La deposizione chimica da fase vapore (CVD) e la deposizione fisica da fase vapore (PVD) sono due tecniche ampiamente utilizzate per depositare film sottili su substrati, ciascuna con processi, vantaggi e applicazioni distinti. La CVD comporta reazioni chimiche tra i precursori gassosi e il substrato, risultando in un rivestimento solido spesso più spesso e uniforme. Funziona a temperature più elevate ed è adatto per un'ampia gamma di materiali, tra cui ceramica e polimeri. Il PVD, d'altro canto, utilizza processi fisici come lo sputtering o l'evaporazione per depositare i materiali direttamente sul substrato in un ambiente sotto vuoto. Funziona a temperature più basse ed è ideale per metalli, leghe e ceramica, producendo rivestimenti più sottili, lisci e durevoli. La scelta tra CVD e PVD dipende da fattori quali compatibilità dei materiali, spessore del rivestimento e requisiti applicativi.
Punti chiave spiegati:
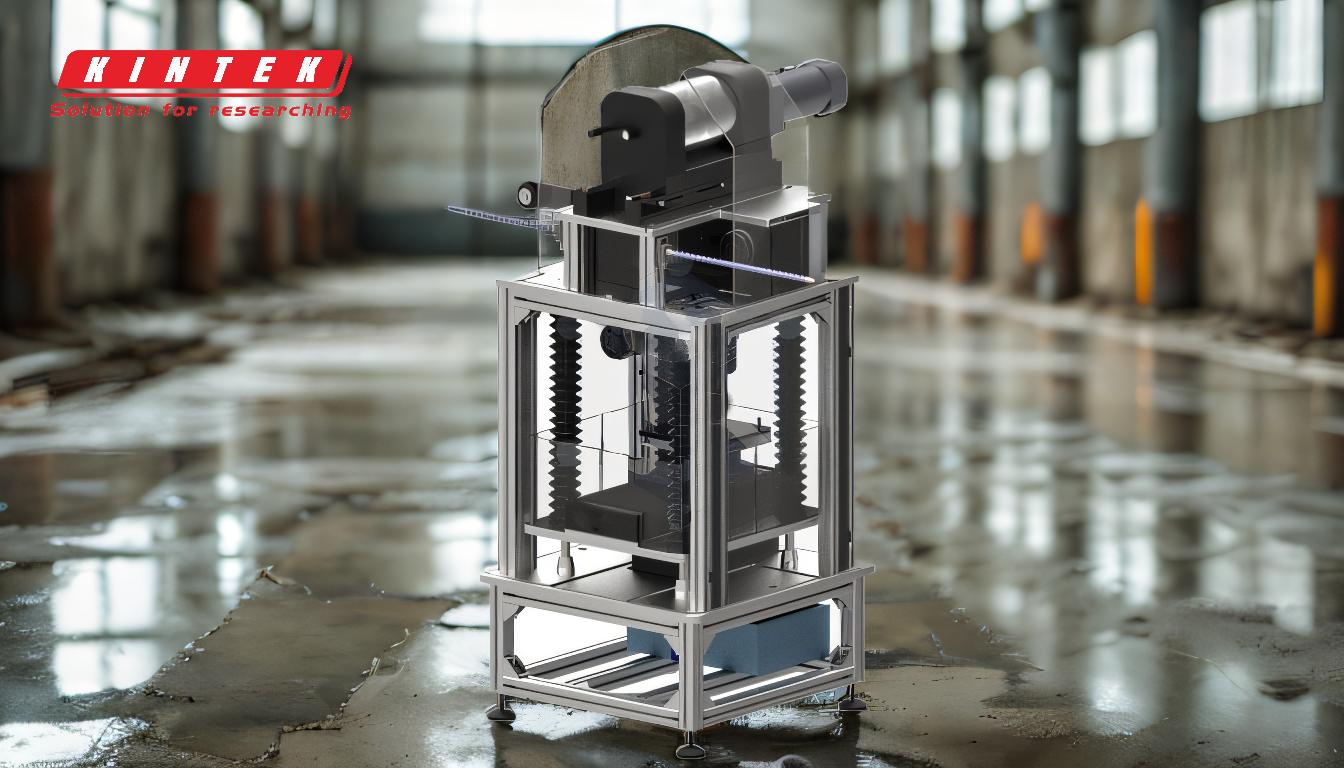
-
Natura del processo di deposizione:
- CVD: Nella CVD la deposizione avviene attraverso reazioni chimiche tra i precursori gassosi e il substrato. Questo processo multidirezionale consente una copertura uniforme, anche su geometrie complesse. Le reazioni chimiche danno come risultato un rivestimento solido che aderisce bene al substrato.
