L'efficienza della macinazione a sfere misura l'efficacia con cui un mulino a sfere riesce a macinare i materiali nelle dimensioni desiderate, riducendo al minimo il consumo energetico e il tempo.È influenzata da diversi fattori, tra cui il design del mulino, le proprietà del materiale da macinare e i parametri operativi.I fattori chiave includono il diametro del tamburo, il rapporto lunghezza/diametro, la dimensione e la densità delle sfere, la velocità di rotazione, la velocità di avanzamento e la durezza del materiale.Per le particelle più fini sono spesso necessarie sfere più piccole e tempi di macinazione più lunghi, mentre la produttività ottimale si ottiene con uno specifico rapporto diametro-lunghezza del tamburo (1,56-1,64).La comprensione di questi fattori aiuta a ottimizzare il processo di macinazione per una migliore efficienza.
Punti chiave spiegati:
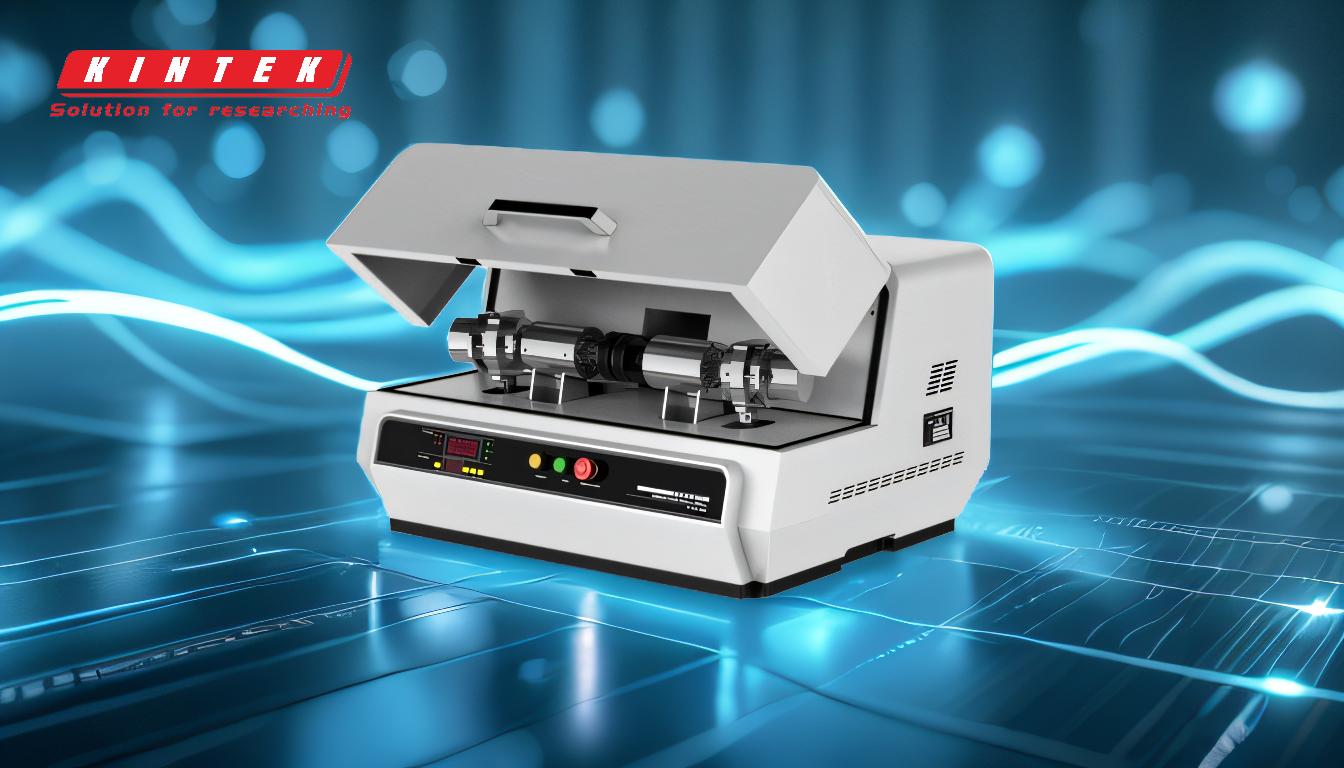
-
Fattori che influenzano l'efficienza della macinazione a sfere
- Tempo di residenza:Il tempo che il materiale trascorre nella camera del mulino influisce sul grado di macinazione.Tempi di permanenza più lunghi portano generalmente a particelle più fini, ma possono ridurre la produttività.
