La progettazione del mulino a sfere è un aspetto critico per ottenere prestazioni di macinazione ottimali e coinvolge diversi parametri chiave che influenzano la produttività e l'efficienza.Questi parametri includono il diametro del tamburo, il rapporto tra diametro e lunghezza del tamburo (rapporto L:D), le proprietà fisico-chimiche del materiale di alimentazione, il riempimento e le dimensioni delle sfere, la forma della superficie della corazza, la velocità di rotazione, la finezza di macinazione e la rimozione tempestiva del prodotto macinato.Inoltre, fattori quali le dimensioni e il tipo di mezzo di macinazione, il rapporto di riempimento del mulino, il tempo di residenza e il carico di solidi svolgono un ruolo significativo nel determinare l'efficacia del processo di macinazione.La comprensione e l'ottimizzazione di questi parametri sono essenziali per progettare un mulino a sfere che soddisfi i requisiti specifici di macinazione.
Punti chiave spiegati:
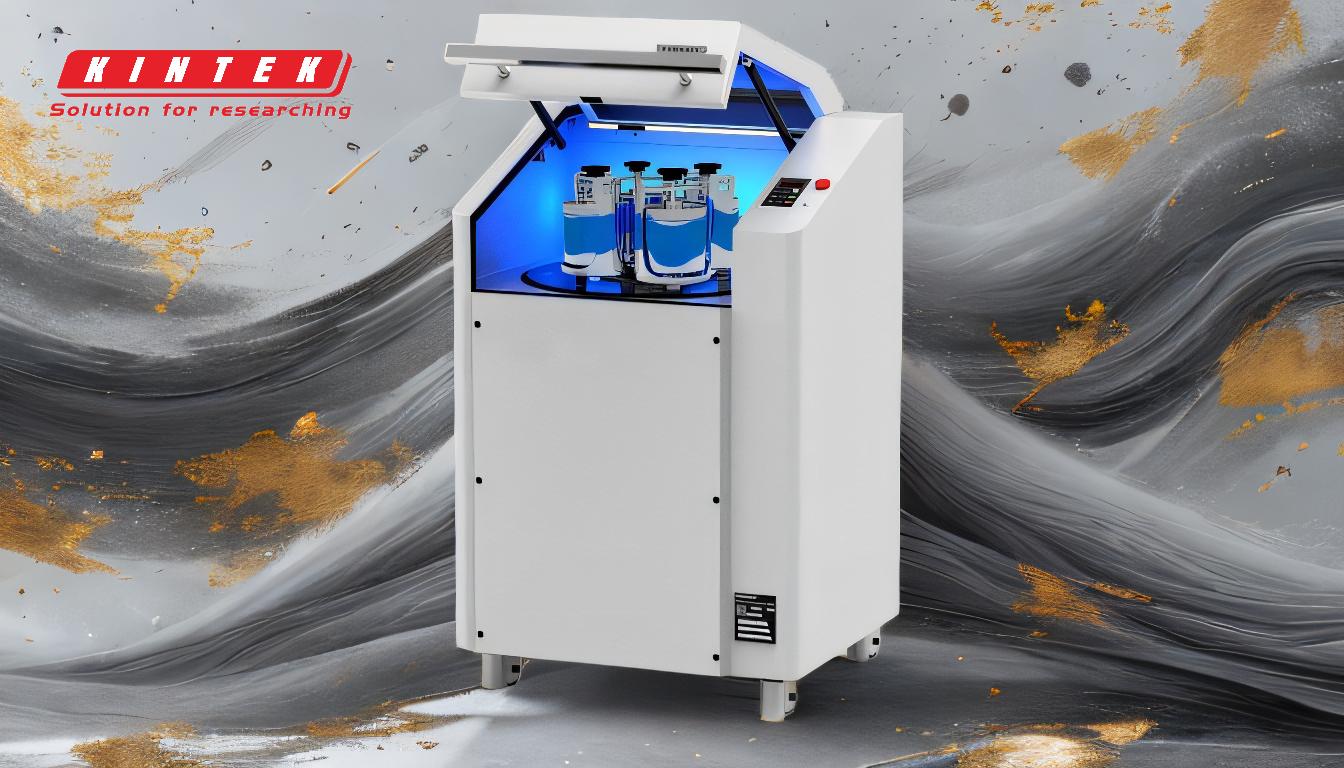
-
Diametro del tamburo e rapporto lunghezza/diametro (rapporto L:D):
- Il diametro del tamburo è un parametro fondamentale nella progettazione dei mulini a sfere, in quanto influenza direttamente la capacità e l'efficienza di macinazione del mulino.Un diametro maggiore del tamburo consente generalmente una maggiore produttività.
- Il rapporto L:D è fondamentale per determinare le condizioni ottimali di macinazione.Le ricerche suggeriscono che un rapporto L:D di 1,56-1,64 è ideale per ottenere una macinazione efficiente.Questo rapporto garantisce un equilibrio tra la superficie di macinazione e il volume del materiale da lavorare.
-
Proprietà fisico-chimiche del materiale in entrata:
- La natura del materiale da macinare, compresa la sua durezza, densità e composizione chimica, influisce in modo significativo sul processo di macinazione.Ad esempio, i materiali più duri possono richiedere mezzi di macinazione più grandi o più densi per raggiungere la finezza desiderata.
- Anche le proprietà del materiale di alimentazione influenzano la scelta dei mezzi di macinazione e le condizioni operative del mulino.
-
Riempimento e dimensioni delle sfere:
- Il rapporto di riempimento delle sfere (la percentuale del volume del mulino riempita con il materiale di macinazione) è un fattore critico nel determinare l'efficienza di macinazione.Un riempimento eccessivo o insufficiente del mulino può portare a prestazioni di macinazione non ottimali.
