Per aumentare l'efficienza di un mulino a sfere, è necessario ottimizzare diversi fattori, tra cui la macinabilità del materiale, la dimensione e la proporzione dei mezzi di macinazione, il tasso di riempimento del mulino e i parametri operativi come la velocità di rotazione e la densità di macinazione.Intervenendo su questi fattori, il processo di macinazione può essere reso più efficiente, con conseguente aumento della produttività e riduzione del consumo energetico.Le strategie chiave includono la regolazione delle dimensioni dell'alimentazione, l'ottimizzazione delle dimensioni delle sfere d'acciaio e del tasso di riempimento, il mantenimento di una densità di macinazione appropriata e la garanzia di una progettazione e di condizioni operative adeguate del mulino.
Punti chiave spiegati:
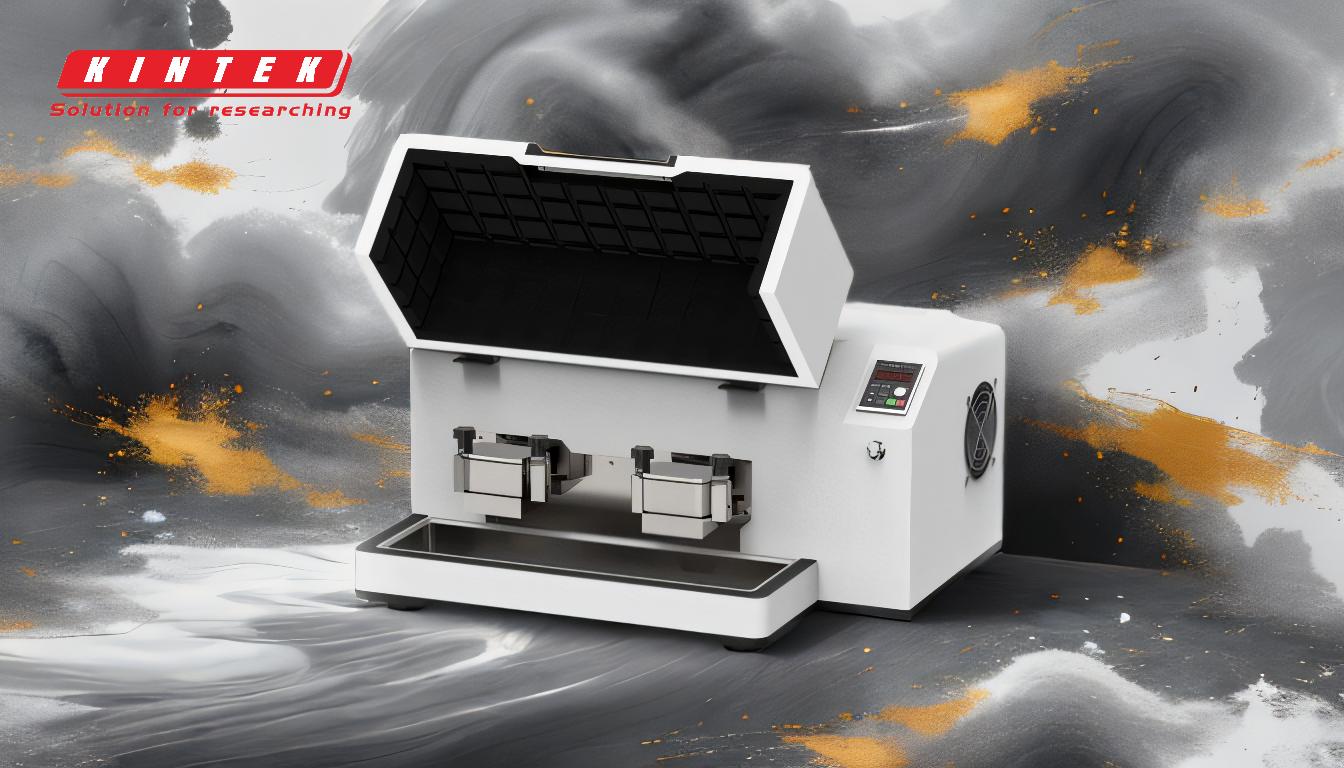
-
Modificare la macinabilità originale
- La macinabilità si riferisce alla facilità con cui un materiale può essere macinato.Alcuni materiali si macinano naturalmente in modo più efficiente di altri.Pretrattando o alterando il materiale (ad esempio, attraverso processi chimici o termici), è possibile migliorarne la macinabilità, ottenendo una macinazione più efficiente.
-
Più frantumazione e meno macinazione
- La riduzione delle dimensioni del materiale in ingresso al mulino a sfere può migliorare significativamente l'efficienza.Le particelle più grandi richiedono più energia per la macinazione, quindi la pre-frantumazione del materiale in dimensioni più piccole riduce il carico di lavoro del mulino e aumenta la produttività.
