Il processo di stampaggio a iniezione è un metodo di produzione altamente efficiente utilizzato per produrre parti in plastica di forma complessa in grandi quantità.Comporta la fusione di materiale plastico e la sua iniezione in uno stampo a pressa cavità ad alta pressione, il raffreddamento per la solidificazione e l'espulsione del prodotto finito.Questo processo è ampiamente utilizzato nelle industrie per la sua precisione, ripetibilità e capacità di produrre disegni intricati.Di seguito viene fornita una spiegazione dettagliata, passo dopo passo, del processo di stampaggio a iniezione.
Punti chiave spiegati:
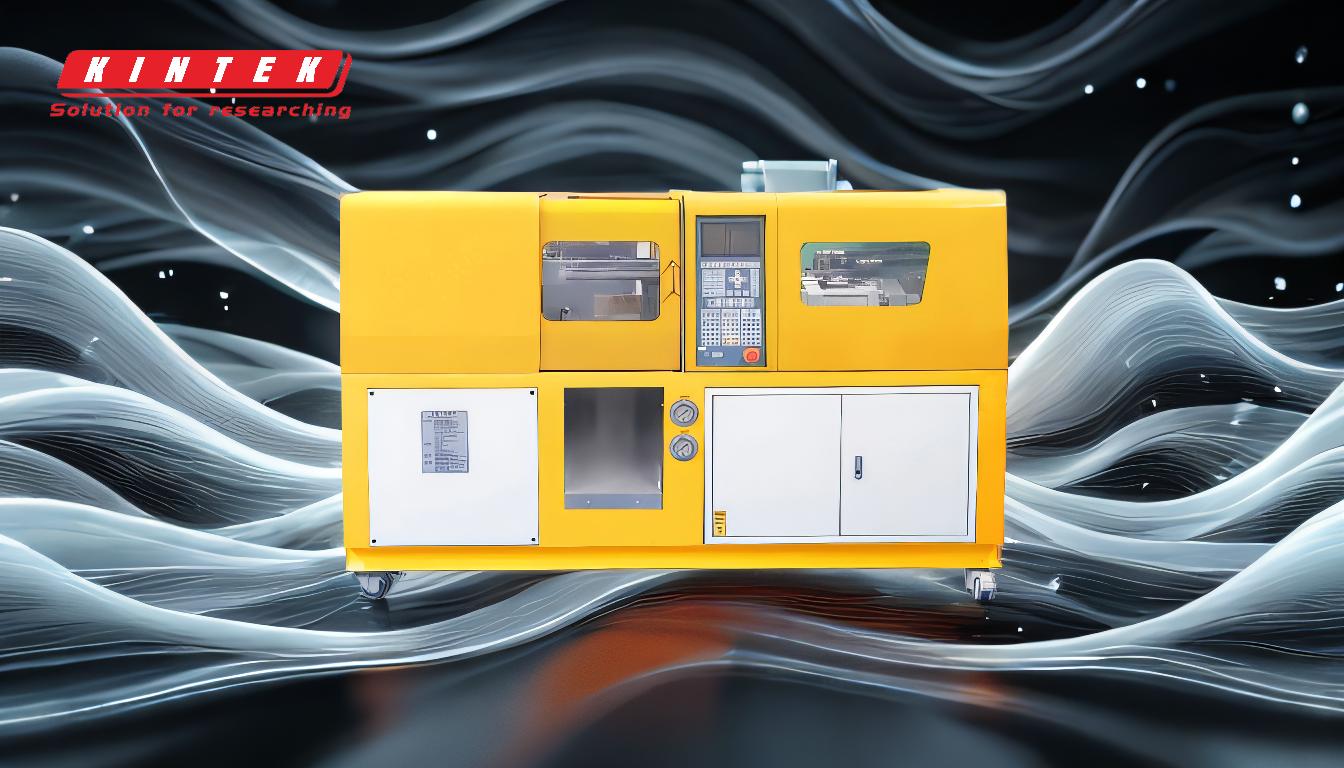
-
Preparazione e alimentazione del materiale
- I pellet o i granuli di plastica vengono introdotti nella tramoggia della pressa a iniezione.
- Il materiale viene quindi trasportato nel cilindro, dove viene riscaldato e miscelato da una vite rotante.
- La coclea assicura una fusione uniforme e l'omogeneizzazione del materiale plastico.
-
Fusione e plastificazione
- All'interno del cilindro, il materiale plastico viene riscaldato fino al punto di fusione, trasformandosi in uno stato fuso.
- La vite continua a mescolare e comprimere la plastica fusa, garantendo una viscosità e una temperatura costanti.
- Questa fase è fondamentale per ottenere pezzi stampati di alta qualità.
-
Iniezione nella cavità dello stampo
- Una volta che la plastica è completamente fusa, la vite si sposta in avanti, agendo come uno stantuffo per iniettare il materiale fuso nella cavità dello stampo.
- Viene applicata una pressione elevata per garantire che il materiale riempia ogni dettaglio dello stampo, comprese le geometrie più complesse.
- Lo stampo è tenuto chiuso da un'unità di serraggio per resistere alla pressione di iniezione.
-
Raffreddamento e solidificazione
- Dopo il riempimento della cavità dello stampo, la plastica fusa inizia a raffreddarsi e a solidificarsi, assumendo la forma dello stampo.
- Il tempo di raffreddamento dipende dalle proprietà del materiale, dallo spessore del pezzo e dalla progettazione dello stampo.
