I rivestimenti PVD (Physical Vapor Deposition) sono effettivamente resistenti ai graffi, grazie alla loro elevata durezza e durata.Questi rivestimenti vengono applicati a livello atomico, consentendo un controllo preciso delle loro proprietà, come la durezza, la densità e l'adesione.I rivestimenti PVD sono quattro volte più duri del cromo e quindi altamente resistenti a graffi, corrosione e usura.La loro durezza varia da 1500 a 4500 HV (Vickers), significativamente superiore a quella di molti materiali tradizionali come l'acciaio al carbonio o l'acciaio nichelato.Inoltre, i rivestimenti PVD si legano fortemente al substrato, garantendo prestazioni durature anche in ambienti difficili.I bassi requisiti di manutenzione e le finiture decorative ne aumentano ulteriormente l'attrattiva per le applicazioni funzionali ed estetiche.
Punti chiave spiegati:
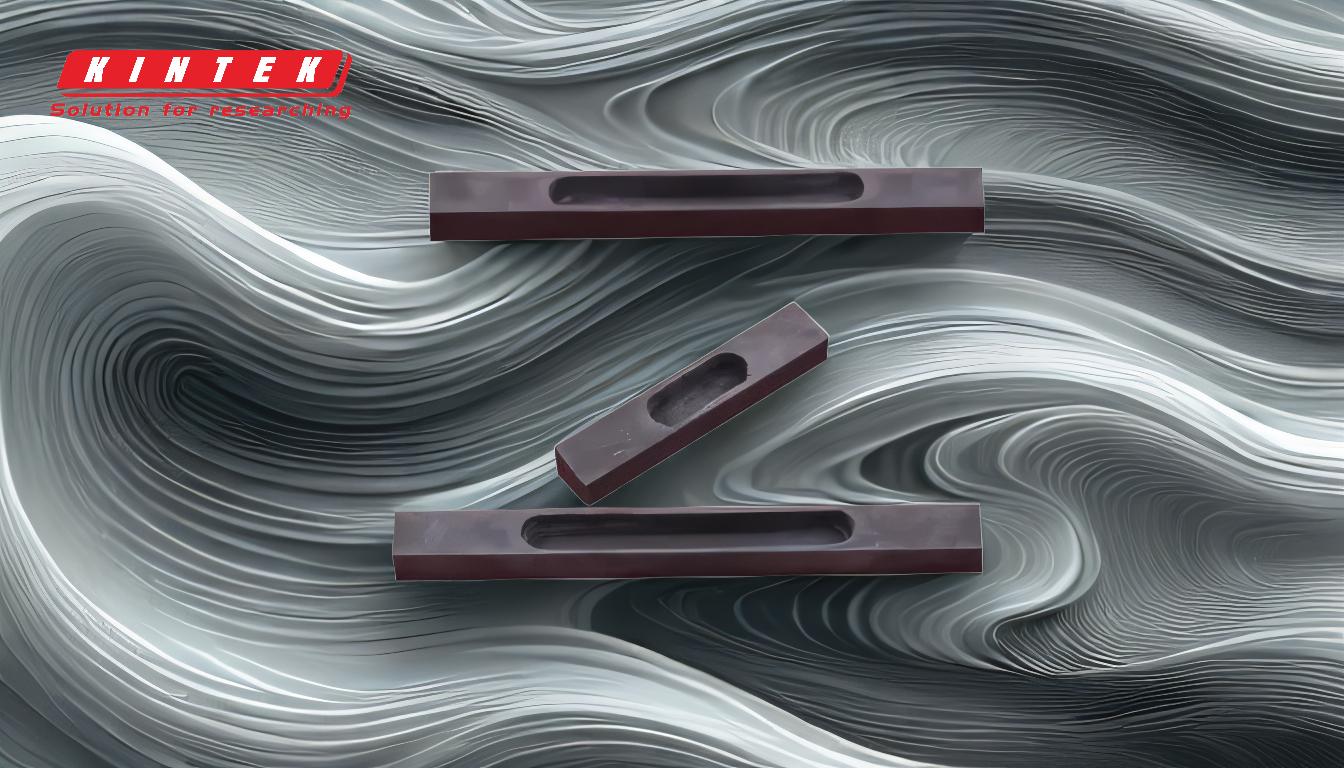
-
Elevata durezza dei rivestimenti PVD:
-
I rivestimenti PVD hanno una durezza di 1500-4500 HV (Vickers), notevolmente superiore a quella di molti materiali tradizionali.Per fare un confronto:
- Acciaio al carbonio: ~250 HV (25 HRC).
