La dimensione delle particelle ottenuta in un mulino a sfere dipende da diversi fattori, tra cui la dimensione iniziale delle particelle del materiale, la dimensione e il tipo di mezzo di macinazione (sfere), il tempo di macinazione e i parametri operativi come la velocità di rotazione e il rapporto di riempimento.In genere, i mulini a sfere vengono utilizzati per ridurre le dimensioni delle particelle nell'intervallo 1-20 μm, con sfere più piccole e tempi di macinazione più lunghi per ottenere particelle più fini.La dimensione finale delle particelle è influenzata dai cicli di macinazione, dal tempo di permanenza e dalle condizioni operative specifiche del mulino.
Punti chiave spiegati:
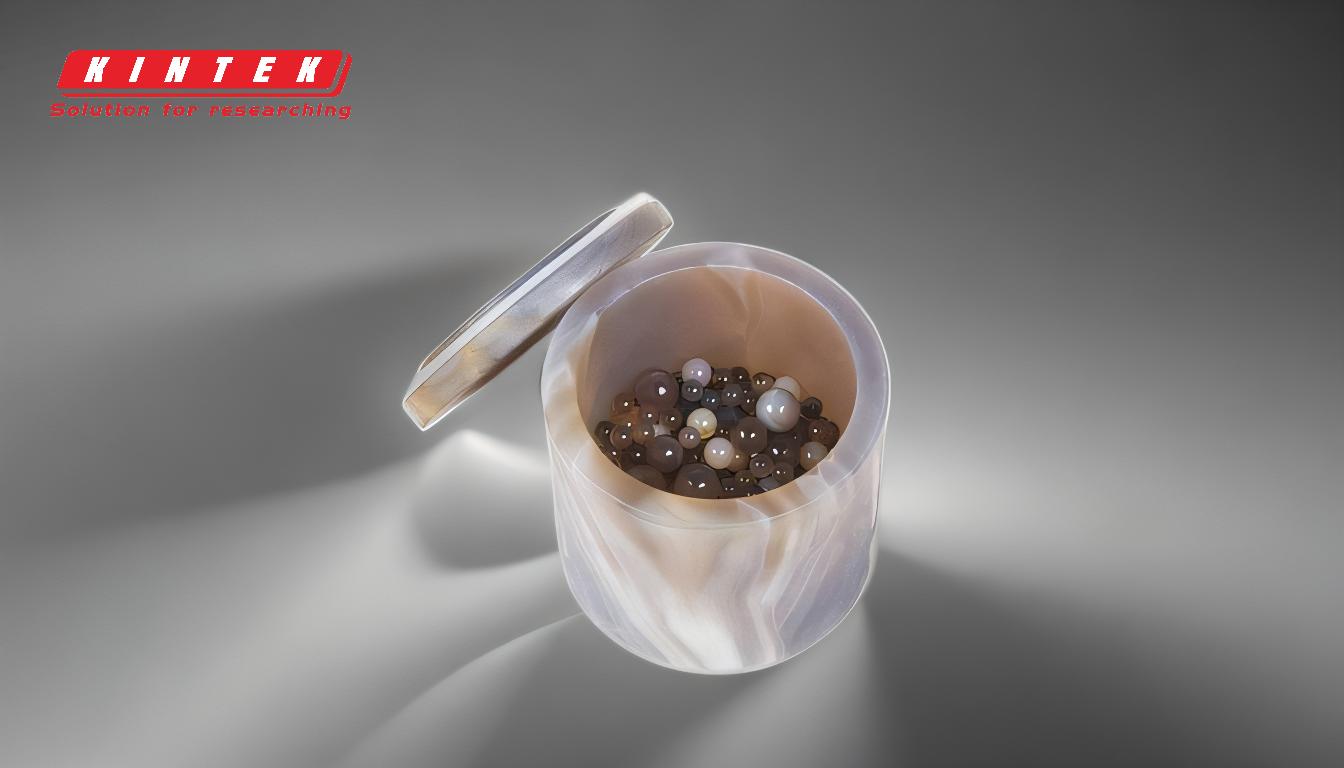
-
Gamma di dimensioni tipiche delle particelle nei mulini a sfere:
- I mulini a sfere sono comunemente utilizzati per ottenere dimensioni delle particelle nell'intervallo tra 1-20 μm in particolare nei laboratori di ceramica e nei processi di sminuzzamento dei minerali.
