Le prestazioni di un mulino a sfere sono influenzate da una serie di fattori, tra cui le dimensioni fisiche del mulino, le proprietà del materiale da macinare, le caratteristiche dei mezzi di macinazione e i parametri operativi.I fattori chiave includono il diametro del tamburo e il suo rapporto con la lunghezza, le proprietà fisico-chimiche del materiale di alimentazione, le dimensioni e il rapporto di riempimento delle sfere di macinazione, la forma della superficie di armatura, la velocità di rotazione, la finezza desiderata del prodotto macinato e l'efficienza della rimozione del prodotto.Inoltre, anche il tempo di permanenza del materiale nel mulino, la durezza del materiale da macinare e la velocità di alimentazione giocano un ruolo importante nel determinare l'efficienza di macinazione complessiva e la produttività del mulino a sfere.
Punti chiave spiegati:
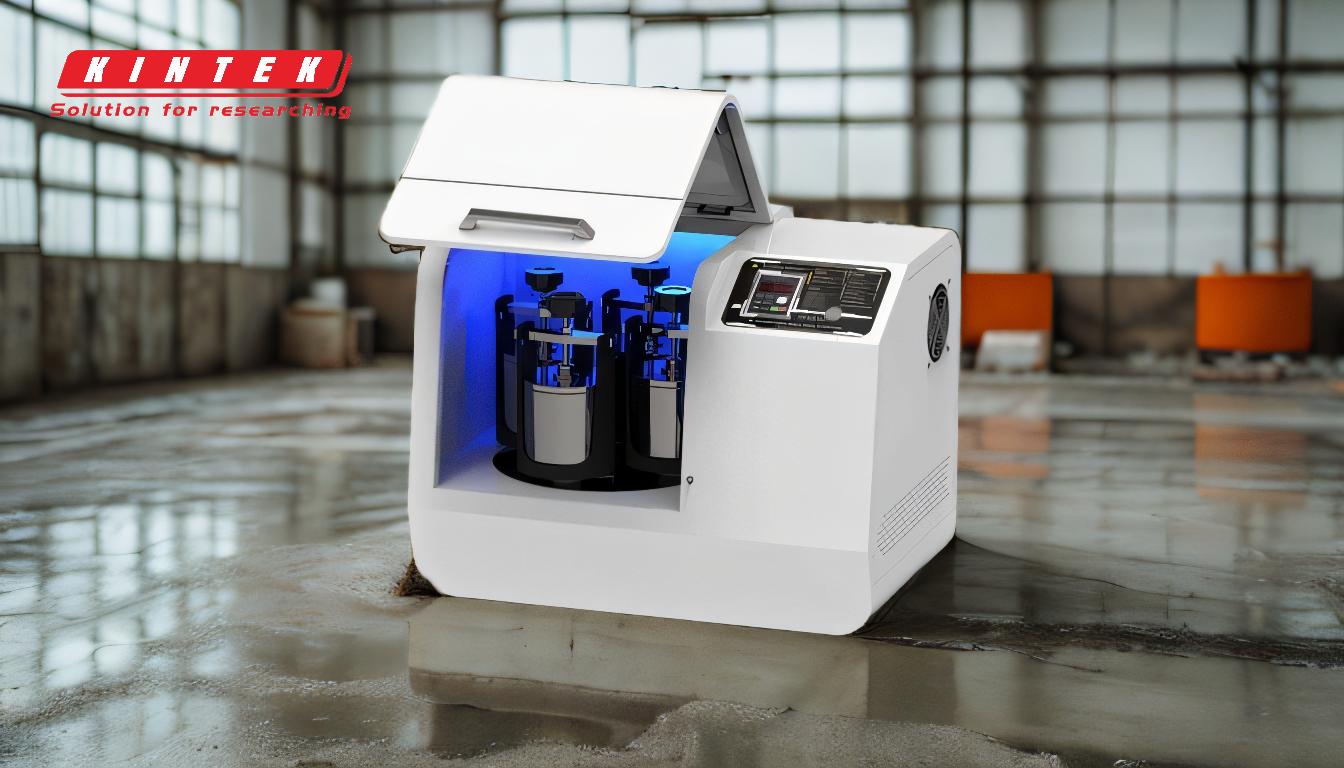
-
Dimensioni e struttura del tamburo:
- Diametro del tamburo e rapporto di lunghezza (rapporto L:D): Il diametro del tamburo e il rapporto tra lunghezza e diametro (rapporto L:D) sono fondamentali per ottenere prestazioni ottimali.Un rapporto L:D ottimale è in genere compreso tra 1,56 e 1,64.Questo rapporto garantisce una macinazione efficiente, bilanciando il tempo di permanenza del materiale e l'apporto di energia.
