La distribuzione granulometrica nella macinazione è influenzata da diversi fattori, tra cui le dimensioni e la densità delle sfere di macinazione, il tempo di macinazione, il numero di cicli di macinazione, il tempo di residenza, la velocità di alimentazione, la velocità di rotazione e la temperatura.Le sfere di macinazione più piccole e i tempi di macinazione più lunghi producono generalmente particelle più piccole, poiché aumentano la frequenza delle collisioni e l'energia trasferita al materiale.Il numero di cicli di macinazione e il tempo di permanenza influiscono direttamente sul grado di riduzione delle dimensioni, con un numero maggiore di cicli che porta a particelle più fini.Inoltre, anche la natura del materiale da macinare, la velocità di alimentazione e la velocità di rotazione del mulino giocano un ruolo importante.La temperatura può influenzare l'equilibrio tra la generazione di difetti e la ricombinazione, incidendo sulla dimensione finale dei grani.
Punti chiave spiegati:
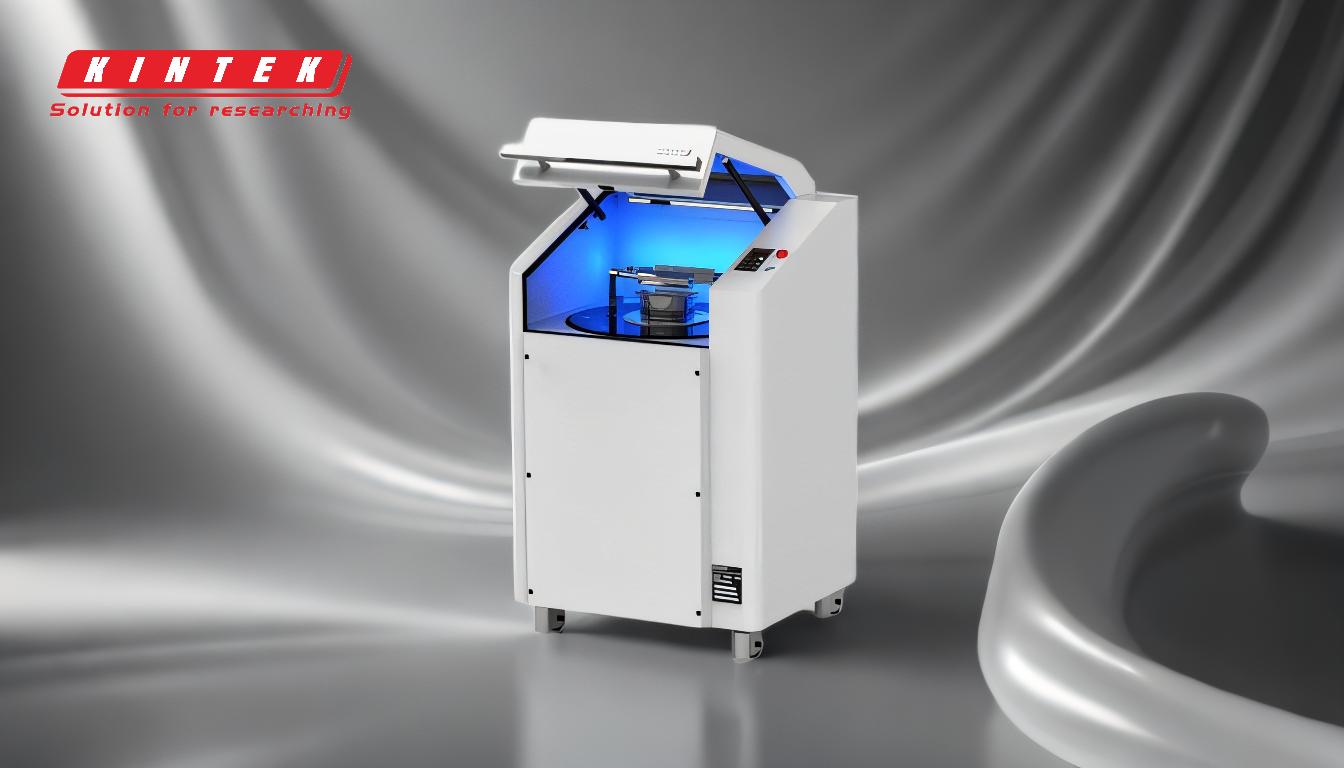
-
Dimensione e densità delle sfere di macinazione:
- Spiegazione:Le sfere di macinazione più piccole sono più efficaci nel produrre particelle più piccole perché aumentano la frequenza delle collisioni e l'energia trasferita al materiale.Anche la densità delle sfere influisce sulla forza d'impatto: i materiali più densi garantiscono una macinazione più efficace.
