La tecnica del pellet pressato per XRF (fluorescenza a raggi X) è un metodo di preparazione del campione utilizzato per creare dischi uniformi e piatti da campioni in polvere.Questa tecnica è fondamentale per un'analisi elementare accurata, in quanto garantisce una presentazione uniforme del campione allo strumento XRF.Il processo prevede la macinazione del campione in polvere fine, la miscelazione con un legante e la compressione ad alta pressione per formare un pellet solido.Questo metodo è ampiamente utilizzato in settori quali l'industria mineraria, la geologia e la metallurgia perché fornisce risultati affidabili e riproducibili per le analisi chimiche.Di seguito illustriamo gli aspetti principali di questa tecnica e la sua importanza.
Punti chiave spiegati:
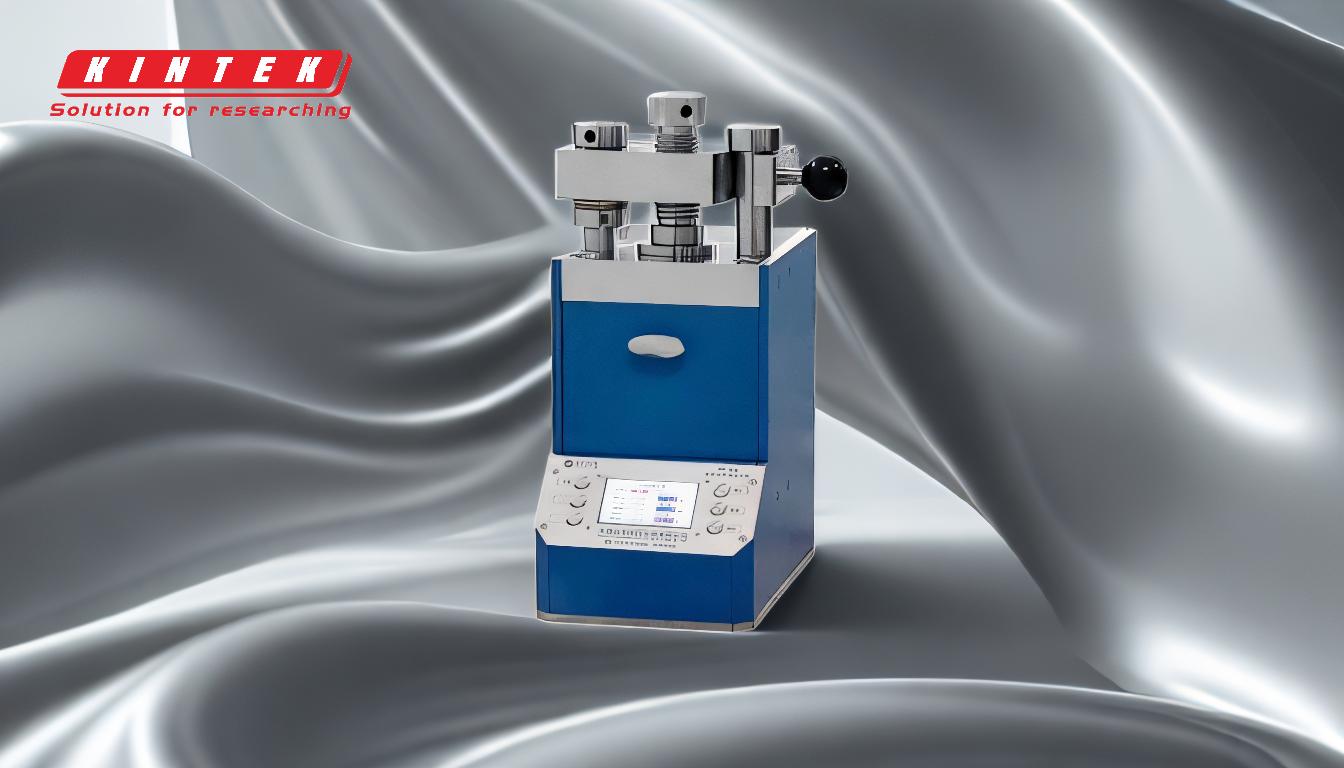
-
Scopo della tecnica del pellet pressato
- L'obiettivo principale della tecnica del pellet pressato è quello di preparare i campioni per l'analisi XRF in una forma che garantisca densità e consistenza superficiale uniformi.
- Questa uniformità è fondamentale per un'accurata identificazione e quantificazione degli elementi, poiché la XRF si basa sull'interazione dei raggi X con la superficie del campione.
- Senza un'adeguata preparazione del campione, i risultati possono essere incoerenti o imprecisi, con conseguenti potenziali errori di analisi.
