La deposizione fisica da vapore (PVD) e la deposizione chimica da vapore (CVD) sono tecnologie di rivestimento avanzate utilizzate per migliorare le proprietà superficiali dei materiali, come la durezza, la resistenza all'usura e la resistenza alla corrosione.La PVD prevede la vaporizzazione di un materiale solido nel vuoto e il suo deposito su un substrato, mentre la CVD utilizza reazioni chimiche di precursori gassosi per formare un rivestimento.Entrambi i processi hanno fasi, vantaggi e applicazioni distinte.Il PVD è più veloce e opera a temperature più basse, rendendolo adatto a una più ampia gamma di materiali, mentre il CVD produce rivestimenti più densi e uniformi, ma richiede temperature più elevate e tempi di lavorazione più lunghi.
Punti chiave spiegati:
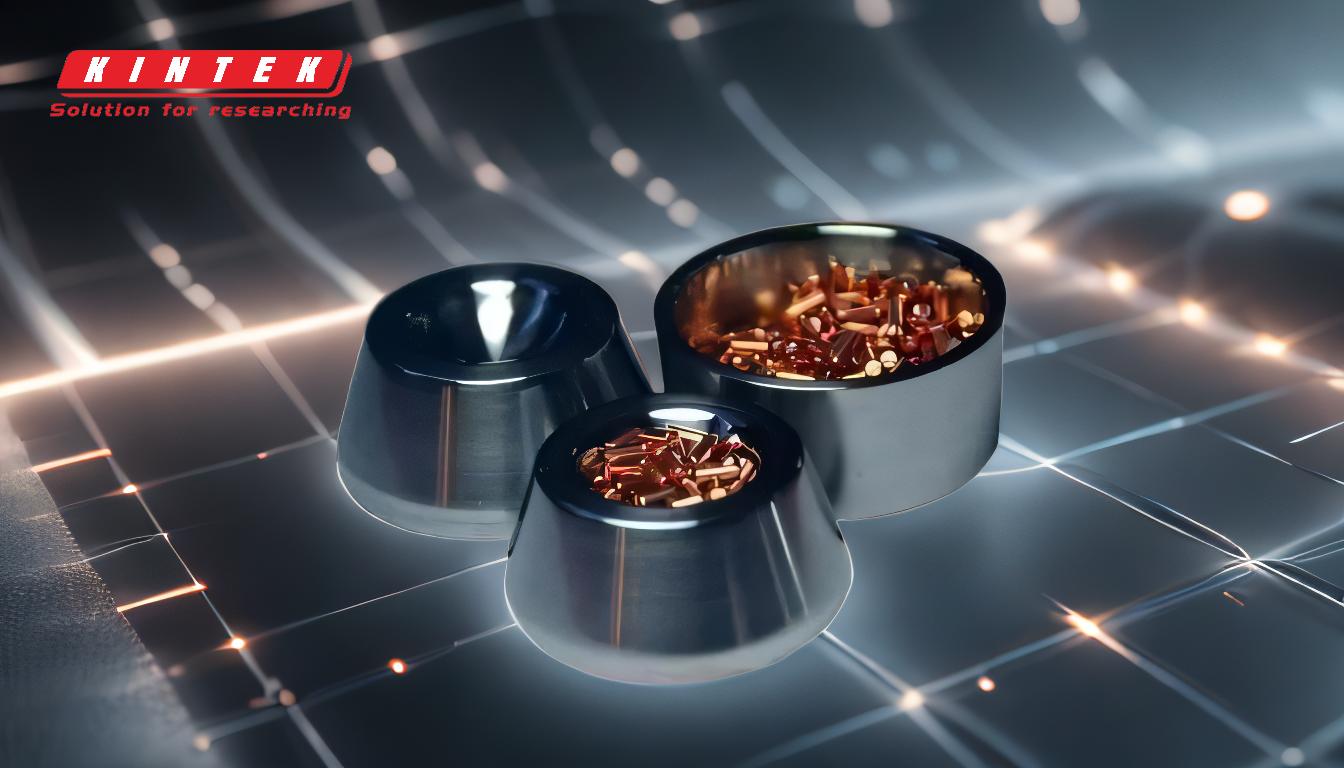
-
Panoramica dei processi di rivestimento PVD e CVD:
- PVD:Consiste nel vaporizzare un materiale solido nel vuoto e nel depositarlo su un substrato.È un processo fisico che opera a temperature inferiori (circa 500 °C) ed è adatto a metalli, leghe e ceramiche.
- CVD:Utilizza reazioni chimiche di precursori gassosi ad alte temperature (800~1000 °C) per depositare un rivestimento.È tipicamente limitato a ceramiche e polimeri e produce rivestimenti più spessi, più densi e più uniformi.
