I materiali refrattari sono essenziali nelle applicazioni industriali ad alta temperatura grazie alla loro capacità di resistere al calore estremo, alla corrosione chimica e alle sollecitazioni meccaniche.Sono ampiamente utilizzati in settori come la siderurgia, la produzione di vetro e la produzione di cemento.I vantaggi dei materiali refrattari comprendono l'elevata resistenza termica, la durata e la capacità di mantenere l'integrità strutturale in condizioni difficili.Tuttavia, presentano anche degli svantaggi, come i costi elevati, la fragilità e la suscettibilità agli shock termici.La comprensione di questi pro e contro è fondamentale per selezionare il materiale refrattario giusto per applicazioni specifiche, garantendo prestazioni ottimali e un buon rapporto costi-benefici.
Punti chiave spiegati:
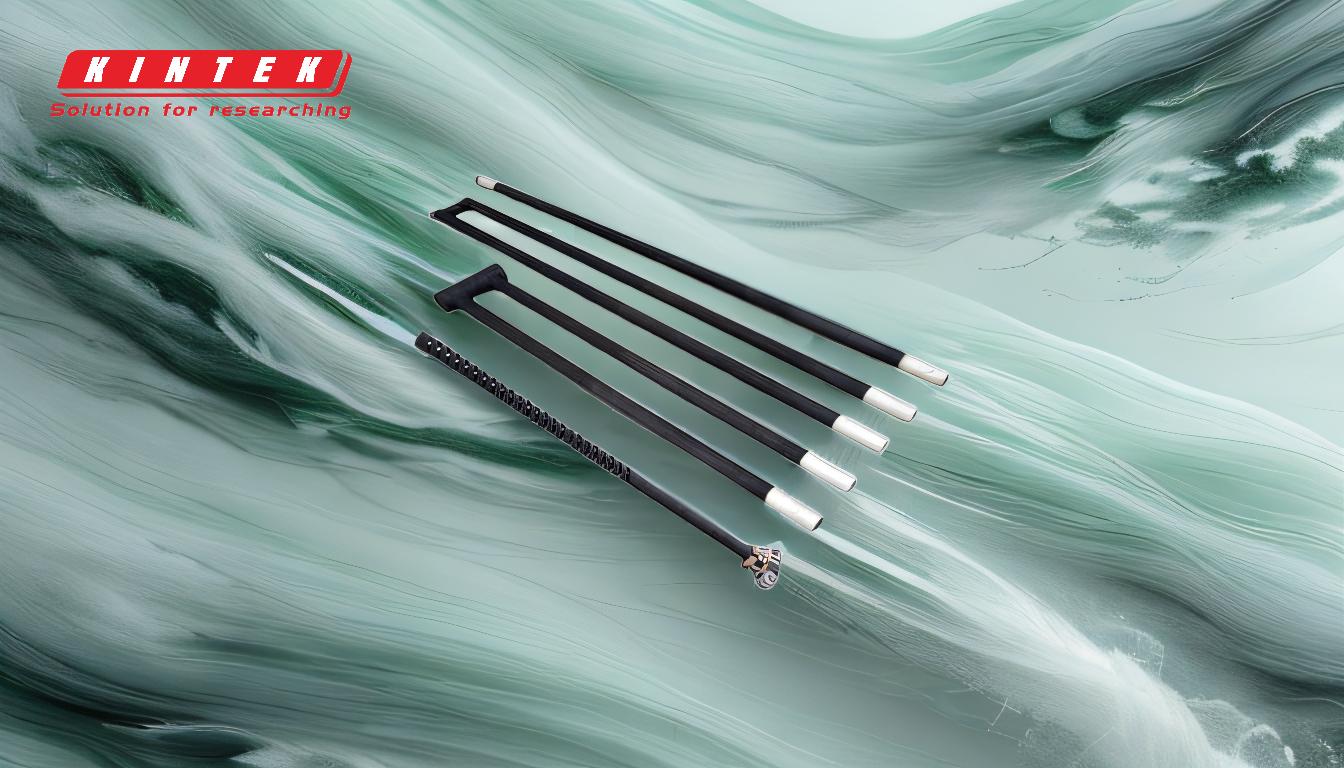
-
Vantaggi dei materiali refrattari:
- Alta resistenza termica:I materiali refrattari sono progettati per resistere a temperature estremamente elevate, spesso superiori a 1000°C, senza fondersi o degradarsi.Questo li rende ideali per applicazioni come forni, fornaci e reattori.
