Un mulino a sfere riduce le dimensioni delle particelle attraverso una combinazione di forze meccaniche, tra cui impatto, estrusione e attrito, esercitate dalle sfere di macinazione all'interno di un cilindro rotante.Il processo inizia caricando i materiali e le sfere di macinazione nel cilindro, che viene poi fatto ruotare a una velocità controllata.Mentre il cilindro ruota, le sfere si scontrano con il materiale, rompendolo in particelle più piccole.Le ripetute collisioni e azioni di macinazione portano all'appiattimento, alla saldatura e alla deformazione delle particelle, ottenendo infine la dimensione desiderata.Il processo è altamente efficiente per la produzione di particelle fini e ultrafini, rendendo i mulini a sfere essenziali in settori come quello minerario, ceramico e farmaceutico.
Punti chiave spiegati:
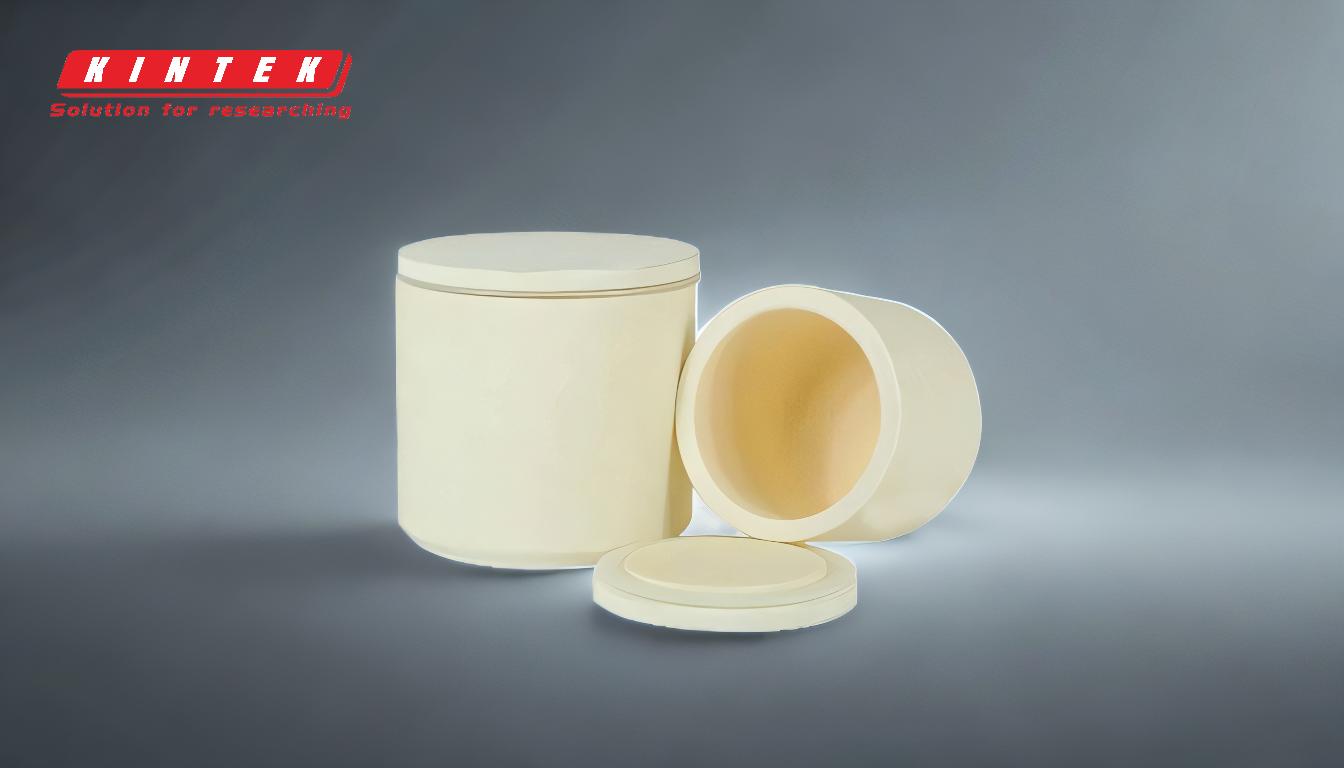
-
Meccanismo di riduzione delle dimensioni delle particelle:
- Impatto:Le sfere di macinazione si scontrano con il materiale, fornendo energia cinetica che rompe le particelle più grandi in quelle più piccole.