- Impatto sulla dimensione delle particelle:Le sfere più piccole e più dense producono particelle più fini grazie alla maggiore frequenza di collisione e al trasferimento di energia.
-
Tempo di macinazione e numero di cicli di macinazione:
- Spiegazione:Tempi di macinazione più lunghi e un maggior numero di cicli di macinazione consentono un maggior numero di collisioni e di trasferimento di energia, con conseguente maggiore riduzione delle dimensioni.Ogni ciclo contribuisce all'erosione delle particelle più grandi in frammenti più piccoli.
- Impatto sulle dimensioni delle particelle:L'aumento del tempo e dei cicli di macinazione determina un numero maggiore di particelle più piccole, mentre le particelle più grandi vengono progressivamente frantumate.
-
Tempo di residenza:
- Spiegazione:Il tempo che il materiale trascorre all'interno della camera del mulino influisce sul grado di riduzione delle dimensioni.Tempi di permanenza più lunghi consentono un maggior numero di interazioni tra i mezzi di macinazione e il materiale.
- Impatto sulla dimensione delle particelle:Tempi di permanenza più lunghi portano generalmente a particelle più fini a causa della maggiore esposizione alle forze di macinazione.
-
Velocità di avanzamento e livello nel recipiente:
- Spiegazione:La velocità di alimentazione del materiale nel mulino e il livello del materiale nel serbatoio possono influenzare l'efficienza del processo di macinazione.La velocità di alimentazione ottimale garantisce una macinazione uniforme, mentre il livello influisce sull'interazione tra il materiale e i mezzi di macinazione.
- Impatto sulla dimensione delle particelle:Velocità di alimentazione e livelli del recipiente adeguati assicurano una macinazione efficiente, che porta a una distribuzione più uniforme delle dimensioni delle particelle.
-
Velocità di rotazione del cilindro:
- Spiegazione:La velocità di rotazione del cilindro del mulino influisce sull'energia cinetica delle sfere di macinazione e sulla frequenza delle collisioni.Velocità più elevate possono aumentare l'energia trasferita al materiale.
- Impatto sulla dimensione delle particelle:Velocità di rotazione più elevate possono portare a particelle più fini grazie alla maggiore frequenza di collisione e al trasferimento di energia.
-
Natura del materiale di macinazione:
- Spiegazione:Le proprietà fisiche e chimiche del materiale da fresare, come la durezza e la fragilità, influenzano la risposta del materiale alla fresatura.I materiali più duri possono richiedere più energia per ottenere una riduzione dimensionale.
- Impatto sulla dimensione delle particelle:La natura del materiale determina la facilità con cui può essere macinato, influenzando la distribuzione granulometrica finale.
-
Temperatura:
- Spiegazione:La temperatura può influenzare l'equilibrio tra la generazione di difetti e la ricombinazione durante la macinazione.Temperature più elevate possono facilitare il recupero dei difetti, influenzando la dimensione finale dei grani.
- Impatto sulla dimensione delle particelle:Il controllo della temperatura è fondamentale per ottenere le dimensioni desiderate delle particelle, poiché influisce sulla risposta del materiale alle forze di macinazione.
Comprendendo e ottimizzando questi fattori, è possibile ottenere la distribuzione granulometrica desiderata nei processi di macinazione.Ogni fattore svolge un ruolo critico nell'efficienza e nell'efficacia del processo di macinazione e la loro interazione determina il risultato finale.
Tabella riassuntiva:
Fattore | Impatto sulla dimensione delle particelle |
---|---|
Dimensione e densità delle sfere di macinazione | Le sfere più piccole e più dense producono particelle più fini grazie alla maggiore frequenza di collisione e al trasferimento di energia. |
Tempo e cicli di macinazione | Tempi di macinazione più lunghi e un numero maggiore di cicli consentono di ottenere particelle più fini grazie alla rottura dei frammenti più grandi. |
Tempo di permanenza | Tempi di permanenza più lunghi portano a particelle più fini grazie alla maggiore esposizione alle forze di macinazione. |
Velocità di alimentazione e livello del serbatoio | La velocità di alimentazione e il livello del serbatoio ottimali garantiscono una macinazione efficiente e una granulometria uniforme. |
Velocità di rotazione | Velocità più elevate aumentano la frequenza di collisione e il trasferimento di energia, producendo particelle più fini. |
Natura del materiale di macinazione | La durezza e la fragilità del materiale determinano la facilità di macinazione e la dimensione finale delle particelle. |
La temperatura | La temperatura influisce sulla generazione e sulla ricombinazione dei difetti, influenzando la dimensione finale dei grani. |
Avete bisogno di aiuto per ottimizzare il vostro processo di fresatura? Contattate i nostri esperti oggi stesso per soluzioni su misura!