- Stabilità chimica:Sono resistenti alla corrosione chimica dei metalli fusi, delle scorie e dei gas, un aspetto fondamentale in settori come la siderurgia e la produzione del vetro.
- Resistenza meccanica:I refrattari sono in grado di resistere alle sollecitazioni meccaniche, come l'abrasione e l'impatto, rendendoli adatti agli ambienti industriali pesanti.
- Isolamento termico:Forniscono un eccellente isolamento, riducendo la perdita di calore e migliorando l'efficienza energetica nei processi ad alta temperatura.
- Lunga durata:Se selezionati e mantenuti correttamente, i materiali refrattari possono avere una lunga durata operativa, riducendo la necessità di frequenti sostituzioni.
-
Svantaggi dei materiali refrattari:
- Costo elevato:I materiali refrattari sono spesso costosi a causa delle materie prime specializzate e dei processi di produzione richiesti.Ciò può aumentare il costo complessivo delle operazioni industriali.
- Fragilità:Molti materiali refrattari sono fragili e inclini a fessurarsi o rompersi in presenza di sollecitazioni meccaniche o shock termici, il che può portare a guasti prematuri.
- Suscettibilità agli shock termici:Le rapide variazioni di temperatura possono causare shock termici, con conseguenti cricche e riduzione delle prestazioni.Si tratta di una limitazione significativa nei processi con temperature fluttuanti.
- Riparabilità limitata:Una volta danneggiati, i rivestimenti refrattari possono essere difficili e costosi da riparare, richiedendo spesso una sostituzione parziale o completa.
- Peso e complessità di installazione:I materiali refrattari sono spesso pesanti e la loro installazione può richiedere tempo e manodopera, con la necessità di tecnici specializzati.
-
Applicazioni e criteri di selezione:
- Acciaieria:I refrattari sono utilizzati negli altiforni, nelle siviere e nelle casseforti, dove devono resistere alle alte temperature e alla corrosione chimica dell'acciaio fuso e delle scorie.
- Produzione del vetro:Nei forni per il vetro, i refrattari devono resistere alle alte temperature e alla corrosione del vetro fuso e dei vapori alcalini.
- Produzione di cemento:I forni rotativi delle cementerie richiedono refrattari in grado di resistere al calore estremo e all'usura meccanica.
- Criteri di selezione:La scelta del materiale refrattario dipende da fattori quali la temperatura di esercizio, l'ambiente chimico, le sollecitazioni meccaniche e i cicli termici.I materiali più comuni sono l'allumina, la silice, la magnesia e la zirconia, ciascuno con proprietà specifiche adatte a diverse applicazioni.
-
Tendenze e innovazioni future:
- Materiali avanzati:Sono in corso ricerche per lo sviluppo di nuovi materiali refrattari con una migliore resistenza agli shock termici, costi inferiori e una maggiore durata.
- Riciclaggio e sostenibilità:Si stanno compiendo sforzi per riciclare i refrattari usati e sviluppare processi produttivi più sostenibili per ridurre l'impatto ambientale.
- Refrattari intelligenti:Si stanno studiando innovazioni come i sensori incorporati nei rivestimenti refrattari per monitorare la temperatura e l'usura in tempo reale, migliorando la manutenzione e le prestazioni.
In conclusione, i materiali refrattari offrono vantaggi significativi nelle applicazioni industriali ad alta temperatura, ma i loro limiti devono essere considerati con attenzione.Comprendendo le loro proprietà e selezionando il materiale giusto per condizioni specifiche, le industrie possono ottimizzare le prestazioni, ridurre i costi e prolungare la durata delle loro apparecchiature.
Tabella riassuntiva:
Aspetto | Dettagli |
---|---|
Vantaggi | Elevata resistenza termica, stabilità chimica, resistenza meccanica, isolamento, lunga durata di servizio |
Svantaggi | Costo elevato, fragilità, suscettibilità agli shock termici, riparabilità limitata, peso e complessità di installazione |
Applicazioni | Acciaieria, produzione di vetro, produzione di cemento |
Criteri di selezione | Temperatura di esercizio, ambiente chimico, stress meccanico, cicli termici |
Tendenze future | Materiali avanzati, riciclaggio e sostenibilità, refrattari intelligenti |
Avete bisogno di aiuto per scegliere il materiale refrattario giusto per la vostra applicazione? Contattate oggi stesso i nostri esperti per soluzioni su misura!