- Acciaio nichelato e cromato: 600-1000 HV.
- Questa elevata durezza contribuisce alla resistenza ai graffi, poiché i materiali più duri sono meno soggetti a deformazioni o danni da abrasione.
-
I rivestimenti PVD hanno una durezza di 1500-4500 HV (Vickers), notevolmente superiore a quella di molti materiali tradizionali.Per fare un confronto:
-
Confronto con il cromo:
- I rivestimenti PVD sono quattro volte più duri del cromo e quindi più resistenti ai graffi e all'usura.
- Questa maggiore durezza ne aumenta anche la durata in ambienti difficili, come le zone costiere o gli ambienti industriali.
-
Applicazione a livello atomico:
- I rivestimenti PVD vengono applicati a livello atomico, consentendo un controllo preciso della loro struttura, densità e stechiometria.
- Questa precisione consente di creare rivestimenti con caratteristiche specifiche, come l'elevata durezza, la lubrificazione e l'adesione, che contribuiscono alla resistenza ai graffi.
-
Forte adesione al substrato:
- I rivestimenti PVD aderiscono fortemente al substrato, anche penetrandolo leggermente, garantendo un'adesione duratura.
- Questo forte legame impedisce la scheggiatura o il distacco, migliorando ulteriormente la resistenza ai graffi e la durata complessiva.
-
Resistenza all'usura e alla corrosione:
- I rivestimenti PVD sono altamente resistenti all'usura e alla corrosione e sono quindi adatti ad applicazioni esposte a condizioni difficili.
- Il basso coefficiente di attrito e la resistenza chimica contribuiscono alla loro longevità e resistenza ai graffi.
-
Vantaggi ambientali e di manutenzione:
- I rivestimenti PVD sono ecologici e richiedono poca manutenzione.
- La loro resistenza all'appannamento, allo sbiadimento e ai graffi garantisce il mantenimento dell'aspetto e della funzionalità nel tempo.
-
Applicazioni e versatilità:
- I rivestimenti PVD sono ideali sia per scopi funzionali che decorativi e offrono una finitura brillante e una resistenza superiore ai graffi.
- Sono ampiamente utilizzati in settori come quello automobilistico, aerospaziale e dei beni di consumo, dove la durata e l'estetica sono fondamentali.
In sintesi, i rivestimenti PVD sono altamente resistenti ai graffi grazie alla loro eccezionale durezza, alla forte adesione ai substrati e alla precisa applicazione a livello atomico.Queste proprietà li rendono una scelta superiore per le applicazioni che richiedono durata, longevità ed estetica.
Tabella riassuntiva:
Proprietà | Rivestimenti PVD | Materiali tradizionali |
---|---|---|
Durezza (HV) | 1500-4500 | Acciaio al carbonio: ~250 |
Resistenza ai graffi | Alta | Da bassa a moderata |
Resistenza all'usura e alla corrosione | Eccellente | Moderata |
Adesione al substrato | Forte | Variabile |
Requisiti di manutenzione | Basso | Alto |
Applicazioni | Automotive, aerospaziale, beni di consumo | Uso generale |
Scoprite come i rivestimenti PVD possono migliorare la durata e l'estetica dei vostri prodotti... contattateci oggi stesso !