- Forma della superficie della corazza: La forma della superficie interna della corazza può influenzare la traiettoria delle sfere di macinazione e del materiale, incidendo sull'efficienza della macinazione.Una superficie ben progettata può migliorare l'azione di macinazione ottimizzando le forze di impatto e di abrasione.
-
Proprietà del materiale:
- Proprietà fisico-chimiche del materiale di alimentazione: La durezza, la densità e la composizione chimica del materiale da macinare influenzano in modo significativo il processo di macinazione.I materiali più duri richiedono più energia e tempo per la macinazione, mentre i materiali con proprietà chimiche specifiche possono reagire in modo diverso alle condizioni di macinazione.
- Natura del materiale da macinare: Anche la natura del materiale, come la sua fragilità o tenacità, svolge un ruolo importante.I materiali fragili tendono a rompersi più facilmente, mentre quelli più tenaci possono richiedere una macinazione più intensa.
-
Caratteristiche dei materiali di macinazione:
- Dimensioni delle sfere e rapporto di riempimento: Le dimensioni delle sfere di macinazione e la percentuale del volume del mulino riempito da queste sfere (rapporto di riempimento) sono fondamentali.Le sfere più grandi possono fornire una maggiore forza d'impatto e sono adatte alla macinazione grossolana, mentre quelle più piccole sono più adatte alla macinazione fine.Il rapporto di riempimento influisce sul trasferimento di energia e sull'efficienza di macinazione.
- Densità e numero di sfere: La densità e il numero di sfere influenzano la cinetica di macinazione.Le sfere a densità più elevata possono fornire una maggiore potenza di macinazione, mentre il numero di sfere influisce sulla frequenza degli impatti e sull'azione di macinazione complessiva.
-
Parametri operativi:
- Velocità di rotazione: La velocità di rotazione del mulino determina la forza centrifuga che agisce sulle sfere di macinazione e sul materiale.La velocità di rotazione ottimale garantisce che le sfere vengano sollevate alla giusta altezza prima di scendere a cascata, fornendo l'impatto necessario per la macinazione.
- Velocità di alimentazione e livello: La velocità di alimentazione del materiale nel mulino e il livello del materiale nel recipiente influiscono sull'efficienza della macinazione.Un sovraccarico del mulino può ridurre l'azione di macinazione, mentre un sottocarico può portare a un uso inefficiente dell'energia.
- Tempo di permanenza: Il tempo che il materiale trascorre nella camera del mulino influisce sul grado di macinazione.Tempi di permanenza più lunghi possono portare a una macinazione più fine, ma possono anche ridurre la produttività.
-
Rimozione del prodotto:
- Rimozione tempestiva del prodotto macinato: Una rimozione efficiente del prodotto macinato è essenziale per evitare una macinazione eccessiva e per mantenere un flusso costante di materiale attraverso il mulino.Meccanismi di scarico adeguati assicurano che il mulino operi alla capacità ottimale senza intasamenti o inutili consumi energetici.
-
Finezza di macinazione:
- Finezza desiderata del prodotto macinato: La finezza desiderata del prodotto influenza i parametri di macinazione.Per ottenere un prodotto più fine può essere necessario modificare le dimensioni delle sfere, la velocità di rotazione e il tempo di permanenza per garantire che il materiale venga macinato secondo le specifiche desiderate.
Considerando e ottimizzando attentamente questi fattori, le prestazioni di un mulino a sfere possono essere notevolmente migliorate, con conseguente aumento dell'efficienza di macinazione, della produttività e della qualità dei prodotti macinati.
Tabella riassuntiva:
Categoria | Fattori chiave |
---|---|
Dimensioni e design del tamburo |
- Diametro del tamburo e rapporto L:D (1,56-1,64 ottimale)
- Forma della superficie dell'armatura |
Proprietà del materiale |
- Durezza, densità, composizione chimica
- Fragilità o tenacità |
Mezzi di macinazione |
- Dimensione delle sfere e rapporto di riempimento
- Densità e numero di sfere |
Parametri operativi |
- Velocità di rotazione
- Velocità e livello di avanzamento - Tempo di permanenza |
Rimozione del prodotto | - Rimozione tempestiva del prodotto macinato |
Finezza di macinazione | - Finezza desiderata del prodotto macinato |
Siete pronti a ottimizzare le prestazioni del vostro mulino a sfere? Contattate i nostri esperti oggi stesso per soluzioni su misura!