I rivestimenti PVD (Physical Vapor Deposition) sono rinomati per la loro eccezionale durata e resistenza all'usura, alla corrosione e alle scheggiature.Questi rivestimenti si legano a livello molecolare con il substrato, creando uno strato forte e sottile altamente resistente alle forze esterne.Grazie alla loro durezza, alla resistenza all'usura e alle proprietà di basso attrito, i rivestimenti PVD hanno minori probabilità di scheggiarsi rispetto ai rivestimenti tradizionali.La loro capacità di resistere ad ambienti difficili, comprese le alte temperature e le condizioni corrosive, ne aumenta ulteriormente la durata.Anche se nessun rivestimento è del tutto immune da danni, i rivestimenti PVD sono tra le opzioni più durevoli disponibili, il che li rende ideali per le applicazioni più impegnative in settori come quello automobilistico, aerospaziale e medico.
Punti chiave spiegati:
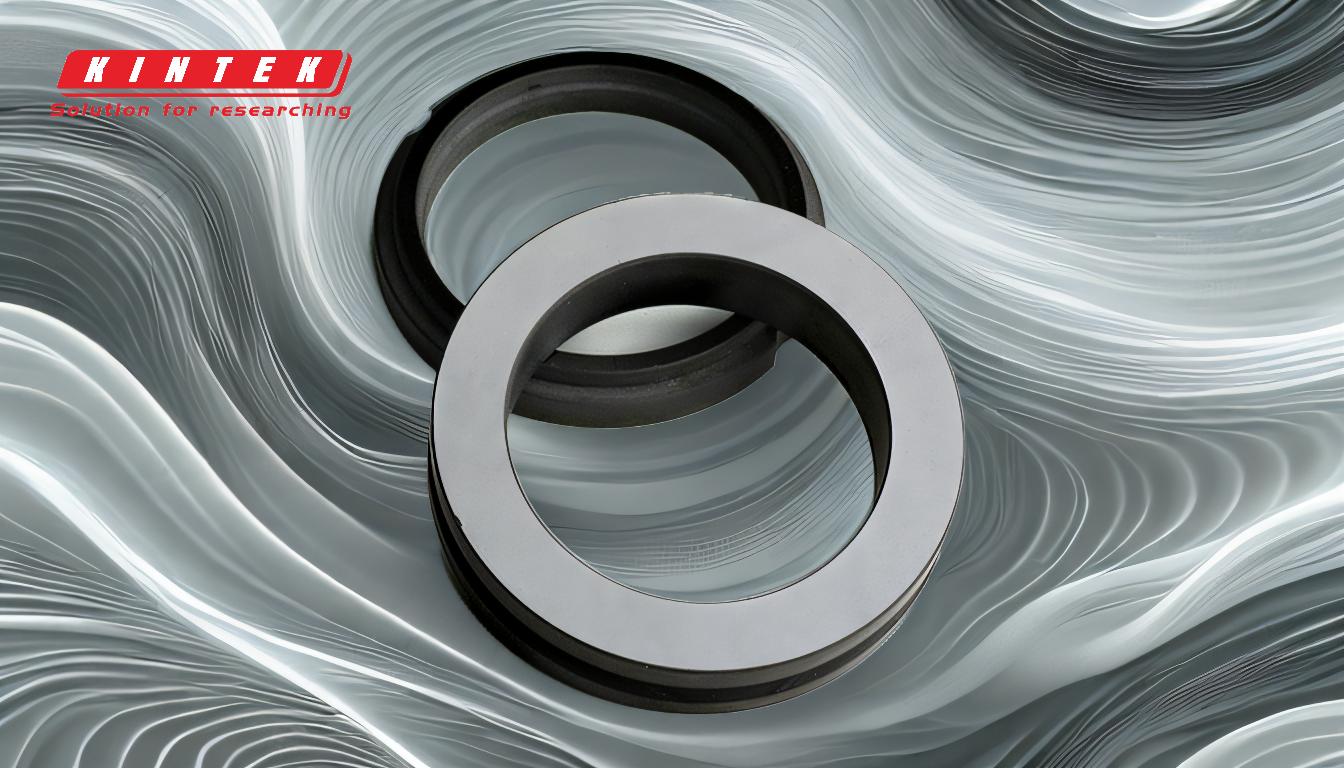
-
Legame molecolare e adesione
- I rivestimenti PVD formano un legame a livello molecolare con il substrato, creando una connessione forte e duratura.