- Estrusione:Le particelle vengono schiacciate tra le sfere di macinazione e le pareti del cilindro, riducendo ulteriormente le loro dimensioni.
- Attrito:Il movimento di rotolamento e di scorrimento delle sfere contro il materiale e tra loro genera forze di attrito che macinano le particelle in dimensioni più fini.
-
Componenti e funzionamento:
- Cilindro:Il cilindro rotante ospita le sfere di macinazione e il materiale da lavorare.
- Sfere di macinazione:Sono in genere realizzati in acciaio, ceramica o altri materiali duri e sono disponibili in varie dimensioni per ottimizzare l'efficienza della macinazione.
- Velocità di rotazione:La velocità del cilindro è fondamentale.Se troppo lenta, le sfere non genereranno una forza sufficiente; se troppo veloce, la forza centrifuga potrebbe impedire la macinazione.
- Carico e scarico:I materiali e le sfere vengono caricati nel cilindro e la macchina viene azionata fino a raggiungere la dimensione desiderata delle particelle.Il materiale lavorato viene quindi rimosso.
-
Fasi della riduzione granulometrica:
- Appiattimento:Le collisioni iniziali appiattiscono le particelle più grandi, aumentandone la superficie.
- Saldatura:In condizioni di alta pressione, le particelle possono saldarsi temporaneamente prima di separarsi.
- Strutture stratificate:Gli impatti ripetuti creano strutture stratificate all'interno delle particelle.
- Deformazione:Questi strati si deformano e si rompono, portando a un'ulteriore riduzione delle dimensioni.
- Formazione di nanoparticelle:La macinazione prolungata può produrre nanoparticelle, che sono particelle estremamente fini.
-
Ruolo della dimensione della sfera:
- Palle grandi:Efficaci per frantumare i materiali grossolani grazie alla loro maggiore energia cinetica.
- Sfere piccole:Riempiono gli spazi vuoti e sono più adatti alla macinazione fine, producendo particelle di dimensioni uniformi.
-
Applicazioni ed efficienza:
- I mulini a sfere sono ampiamente utilizzati nei settori che richiedono particelle di dimensioni fini e ultrafini, come l'industria mineraria (per la macinazione dei minerali), la ceramica (per la preparazione delle polveri) e la farmaceutica (per la formulazione dei farmaci).
- Il processo è altamente efficiente grazie all'azione meccanica continua, che garantisce una riduzione costante delle dimensioni delle particelle.
-
Fattori che influenzano l'efficienza della macinazione:
- Rapporto sfera/materiale:La proporzione tra sfere e materiale influisce sull'efficienza di macinazione.
- Velocità del cilindro:La velocità ottimale garantisce una macinazione efficace senza eccessiva usura o consumo di energia.
- Proprietà del materiale:La durezza, la fragilità e il contenuto di umidità del materiale influenzano il processo di macinazione.
Comprendendo questi punti chiave, gli acquirenti di attrezzature e materiali di consumo possono prendere decisioni informate sulla scelta del mulino a sfere e dei parametri di macinazione più adatti alle loro esigenze specifiche.
Tabella riassuntiva:
Aspetto | Dettagli |
---|---|
Meccanismo | Impatto, estrusione e attrito riducono le dimensioni delle particelle. |
Componenti chiave | Cilindro rotante, sfere di macinazione, velocità controllata. |
Fasi di riduzione | Appiattimento, saldatura, deformazione, formazione di nanoparticelle. |
Ruolo delle sfere | Sfere grandi per la macinazione grossolana, sfere piccole per la macinazione fine. |
Applicazioni | Minerario, ceramico, farmaceutico. |
Fattori di efficienza | Rapporto sfere/materiale, velocità del cilindro, proprietà del materiale. |
Avete bisogno di un mulino a sfere per il vostro settore? Contattateci oggi stesso per trovare la soluzione perfetta!