La dimensione del prodotto in un mulino a sfere è influenzata da diversi fattori, tra cui la dimensione e la densità delle sfere di macinazione, la durata della macinazione, le proprietà fisiche e chimiche del materiale di alimentazione, la velocità di rotazione del mulino, la velocità di alimentazione e il design del mulino stesso (come il rapporto tra diametro e lunghezza del tamburo).Le sfere più piccole e i tempi di macinazione più lunghi producono in genere particelle più fini, mentre la durezza e la natura del materiale da macinare svolgono un ruolo significativo.Inoltre, l'efficienza del processo di macinazione può essere influenzata dalla rimozione tempestiva del prodotto macinato e dalla forma della superficie di armatura del mulino.
Punti chiave spiegati:
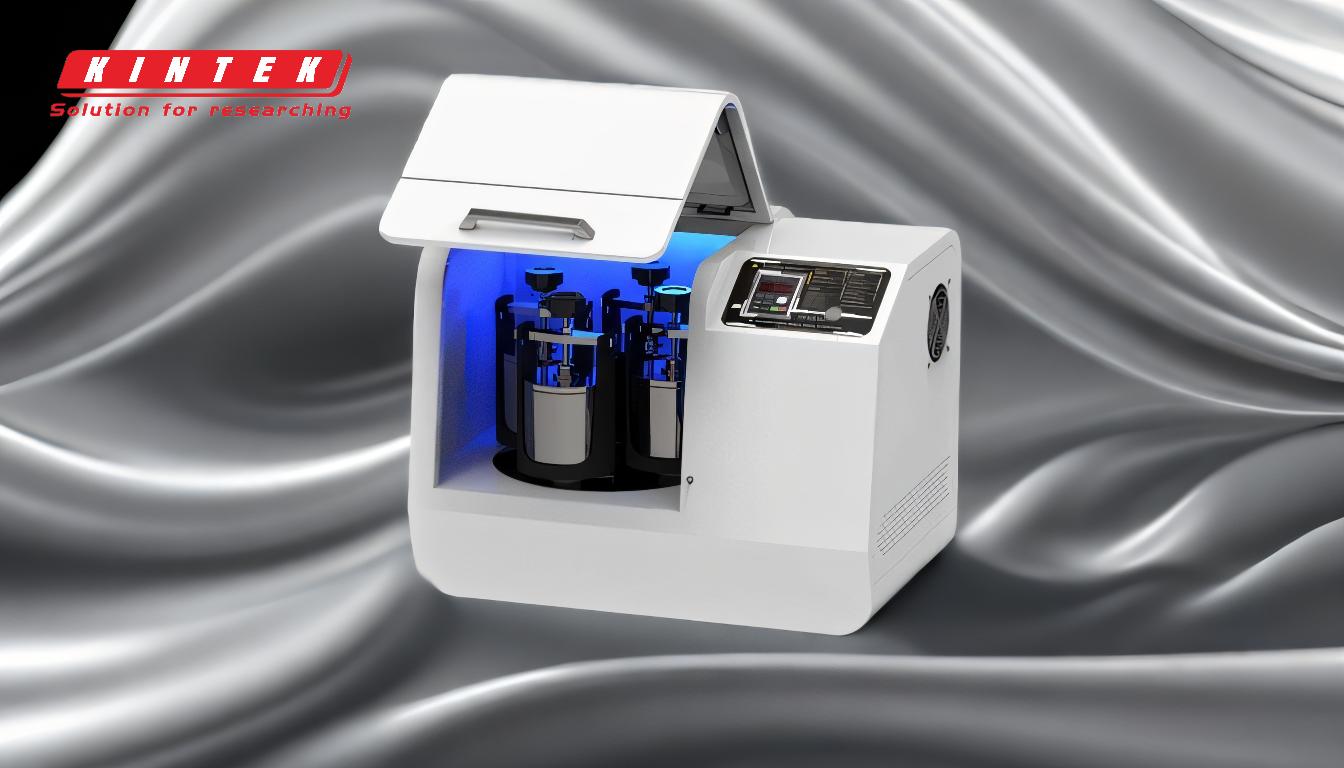
-
Dimensione e densità delle sfere di macinazione:
- Palline più piccole:Le sfere di macinazione più piccole sono più efficaci nel produrre particelle più fini perché hanno una superficie maggiore rispetto al loro volume, consentendo un maggior numero di punti di contatto con il materiale da macinare.
