La differenza principale tra l'evaporazione a fascio elettronico e l'evaporazione termica risiede nel metodo utilizzato per vaporizzare il materiale. L'evaporazione a fascio elettronico impiega un fascio di elettroni ad alta energia per riscaldare e vaporizzare direttamente il materiale bersaglio, rendendola adatta a materiali ad alto punto di fusione come gli ossidi. L'evaporazione termica, invece, utilizza una resistenza elettrica per riscaldare un crogiolo, che poi fonde ed evapora il materiale di partenza, ed è quindi ideale per materiali con temperature di fusione più basse. L'evaporazione a fascio elettronico offre vantaggi quali rivestimenti di film sottili più densi, tassi di deposizione più elevati e minori rischi di impurità rispetto all'evaporazione termica.
Punti chiave spiegati:
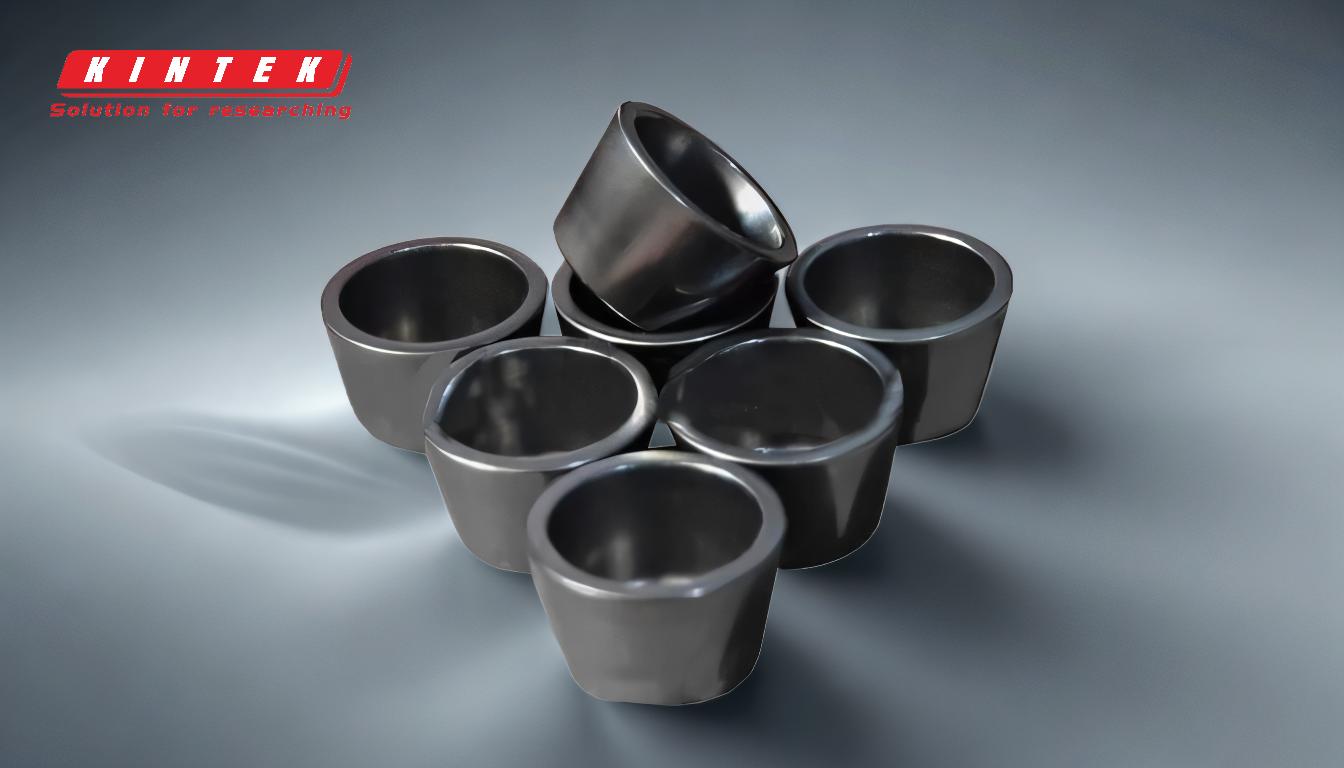
-
Metodo di vaporizzazione:
- Evaporazione a fascio elettronico: Utilizza un fascio di elettroni ad alta energia per riscaldare e vaporizzare direttamente il materiale bersaglio. Questo metodo trasferisce energia cinetica al materiale, facendolo evaporare.
