CVD (Chemical Vapor Deposition) e PVD (Physical Vapor Deposition) sono due tecniche di rivestimento ampiamente utilizzate per gli inserti, ciascuna con processi, proprietà e applicazioni distinti. La CVD prevede reazioni chimiche ad alte temperature (800–1000 °C) per depositare rivestimenti più spessi (10–20 μm), mentre il PVD utilizza la vaporizzazione fisica a temperature più basse (250–500 °C) per creare pellicole più sottili e ultra-dure (3 –5 µm). I rivestimenti CVD sono più densi e più uniformi ma possono introdurre stress da trazione e crepe sottili a causa delle elevate temperature di lavorazione. I rivestimenti PVD, d'altro canto, formano sollecitazioni di compressione e sono ideali per applicazioni di precisione che richiedono superfici lisce e durevoli. La scelta tra CVD e PVD dipende da fattori quali lo spessore del rivestimento, la temperatura operativa e i requisiti applicativi specifici.
Punti chiave spiegati:
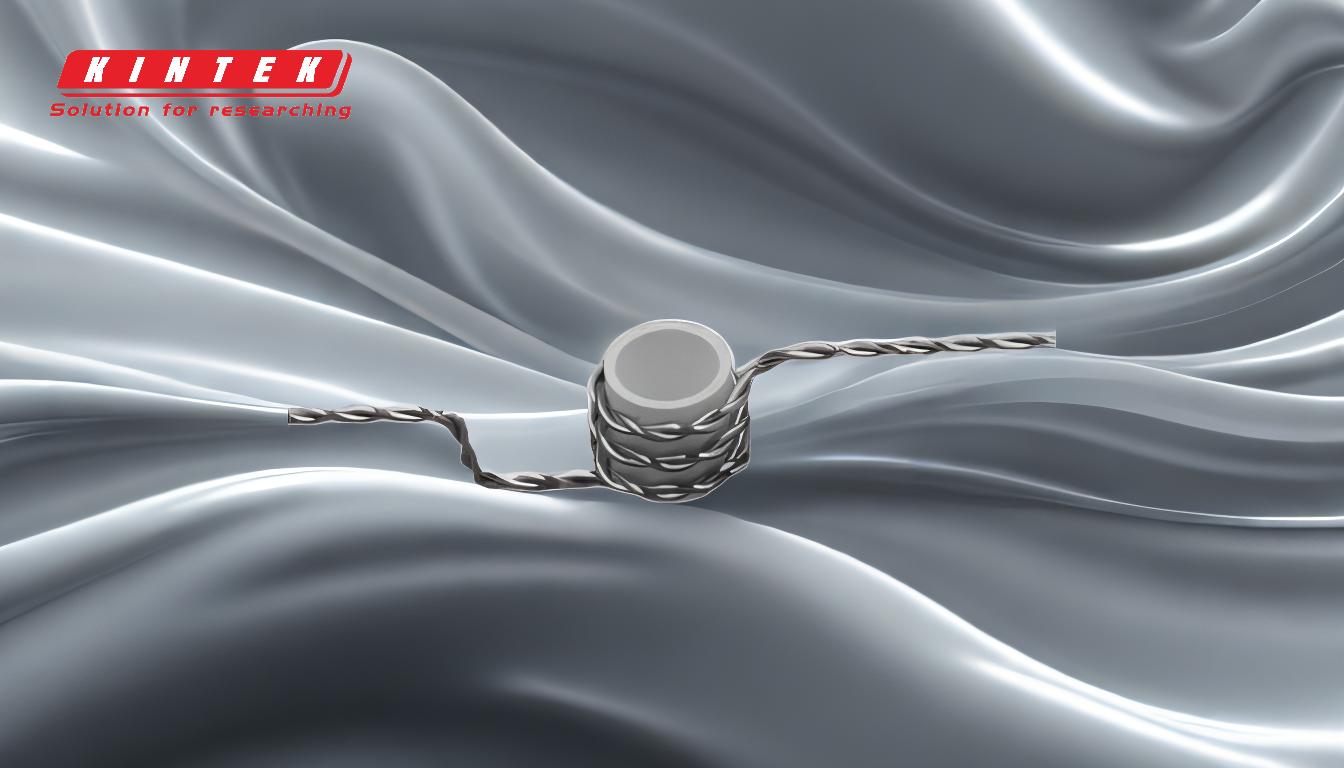
-
Meccanismo di deposizione:
- CVD: Coinvolge reazioni chimiche tra precursori gassosi e il substrato ad alte temperature (800–1000 ° C). Ciò si traduce in una deposizione multidirezionale, in cui il rivestimento si forma uniformemente su tutte le superfici, comprese le geometrie complesse.