- Caratteristiche della sfera:Le dimensioni, la densità e il numero di sfere influiscono sull'efficienza di macinazione.Le sfere più piccole sono più adatte a produrre particelle più fini, mentre quelle più grandi sono più efficaci per la macinazione grossolana.
- Proprietà del materiale:La durezza e la natura del materiale da macinare determinano l'energia necessaria per la macinazione.I materiali più duri richiedono più energia e tempi di macinazione più lunghi.
- Velocità e livello di avanzamento:La velocità di alimentazione del materiale nel mulino e il livello del materiale nel serbatoio influenzano l'efficienza di macinazione.Il sovraccarico o il sottocarico possono ridurre l'efficienza.
- Velocità di rotazione:La velocità del cilindro del mulino influisce sull'energia cinetica delle sfere.La velocità ottimale garantisce una macinazione efficace senza eccessiva usura o spreco di energia.
-
Parametri di progettazione che influiscono sull'efficienza
- Diametro del tamburo e rapporto lunghezza/diametro:Il diametro del tamburo e il suo rapporto con la lunghezza (il rapporto ottimale L:D è 1,56-1,64) hanno un impatto significativo sulla produttività.Un mulino ben progettato garantisce una macinazione efficiente e un uso efficiente dell'energia.
- Forma della superficie della corazza:La forma della superficie interna del mulino (armatura) influenza il movimento delle sfere e del materiale, incidendo sull'efficienza di macinazione.
- Rimozione tempestiva del prodotto macinato:La rimozione efficiente del materiale macinato previene la sovramacinazione e garantisce una qualità costante del prodotto.
-
Considerazioni operative
- Tempo di macinazione:Per ottenere particelle più fini sono necessari tempi di macinazione più lunghi, ma ciò deve essere bilanciato con il consumo energetico e la produttività.
- Riempimento e dimensioni delle sfere:Il corretto riempimento del mulino con le sfere e la scelta delle dimensioni giuste per il materiale da macinare sono fondamentali per una macinazione efficiente.
- Velocità di rotazione:La regolazione della velocità di rotazione in base al materiale e alle dimensioni desiderate delle particelle garantisce una macinazione ottimale senza inutili spese energetiche.
-
Implicazioni pratiche per gli acquirenti
- Ottimizzazione specifica del materiale:La comprensione delle proprietà del materiale aiuta a selezionare il giusto design del mulino e i parametri operativi.
- Efficienza energetica:Il bilanciamento del tempo di macinazione, delle dimensioni delle sfere e della velocità di rotazione può ridurre il consumo energetico e i costi operativi.
- Produzione e qualità:L'ottimizzazione della velocità di alimentazione, del tempo di permanenza e della rimozione del prodotto garantisce una qualità costante e un'elevata produttività.
Prendendo in considerazione questi fattori, gli acquirenti possono scegliere e far funzionare i mulini a sfere in modo più efficace, garantendo un'elevata efficienza e un buon rapporto costi-benefici nei processi di macinazione.
Tabella riassuntiva:
Fattore | Impatto sull'efficienza |
---|---|
Tempo di permanenza | Tempi più lunghi producono particelle più fini, ma possono ridurre la produttività. |
Caratteristiche delle sfere | Sfere più piccole per le particelle fini; sfere più grandi per la macinazione grossolana. |
Proprietà del materiale | I materiali più duri richiedono più energia e tempi di macinazione più lunghi. |
Velocità e livello di alimentazione | Il sovraccarico o il sottocarico riducono l'efficienza. |
Velocità di rotazione | La velocità ottimale garantisce una macinazione efficace senza eccessivi sprechi di energia. |
Design del tamburo | Il rapporto L:D ottimale (1,56-1,64) aumenta la produttività e il consumo di energia. |
Tempo di macinazione | Tempi più lunghi per particelle più fini, in rapporto al consumo energetico e alla produttività. |
Avete bisogno di aiuto per ottimizzare il vostro processo di macinazione a sfere? Contattate i nostri esperti oggi stesso per soluzioni su misura!