- La dimensione media iniziale delle particelle (d50) del materiale da macinare svolge un ruolo importante nel determinare la dimensione finale delle particelle.
-
Fattori che influenzano la dimensione delle particelle:
- Mezzo di macinazione (sfere): Le sfere più piccole sono più efficaci nel produrre particelle più fini.Le dimensioni, la densità e il numero di sfere influiscono direttamente sull'efficienza di macinazione.
- Tempo di macinazione: Tempi di macinazione più lunghi producono generalmente particelle di dimensioni più piccole, poiché il materiale è sottoposto a un maggior numero di collisioni e abrasioni.
- Tempo di permanenza: Il tempo che il materiale trascorre nella camera del mulino influisce sul grado di riduzione delle dimensioni.Tempi di permanenza più lunghi consentono una macinazione più accurata.
- Velocità di rotazione: La velocità di rotazione del mulino influenza l'energia impartita al mezzo di macinazione e al materiale.Velocità più elevate possono aumentare l'efficienza di macinazione, ma devono essere ottimizzate per evitare un'usura eccessiva o il surriscaldamento.
- Rapporto di riempimento: La percentuale del volume del mulino riempito con il mezzo di macinazione (sfere) influisce sulle prestazioni di macinazione.Un rapporto di riempimento ottimale garantisce una macinazione efficiente senza sovraccaricare il mulino.
-
Parametri operativi:
- Dimensioni del tamburo: Il diametro e la lunghezza del tamburo, così come il rapporto tra diametro e lunghezza del tamburo (il rapporto ottimale L:D è 1,56-1,64), influenzano l'efficienza di macinazione.
- Velocità e livello di alimentazione: La velocità di alimentazione del materiale nel mulino e il livello del materiale nel serbatoio possono influenzare il processo di macinazione.Velocità di alimentazione costanti aiutano a mantenere condizioni di macinazione ottimali.
- Proprietà del materiale: La durezza e le proprietà fisico-chimiche del materiale da macinare contribuiscono a determinare l'efficienza di macinazione e la dimensione finale delle particelle.
-
Ottimizzazione per applicazioni specifiche:
- Nelle applicazioni industriali, l'ottimizzazione dei parametri del mulino a sfere è fondamentale per ottenere la distribuzione granulometrica desiderata.Ciò include la selezione della dimensione appropriata della sfera, la regolazione della velocità di rotazione e il controllo del rapporto di riempimento.
- Per le applicazioni ceramiche, l'obiettivo è spesso quello di ottenere uno stato di completa miscelazione delle polveri di partenza con una specifica gamma di dimensioni delle particelle.
-
Considerazioni pratiche:
- Cicli di macinazione: Il numero di cicli di macinazione e il tempo di permanenza nel mulino determinano il grado di riduzione delle dimensioni.Possono essere necessari più cicli per raggiungere la finezza desiderata.
- Rimozione tempestiva del prodotto macinato: Una rimozione efficiente del materiale macinato dal mulino impedisce una macinazione eccessiva e garantisce una distribuzione granulometrica uniforme.
Controllando attentamente questi fattori, gli operatori possono ottenere le dimensioni desiderate delle particelle nei processi di macinazione a sfere, sia per la sminuzzatura di minerali industriali che per la preparazione di polveri ceramiche.
Tabella riassuntiva:
Fattore | Impatto sulla dimensione delle particelle |
---|---|
Mezzo di macinazione (sfere) | Le sfere più piccole producono particelle più fini; la dimensione, la densità e il numero influiscono sull'efficienza di macinazione. |
Tempo di macinazione | Tempi di macinazione più lunghi producono particelle più piccole a causa di maggiori collisioni e abrasioni. |
Velocità di rotazione | Le velocità più elevate aumentano l'efficienza della macinazione, ma devono essere ottimizzate per evitare l'usura o il surriscaldamento. |
Rapporto di riempimento | Il rapporto di riempimento ottimale garantisce una macinazione efficiente senza sovraccaricare il mulino. |
Dimensioni del tamburo | Diametro, lunghezza e rapporto L:D influenzano l'efficienza di macinazione. |
Proprietà del materiale | La durezza e le proprietà fisico-chimiche influenzano l'efficienza di macinazione e la dimensione finale delle particelle. |
Ottimizzate il vostro processo di macinazione a sfere per ottenere particelle di dimensioni precise. contattate i nostri esperti oggi stesso !