- PVD: Utilizza un processo fisico, come lo sputtering o l'evaporazione, per depositare il materiale direttamente sul substrato in modo visivo. Ciò limita la copertura alle superfici esposte ma consente un controllo preciso sulle proprietà della pellicola.
-
Temperatura operativa:
- CVD: Richiede temperature elevate (800–1000 °C), che possono influire sulle proprietà meccaniche del substrato e provocare sollecitazioni di trazione o sottili crepe nel rivestimento.
- PVD: Funziona a temperature più basse (250–500 °C), rendendolo adatto a materiali sensibili al calore e riducendo il rischio di deformazione del substrato.
-
Spessore e uniformità del rivestimento:
- CVD: Produce rivestimenti più spessi (10–20 μm) con eccellente uniformità, rendendolo ideale per applicazioni che richiedono elevata resistenza all'usura e durata.
- PVD: Forma rivestimenti più sottili (3–5 μm) con levigatezza e precisione superiori, adatti per applicazioni che richiedono finiture superficiali fini e variazioni dimensionali minime.
-
Stress e adesione:
- CVD: Temperature di lavorazione elevate possono portare a sollecitazioni di trazione nel rivestimento, che in alcuni casi possono causare microfessure e ridotta adesione.
- PVD: Genera stress da compressione durante il raffreddamento, migliorando l'adesione e la durata del rivestimento, soprattutto nelle applicazioni ad alta precisione.
-
Compatibilità dei materiali:
- CVD: Utilizzato principalmente per ceramiche e polimeri, offre eccellente resistenza chimica e stabilità termica.
- PVD: Può depositare una gamma più ampia di materiali, inclusi metalli, leghe e ceramiche, offrendo maggiore versatilità per varie applicazioni.
-
Applicazioni:
- CVD: Comunemente utilizzato nelle industrie che richiedono rivestimenti spessi e resistenti all'usura, come utensili da taglio, componenti aerospaziali e produzione di semiconduttori.
- PVD: Preferito per applicazioni che richiedono rivestimenti sottili, lisci e precisi, come dispositivi medici, componenti ottici e finiture decorative.
-
Costo e tempo di elaborazione:
- CVD: Generalmente più costoso e dispendioso in termini di tempo a causa delle alte temperature e dei complessi processi chimici coinvolti.
- PVD: Offre tempi di lavorazione più rapidi e costi inferiori, rendendolo più economico per la produzione di volumi elevati.
In sintesi, la scelta tra inserti di rivestimento CVD e PVD dipende dai requisiti specifici dell'applicazione, inclusi spessore del rivestimento, temperatura operativa, compatibilità dei materiali e proprietà superficiali desiderate. Il CVD è ideale per rivestimenti spessi e uniformi in ambienti ad alta temperatura, mentre il PVD eccelle nelle applicazioni di precisione che richiedono superfici lisce e durevoli a temperature più basse.
Tabella riassuntiva:
Aspetto | CVD | PVD |
---|---|---|
Meccanismo di deposizione | Reazioni chimiche ad alta temperatura (800–1000 °C), multidirezionali | Vaporizzazione fisica a temperature più basse (250–500 °C), in linea visiva |
Spessore del rivestimento | Più spesso (10–20 μm), uniforme | Più sottile (3–5 μm), ultra duro e liscio |
Temperatura operativa | Elevato (800–1000 ° C), può causare stress da trazione | Basso (250–500 °C), riduce la deformazione del substrato |
Stress e adesione | Sollecitazione di trazione, potenziali microfessurazioni | Sollecitazione di compressione, adesione migliorata |
Compatibilità dei materiali | Ceramiche, polimeri, elevata resistenza chimica | Metalli, leghe, ceramiche, versatili |
Applicazioni | Utensili da taglio, aerospaziale, semiconduttori | Dispositivi medici, ottica, finiture decorative |
Costo ed elaborazione | Costoso, richiede tempo | Elaborazione economica e più rapida |
Hai bisogno di aiuto nella scelta tra CVD e PVD per la tua applicazione? Contatta i nostri esperti oggi stesso per una consulenza personalizzata!