- PVD: Il PVD è un processo in linea di vista, il che significa che il materiale viene depositato direttamente sul substrato senza interazione chimica. Questo metodo è più direzionale, il che lo rende meno adatto al rivestimento di forme complesse ma ideale per applicazioni che richiedono rivestimenti precisi e sottili.
-
Temperature di funzionamento:
- CVD: Funziona tipicamente a temperature più elevate, comprese tra 450°C e 1050°C. Questo ambiente ad alta temperatura facilita le reazioni chimiche necessarie per la deposizione.
- PVD: Funziona a temperature più basse, solitamente tra 250°C e 450°C. Ciò rende il PVD adatto a substrati che non possono resistere alle alte temperature, come alcune plastiche o materiali sensibili al calore.
-
Natura della sostanza di rivestimento:
- CVD: Utilizzato principalmente per depositare ceramiche e polimeri. Le reazioni chimiche consentono la formazione di rivestimenti densi e uniformi.
- PVD: Può depositare una gamma più ampia di materiali, inclusi metalli, leghe e ceramiche. La natura fisica del processo si traduce in rivestimenti meno densi ma altamente durevoli.
-
Area di copertura del rivestimento:
- CVD: Fornisce un'eccellente copertura, anche su geometrie complesse, grazie al processo di deposizione multidirezionale.
- PVD: Offre una copertura limitata a causa della sua natura in linea di vista, rendendolo più adatto a superfici piane o meno complesse.
-
Spessore e levigatezza del film:
- CVD: Produce rivestimenti più spessi e ruvidi, che possono essere utili per applicazioni che richiedono durabilità e resistenza all'usura.
- PVD: Genera rivestimenti più sottili, lisci e uniformi, ideali per applicazioni che richiedono precisione e pregio estetico.
-
Applicazioni:
- CVD: Comunemente utilizzato nei settori che richiedono rivestimenti ad alte prestazioni, come la produzione di semiconduttori, rivestimenti per utensili e applicazioni resistenti all'usura.
- PVD: Ampiamente utilizzato in applicazioni che richiedono rivestimenti sottili, durevoli ed esteticamente gradevoli, come nell'industria automobilistica, aerospaziale e decorativa.
-
Metodi primari:
- CVD: Si basa su reazioni chimiche tra le molecole di gas e il substrato. I metodi comuni includono CVD a pressione atmosferica, CVD a bassa pressione e CVD potenziata dal plasma.
- PVD: Coinvolge processi fisici come lo sputtering, l'evaporazione termica e l'evaporazione del fascio di elettroni. Questi metodi consentono la creazione di rivestimenti a film sottile di dimensioni nanometriche con diverse composizioni.
In sintesi, sebbene sia la CVD che il PVD siano tecniche essenziali per la deposizione di film sottile, differiscono significativamente nei processi, nelle condizioni operative e nelle applicazioni. Il CVD è preferito per la sua capacità di produrre rivestimenti spessi e uniformi su geometrie complesse, mentre il PVD è preferito per la sua precisione, temperature operative più basse e capacità di depositare un'ampia gamma di materiali. La scelta tra i due dipende dai requisiti specifici dell'applicazione, inclusa la compatibilità dei materiali, lo spessore del rivestimento e le proprietà desiderate.
Tabella riassuntiva:
Aspetto | CVD | PVD |
---|---|---|
Processo di deposizione | Reazioni chimiche tra precursori gassosi e substrato. | Processi fisici come lo sputtering o l'evaporazione nel vuoto. |
Intervallo di temperatura | da 450°C a 1050°C | da 250°C a 450°C |
Materiali di rivestimento | Ceramiche, polimeri | Metalli, leghe, ceramiche |
Copertura | Multidirezionale, ottimo per geometrie complesse | Linea di vista, limitata a superfici piane o meno complesse |
Spessore della pellicola | Rivestimenti più spessi e ruvidi | Rivestimenti più sottili e lisci |
Applicazioni | Produzione di semiconduttori, rivestimenti di utensili, resistenza all'usura | Industrie automobilistiche, aerospaziali e decorative |
Hai bisogno di aiuto nella scelta tra CVD e PVD per la tua applicazione? Contatta i nostri esperti oggi!