I rivestimenti PVD (Physical Vapor Deposition) sono altamente resistenti alla corrosione e sono quindi adatti ad applicazioni impegnative in cui la durata è fondamentale.Questi rivestimenti creano uno strato sottile, duro e durevole che si lega fortemente al substrato, migliorandone la resistenza alla corrosione, all'ossidazione e all'usura.Il processo prevede la vaporizzazione di un materiale target nel vuoto e il suo deposito sul substrato, garantendo un rivestimento puro e duraturo.I rivestimenti PVD, come il nitruro di zirconio (ZrN), hanno dimostrato prestazioni eccezionali nei test di resistenza alla corrosione, compresi quelli in nebbia salina neutra e CASS.La loro durezza, lo spessore ridotto e la forte adesione li rendono ideali per gli ambienti difficili, comprese le zone costiere.
Punti chiave spiegati:
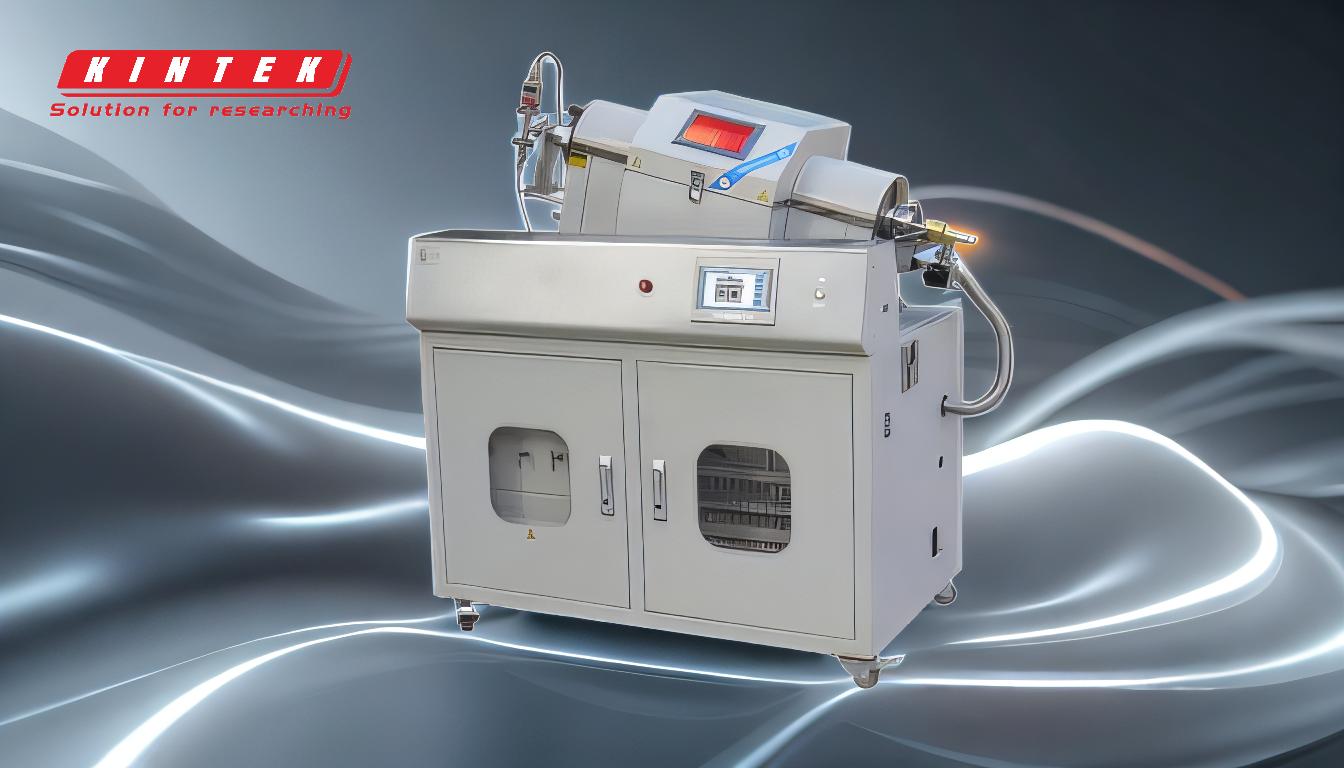
-
Resistenza alla corrosione dei rivestimenti PVD:
- I rivestimenti PVD sono altamente resistenti alla corrosione e all'ossidazione.Formano uno strato protettivo che protegge il substrato dai fattori ambientali che causano ruggine, appannamento o degrado.