-
Tasso di riempimento ragionevole delle sfere d'acciaio
- Il tasso di riempimento delle sfere d'acciaio (la percentuale del volume del mulino occupata dai mezzi di macinazione) deve essere ottimizzato.Un numero insufficiente di sfere riduce l'efficienza di macinazione, mentre un numero eccessivo può portare a un consumo energetico e a un'usura eccessivi.Un tasso di riempimento di circa il 30-40% è spesso ottimale.
-
Dimensioni e proporzioni ragionevoli delle sfere d'acciaio
- Le dimensioni e la proporzione delle sfere d'acciaio hanno un impatto diretto sull'efficienza di macinazione.Le sfere più grandi sono migliori per la macinazione grossolana, mentre quelle più piccole sono più efficaci per la macinazione fine.Un mix bilanciato di dimensioni delle sfere garantisce una macinazione efficiente per le diverse dimensioni delle particelle.
-
Ricarica accurata delle sfere d'acciaio
- Con il tempo, le sfere d'acciaio si consumano e devono essere sostituite.Riempire regolarmente il mulino con sfere di dimensioni e proporzioni corrette garantisce prestazioni di macinazione costanti e previene le inefficienze causate da sfere usurate o mancanti.
-
Densità di macinazione adeguata
- La densità di macinazione (la concentrazione di materiale solido nel fango) influisce sull'efficienza del processo di macinazione.Una densità troppo elevata può causare intasamenti, mentre una densità troppo bassa riduce l'impatto dei mezzi di macinazione.Il mantenimento di una densità ottimale garantisce una macinazione efficiente e previene i problemi operativi.
-
Ottimizzare il design del mulino (rapporto L:D)
- Il rapporto lunghezza/diametro (L:D) del mulino è fondamentale per l'efficienza.Un rapporto L:D ottimale (in genere 1,56-1,64) garantisce un flusso di materiale e un'azione di macinazione adeguati, massimizzando la produttività.
-
Controllo della velocità di rotazione
- La velocità di rotazione del mulino influisce sull'azione di macinazione.Una velocità troppo bassa riduce l'impatto dei mezzi di macinazione, mentre una velocità troppo alta può causare la centrifugazione delle sfere, riducendo l'efficienza della macinazione.La velocità critica (la velocità alla quale le sfere iniziano a centrifugare) deve essere gestita con attenzione.
-
Monitoraggio della velocità e del livello di alimentazione
- La velocità e il livello di alimentazione del mulino devono essere controllati per garantire una macinazione uniforme.Un sovraccarico del mulino può ridurre l'efficienza, mentre un sottocarico può portare a una macinazione non uniforme e a un aumento dell'usura.
-
Rimozione tempestiva del prodotto macinato
- La rimozione tempestiva del materiale macinato evita la macinazione eccessiva e riduce il consumo energetico.Meccanismi di scarico efficienti e un'adeguata progettazione del mulino sono essenziali per mantenere la produttività.
Affrontando questi fattori, l'efficienza di un mulino a sfere può essere significativamente migliorata, portando a migliori prestazioni di macinazione, a un consumo energetico ridotto e a costi operativi inferiori.
Tabella riassuntiva:
Fattore chiave | Strategia di ottimizzazione |
---|---|
Macinabilità | Pretrattare i materiali per migliorare la macinabilità attraverso processi chimici o termici. |
Dimensione dell'alimentazione | Ridurre le dimensioni dell'alimentazione attraverso la pre-frantumazione per migliorare l'efficienza di macinazione. |
Tasso di riempimento delle sfere d'acciaio | Mantenere un tasso di riempimento del 30-40% per un'efficienza di macinazione ottimale. |
Dimensioni e proporzioni delle sfere d'acciaio | Utilizzare un mix equilibrato di dimensioni delle sfere per la macinazione grossolana e fine. |
Ricarica delle sfere d'acciaio | Sostituire regolarmente le sfere usurate per mantenere costanti le prestazioni di macinazione. |
Densità di macinazione | Mantenere la densità ottimale dello slurry per evitare intasamenti o riduzione dell'impatto di macinazione. |
Progettazione del mulino (rapporto L:D) | Ottimizzare il rapporto lunghezza/diametro (1,56-1,64) per ottenere un flusso di materiale e una macinazione adeguati. |
Velocità di rotazione | Controllare la velocità per evitare la centrifugazione e garantire un'azione di macinazione efficace. |
Velocità e livello di alimentazione | Monitorare la velocità di avanzamento per evitare di sovraccaricare o sottocaricare il mulino. |
Rimozione del prodotto macinato | Rimuovere tempestivamente il materiale macinato per evitare la macinazione eccessiva e lo spreco di energia. |
Siete pronti a ottimizzare l'efficienza del vostro mulino a sfere? Contattate i nostri esperti oggi stesso per soluzioni su misura!