- Questo meccanismo di legame assicura che il rivestimento aderisca saldamente alla superficie, rendendolo resistente alle scheggiature anche in caso di stress meccanico o di impatto.
-
Durezza e resistenza all'usura
- I rivestimenti PVD sono noti per la loro elevata durezza, spesso superiore a quella dei rivestimenti tradizionali.
- La durezza del rivestimento contribuisce alla sua capacità di resistere all'usura, all'abrasione e alla scheggiatura, anche in ambienti sottoposti a forti sollecitazioni.
-
Strato sottile e durevole
- I rivestimenti PVD sono estremamente sottili, in genere da 0,5 a 5 micron.
- Nonostante la loro sottigliezza, questi rivestimenti sono molto resistenti e difficili da rimuovere, riducendo ulteriormente la probabilità di scheggiature.
-
Resistenza alla corrosione e all'ossidazione
- L'ambiente sotto vuoto durante il processo PVD elimina la contaminazione e previene l'ossidazione, dando vita a un rivestimento altamente resistente alla corrosione e al degrado ambientale.
- Questa resistenza aumenta la durata e la longevità complessiva del rivestimento, riducendo il rischio di scheggiature nel tempo.
-
Applicazioni in settori esigenti
- I rivestimenti PVD sono ampiamente utilizzati in settori come quello automobilistico, aerospaziale e medico, dove la durata e la resistenza all'usura sono fondamentali.
- La loro capacità di resistere a condizioni difficili e a sollecitazioni meccaniche li rende meno inclini a scheggiarsi rispetto ad altri rivestimenti.
-
Confronto con i rivestimenti tradizionali
- A differenza delle finiture tradizionali, i rivestimenti PVD sono molto più duri e resistenti all'usura e alla corrosione.
- Grazie a questa durata superiore, è meno probabile che si scheggino, anche quando sono sottoposti a manipolazioni brusche o a condizioni estreme.
-
Prestazioni nel mondo reale
- È stato dimostrato che i rivestimenti PVD migliorano il limite di fatica e la resistenza dei materiali, come la lega Ti-6Al-4V, di percentuali significative.
- Questi miglioramenti delle prestazioni dimostrano ulteriormente la capacità del rivestimento di resistere ai danni, compresa la scheggiatura, in condizioni reali.
In sintesi, sebbene nessun rivestimento sia del tutto immune da danni, i rivestimenti PVD sono tra le opzioni più durevoli e resistenti alle scheggiature disponibili.Il loro legame molecolare, la durezza, la sottigliezza e la resistenza alla corrosione e all'usura li rendono una scelta eccellente per le applicazioni in cui la durata e la longevità sono fondamentali.
Tabella riassuntiva:
Caratteristica chiave | Descrizione |
---|---|
Legame molecolare | Forma un forte legame a livello molecolare con il substrato, riducendo i rischi di scheggiatura. |
Durezza e resistenza all'usura | Supera i rivestimenti tradizionali, offrendo una resistenza superiore all'usura e all'abrasione. |
Strato sottile e resistente | Estremamente sottile (0,5-5 micron) ma altamente resistente, riduce al minimo le scheggiature. |
Resistenza alla corrosione | Resiste alla corrosione e all'ossidazione, aumentando la longevità in ambienti difficili. |
Applicazioni industriali | Ampiamente utilizzato nei settori automobilistico, aerospaziale e medicale per la sua durata e le sue prestazioni. |
Prestazioni nel mondo reale | Migliora i limiti di fatica e la resistenza, riducendo i danni in condizioni estreme. |
Volete migliorare la durata dei vostri materiali con i rivestimenti PVD? Contattateci oggi per saperne di più!