I fattori che influenzano le prestazioni e l'efficienza di un mulino a sfere possono essere classificati in tre aree principali: caratteristiche del materiale, progettazione dell'apparecchiatura e condizioni operative.Le caratteristiche del materiale comprendono le proprietà fisiche e chimiche del materiale di alimentazione, come la durezza, la densità e il contenuto di umidità.I fattori di progettazione dell'apparecchiatura comprendono il diametro del tamburo, il rapporto lunghezza/diametro, il tipo e le dimensioni dei mezzi di macinazione e il materiale di rivestimento.Le condizioni operative riguardano la velocità di rotazione, il rapporto di riempimento del mulino, la velocità di alimentazione e la rimozione tempestiva del prodotto macinato.La comprensione di questi fattori è fondamentale per ottimizzare il processo di macinazione e ottenere i risultati desiderati.
Punti chiave spiegati:
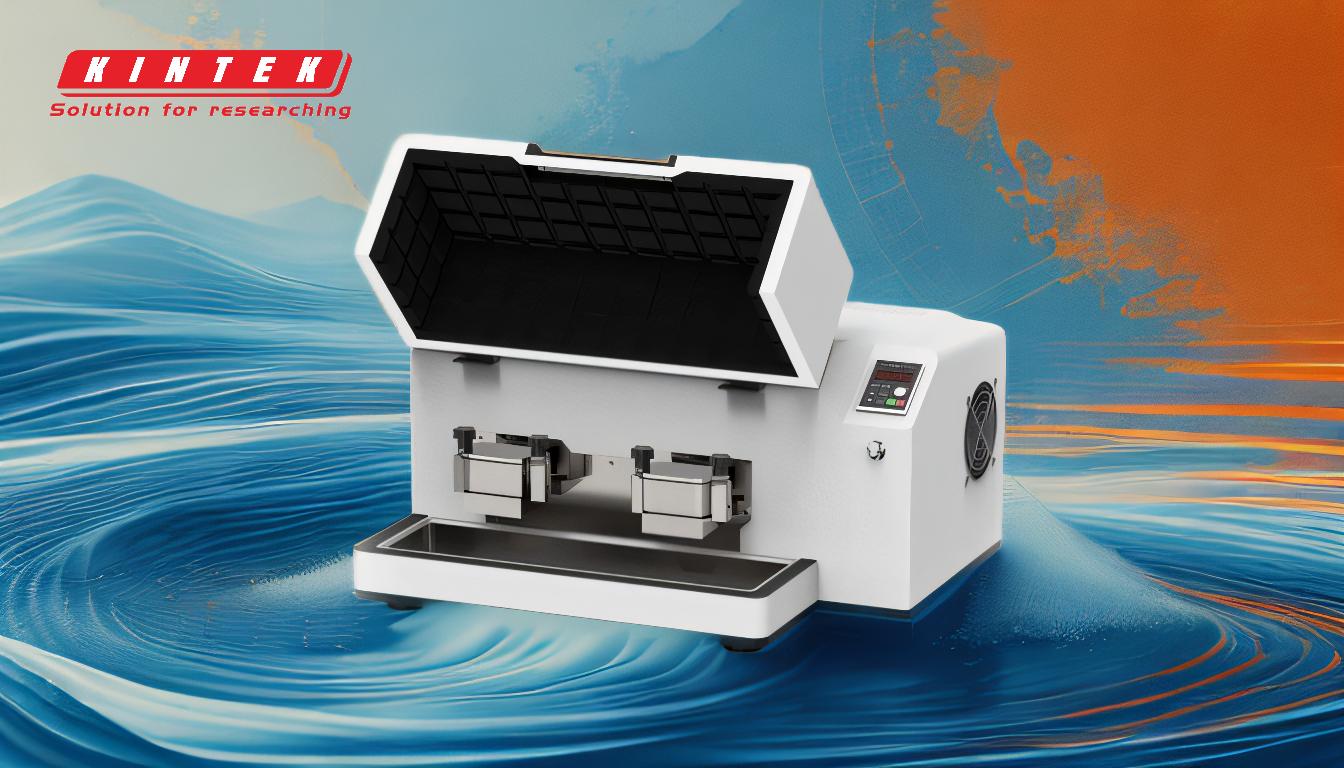
-
Caratteristiche del materiale:
- Durezza:I materiali più duri richiedono una maggiore energia per la macinazione, incidendo sull'efficienza del mulino a sfere.
- Densità:I materiali più densi possono richiedere una regolazione dei mezzi di macinazione per ottenere una macinazione efficace.
- Contenuto di umidità:Un elevato contenuto di umidità può causare intasamenti e ridurre l'efficienza di macinazione.
-
Design dell'apparecchiatura:
- Diametro del tamburo e rapporto lunghezza/diametro:La produttività dei mulini a sfere è influenzata dal diametro del tamburo e dal rapporto ottimale tra lunghezza e diametro, tipicamente compreso tra 1,56 e 1,64.
- Mezzi di macinazione:Le dimensioni, il tipo e la densità delle sfere di macinazione (acciaio, acciaio inossidabile, ceramica o gomma) hanno un impatto significativo sull'efficienza di macinazione.
- Materiale del rivestimento:La superficie interna del mulino è rivestita con materiali resistenti all'abrasione, come l'acciaio al manganese o la gomma, per proteggere il mantello e migliorare la macinazione.
-
Condizioni operative:
- Velocità di rotazione:La velocità di rotazione del mulino influisce sul movimento dei mezzi di macinazione e del materiale, influenzando l'efficienza di macinazione.
- Rapporto di riempimento:La percentuale del volume del mulino riempito con il mezzo di macinazione (sfere) deve essere ottimizzata per bilanciare l'efficienza di macinazione e il consumo energetico.
- Velocità e livello di alimentazione:Il controllo della velocità di alimentazione e il mantenimento di un livello adeguato di materiale nel mulino assicurano una macinazione costante e prevengono il sovraccarico.
- Rimozione tempestiva del prodotto macinato:La rimozione efficiente del prodotto macinato è essenziale per mantenere un funzionamento continuo ed evitare una nuova macinazione.
-
Considerazioni aggiuntive:
- Tempo di permanenza:Il tempo di permanenza del materiale nella camera del mulino influisce sul grado di macinazione.Tempi di permanenza più lunghi possono portare a una macinazione più fine, ma possono anche aumentare il consumo energetico.
- Forma della superficie della corazza:La forma della superficie della corazza può influenzare il movimento e l'impatto dei mezzi di macinazione, incidendo sulle prestazioni complessive della macinazione.
Considerando attentamente e ottimizzando questi fattori, gli operatori possono migliorare le prestazioni e l'efficienza dei mulini a sfere, ottenendo migliori risultati di macinazione e riducendo i costi operativi.
Tabella riassuntiva:
Categoria | Fattori chiave |
---|---|
Caratteristiche del materiale | Durezza, densità, contenuto di umidità |
Progettazione dell'apparecchiatura | Diametro del tamburo, rapporto lunghezza/diametro, materiale di macinazione, materiale del rivestimento |
Condizioni operative | Velocità di rotazione, rapporto di riempimento, velocità di avanzamento, rimozione tempestiva del prodotto macinato |
Considerazioni aggiuntive | Tempo di permanenza, forma della superficie dell'armatura |
Ottimizzate le prestazioni del vostro mulino a sfere oggi stesso. contattate i nostri esperti per una consulenza !