- Anche la dimensione delle sfere di macinazione è importante.Le sfere più grandi sono più efficaci per la macinazione grossolana, mentre quelle più piccole sono più adatte per la macinazione fine.La scelta delle dimensioni delle sfere deve basarsi sulla finezza desiderata del prodotto macinato.
-
Forma della superficie dell'armatura:
- La forma e il design dell'armatura interna del mulino (rivestimenti) possono influire sul processo di macinazione, influenzando il movimento dei mezzi di macinazione e del materiale macinato.I rivestimenti lisci possono favorire un movimento a cascata, mentre le barre di sollevamento possono migliorare l'impatto e l'azione di macinazione.
-
Velocità di rotazione:
- La velocità di rotazione velocità di rotazione del mulino è un parametro chiave che determina il movimento dei mezzi di macinazione e del materiale all'interno del mulino.La velocità di rotazione ottimale dipende dal diametro del mulino e dall'azione di macinazione desiderata.Una velocità troppo elevata può portare a un'usura eccessiva, mentre una velocità troppo bassa può causare una macinazione insufficiente.
-
Finezza di macinazione e rimozione tempestiva del prodotto macinato:
- La finezza desiderata del prodotto macinato è un fattore critico nella progettazione del mulino a sfere.Il raggiungimento della finezza richiesta spesso comporta la regolazione di parametri quali la dimensione della sfera, la velocità di rotazione e il tempo di permanenza.
- La rimozione tempestiva del prodotto macinato è essenziale per evitare una macinazione eccessiva e per mantenere costante la qualità del prodotto.Questo obiettivo può essere raggiunto attraverso una corretta progettazione del sistema di scarico.
-
Tempo di residenza e velocità di alimentazione:
- Il tempo di permanenza del materiale nella camera del mulino è un fattore importante che influenza il grado di macinazione.Tempi di permanenza più lunghi comportano generalmente una macinazione più fine, ma possono anche comportare un maggiore consumo energetico.
- La velocità di alimentazione e il livello di materiale nel mulino devono essere attentamente controllati per garantire prestazioni di macinazione costanti.Il sovraccarico del mulino può ridurre l'efficienza di macinazione, mentre il sottocarico può portare a un'usura eccessiva dei mezzi di macinazione.
-
Carico di solidi:
- Il carico di solidi (la percentuale di solidi nel liquame) è un altro parametro critico nella progettazione dei mulini a sfere, in particolare per le operazioni di macinazione a umido.Un carico ottimale di solidi garantisce una macinazione efficiente, riducendo al minimo il consumo energetico.
-
Variabili indipendenti nella macinazione a secco:
- Nelle operazioni di macinazione a secco, le principali variabili indipendenti comprendono diametro del mulino, velocità del mulino, dimensione del materiale, carico di solidi e tempo di permanenza. .Queste variabili devono essere attentamente controllate per ottenere le prestazioni di macinazione desiderate.
-
Mezzo di macinazione:
- Il tipo e le dimensioni del mezzo di macinazione (sfere) sono fattori critici nella progettazione del mulino a sfere.La densità, la durezza e la distribuzione dimensionale del mezzo di macinazione devono essere selezionate in base al materiale da macinare e alla finezza desiderata del prodotto.
Considerando attentamente e ottimizzando questi parametri, gli ingegneri possono progettare mulini a sfere che raggiungono le prestazioni di macinazione desiderate, riducendo al minimo il consumo energetico e l'usura.Ogni parametro svolge un ruolo unico nel processo di macinazione e le sue interazioni devono essere comprese a fondo per garantire una progettazione ottimale del mulino.
Tabella riassuntiva:
Parametro | Descrizione | Valore ottimale/Considerazione |
---|---|---|
Diametro del tamburo | Influenza la capacità del mulino e l'efficienza di macinazione. | Un diametro maggiore aumenta la produttività. |
Rapporto L:D | Bilancia la superficie di macinazione e il volume del materiale. | 1,56-1,64 per una macinazione efficiente. |
Proprietà del materiale di alimentazione | La durezza, la densità e la composizione chimica influiscono sulla macinazione. | I materiali più duri richiedono mezzi di macinazione più densi. |
Rapporto di riempimento delle sfere | Percentuale del volume del mulino riempita con i mezzi di macinazione. | Evitare il riempimento eccessivo o insufficiente. |
Dimensioni delle sfere | Sfere più grandi per la macinazione grossolana, più piccole per la macinazione fine. | Abbinare le dimensioni delle sfere alla finezza desiderata. |
Forma della superficie della corazza | Influenza il movimento dei mezzi di macinazione e del materiale. | Lamiere lisce o barre di sollevamento per azioni specifiche. |
Velocità di rotazione | Determina il movimento del materiale di macinazione e l'azione di macinazione. | Regolare in base al diametro del mulino e alla produzione desiderata. |
Finezza di macinazione | Finezza desiderata del prodotto macinato. | Regolare la dimensione della sfera, la velocità e il tempo di permanenza. |
Tempo di residenza | Tempo che il materiale trascorre nella camera del mulino. | Tempo più lungo per una macinazione più fine, ma energia più elevata. |
Carico di solidi | Percentuale di solidi nel liquame (macinazione a umido). | Il carico ottimale riduce al minimo il consumo di energia. |
Mezzo di macinazione | Tipo e dimensioni delle sfere di macinazione. | Adattare la densità e la durezza al materiale. |
Ottimizzate il progetto del vostro mulino a sfere per ottenere la massima efficienza. contattate i nostri esperti oggi stesso !