- La sottigliezza dei rivestimenti PVD (da 0,5 a 5 micron) non ne compromette l'efficacia.Al contrario, la loro estrema sottigliezza ne rende difficile la rimozione, garantendo una protezione a lungo termine.
-
Durata e durezza:
- I rivestimenti PVD sono quattro volte più duri del cromo e quindi altamente resistenti ai graffi e durevoli.Questa durezza contribuisce alla loro capacità di resistere a condizioni difficili, compresi gli ambienti corrosivi.
- La durezza del rivestimento è un fattore critico per la sua durata.Ad esempio, un rivestimento TiN (nitruro di titanio) può aumentare il limite di fatica e la resistenza di un materiale di substrato come la lega Ti-6Al-4V.
-
Adesione e longevità:
- I rivestimenti PVD aderiscono fortemente al substrato, penetrandolo anche leggermente.Questa forte adesione garantisce che il rivestimento rimanga intatto per lunghi periodi, aumentando la durata del prodotto fino a dieci volte in alcuni casi.
- Il processo di ricottura utilizzato nel rivestimento PVD assicura che lo strato sia privo di impurità, migliorando ulteriormente la durata e la resistenza all'usura e alla corrosione.
-
Prestazioni nei test di corrosione:
- I rivestimenti PVD, come il nitruro di zirconio (ZrN), hanno dimostrato prestazioni eccezionali nei test di corrosione standardizzati.Ad esempio, hanno superato le 1200 ore di test in nebbia salina neutra (ASTM B117) e le 150 ore di test CASS, misure rigorose di resistenza alla corrosione.
- Questi risultati evidenziano l'idoneità dei rivestimenti PVD per applicazioni esposte ad ambienti corrosivi, come quelli marini o costieri.
-
Applicazioni in ambienti difficili:
- I rivestimenti PVD sono ideali per i progetti esposti ad ambienti difficili, compresi quelli vicini alla costa, dove l'acqua salata e l'umidità possono accelerare la corrosione.
- La loro capacità di replicare la finitura originale dei materiali con il minimo sforzo li rende versatili per applicazioni sia funzionali che estetiche.
-
Processo e purezza:
- Il processo PVD prevede la vaporizzazione di un materiale bersaglio sotto vuoto e il suo deposito sul substrato.In questo modo si ottiene un rivestimento puro e privo di impurità, che migliora la durata e la resistenza alla corrosione.
- Il processo consente un controllo preciso delle proprietà del rivestimento, tra cui lo spessore, la durezza e l'adesione, garantendo prestazioni ottimali per applicazioni specifiche.
In sintesi, i rivestimenti PVD sono altamente resistenti alla corrosione grazie alla loro durezza, alla forte adesione e alla purezza.Le loro prestazioni nei rigorosi test di corrosione e l'idoneità agli ambienti difficili li rendono una scelta eccellente per le applicazioni che richiedono una lunga durata e protezione dalla corrosione.
Tabella riassuntiva:
Caratteristica | Dettagli |
---|---|
Resistenza alla corrosione | Altamente resistente alla ruggine, all'appannamento e all'ossidazione; ideale per ambienti difficili. |
Durezza | 4 volte più dura del cromo; resistente ai graffi e durevole. |
Adesione | Aderisce fortemente ai substrati, aumentando la durata fino a 10 volte. |
Prestazioni nei test | Supera le 1200 ore di test in nebbia salina neutra e le 150 ore di test CASS. |
Applicazioni | Adatto per ambienti marini, costieri e altri ambienti corrosivi. |
Processo | Rivestimenti puri, privi di impurità, ottenuti mediante vaporizzazione sotto vuoto, che garantiscono la durata nel tempo. |
Migliorate la durata del vostro progetto con i rivestimenti PVD. contattate i nostri esperti oggi stesso !