- Un raffreddamento adeguato è essenziale per evitare difetti come deformazioni o segni di affondamento.
-
Apertura dello stampo ed espulsione
- Una volta che il pezzo si è solidificato, lo stampo si apre e i perni di espulsione spingono il prodotto finito fuori dalla cavità dello stampo.
- Il pezzo espulso viene quindi raccolto per essere ulteriormente lavorato o confezionato.
- Lo stampo si richiude e il ciclo si ripete per il pezzo successivo.
-
Post-lavorazione (se necessaria)
- Alcuni pezzi possono richiedere ulteriori fasi come la rifilatura, la verniciatura o l'assemblaggio.
- Queste fasi assicurano che il prodotto finale soddisfi le specifiche e gli standard di qualità desiderati.
Spiegazione dettagliata:
-
Preparazione e alimentazione del materiale
Il processo inizia con la selezione del materiale plastico appropriato, in genere sotto forma di pellet o granuli.Questi materiali vengono caricati nella tramoggia, che li alimenta nel cilindro della pressa a iniezione.Il cilindro è dotato di una vite rotante che trasporta il materiale in avanti riscaldandolo alla temperatura richiesta.Questa fase assicura che il materiale sia pronto per la successiva fase di fusione e plastificazione. -
Fusione e plastificazione
All'interno del cilindro, il materiale plastico è sottoposto al calore e al taglio meccanico della vite.La combinazione di calore e attrito fonde la plastica, trasformandola in un fluido viscoso.Il design della vite assicura una miscelazione completa, eliminando qualsiasi incongruenza nel materiale.Questa fase è fondamentale perché la qualità della plastica fusa influisce direttamente sulle proprietà del prodotto finale, come la resistenza, la finitura superficiale e la precisione dimensionale. -
Iniezione nella cavità dello stampo
Una volta che la plastica è completamente fusa, inizia la fase di iniezione.La vite si muove in avanti, agendo come un pistone per iniettare il materiale fuso nella cavità dello stampo.Lo stampo è progettato con precisione per creare la forma desiderata del pezzo.Durante l'iniezione viene applicata un'elevata pressione per garantire che il materiale riempia tutte le aree dello stampo, compresi i dettagli fini e le sezioni sottili.L'unità di bloccaggio tiene lo stampo ben chiuso per resistere all'elevata pressione di iniezione, evitando perdite o deformazioni. -
Raffreddamento e solidificazione
Dopo il riempimento della cavità dello stampo, inizia la fase di raffreddamento.La plastica fusa inizia a raffreddarsi e a solidificarsi, assumendo la forma dello stampo.Il tempo di raffreddamento è un fattore critico nel processo di stampaggio a iniezione, in quanto determina il tempo di ciclo e influisce sulla qualità del pezzo.Un raffreddamento adeguato garantisce che il pezzo si solidifichi in modo uniforme, riducendo al minimo difetti come deformazioni, segni di affossamento o tensioni interne.Il sistema di raffreddamento all'interno dello stampo, che spesso utilizza canali d'acqua, aiuta a regolare la temperatura e ad accelerare il processo. -
Apertura dello stampo ed espulsione
Una volta che il pezzo si è raffreddato e solidificato a sufficienza, lo stampo si apre e il prodotto finito viene espulso.Per spingere il pezzo fuori dalla cavità dello stampo si utilizzano perni o piastre di espulsione.Lo stampo si chiude e il ciclo si ripete per il pezzo successivo.Questa fase richiede precisione per garantire che il pezzo venga espulso senza danni e che lo stampo sia pronto per l'iniezione successiva. -
Post-trattamento (se necessario)
A seconda dell'applicazione, alcuni pezzi possono richiedere ulteriori fasi di post-elaborazione.Queste possono includere il taglio del materiale in eccesso (flash), la verniciatura o il rivestimento a fini estetici o l'assemblaggio di più componenti.La post-elaborazione assicura che il prodotto finale soddisfi le specifiche e gli standard di qualità richiesti.
Conclusioni:
Il processo di stampaggio a iniezione è un metodo versatile ed efficiente per produrre parti in plastica di alta qualità con geometrie complesse.Seguendo le fasi di preparazione del materiale, fusione, iniezione, raffreddamento, espulsione e post-lavorazione, i produttori possono ottenere risultati coerenti e precisi.Questo processo è ampiamente utilizzato in tutti i settori industriali per la sua capacità di produrre grandi quantità di pezzi con scarti minimi ed elevata ripetibilità.
Tabella riassuntiva:
Passo | Descrizione |
---|---|
1.Preparazione del materiale | I pellet di plastica vengono introdotti nella tramoggia, riscaldati e mescolati nel barile. |
2.Fusione e plastificazione | Il materiale viene fuso e omogeneizzato dalla vite per ottenere una viscosità costante. |
3.Iniezione nello stampo | La plastica fusa viene iniettata nella cavità dello stampo ad alta pressione. |
4.Raffreddamento e solidificazione | La plastica si raffredda e si solidifica nella forma desiderata. |
5.Apertura dello stampo ed espulsione | Lo stampo si apre e i perni di espulsione spingono fuori il pezzo finito. |
6.Post-elaborazione | Per ottenere la qualità finale possono essere necessarie ulteriori fasi, come la rifilatura o la verniciatura. |
Siete pronti a ottimizzare il vostro processo di produzione? Contattateci oggi per saperne di più sulle soluzioni di stampaggio a iniezione!