-
Fasi della tecnica del pellet pressato
- Preparazione del campione:Il campione viene prima macinato in polvere fine per garantire l'omogeneità.Questa fase è fondamentale perché le particelle più grandi possono portare a risultati non uniformi.
- Miscelazione con un legante:Al campione in polvere viene spesso aggiunto un agente legante che lo aiuta a rimanere unito durante la compressione.I leganti più comuni sono le cere, la cellulosa o altri composti organici.
- Compressione:La miscela viene posta in uno stampo e sottoposta a una pressione elevata (in genere 10-40 tonnellate) mediante una pressa idraulica.In questo modo la polvere viene compressa in un disco solido e piatto.
- Pellet finale:Il pellet ottenuto è un disco uniforme e resistente che può essere analizzato direttamente con la tecnica XRF.
-
Vantaggi della tecnica dei pellet pressati
- Consistenza:La tecnica produce pellet con densità e proprietà superficiali uniformi, essenziali per un'analisi XRF affidabile.
- Versatilità:Può essere utilizzato per un'ampia gamma di tipi di campioni, tra cui minerali, metalli, ceramiche e materiali geologici.
- Costo-efficacia:Rispetto ad altri metodi di preparazione del campione, come la fusione, i pellet pressati sono relativamente economici e richiedono meno attrezzature specializzate.
- Perdita minima di campione:Il processo conserva la composizione originale del campione, garantendo una rappresentazione accurata del suo contenuto elementare.
-
Applicazioni in settori chiave
- Miniere e geologia:Utilizzato per analizzare i campioni di minerale alla ricerca di elementi preziosi e impurità.
- Metallurgia:Contribuisce al controllo della qualità identificando la composizione di metalli e leghe.
- Scienze ambientali:Utilizzato per analizzare campioni di suolo e sedimenti alla ricerca di contaminanti.
- Prodotti farmaceutici e alimenti:Garantisce la conformità agli standard di sicurezza analizzando gli elementi in traccia.
-
Sfide e considerazioni
- Dimensione delle particelle:Se il campione non viene macinato in modo sufficientemente fine, si può verificare una compressione non uniforme e risultati incoerenti.
- Selezione del legante:La scelta del legante può influenzare la durata del pellet e l'accuratezza dell'analisi.
- Controllo della pressione:L'applicazione di una pressione eccessiva o insufficiente può produrre pellet troppo fragili o non sufficientemente densi.
- Contaminazione:È necessario prestare attenzione per evitare di introdurre materiali estranei durante il processo di macinazione o pressatura.
-
Confronto con altri metodi di preparazione dei campioni
- Pellet pressati vs. fusione:La fusione prevede la fusione del campione con un flusso per creare un disco di vetro.Pur garantendo un'eccellente omogeneità, la fusione è più complessa e costosa dei pellet pressati.
- Pellet pressati vs. polvere sciolta:L'analisi della polvere sfusa è più semplice ma meno accurata a causa delle variazioni nella dimensione e nella distribuzione delle particelle.
- Pellet pressati e campioni solidi:I campioni solidi possono non richiedere una preparazione, ma spesso non hanno l'uniformità necessaria per un'analisi XRF precisa.
-
Attrezzatura necessaria
- Pressa idraulica:Utilizzato per applicare la pressione necessaria alla formazione dei pellet.
- Mulino di macinazione:Assicura che il campione sia finemente macinato prima della pressatura.
- Set di stampi:Trattiene il campione durante la compressione e lo modella in un pellet.
- Legante:Opzionale, a seconda del tipo di campione e dei requisiti di analisi.
In sintesi, la tecnica dei pellet pressati è un metodo fondamentale per preparare i campioni per l'analisi XRF.La sua capacità di produrre pellet uniformi e durevoli la rende indispensabile per le industrie che richiedono analisi elementari precise.Sebbene il processo richieda un'attenta cura dei dettagli, i suoi vantaggi in termini di coerenza, versatilità ed economicità lo rendono una scelta privilegiata per molte applicazioni.
Tabella riassuntiva:
Aspetto | Dettagli |
---|---|
Scopo | Assicura una densità e una consistenza superficiale uniformi per un'analisi XRF accurata. |
Passi | 1.Macinare il campione in polvere fine.2.Miscelare con il legante.3.Comprimere in pellet. |
Vantaggi | Consistenza, versatilità, economicità, perdita minima di campioni. |
Applicazioni | Miniere, geologia, metallurgia, scienze ambientali, farmaceutica. |
Sfide | Dimensione delle particelle, selezione del legante, controllo della pressione, contaminazione. |
Confronto | Più conveniente della fusione; più accurata dell'analisi delle polveri sfuse. |
Attrezzatura | Pressa idraulica, mulino di macinazione, set di stampi, legante. |
Scoprite come la tecnica del pellet pressato può ottimizzare le vostre analisi XRF. contattate i nostri esperti oggi stesso !