- Densità:Le sfere a densità più elevata possono imprimere una maggiore energia al materiale, con conseguente macinazione più efficace.Tuttavia, le dimensioni e la densità ottimali dipendono dal materiale da lavorare.
-
Tempo di macinazione:
- Tempi di macinazione più lunghi:Il prolungamento del tempo di macinazione consente un maggior numero di collisioni tra le sfere e il materiale, che in genere si traduce in particelle di dimensioni inferiori.Tuttavia, esiste un punto di diminuzione dei rendimenti in cui un'ulteriore macinazione non può ridurre significativamente le dimensioni delle particelle.
-
Proprietà fisiche e chimiche del materiale di alimentazione:
- Durezza:I materiali più duri richiedono più energia per la macinazione e possono richiedere sfere di dimensioni diverse o tempi di macinazione più lunghi.
- Natura del materiale:La fragilità, il contenuto di umidità e altre proprietà del materiale di alimentazione possono influenzare la facilità di macinazione.
-
Velocità di rotazione del mulino:
- Velocità ottimale:La velocità di rotazione del mulino deve essere attentamente controllata.Se la velocità è troppo bassa, le sfere potrebbero non lavorare a cascata in modo efficace, riducendo l'efficienza della macinazione.Se la velocità è troppo alta, le sfere possono centrifugare, riducendo l'efficienza.
-
Velocità di alimentazione e livello nel recipiente:
- Velocità di avanzamento:Una velocità di alimentazione costante e adeguata garantisce che il mulino non venga sovraccaricato, riducendo l'efficienza di macinazione.
- Livello del materiale:Il livello di materiale nel mulino influisce sull'azione di macinazione.Troppo materiale può attutire l'impatto delle sfere, mentre troppo poco può portare a una macinazione inefficiente.
-
Design del mulino:
- Diametro e lunghezza del tamburo:Il rapporto ottimale tra il diametro e la lunghezza del tamburo (rapporto L:D) è in genere compreso tra 1,56 e 1,64.Questo rapporto influisce sul tempo di permanenza del materiale nel mulino e sull'efficienza del processo di macinazione.
- Forma della superficie della corazza:La forma della superficie interna del mulino può influenzare il movimento delle sfere e del materiale, incidendo sull'efficienza di macinazione.
-
Rimozione tempestiva del prodotto macinato:
- Efficienza:La rimozione tempestiva del prodotto macinato impedisce una macinazione eccessiva e garantisce un funzionamento efficiente del mulino.Una macinazione eccessiva può comportare uno spreco di energia e può degradare la qualità del prodotto finale.
-
Tempo di permanenza:
- Tempo di permanenza del materiale:Il tempo di permanenza del materiale nella camera del mulino influisce direttamente sul grado di macinazione.Tempi di permanenza più lunghi portano generalmente a particelle più fini, ma devono essere bilanciati con altri fattori per evitare inefficienze.
Controllando attentamente questi fattori, gli operatori possono ottimizzare il processo di macinazione a sfere per ottenere la distribuzione granulometrica desiderata per la loro specifica applicazione.
Tabella riassuntiva:
Fattore | Impatto sulla dimensione delle particelle |
---|---|
Dimensione e densità delle sfere di macinazione | Le sfere più piccole e la densità più elevata producono particelle più fini. |
Tempo di macinazione | Tempi di macinazione più lunghi riducono le dimensioni delle particelle, ma possono avere un rendimento decrescente. |
Proprietà del materiale di alimentazione | I materiali più duri o fragili richiedono più energia e tempo per la macinazione. |
Velocità di rotazione | La velocità ottimale garantisce una macinazione efficiente; una velocità troppo bassa o troppo alta riduce l'efficacia. |
Velocità di avanzamento e livello del materiale | Una velocità di avanzamento costante e un livello di materiale adeguato migliorano l'efficienza di macinazione. |
Design del mulino | Il rapporto diametro-lunghezza del tamburo (1,56-1,64) e la forma della superficie della corazza influiscono sull'efficienza di macinazione. |
Rimozione tempestiva del prodotto | Previene la macinazione eccessiva e mantiene l'efficienza. |
Tempo di residenza | Tempi di residenza più lunghi producono particelle più fini, ma devono essere bilanciati per garantire l'efficienza. |
Ottimizzate il vostro processo di macinazione a sfere per ottenere risultati superiori. contattate i nostri esperti oggi stesso !