-
Fasi del processo di rivestimento PVD:
- Fase 1: pulizia del substrato:Il substrato viene pulito per rimuovere i contaminanti e garantire una migliore adesione del rivestimento.
- Fase 2: Pretrattamento:Il substrato viene sottoposto a un pretrattamento per migliorare l'adesione del rivestimento, che spesso comporta l'attivazione o l'incisione della superficie.
- Fase 3: rivestimento:Il materiale target viene vaporizzato con tecniche come il fascio di elettroni, il bombardamento ionico o l'arco catodico.Il materiale vaporizzato viene quindi trasportato sul substrato e depositato come film sottile.
- Fase 4: Controllo di qualità:Il substrato rivestito viene ispezionato per garantire che il rivestimento soddisfi gli standard specificati, quali spessore, uniformità e adesione.
- Fase 5: Finitura:Per migliorare l'aspetto o le prestazioni del rivestimento possono essere applicati ulteriori trattamenti, come la lucidatura o la ricottura.
-
Fasi del processo di rivestimento CVD:
- Fase 1: Introduzione del precursore:I precursori gassosi vengono introdotti nella camera di reazione.
- Fase 2: Reazione chimica:I precursori reagiscono ad alte temperature (800~1000 °C) per formare il materiale di rivestimento desiderato.
- Fase 3: Deposizione:I prodotti di reazione vengono depositati sul substrato, formando un rivestimento denso e uniforme.
- Fase 4: Post-trattamento:Il substrato rivestito può essere sottoposto a trattamenti aggiuntivi, come la ricottura o la finitura superficiale, per migliorarne le proprietà.
-
Differenze chiave tra PVD e CVD:
- Temperatura:La PVD opera a temperature più basse (circa 500 °C), mentre la CVD richiede temperature elevate (800~1000 °C).
- Spessore del rivestimento:La PVD produce rivestimenti più sottili (3~5μm), mentre la CVD produce rivestimenti più spessi (10~20μm).
- Densità e uniformità del rivestimento:I rivestimenti CVD sono più densi e uniformi rispetto ai rivestimenti PVD.
- Compatibilità dei materiali:Il PVD può depositare una gamma più ampia di materiali, tra cui metalli, leghe e ceramiche, mentre il CVD è tipicamente limitato a ceramiche e polimeri.
- Tempo di lavorazione:La PVD è più rapida e quindi adatta ad applicazioni che richiedono tempi rapidi, mentre la CVD richiede tempi più lunghi a causa delle reazioni chimiche coinvolte.
-
Applicazioni di PVD e CVD:
- PVD:Comunemente utilizzato in applicazioni che richiedono un'elevata resistenza all'usura, come utensili da taglio, rivestimenti decorativi e componenti aerospaziali.È anche adatto a processi di taglio interrotti come la fresatura.
- CVD:Ideale per applicazioni che richiedono rivestimenti spessi, densi e uniformi, come la produzione di semiconduttori, rivestimenti resistenti all'usura per processi di taglio continuo come la tornitura e applicazioni ad alta temperatura.
-
Vantaggi e limiti:
- Vantaggi PVD:Lavorazione più rapida, temperature di esercizio più basse e compatibilità con un'ampia gamma di materiali.
- Limitazioni del PVD:Rivestimenti meno densi e meno uniformi rispetto alla CVD.
- Vantaggi della CVD:Rivestimenti più densi e uniformi, adatti ad applicazioni ad alta temperatura.
- Limiti della CVD:Temperature di lavorazione più elevate, tempi di lavorazione più lunghi e compatibilità dei materiali limitata.
Comprendendo le fasi e le differenze dettagliate tra i processi di rivestimento PVD e CVD, gli acquirenti di apparecchiature e materiali di consumo possono prendere decisioni informate in base ai requisiti specifici delle loro applicazioni, come le proprietà di rivestimento desiderate, la compatibilità dei materiali e i vincoli di lavorazione.
Tabella riassuntiva:
Aspetto | PVD | CVD |
---|---|---|
Temperatura di esercizio | Inferiore (circa 500 °C) | Superiore (800~1000 °C) |
Spessore del rivestimento | Più sottile (3~5μm) | Più spesso (10~20μm) |
Densità del rivestimento | Meno denso | Più denso e uniforme |
Compatibilità dei materiali | Metalli, leghe, ceramica | Ceramica, polimeri |
Tempo di lavorazione | Più veloce | Più lungo |
Applicazioni | Utensili da taglio, rivestimenti decorativi, componenti aerospaziali | Produzione di semiconduttori, rivestimenti resistenti all'usura, applicazioni ad alta temperatura |
Avete bisogno di aiuto per scegliere il processo di rivestimento più adatto alla vostra applicazione? Contattate i nostri esperti oggi stesso !