- Evaporazione termica: Si basa sulla resistenza elettrica per riscaldare un crogiolo, che poi fonde ed evapora il materiale di partenza. Il calore viene applicato indirettamente attraverso il crogiolo.
-
Compatibilità dei materiali:
- Evaporazione a fascio elettronico: Adatto per materiali ad alto punto di fusione, come gli ossidi, che non sublimano facilmente durante l'evaporazione termica.
- Evaporazione termica: È più adatto per i materiali con temperature di fusione più basse, poiché non è in grado di vaporizzare efficacemente i materiali ad alto punto di fusione.
-
Qualità del rivestimento:
- Evaporazione a fascio elettronico: Produce rivestimenti a film sottile più densi grazie al processo ad alta energia, con conseguente migliore adesione e uniformità.
- Evaporazione termica: Tende a produrre rivestimenti meno densi, che possono richiedere ulteriori passaggi per ottenere una qualità comparabile.
-
Tasso di deposizione:
- Evaporazione a fascio elettronico: Offre un tasso di deposizione più elevato, rendendolo più efficiente per applicazioni su larga scala o ad alta produttività.
- Evaporazione termica: Ha un tasso di deposizione più lento, che può limitarne l'uso nei processi sensibili ai tempi.
-
Rischi di impurità:
- Evaporazione a fascio elettronico: Minore rischio di impurità perché il fascio di elettroni si rivolge direttamente al materiale, riducendo al minimo la contaminazione dal crogiolo.
- Evaporazione termica: Rischio più elevato di impurità a causa di potenziali reazioni tra il materiale e il crogiolo durante il riscaldamento.
-
Idoneità all'applicazione:
- Evaporazione a fascio elettronico: Ideale per le applicazioni avanzate che richiedono materiali di elevata purezza e ad alto punto di fusione, come nella produzione di semiconduttori o nei rivestimenti ottici.
- Evaporazione termica: Più adatto per applicazioni più semplici che coinvolgono materiali a basso punto di fusione, come nella deposizione di base di film sottili o nei rivestimenti decorativi.
Comprendendo queste differenze chiave, gli acquirenti di attrezzature e materiali di consumo possono prendere decisioni informate in base ai requisiti specifici delle loro applicazioni, come il tipo di materiale, la qualità di rivestimento desiderata e l'efficienza produttiva.
Tabella riassuntiva:
Aspetto | Evaporazione a fascio elettronico | Evaporazione termica |
---|---|---|
Metodo di vaporizzazione | Il fascio di elettroni ad alta energia riscalda e vaporizza direttamente il materiale. | La resistenza elettrica riscalda un crogiolo, che fonde ed evapora il materiale. |
Compatibilità dei materiali | Adatto per materiali ad alto punto di fusione come gli ossidi. | Ideale per materiali con temperature di fusione inferiori. |
Qualità del rivestimento | Produce rivestimenti più densi e uniformi con una migliore adesione. | Rivestimenti meno densi; possono richiedere fasi aggiuntive per la qualità. |
Tasso di deposizione | Velocità di deposizione più elevata, ideale per applicazioni su larga scala o ad alta produttività. | Velocità di deposizione più bassa, meno efficiente per i processi sensibili ai tempi. |
Rischi di impurità | Minor rischio di impurità grazie al puntamento diretto del materiale. | Rischio più elevato di impurità derivanti da reazioni al crogiolo. |
Idoneità all'applicazione | Applicazioni avanzate come semiconduttori e rivestimenti ottici. | Applicazioni più semplici, come la deposizione di base di film sottili o rivestimenti decorativi. |
Avete bisogno di aiuto per scegliere il metodo di evaporazione più adatto alla vostra applicazione? Contattate i nostri esperti oggi stesso!