensioni limitate del target:
- Le dimensioni dei componenti che possono essere lavorati con l'HIP sono limitate dalla pressione e dalle dimensioni del cilindro di lavoro dell'apparecchiatura.
- Questa limitazione rende difficile la produzione di target di grandi dimensioni, limitando l'applicazione dell'HIP nei settori che richiedono componenti di grandi dimensioni.
-
Bassa efficienza produttiva:
- L'HIP ha tassi di produzione relativamente bassi rispetto a metodi come l'estrusione o la compattazione in stampo.
- Il processo richiede molto tempo, il che ne riduce ulteriormente l'efficienza e aumenta i costi di produzione.
-
Sfide nel controllo della temperatura:
- Il controllo preciso della temperatura è difficile a causa del riscaldamento del mezzo di pressione dovuto all'attrito e alla sovralimentazione.
- Anche garantire una distribuzione uniforme della temperatura all'interno del cilindro di lavoro è una sfida, che può influire sulla qualità del prodotto finale.
-
Requisiti di competenza specialistica:
- Il funzionamento delle apparecchiature HIP richiede una manodopera qualificata, che potrebbe non essere facilmente disponibile.
- La complessità del processo richiede una formazione specializzata, che aumenta il costo complessivo e ne limita l'adozione in alcune regioni.
-
Problemi di compatibilità dei materiali:
- Le polveri lavorate con l'HIP spesso non sono compatibili con i processi di fusione, in quanto richiedono temperature troppo elevate o danno luogo a microstrutture sfavorevoli.
- Questa limitazione limita la gamma di materiali che possono essere lavorati efficacemente con l'HIP.
-
Precisione della superficie e requisiti di lavorazione:
- Le superfici dei componenti pressati adiacenti al sacco flessibile in HIP hanno una precisione inferiore rispetto alla pressatura meccanica o all'estrusione.
- Ciò rende spesso necessaria una lavorazione aggiuntiva, aumentando i tempi e i costi di produzione complessivi.
-
Elevati costi e investimenti iniziali:
- I costi iniziali per la creazione di un impianto HIP sono elevati e comprendono il costo della pressa, delle attrezzature ausiliarie e dell'infrastruttura.
- Questo elevato investimento iniziale può rappresentare un ostacolo per le aziende più piccole o con budget limitati.
In sintesi, se da un lato l'HIP offre vantaggi significativi in termini di proprietà dei materiali e qualità dei componenti, dall'altro i suoi svantaggi - come i costi elevati, le dimensioni limitate, la bassa efficienza e le competenze specialistiche richieste - lo rendono meno adatto ad alcune applicazioni. Questi fattori devono essere considerati attentamente quando si valuta l'uso dell'HIP nei processi produttivi.
Tabella riassuntiva:
Svantaggi | Spiegazione |
---|---|
Elevati costi di produzione e di attrezzature | Apparecchiature costose, manutenzione elevata e materiali di processo costosi. |
Dimensioni limitate del target | Limitato dalle dimensioni delle apparecchiature, che rendono difficile la produzione di componenti di grandi dimensioni. |
Bassa efficienza produttiva | Processo che richiede tempo, con tassi di produzione più lenti rispetto ad altri metodi. |
Sfide nel controllo della temperatura | Difficoltà nel mantenere una distribuzione precisa e uniforme della temperatura. |
Requisiti di abilità specializzati | Richiede operatori qualificati e formazione specializzata, con conseguente aumento dei costi. |
Problemi di compatibilità dei materiali | Compatibilità limitata con alcuni materiali in polvere, che limita le applicazioni. |
Precisione della superficie e lavorazione | La minore precisione della superficie richiede spesso una lavorazione aggiuntiva, con conseguente aumento dei costi. |
Costi e investimenti iniziali elevati | Significativo investimento iniziale in attrezzature e infrastrutture. |
State considerando l'HIP per il vostro processo di produzione? Contattate i nostri esperti oggi stesso per discutere le vostre esigenze!